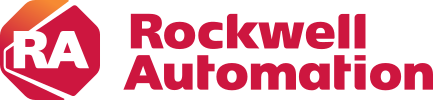
This story is about us! Rockwell Automation, Inc is a global leader in industrial automation and digital transformation. We connect the imaginations of people with the potential of technology to expand what is humanly possible.
- Identify degrading process performance due to worn tooling equipment before it causes disruptions to production
- Earlier detection of a worn item of up to 30-60 days
- Fail rate improved by up to 22%
- $45K savings in labor reduction
- $9M revenue was realized sooner
What’s the upside to having a flat tire? Typically, you’re alerted to the problem immediately. A warning light appears on your dashboard, or you feel a difference when you drive. You patch or replace the tire and continue driving without issue. The problem remains isolated to the tire.
That’s not the case with many manufacturing processes. Often, when a piece of tooling begins to wear, operators aren’t aware that intervention is needed until a larger interruption in the process occurs. This could mean that additional parts of the line are subject to disruption. Product on the line may be damaged. Production may be halted.
Had operators been able to identify the individual issue earlier, they could’ve taken action. Instead, the manufacturer incurs downtime, material waste, and lost production.
Rockwell Automation, specifically Software Architect Kai Lin, and PBCA Process Engineers Miki Cvijetinovic and Gregory Vance, knew this was a problem for our customers and decided to do something about it. They piloted a solution in the Rockwell Automation manufacturing plant in Twinsburg, Ohio.
Challenge
Here's a snapshot of what our electronic assembly operations involves across Rockwell Automation facilities:
- 4K unique circuit board designs produced per year
- 9M components placed per day
- 23M solder joints formed per day
- 14K panels produced per day
Our Twinsburg location has 8 manufacturing lines. Twinsburg is a large production facility, and like all facilities, there are many processes that could impact production. For our pilot, we chose to focus on the stencil printing process.
Understanding the Process
A stencil foil has laser etched apertures, under which a circuit board is mated. Then, a squeegee blade pushes solder paste from the front to the rear of the stencil, filling apertures with solder paste that will deposit and stick to circuit board. At the end of the stroke, the circuit board is transferred and then inspected. The next circuit board is printed in the opposite direction with a different squeegee blade. Each part of this process generates performance data.
More Complex Than Meets the Eye
Like any seemingly simple manufacturing process, there are hidden complexities. First, the stencil printing process is complex with many independent variables. This makes it difficult for support staff to detect wear or degrading performance of the stencils and squeegees, especially when that wear is hard to see with the naked eye. Further, the start of the process and long pauses during the process change the effectiveness of paste transfer, making it difficult to analyze the long-term wear of the tooling.
Additionally, stencils that are thinner or have special coatings have different lifespans, creating even more unpredictability in the wear and tear that happens. And while each step of the process generates performance data, support staff are unable to gather and analyze this vast amount of data—IT, OT, and engineering—in real time.
Support staff needed a better way to collect and analyze real-time performance data on their equipment and be alerted immediately to any equipment anomalies or damage. This was the perfect use case for our anomaly detection algorithm, the computation of which could be calculated and displayed through FactoryTalk® DataMosaix™ seconds after print inspection.
Solution
Our project engineer and software teams took an algorithmic approach to this challenge. They created a patented anomaly detection algorithm, owned by Rockwell Automation, that monitors the tooling in the stencil printing process and sends performance data to support staff. Then, they implemented notifications on that algorithm so plant personnel could receive immediate alerts on anomalies without having to perform tedious post hoc analysis.
Tags and Sensors Needed
First, the engineering team added RFID tags to each of our stencils and squeegee blades, along with a sensor to detect the direction in which the gantry was moving. The team collected the data and tied it against the serial numbers of the printed circuit boards that entered machines that were captured by an existing programmable logic controller (PLC). They also tied the data to the corresponding stencil and squeegee to get the performance data about anomalies, defects and solder paste inspection.
Elegant Data Collection and Contextualization
Next, we turned to FactoryTalk DataMosaix. FactoryTalk DataMosaix is a SaaS application designed to bring in high volumes of raw data from various sources, contextualize it into one platform, and make it useful for applications used by operations management teams.
Why was FactoryTalk DataMosaix selected for this project? Typical BI tools didn’t provide enough data relationship modeling along with the ability to perform this contextualization in real time. Power BI, for example, required someone to perform the analysis manually.
For the Twinsburg plant, this analysis was conducted monthly. With FactoryTalk DataMosaix, the analysis could be done in real time, a requirement for plant personnel to be notified of immediate anomalies in performance.
Additionally, FactoryTalk DataMosaix tracks the entire lifecycle of the squeegee blades and stencils as they move around the plant floor. Typically, when a stencil is used in one line, its data is tracked. When it’s brought back and put in another line later, the data that speaks to the stencil’s past runtime and performance is not considered, thus increasing the likelihood personnel could miss potential performance issues.
Using FactoryTalk DataMosaix, we plotted the data on a chart that identified the risk of equipment failure. This analytical method is a “really elegant way to look at the performance of the line,” says Kai Lin, Software Architect at Rockwell Automation. “It really speaks to whether the line is getting better or worse."
Real-Time Alerts on Teams
Finally, the team built a channel on Microsoft Teams to which anyone at the plant could subscribe and receive real-time notifications of equipment abnormalities or defects. Alerts could have been generated in a variety of ways. Our team chose to use Microsoft Teams because it’s the business system the team was already using.
Here’s how the process used to work. When the Solder Paste Inspection machine detected an issue with a circuit board, the operator had to manually check or clean it, leading to delays or potential errors in judgment. Today, by monitoring the performance of the tooling equipment—squeegees and stencils—the algorithm triggers alerts for unusually high failure rates of the boards, prompting operators to pause and investigate the issue promptly.
Thanks to the implemented solution, operators can quickly identify the equipment causing the failures, whereas previously, the nature of the production environment made it difficult to identify the root of the issue.
Now, it was time to see if the solution worked. The plant went live with the algorithm, FactoryTalk DataMosaix, and Microsoft Teams project in late 2023 and collected data for about 70 days.
Result
Reduction in Failed Inspections
There were several instances in which the engineering team and plant personnel received a notification about a stencil anomaly or defect and were able to react accordingly. Instead of waiting for failure (or wastefully replacing stencils based on a calendar date), the algorithm gave operators a 30–60-day advance warning of stencil failure. And after replacing or repairing the damaged stencil in each instance, the fail rate improved by 22%.
Improved Operator Productivity
Additionally, machine operators became more productive. Now that the support personnel are alerted to stencil issues before they affected the rest of the production line, and had meaningful data to work with, and operators had fewer distractions and could be more efficient.
ROI for Twinsburg and Beyond
After a four-month evaluation at our Twinsburg facility, we calculated that the annual labor savings was dramatically higher than the costs, with an ROI of approximately 200%. With additional use cases planned, we feel confident that the FactoryTalk DataMosaix ROI will increase further, justifying this annual expense.
Revenue Disruption
Finally, the improved fail rate and maximized productivity correspond to revenue wins. Specifically, this enabled the plant to realize $9M worth of revenue sooner due to less disruption.
The Future is Bright...And Productive
What does the future hold for the algorithm and FactoryTalk DataMosaix integration? Engineering and software teams are working to deploy it at scale in Twinsburg, as well as our plants in Mequon, Monterrey, and Singapore. We’re also looking for other applications of this solution within our own operations.
Because Rockwell Automation owns the algorithm, the use cases for our customers are truly endless. As Kai Lin says, “When you think about what the algorithm provides...then really correlating that back to monitoring performance of tooling in the process, I would see a very wide applicability in discrete manufacturing.”
Published June 26, 2024