“We conducted a thorough site audit at the plant and documented the existing system and current processes. As part of this, we also consulted with the manufacturer to understand the key requirements of the system and the enduser specifications,” explained Doherty.
Challenge
- To upgrade legacy DCS system to mitigate production risk with minimal disruption to production processes and output
Solutions
- Integrated plant-wide control - PlantPAx® distributed system delivers integrated plant-wide control
- Innovative project execution - FEED mitigated project risks and reduced execution time
- FAT and operator training reduced project risks
- IO adaptor card significantly reduced integration time
Results
- Minimal downtime to A-grade product - Careful planning, operator input, FEED and FAT prior to commissioning minimised downtime at the plant during changeover
- Safeguarding production - New system helps secure gelatine production for many years to come
Gelatine is a multitalented ingredient for countless applications. It is a key ingredient in gummy candies, marshmallows, yogurts, desserts and much more. Food applications are perhaps the best known examples but they’re not the only ones with pharmaceuticals, emergency medicine and photographic films also utilising gelatine products.
Derived from the collagen found in the bones, connective tissue, and skin of pigs, cattle, and other animals, gelatine manufacturers must adhere to stringent national and international food processing requirements.
These regulations include but are not limited to cleanliness of the plant, equipment; and adhere to allowable percentages of additives, flavourings, and colourings.
To help safeguard future production of a large-scaled gelatine manufacturing plant, an innovative risk management approach was undertaken to identify and subsequently replace legacy equipment with assistance from Rockwell Automation.
The ultimate goal was to identify and replace legacy equipment with minimal interruption to production.
Safeguarding Gelatine Production
The existing legacy distributed control system (DCS) was over 15 years old and although it was still in operation, if it were to malfunction or breakdown, there was limited ability to have it operational in a timely manner which presented a production risk too great to ignore.
A vendor selection process was undertaken by the manufacturer to assess new technologies that could provide an effective solution for the plant’s requirements.
Through this process it was identified that the Rockwell Automation PlantPAx® distributed system was the most appropriate choice for this application.
The PlantPAx process automation system is built on a standard-based architecture using Integrated Architecture components. This system helps operators make faster, informed decisions and respond quickly to changing demands. It utilises a common automation platform for seamless integration to increase efficiencies and productivity.
The PlantPAx system connects process, discrete, power, information and safety control into one plant-wide infrastructure, leveraging EtherNet/IP™ as its backbone. As a result real time information is readily available throughout the enterprise.
According to Sean Doherty, account manager – Food & Beverage at Rockwell Automation, “In addition to the technology capabilities provided by the PlantPAx solution, a key focus for this project was to design a solution to meet the requirements of the plant, while minimising any production loss and operational risks associated with the changeover to the new system.”
Innovative Project Execution
In the first stage of this project, the Rockwell Automation Global Solutions team were engaged to conduct a Front End Engineering and Design (FEED) specification. As part of this process, technical specifications, scope definition, and risk assessments were evaluated to reduce overall project risks and execution time.
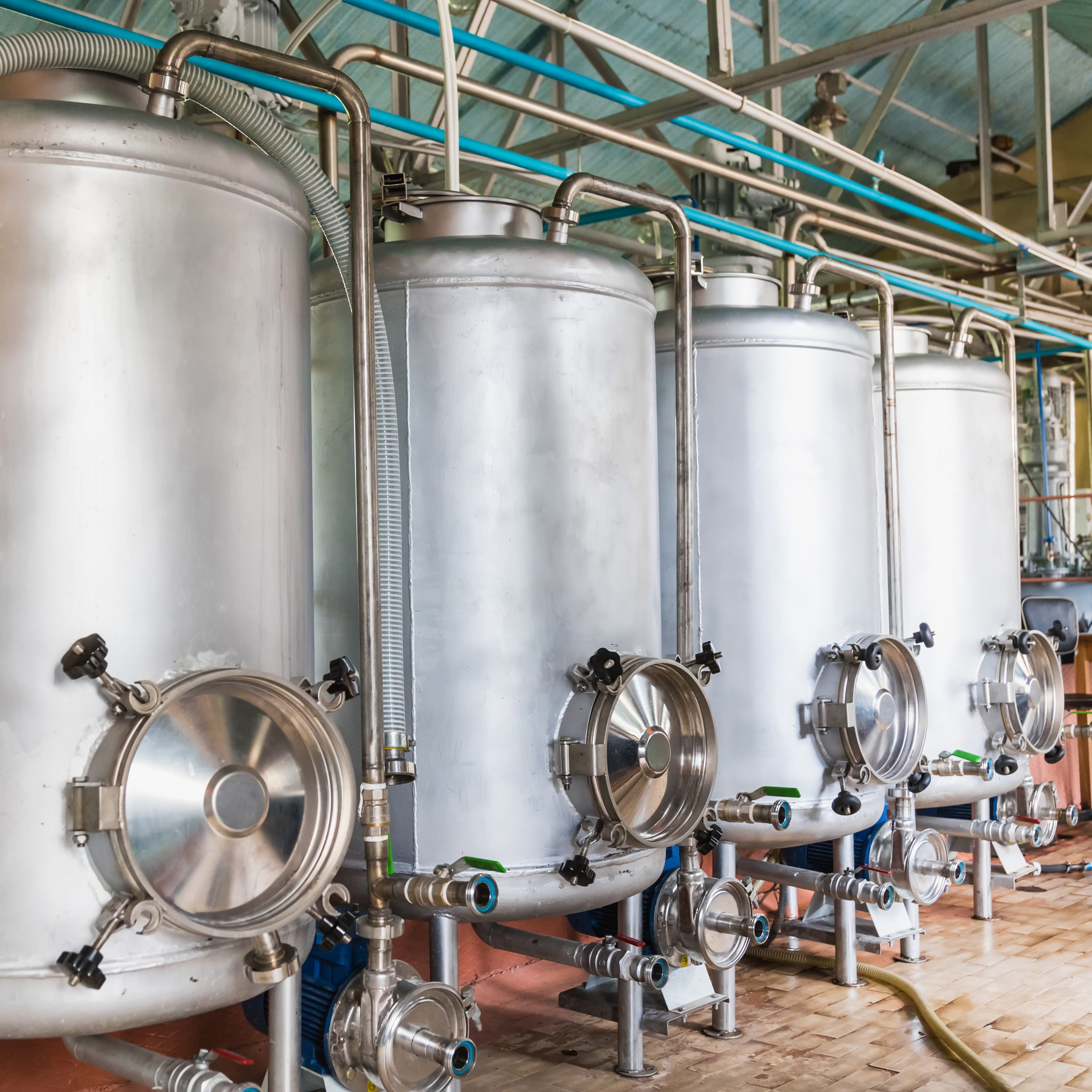
Within a turnaround time of approximately four days, there was a very smooth transition to the new system and the factory was manufacturing A-grade quality gelatine.
To address concerns around risk mitigation, an additional level of testing was introduced for the system with detailed Factory Acceptance Testing (FAT) being conducted at the Rockwell Automation facility.
The plant operators were actively involved in the review process and hands on training as well as testing of the system was conducted to make sure it was functioning to meet all expectations.
The testing was conducted over a two week period to help mitigate any hardware risks and validate it was fully tested and the entire system was working as intended.

The PlantPAx system connects process, discrete, power, information and safety control into one plant-wide infrastructure.
Smart Commissioning
When replacing a legacy DCS system, if the field wiring is replaced simultaneously a significant risk is introduced.
In this particular manufacturing plant there were approximately 1500 IO or approximately 4000 wires in the system, which needed upgrading.
“To have someone disconnect 4000 wires and manually reconnect them, the odds are that some of them are not going to be connected correctly, some of them may be back to front or loose. This would then add over a week to the commissioning team because you would have to go and test every single field connection,” explained Doherty.
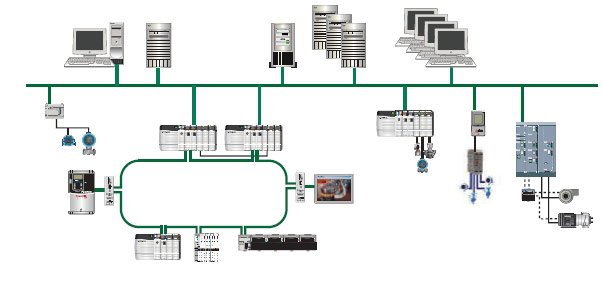
The PlantPAx process automation system is built on a standard-based architecture using Integrated Architecture components.
“To avoid this, we developed an IO adaptor card that would allow us to remove the old DCS and module and replace it with our proprietary designed module so we could signal through our system without having to change the IO wiring. This reduced the changeover time significantly,” he said.
Straight to A-Grade Quality
This project highlights the importance of careful planning and risk mitigation to deliver a successful outcome. From the initial stage of working together to document existing functionality to testing and commissioning, the new system was integrated seamlessly and three days ahead of schedule.
Within a turnaround time of approximately four days, there was a very smooth transition to the new system and the factory was manufacturing A-grade quality gelatine.
Allen‑Bradley, Listen. Think. Solve, PlantPAX, Rockwell Automation and Rockwell Software are trademarks of Rockwell Automation, Inc.
EtherNet/IP is a trademark of ODVA, Inc.
Published April 20, 2018
Recommended For You