Für Sie empfohlen
Für den Verpackungs-OEM Harpak-ULMA geht es bei der digitalen Transformation nicht nur darum, die Möglichkeiten im eigenen Betrieb zu erweitern, sondern auch die in den Betrieben seiner Kunden.
Der Hersteller von Verpackungsmaschinen und End-to-End-Automatisierungslösungen für Verpackungsstraßen begann 2018 mit seiner digitalen Transformation. Die mehrphasige, auf mehrere Jahre angelegte Initiative zielt darauf ab, das Umsatzwachstum zu fördern und neue Geschäftsbereiche für Harpak-ULMA zu schaffen. Das Unternehmen will aber auch die Möglichkeiten für Kunden in der Lebensmittel-, Medizin- und Industriebranche verändern, indem es sie mit intelligenten, vernetzten Verpackungsmaschinen ausstattet.
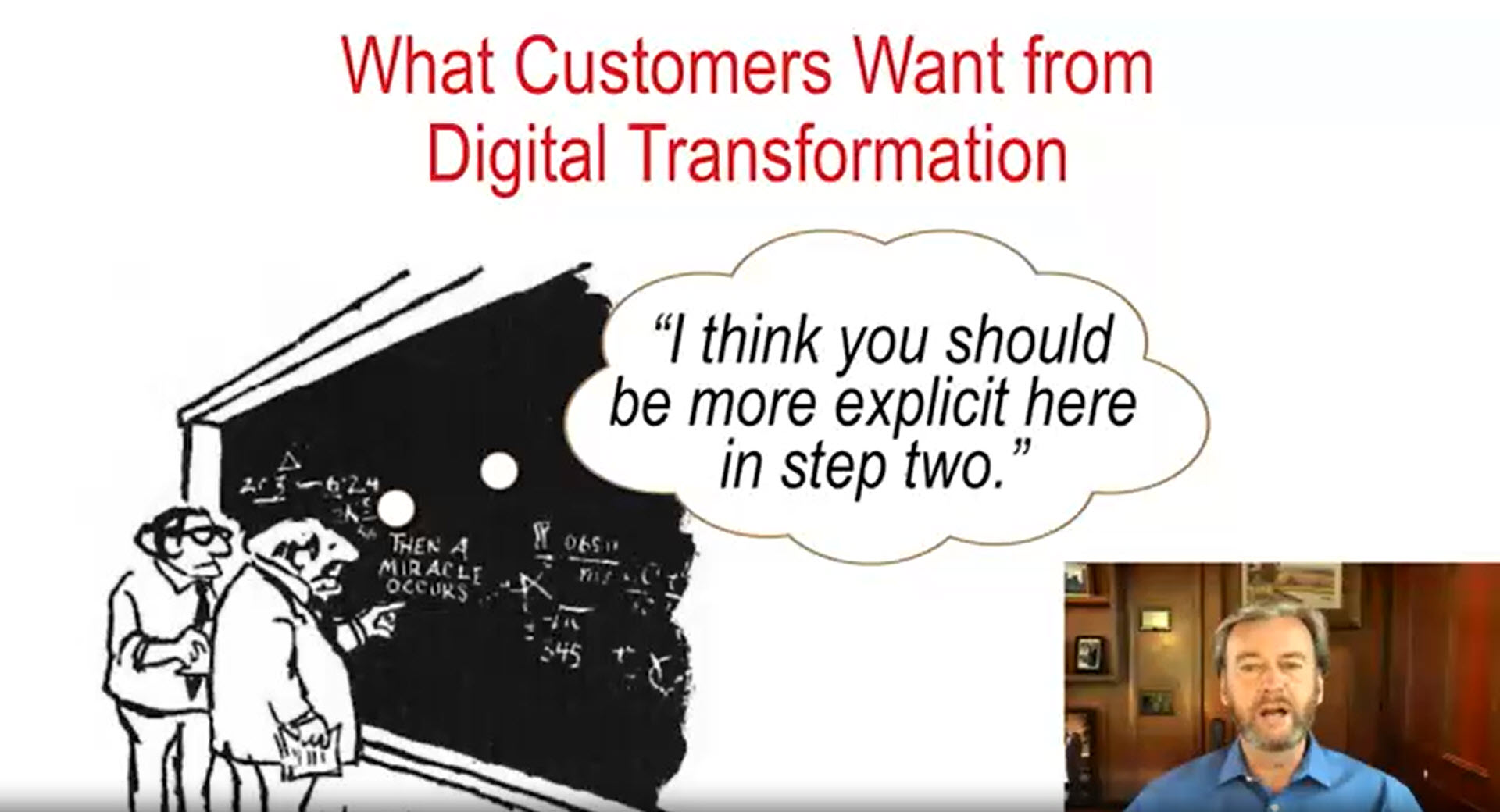
Verbesserung der Flexibilität
Für Harpak-ULMA liegt der Wert der digitalen Transformation in der Fähigkeit, Kunden zu helfen, sich besser an Marktveränderungen anzupassen.
„Digitale Transformation ist nicht ohne Grund so erfolgreich“, meint Kevin Roach, President von Harpak-ULMA. „Sie hilft uns, mehr in kürzerer Zeit zu erreichen, indem wir Daten nutzen, um die traditionellen Hindernisse für Veränderungen – also Zeit, Kosten und Risiken – leichter zu überwinden.
Das Unternehmen startete seine Initiative zur digitalen Transformation im Oktober 2018 mit einer Technologieroadmap, die vier Phasen umfasst.
In der ersten Phase sollte durch Migration auf eine einzige, standardisierte Steuerungsplattform eine intelligente, vernetzte Grundlage für die Kunden geschaffen werden. Harpak-ULMA entschied sich für die Standardisierung auf Steuerungen und Komponenten von Rockwell Automation. Dadurch konnte das Unternehmen eine Grundlage mit offener Architektur für intelligente, vernetzte Maschinen schaffen. Die Steuerungslösungen von Rockwell Automation boten zudem eine vorab integrierte Kompatibilität mit den innovativen IoT-Softwareanwendungen von PTC, z. B. Vuforia und ThingWorx, die dazu beitragen, die Art und Weise, wie Menschen Produktionsanlagen betreiben und warten, neu zu definieren.
In der zweiten Phase wurden Augmented-Reality-Workflows implementiert, um die Produktivität zu steigern.
Mit On-Demand-Know-how und visueller Anleitung, die durch Augmented-Reality-Technologie (AR) bereitgestellt werden, kann Harpak-ULMA Kunden von überall aus unterstützen und neue Funktionen wie virtuelle Werksabnahmeprüfungen einführen. Inzwischen können Kunden die Technologie auch nutzen, um die Lernkurve der Bediener und die Einarbeitungszeiten zu reduzieren.
Gewinnen neuer Einblicke
Harpak-ULMA hat in der zweiten Phase enorme Fortschritte gemacht und arbeitet nun an der dritten Phase, in der weitere IoT-Touchpoints integriert werden sollen. Dabei werden im Wesentlichen Verpackungsmaschinen mit ihren digitalen Zwillingen kombiniert, um eine verbesserte Bedienererfahrung und Informationsintegration zu ermöglichen.
„Durch die Erweiterung des Umfangs und der Tiefe des eingebetteten IoT können wir fortschrittliche IoT-Anwendungen integrieren, die den Produktionsmitarbeitern detaillierte Maschinenabläufe in Echtzeit darlegen“, meint Roach.
Für die Kunden bedeuten mehr Daten, dass mehr kontextbezogene Produktionsinformationen in Echtzeit sowohl für die Mitarbeiter als auch für die Onboard-Diagnose verfügbar sind.
„In dieser Phase erweitern wir die AR-Fähigkeiten, um verschiedene Echtzeitfunktionen bereitzustellen, die es den Mitarbeitern ermöglichen, eine Art Röntgenblick zu erhalten“, so Roach. „Die Offenlegung des digitalen Zwillings einer Maschine ist ein interaktiver Weg, um mehr zu lernen und bessere Diagnosen zu stellen.“
Wenn beispielsweise einem Techniker ein Maschinenproblem gemeldet wird, muss er nicht die Maschine abschalten, die Verriegelungs-/Kennzeichnungsverfahren durchlaufen und den Schaltschrank öffnen, um das Problem zu untersuchen. Stattdessen kann er einfach ein AR-Headset, ein Smartphone oder ein Tablet verwenden, um einen digitalen Zwilling der Maschine anzusehen und den Fehler zu bestimmen.
Prognosen für die Zukunft
Die vierte Phase der digitalen Transformation von Harpak-ULMA besteht darin, maschinelles Lernen und künstliche Intelligenz auf die riesigen Datenmengen anzuwenden, die während der Produktion erfasst werden. Dieses Vorhaben, das sich noch in der Planungsphase befindet, wird es dem Unternehmen ermöglichen, neue Geschäftsmodelle durch die Einführung cloudbasierter, vorausschauender Wartungs- und Benchmarking-Dienste zu entwickeln.
„Diese letzte Phase ist für die Kunden ein evolutionärer Schritt hinsichtlich der Beziehung zu Ihrem OEM“, führt Roach weiter aus. „Big-Data-Lösungen, die maschinelles Lernen und künstliche Intelligenz nutzen, werden dafür sorgen, dass der heilige Gral der vorausschauenden Instandhaltungsanalyse in unseren Märkten erreichbar wird.“
Kunden kann die vorausschauende Instandhaltung dabei unterstützen, ungeplante Ausfallzeiten zu reduzieren und veraltete Instandhaltungs- und Kostenmodelle umzustrukturieren. Und das branchenweite Benchmarking bietet ihnen die Möglichkeit, neue Erkenntnisse zur Effektivität ihrer Produktionsprozesse zu gewinnen.
Natürlich ist die Umsetzung dieser Konzepte in den Produktionsumgebungen der Kunden mit Herausforderungen verbunden.
„Wir müssen Bedenken bezüglich des Dateneigentums ausräumen und Konnektivitätsprobleme lösen, die bei der Überwachung der vorausschauenden Instandhaltung auftreten“, erklärt Roach. „Aber es ist ja nicht so, dass dies völlig neues Terrain wäre. Wenn sich diese Konzepte für Flugzeugtriebwerke umsetzen lassen, ist dies auch in einer Produktionsumgebung der Verpackungsindustrie möglich.
Veröffentlicht 1. Dezember 2020