The global food system is facing challenges from geo-politics and global warming that are disrupting food production and supply chains. Singapore is especially vulnerable to supply disruptions as it imports more than 90% of its food.
To mitigate these risks, Singapore aims to produce 30% of its food domestically by 2023. This will require Food and Beverage (F&B) manufacturers to adopt new technologies and practices to produce and distribute food in a highly productive and resource-efficient approach.
However, local F&B manufacturers will need to overcome challenges such as high labour costs, lack of skilled workers, and competition from neighbouring countries. At the same time, environmental concerns from consumers are pushing the industry to embrace sustainable practices, like eco-friendly packaging, waste reduction, and energy-efficient processing methods.
Automation, Digitalisation and Information Solutions
F&B manufacturers are turning to smart solutions to improve inventory management, reduce labour constraints, and meet new industry standards. By harnessing integrated automation and information solutions, manufacturers can adapt their operations to accommodate an increasing number of stock keeping units (SKUs) and label requirements, navigate the complexities of evolving channels and routes to market, comply with food traceability regulations, optimise workforce and asset utilisation, and utilise data to meet productivity objectives such as yield and throughput.
Let us explore how smart manufacturing can be applied to help resolve some of these emerging challenges:
Energy Management
F&B manufacturers can gain real-time energy awareness and identify areas to optimise without disrupting production by implementing energy intelligence solutions. In manufacturing processes, the costs associated with water, air, gas, electricity, and steam (WAGES) are crucial but often overlooked.
Energy intelligence solutions allow manufacturers to gain a strategic cost advantage by actively tracking and effectively managing these resources. For example, manufacturers are using Rockwell Automation's sustainability calculator to gain valuable insights into their resources. The tool provides information that helps manufacturers optimise their automation asset maintenance and minimise costly replacements.
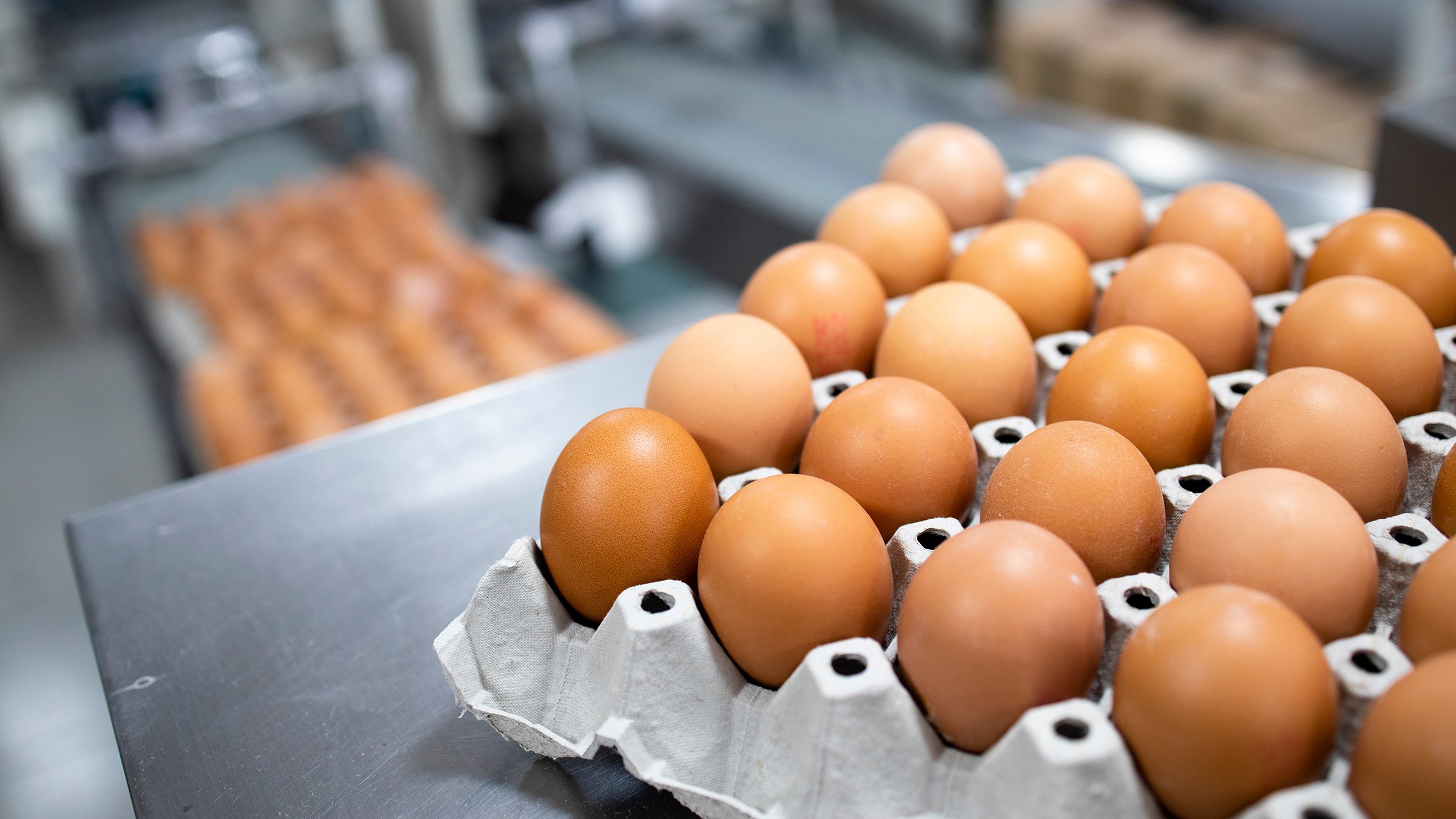
Food Safety
Ensuring food safety is critical in the F&B industry. Automation and control systems can play a crucial role in maintaining product quality and safety, particularly when dealing with variations in raw material specifications.
F&B manufacturers can adopt Industrial Internet of Things (IIoT) technology to build a converged network architecture. This architecture can simplify system operations by enabling production software to collect data from embedded sensors, smart machines, drives, and other physical devices. The resulting manufacturing intelligence can be used for deeper analysis and inform decision-making in a scalable manufacturing execution system (MES). An MES can provide the foundation for a robust food safety and quality system, streamlining traceability and compliance processes. It helps manufacturers verify quality, ingredients, and entire production processes.
Optimising Operations
Many businesses in the F&B industry are struggling with a shortage of skilled workers; as much as 20% of companies are reporting lower yields and an inability to expand due to workforce challenges, based on Rockwell Automation’s Smart Manufacturing Study: A Digital Recipe for the Future Food & Beverage industry.
F&B manufacturers may want to consider adopting digital workforce productivity solutions to help ease the crunch. For instance, using newer technology like virtual reality (VR), technicians can interact with the digital twin of a machine to test new configurations and identify potential issues, all without production interruptions.
Packaging Automation
Applying automation in F&B packaging is fast becoming a crucial strategy for many industry players. The number of SKUs and label requirements continues to multiply and there is growing demand for sustainable materials, retail-ready packaging, and optimised pallet usage. To F&B manufacturers, this translates to the need for more recipes, smaller batches, and countless packaging configurations.
High-performing packaging automation systems offer manufacturers a range of benefits. Aside from enhancing productivity, automation allows manufacturers to accommodate diverse product varieties and sizes and allow for more packaging flexibility. Other benefits include reduced complexity and scalable process control, and the simplifying of operations and maintenance with unified machine control. Leveraging smart technologies allows manufacturers to reduce complexity, save time, and lower costs associated with machine design.
A Collaborative Cyber Strategy
There is no doubt that smart manufacturing is the way forward for F&B industry players in Singapore. There are multiple ways for manufacturers to enhance their operations, including managing product quality and safety, resource and supply chain, minimising environmental impact and driving sustainability.
Nonetheless, F&B players will need to take a strategic approach to their digitalisation and technology adoption efforts. Many operational technology (OT) departments and processes are not equipped to handle the connectivity and data demands of smart devices and systems. They need a collaborative cyber strategy that evolves alongside new technology, bridging IT/OT departmental silos and effectively managing security risks in modern operations. To do that effectively, F&B players will need a cross-functional committed team and partners that they can trust.
Originally published on The Business Times