You may also be interested in
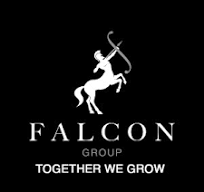
Headquartered in Dubai, UAE, Falcon Group is an established precision engineering company with more than three decades of experience in the delivery of high-quality services to many industries, including aerospace, space exploration, defense, oil & gas, power and utilities transmission, and industrial manufacturing.
Comprising four industrial operations in the UAE and three others in the Kingdom of Saudi Arabia, Nigeria and Oman, it offers a broad range of capabilities, including precision machining & fabrication; custom tool design; manufacture & refurbishment; and industrial automation solutions.
- Manually collected machine-utilization data was presenting a false picture of machine-shop efficiencies
- The company was looking to invest in new machines to counter the perceived capacity shortfall
- Short-term remedies often saw work being handed to competing supplier
- Falcon Group now has a more informed window into its operations, and can make far better decisions based on real-time insights
- On a single machine, utilization has risen from 8% to 57% with ambitions to reach a target of 75%
- $2 million in capital expenditure for new machines to support increased capacity is now no longer necessary
- Machining work can now be kept in house rather than subcontracting
Challenge
Falcon Group is an established precision engineering company based in Dubai, UAE. With four industrial operations in the UAE and three others in the Kingdom of Saudi Arabia, Nigeria and Oman, it offers a broad range of capabilities, including precision machining & fabrication; custom tool design; manufacture & refurbishment; and industrial automation solutions.
The specialist precision engineering and fabrication division offers a range of machining capabilities, including CNC (computer numerical control), custom fabrication and welding, gun & BTA deep-hole drilling, coordinate measuring (CMM), cutting (wire, water & laser), prototyping, and 3D printing.
At the heart of these operations are 16 CNC machines, all of which are essential to the company’s machining capabilities, with their utilization defining much of the capacity planning and the critical path of many of the company’s projects.
In a recent performance evaluation, Falcon Group was assessing the purchase of new machines to help it keep pace with customer demand and to support maintenance downtime for those on the critical path, coupled to the fact that peak capacity often saw it subcontracting work to competitors. Growing by purchasing new machinery was not cheap – with each machine costing between .5 and 2 million dollars.
Before signing off on any additional machinery, the company undertook a machine-utilization study and discovered that although its CNC assets appeared to be working 24/7, some machines were only operating at 12-15% utilization, a figure that offered significant room for improvement.
“We used to collect data manually,” explains Prabhu Badrinathen, CEO, Falcon Group, “using routing cards and manual timing, but we knew this was not giving us the bigger picture, in real time. Our industry software team explained that we could use software to measure OEE (overall equipment effectiveness) and, having looked at the various software use cases, we quickly realized that different elements of each example would work for us, but no single application example mirrored our needs.
“We needed a flexible solution that would address our precise requirements, which is when we started discussions with Rockwell’s UAE Value Add Distributor Al-Ghandi Electrical and Automation."
Solution
This realization that significant efficiency gains were within reach triggered the beginning of a digital transformation that would result in some truly staggering results.
And, for the foundation of this transformation, Al-Ghandi – a member of the Rockwell Automation PartnerNetwork™ – introduced Falcon Group to the ThingWorx IIoT platform, part of the FactoryTalk® InnovationSuite, powered by PTC.
Falcon Group’s FG Engineering and Maintenance Services LLC rose to the challenge by spearheading the development of the ThingWorx IIoT solution in a region with limited support for such a complex use case.
The solution used ThingWorx IIoT to connect different devices, including PLCs and sensors, and then collect, collate, store and present all the operational data to the management team at Falcon Group using tailored software dashboards.
Result
An Early Win in Operational Efficiency and Foundation for Future Success
The collaborative efforts culminated in the deployment of a robust application that seamlessly integrates with Falcon Group's operations. By harnessing the power of ThingWorx, and the acquisition of precise data, Falcon Group is now able to optimize its operational efficiency.
“Step One of any improvement journey is accepting you may not be working to the best of your capabilities,” explained Badrinathen in a recent ROKStudios session. “All subsequent steps then involve working with your suppliers and integrators as a team – honestly and transparently – to find a remedy.”
Falcon measured OEE on one machine to create the baseline and then deployed the ThingWorx IIoT Platform to root out and then highlight the pain points and inefficiencies. In just nine months, the company saw improvement.
“We very quickly had the machine go from 8% utilization up to 38%,” Badrinathen continues, “and with further fine tuning, it is now up to 57%. This is a huge growth and was on just one machine! We have set an ambitious future target of 75% – a growth of more than 365%.”
"All our partnerships start with truly understanding the issues our customers are facing,” said Srikrishna Ganesan, CEO, Al Ghandi Electrical & Automation, in the same ROKStudios session. “We then look to develop solutions rather than simply sell products. We were very happy to have found a platform that delivered not just major additional efficiencies but also significant cost savings.”
Added Efficiency with AMR Use
Further aligning with the company’s test-and-learn culture is Falcon’s decision to analyze the efficiency of their workforce on the plant floor, which spans 65,000 square feet. Falcon found that between traversing the floor to collect a tool or material, take a break, or replace safety glasses or other personal equipment, operators were walking 900 kilometers, or about 560 miles, per year. The amount of time workers had to spend walking instead of being able to focus more on critical job tasks prompted Falcon to find a solution.
The Falcon team worked with Rockwell Automation company OTTO to introduce Autonomous Mobile Robots (AMRs) onto their plant floor. Acquired by Rockwell Automation in 2023, OTTO develops autonomous material handling solutions for manufacturers worldwide.OTTO helped Falcon deploy AMRs on a test basis to enhance what operators can do and reduce employee travel time. AMRs did the work of traveling throughout the plant floor to bring requested tools, materials, and equipment to workers as they focused on higher level tasks. Since deploying AMRs, Falcon has not only seen an increase in worker productivity and morale, but the company has also established itself as a model for using robotics and AI in the discrete manufacturing sector in the Middle East.
In fact, Falcon is now the first certified Systems Integrator for using OTTO. As Badrinathen says, “There’s a gap in the UAE region’s use of advanced technologies, and we are a pioneer of a lot of new projects, such as using OTTO. We want to showcase our facility as a lighthouse in our region for best practices in the discrete manufacturing sector.”
Published January 27, 2025