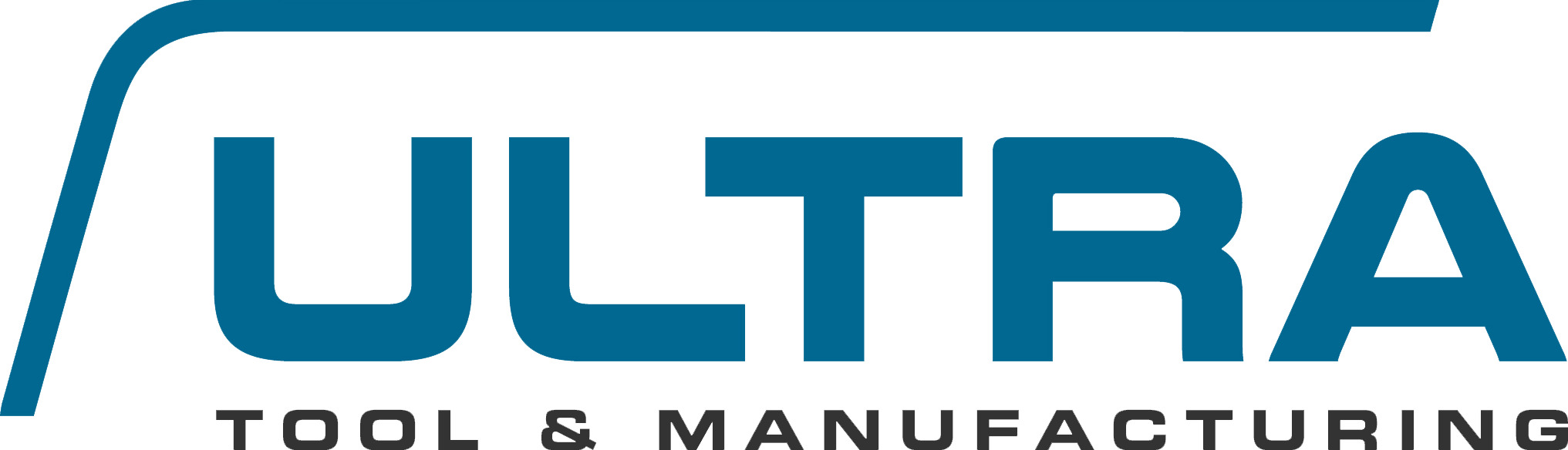
Ultra Tool & Manufacturing, located in Wisconsin, is a privately owned manufacturer focused on quality and repeatability for metal parts and tooling dies from design to production. Specializing in stamping and fabrication, Ultra Tool & Manufacturing produces precision metal components that serve the recreational vehicle, automotive, electrical, lawn and garden, small engine, and military defense industries. With just over 100 employees on board, 2023 marks 54 years of business for Ultra.
- Better control plant floor performance
- Realized $48K annual savings from automating production recording and label-making
- Reduced work center setup time resulting in $80K annual savings
- Saved 243 manual labor hours saved annually
Challenge
Eagerness for Growth
With a humble beginning in 1969 as a Milwaukee-based tool and die shop, Ultra Tool & Manufacturing has grown to include additional services like metal stamping, die design, and metal fabrication. Their world-class operation is headquartered out of Germantown, WI. While they might be located in a smaller town, Ultra manages a larger-scale operation. They have provided their customers with excellent quality and service for over 50 years and continue to thrive today.
This eagerness for growth is why Ultra has gone on to receive national recognition—the company’s leaders have never been afraid of embracing new technology. A new facility in 2015 opened the doors for larger presses and expanded capabilities, including the implementation of Plex’s Cloud Manufacturing software. Over the years, Plex has helped Ultra improve quality, processes, and responsiveness. Since this implementation, Ultra identified a new need for their growing business: the ability to better control plant floor performance.
Improving Plant Floor Performance
When a company makes millions of parts per year, the ability to track and gain visibility is an important capability. Ultra recognized that lack of automation and insight into data at a granular level left a lot of room for mystery—and with mystery comes cost. For Ultra, that cost equated to tens of thousands of dollars in manual labor for setup and more than 240 extra operating hours each year.
When searching for their plant floor automation solution, Ultra identified a variety of pain points they hoped to be addressed. Overall, they lacked visibility on the plant floor. Little to no plant floor insight brought with it a domino effect of other issues: Ultra had no way of knowing machine rates, what they should be, or why an operator failed to meet rate expectations. Some issues, like an operator forgetting to log in or out of production, boiled down to manual error.
Solution
Automating Tasks and Workflows
Plex’s MES Automation and Orchestration (A&O) — a powerful low-code toolset that connects Plex MES to the plant edge, allowing for automation of tasks and orchestration of workflows to remove human error and manual oversight—offered Ultra the solutions they were looking for. Since implementing the system in June 2021, Ultra has experienced a variety of positive changes like increasing visibility into production and tracking data.
After starting with just one stamping press, Ultra moved through nine more over the course of a year and upgraded the controls on machines that were old or obsolete. Their implementation went beyond just machines and included training or retraining operators on how to best use the system. This was a crucial move for Ultra as their operators often hop from machine to machine. A big transition for Ultra, the implementation went smoothly as they broke up the process into sizeable pieces.
Result
Visibility Gained
Gaining visibility has been invaluable for Ultra, saving both money and time. A testament to the immediate benefit of this implementation, Ultra saved $48K in production productivity in their first year. Andrew Loescher, Industrial Automation Specialist at Ultra, speaks to the excitement of such savings, “One of my sole focuses right away was just figuring out what we’re really saving from a standpoint of automating production recording and label making. So in just those two things alone, we captured right around $48,000 of annual savings which basically paid for the product easily.”
Additionally, before migrating to the new system, Ultra was spending 64 hours of manual setup time in excess of their typical setup times. Plex now gives Ultra’s managers the tools they need with tracking, alerting, and utilization of custom screens that visibly display setup times. With all machines considered that are automated with the system, this amounts to $80,000 annual savings from eliminating this non-value-added excess setup.
Next Steps
Ultra’s current implementation is only the first phase. As they continue to move forward, the plan is to continue automating other areas of the company. Increased visibility has led to better decision-making, and the company believes there are more benefits to come down the road. The newfound visibility has inspired Ultra to update other systems in the company, as they continue to streamline processes and unify their teams across all departments.
Published February 7, 2024