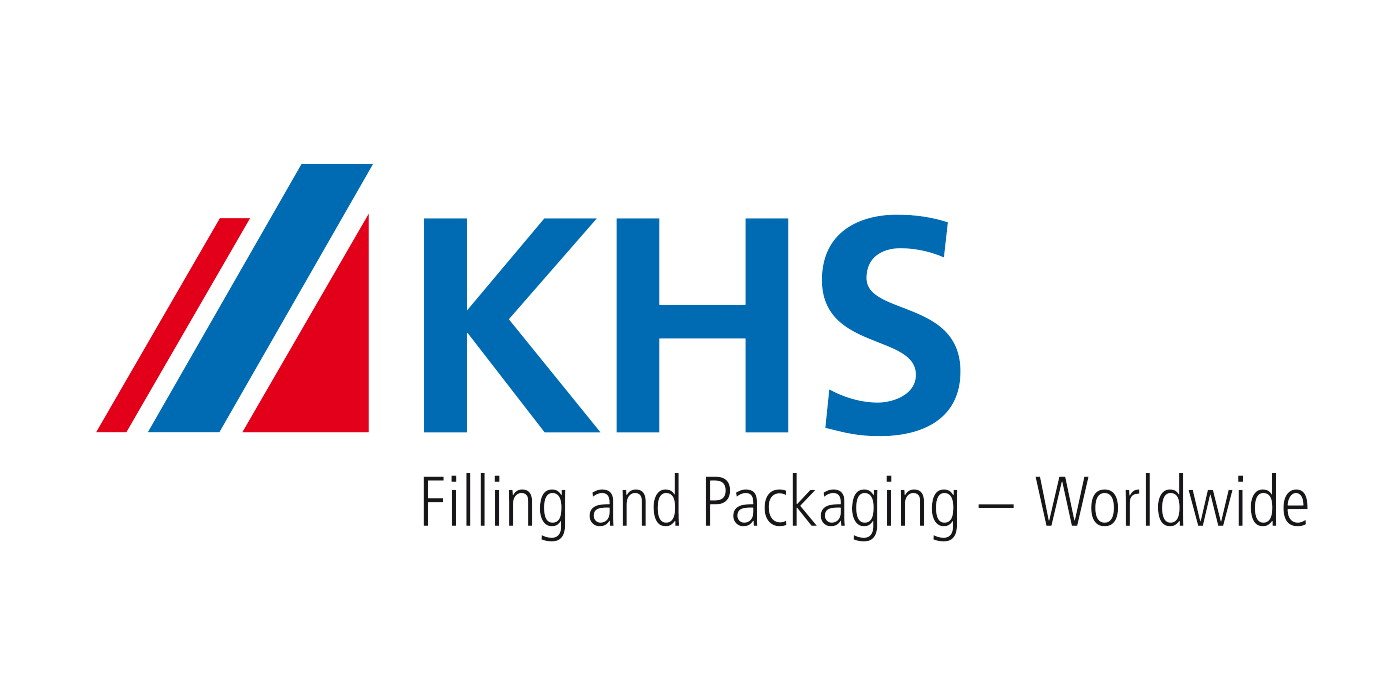
KHS Group is a global manufacturer of filling and packaging systems for the beverage and liquid food industries. The company’s leading subsidiary, KHS USA, is headquartered in Waukesha, Wisconsin.
Rockwell Automation Integrated Architecture System, featuring Allen-Bradley GuardLogix Safety Controllers and Kinetix Servo Drives.
- Speeds installation.
- Improves fill accuracy.
- Simplifies troubleshooting and maintenance.
Challenge
Making the Switch from Bottles to Cans
Microbrewing expanded rapidly across the United States in the 1980s. And Lakefront Brewery was one of the first craft brewers to set up shop in Milwaukee, Wisconsin – a city known for its rich beer heritage.
Established in 1987, Lakefront currently offers more than 20 different beers available in over 30 states and distributed to multiple countries. The brewery is known for its innovative ales and lagers – and boasts one of the most popular brewery tours in the United States.
From the beginning, Lakefront packaged their shelf-stable offerings in glass bottles. But recently, the company opted to transition to cans as a more economical, efficient and environmentally friendly choice. Cans also maintain better quality, since no light can enter the can and degrade the product.
To make the switch, Lakefront called on the same OEM who had delivered the existing bottling line about 10 years before – KHS.
KHS Group is a global manufacturer of filling and packaging systems for the beverage and liquid food industries. The company’s leading subsidiary, KHS USA, is headquartered in Waukesha, Wisconsin. KHS is part of the Rockwell Automation® PartnerNetwork™ program.
Conserving Space. Easing Use.
Transitioning from one packaging paradigm to another is challenging under any circumstances. But space constraints at the Lakefront operation, housed in a historic 1908 power plant, added to the complexity.
“Our space is quite limited,” said David Karrer, director of brewing operations, Lakefront Brewery. “That was a driving factor in our technology decision. We required a solution with a compact footprint.”
In addition, Lakefront did not have the space to run the existing bottling line and new canning application concurrently.
“We had to remove our entire bottling line and start over with the new system,” Karrer said. “To maintain as much productivity as possible, we obviously needed a solution that was easy to install and use.”
To simplify installation and integration with other equipment in the brewery, Lakefront specified a Rockwell Automation control solution for the entire canning line.
Solution
Ongoing Improvements Match Requirements
KHS offered an ideal solution for the Lakefront application – the Innofill Can C filler. Especially suitable for craft brewers, the Innofill Can C fills and seals between 10,000 and 60,000 cans per hour. In addition, the machine’s compact design accommodates the 13-foot X 7-foot space available at the Lakefront facility.
“Our Innofill Can C system delivers the innovations of our larger filling machines in one self-contained skid,” said Brian Anderkay, electrical engineering manager, KHS. “ Its unique combination of size and speed allows higher output capacity when space is at a premium.”
Coincidentally, KHS USA was already working on transitioning the machine’s control system to a complete Rockwell Automation solution when Lakefront approached the company about the project. The original system included Rockwell Automation components, but also a third-party HMI system and fill computer. The dedicated fill computer provided inputs and outputs, but the logic used to generate the output was not visible. As a result, the system was difficult to maintain.
The updated system features a Rockwell Automation platform including an Allen-Bradley® GuardLogix® safety controller, Kinetix® 5700 servo drives and PowerFlex® 525 AC drives. The system runs on an EtherNet/IP™ network and is monitored by FactoryTalk® View HMI software on an Allen-Bradley PanelView™ graphic terminal.
To incorporate the fill computer logic into the main controller, KHS rewrote the program from the ground up.
“Our goal with the rewrite was to keep all functionality of the original machine, while simplifying the actual troubleshooting of the code and overall operation,” said Matthew Herrick, electrical engineer, KHS.
Result
Fast Installation. Better Accuracy & Troubleshooting.
With the Rockwell Automation platform in place, KHS completed installation and commissioning in under two weeks. The 21-valve system currently runs at a rate of 230 to 235 cans per minute to match upstream processing speed.
The switch from bottles to cans also enabled Lakefront to improve fill accuracy. Instead of measuring the product, the bottler used vent tubes to achieve a specific fill level. The canning technology measures product volume using flowmeters.
“As a result, we can individually dial in every single valve to improve consistency,” said Tom Giese, plant engineer, Lakefront Brewery.
In addition, Lakefront anticipates they will be able to handle most maintenance issues with in-house staff.
“Luckily we haven’t had to really troubleshoot yet,” said Giese. “But I can see that troubleshooting and maintenance will be much easier, since everything uses one software and control platform.”
And Lakefront knows they can always rely on KHS for support, if necessary.
“We’re just up the road – only 25 minutes away,” said Anderkay.
Learn more about OEM Solutions.
Published November 15, 2023