“We’ve had this relationship in place for years,” Harris says. “And actually, it aligns with our broader Team Lily approach, where we believe it’s the cross-functional teams and cross-functional relationships that really drive success. And it’s that teamwork that helps us advance our agenda.”
Throughout history, pandemics have reshaped our political, social and technological ways of life. They have disrupted industries and communities as a whole and resulted in the initiation of technological innovations.
The current COVID-19 pandemic has been a disruptor for many industries by compounding existing challenges and putting pressure on companies to address them. As technology evolves, leading global innovators in the life sciences and consumer packaged goods industries have been able to confront these challenges. The result is achieving business continuity and generating sustainable revenue.
Vaccinations are an important weapon in the fight against pandemics. However, despite the tremendous advances in medical science, there is still so much about the human body that we are yet to discover. The response to infectious diseases presents a hugely significant area in improving global health and life expectancy.
Innovating vaccine development
The sense of urgency that comes with infectious diseases can itself fast-track progress towards arriving at a vaccine. The need for immediate action unites a range of bodies – from researchers and clinicians through to regulatory bodies and manufacturers – in the quest to get an effective treatment into the hands of healthcare professionals as quickly as possible.
There are a number of steps that are essential in ensuring that the vaccine produced is effective and safe, that any side-effects are properly understood. Then the vaccine will need to be produced at scale on a consistent basis until the threat of illness has been sufficiently minimised.
Historically, the complexity, regulation and cost involved in each of these stages has slowed down the response to emerging health issues. Now, due to advances in AI-related technologies, we have an opportunity to rapidly accelerate the process through which we can deploy treatments into the field.
AI aids the process
While we can never expect overnight success when dealing with something as complex as vaccine development, we can act to remove some of the constraints and bottlenecks that may hamper progress. Advances in automating data analysis and improving visualisation of what is happening at each step of the discovery stage can address some of these inefficiencies, helping to accelerate the process of vaccine development and streamline operations to upscale production.
In the initial, exploratory phases of vaccine development, researchers can use artificial intelligence (AI) to process vast digital libraries of data (such as analysing the properties of thousands of pharmaceutical compounds) with significantly more accuracy than manual processing, to arrive at potential treatment candidates. AI can also be used in these stages for DNA sequencing based on complex human data, allowing clinicians to conduct tests in genetic matching and immunity response.
Once suitable compounds have been identified, the process moves towards live testing. Different patients will react differently to treatments based on factors such as age and prior medical history. The tests therefore need to be comprehensive enough to cover marginal cases where a patient may react badly to treatment.
By training deep learning algorithms, researchers can conduct these tests at a previously unimaginable scale, even before physically administering the vaccine candidate to test patients. These algorithms can be used to identify and sample antibodies to fight infectious diseases with drastic improvements in speed and cost. Advanced analytics and data visualisation of human response to the potential vaccines can then be used to assist with rapid testing, allowing for more intricate analysis and lower error rates.
Upon regulatory approval of vaccine products, the race is on to develop and distribute the medicine across a vast network of hospitals and clinics. Combining AI and sensor-based technologies, manufacturers can harness granular data to bring greater supply chain efficiencies. This helps to avoid demand-supply misalignments in their production processes and minimises the risk of products being spoiled in distribution.
Productivity during the pandemic
Businesses that have embraced digital transformation are better positioned to adapt to immediate demands while maintaining production of other critical goods. In particular, there are three areas in which technology is proving vital in helping these businesses make a difference:
1. Safety and business continuity
Businesses always put the safety of employees first, but the definition of ‘safety’ has changed: it must now incorporate adequate social distancing to prevent their workforce from getting sick. For office-based employees, working from home is generally straightforward; for manufacturers, on-site operators and engineers are usually essential.
Continuity is also a major consideration for manufacturers. Human needs still exist even in the midst of crisis. For pharmaceutical manufacturers, this is especially pronounced, as people still need other critical and sometimes life sustaining medicines. Keeping their production lines operating and getting drugs to market in the midst of this crisis is extremely challenging.
Businesses with the capability to manage their critical operations remotely are far better positioned to ensure plant safety while taking appropriate measures to safeguard continuity. For example, augmented reality (AR) provides machine operators with step-by-step instructions direct to smartphones and wearable devices such as smart glasses.
This also enables remote engineers to provide guidance to site-based operations staff even when they are not on-site – vital to ensuring social distance while maintaining operations and adapting production lines. It also allows technical specialists from essential equipment suppliers to remotely troubleshoot and support manufacturing operations.
2. Responding to increased demands at scale
Prior to the Coronavirus outbreak, the NHS had 8,175 ventilators, and now many thousands more are urgently required. China was responsible for manufacturing 60% of the world’s face masks. Ramping up operations and supply chains to meet immediate demand is an issue all manufacturers are wrestling with.
Technologies such as advanced analytics of digitised operations enable businesses to accurately forecast how they can scale production to meet market demand and positions them for data-driven decision-making.
It provides real-time insight into the functioning of their production lines, where they are losing productivity, what steps are creating bottlenecks, where preventative maintenance is required and any process improvements that can be made. To achieve this level of insight, manufacturers must have connected operations, enabling the large volumes of data produced by their connected assets to be contextualised. This allows tools such as analytics to deliver real value.
3. Flexibility and knowledge transfer
Car manufacturers, for example, are not accustomed to producing ventilators, and will need to dramatically alter their production lines and supply chains in order to do so. At the same time their engineers are trying to overcome the challenges of learning to produce a completely new product.
Businesses that have adopted technologies such as independent cart technology (ICT) have a high degree of flexibility already built into their production lines. These technologies enable businesses to rapidly adapt to changing demands and deliver increased throughput and much faster machine changeover times to produce new products at scale. A high degree of automation means that less on-site intervention is required than with traditional production lines, enabling plants to run effectively on a skeleton staff.
Race against time
For the research labs, pharmaceutical firms, and biomanufacturers racing against time, accelerating production capabilities and reducing time to market is key to saving as many lives as possible. To address the added layer of complication brought on by the disruption to global supply chains, Rockwell Automation has managed to reduce production turnaround time from weeks to just days by helping manufacturers quickly implement innovative automation solutions at scale while helping ensure adherence to the stringent regulatory and compliance requirements for medical devices.
Customer servicing and learning and development did not take a backseat during the lockdowns. Employees were equipped with technology to help them remotely service customers, troubleshoot implementation issues, and continue monitoring ongoing projects through their laptops and even mobile phones, reducing their need to return to our offices.
During the pandemic’s peak, when complete lockdowns were imposed by many governments, we arranged virtual technical training sessions to educate our customers on how to troubleshoot and maintain their enterprise tech tools, such as drives, servos, programmable logic controllers (PLC), and more. At the same time, our technical support teams were readily available to help address any questions or issues faced by manufacturers.
We also ran complimentary e-learning courses for our customers to keep their employees up-to-date with the latest developments and equip them with the skills necessary to successfully deploy the tools provided.
Making history
We are all in a situation without precedent, essentially living in a pandemic that will go down in history as one of the greatest challenge of all times. We all have a role to play in resolving it, and it is uplifting to see industry working together to stop the spread of COVID-19 as quickly as possible. Speed is the word, here: speed of separation of people, speed of production, speed of increasing capacity of the critical supply chain for those essential items required to defeat the virus.
Manufacturers that have already invested in digital technology – those that have successfully connected their enterprise and operations – are able to maintain production and react faster to rapidly shifting market dynamics. Through the deployment of technologies that support remote working, data-driven decisions and flexible production, they are best suited to moving quickly and adapting their operations and supply chains to meet the challenge at hand.
When implemented successfully, the digital transformation of operations and processes seamlessly merges the formidable capabilities of human knowledge and artificial intelligence. Digitalization can help us combat COVID-19, providing the foundation for our post-pandemic future.
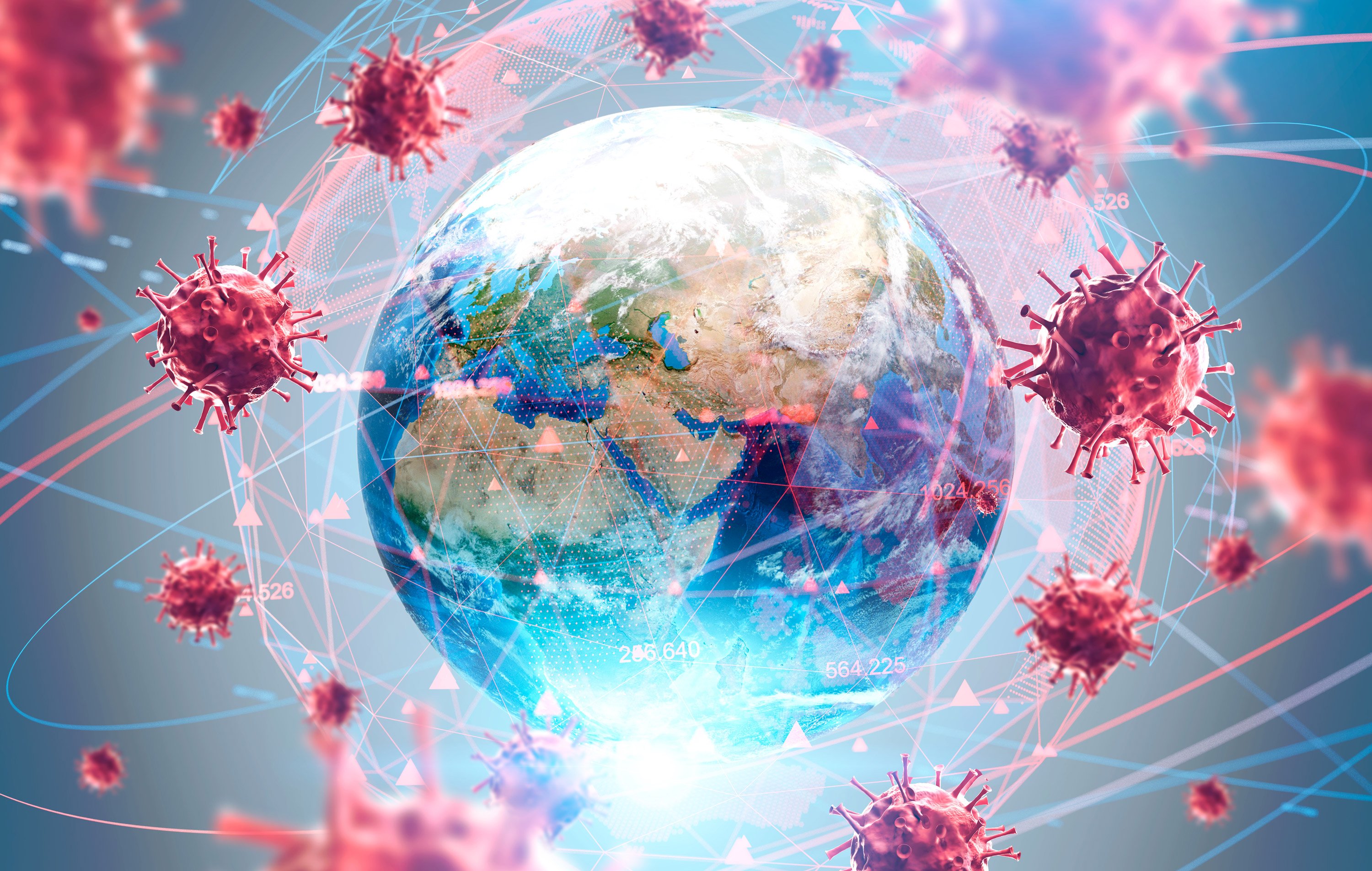
Learning from the best
There are a number of key application successes of leading innovators in life sciences that are a result of effective digitalization initiatives. These application successes address common challenges experienced by the life sciences industry including; compliance, quality, cybersecurity, serialization and operational efficiencies.
Digital strategy boosts throughput
Pfizer Global Supply (PGS) produces more than 23 billion doses of medicine every year across its network of 42 global manufacturing sites. The company set the goal, to support the Pfizer purpose of “breakthroughs that change patients’ lives” by transforming operations into a seamless, data-driven insight engine that drives world-class performance.
This would be no simple task. PGS manufacturing facilities represents a heritage of more than 30 legacy pharmaceutical companies which all had a diverse set of systems and datasets. The first step was to upgrade and improve the security infrastructure across manufacturing sites. This created a standardized way for PGS to not only better secure the plant network, but also help unlock shop-floor data from outside the site.
With the arrival of COVID-19, the firm rolled out digital solutions that allowed teams to continue face-to-face meetings while staying socially distant. Remote collaboration tools like Vuforia Chalk from Rockwell Automation Strategic Alliance Partner PTC were deployed across the global enterprise within a two-week window.
While its digital transformation journey continues, PGS has documented major improvements to date in areas like cycle time, manufacturing throughput and yield, and right-first time quality. At just one manufacturing site, the digital transformation program has been credited with enabling the manufacture of 3 million additional doses of one product above what was planned for in 2019.
Transforming IT/OT to get results
Indianapolis-based Eli Lilly, a global healthcare leader with products marketed in 120 countries, has long fostered a willingness to continually improve and adapt digital technologies. Central to its digital transformation journey is its strong partnership between information technology (IT) and operational technology (OT).
To help with technology implementations both at the strategic and execution levels, the company engages its core collaborators like Rockwell Automation and its Strategic Alliance Partner Microsoft, among others. It also is putting a focus on hiring and developing workers who are digitally empowered.
And of course, continuing to develop and build on the strong partnership between IT and OT will continue to be central to the company’s digital transformation. It is driving the company’s serialization, cybersecurity, analytics and other digitalization efforts.
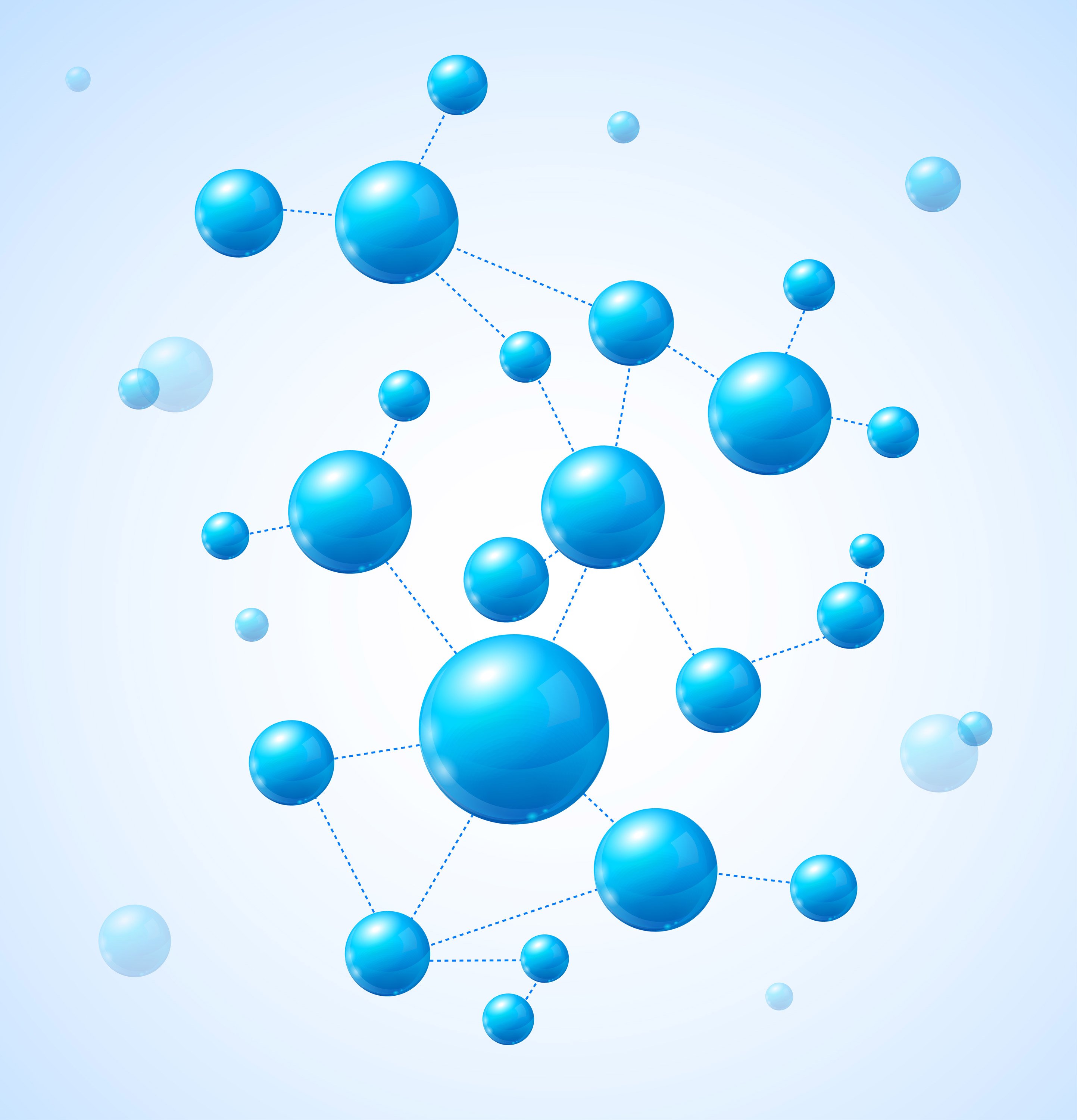
Data integrity and compliance
The journey at Thermo Fisher Scientific began years ago with data integrity. “We began looking at all the ways we could reduce risk by taking advantage of the data we had, and could take us from reactive to proactive,” said Chris Binion, director of innovative and immersive technology, Thermo Fisher Scientific. “We wanted not just the reduction, but the replacement of paperwork. We are enabling our employees with superpowers: the ability to access data and look at historical trends.”
For Cytiva customers, quality and compliance are top priorities. “It is possible to fill an entire bookshelf with the paperwork that is generated for just few batches in the pharmaceutical industry,” emphasized Kirsten Manchester, senior product manager, MES and sensors, Cytiva. “We are on our journey at the same time we are helping our customers. From our side, we are approaching Level 3 of the digital plant maturity model.”
Cytiva is working on how to manage large data sets and how to be able to use tools on top of that to do analytics. There are efficiency benefits in terms of reduced paper and now people are trying to use the information that used to just live in these binders of paper.
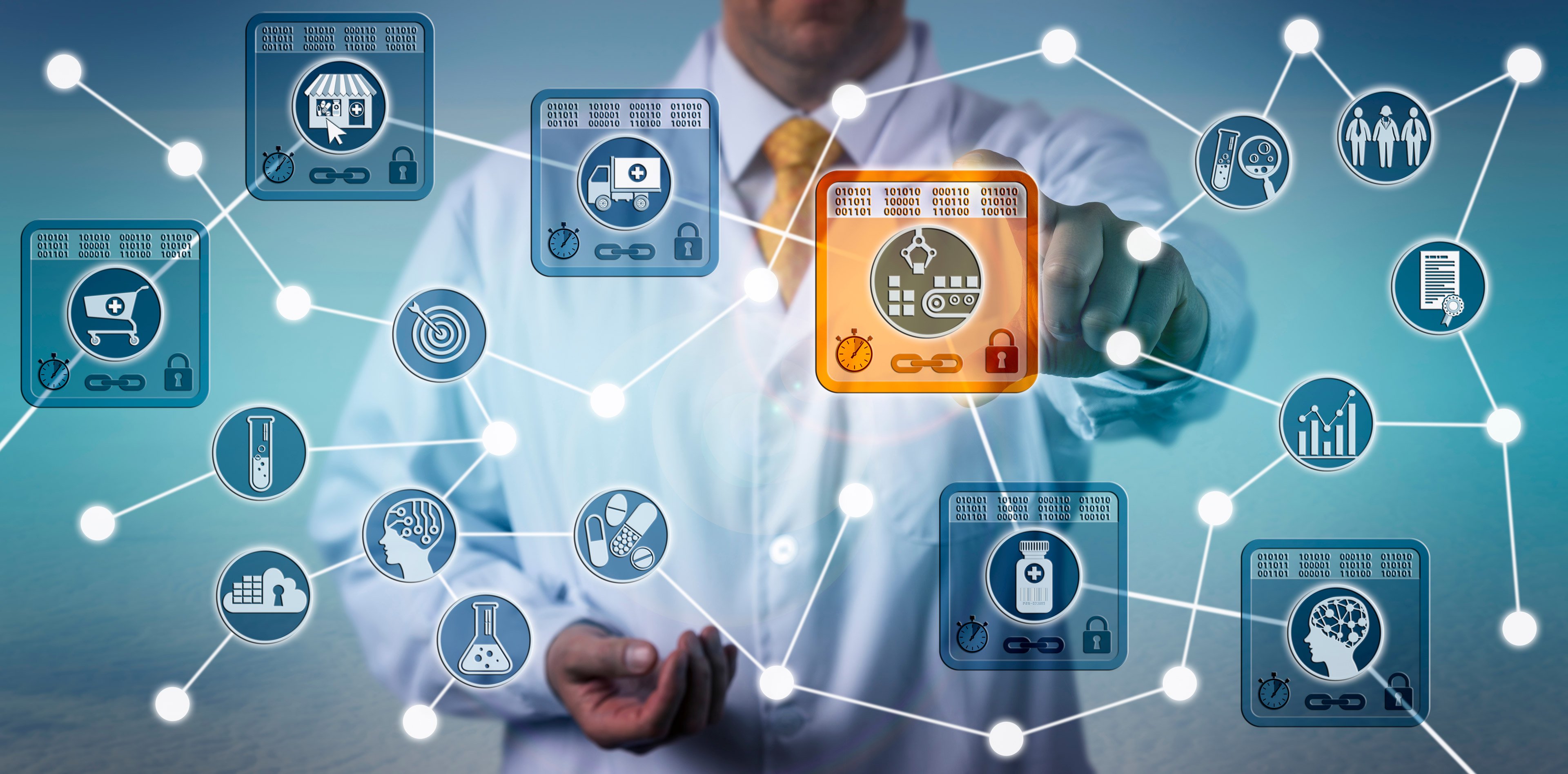
MES for more agile production
Every day there are new demands on manufacturers to achieve extraordinary flexibility at extraordinary speed – making agility critical in today’s fast-changing environment. When Roche Diagnostics needed to transition assets in three of its major facilities to manufacture COVID-19 testing kits, they implemented Rockwell Automation FactoryTalk PharmaSuite MES (Manufacturing Execution System) software. This delivered the flexibility and agility the required to produce more testing kits at a time when there was a significant shortage.
Lonza, a leading global provider of integrated healthcare solutions, recently digitized their operations and in doing so, ushered in a new era of agility and operational efficiency. They will use PharmaSuite MES software, along with FactoryTalk InnovationSuite software to better trace product down to the individual capsule carton and gain insights into performance and production. A segregation of SAP and PharmaSuite MES will also help avoid the disruption of a global enterprise resource planning (ERP) shutdown or required maintenance by enforcing workflows and collecting necessary information.