- Procedures: This is where you explain what steps need to be followed to enact the policy. When documented and put into place, procedures provide great value as playbooks that anyone should be able to understand and follow. Procedures bring it full circle – ensuring that the people involved are properly communicated with, that consistency is maintained through any workforce turnover, and that a culture of security is part of the conversation.
If your equipment goes down, how prepared are you to recover quickly? Most companies require some level of outside support – especially as they contend with skills shortages, obsolescence risks and increasing operational complexity
As companies continue to reinvent their operating models, products, production and value chains, their key goal is to minimize risk and maximize productivity. Manufacturers are challenged to keep up with advances in technology that can transform the plant floor. Your ability to support, maintain and keep your current systems running optimally – while also equipping your workers for success is critical.
Through innovation, domain expertise and a culture of integrity, Rockwell Automation offers the technology-specific expertise you need, adding value to your solutions throughout the lifecycle of your investment.
The challenges you face can vary by day, location and industry. You may have a skills gap looming on the horizon in one plant or region and need to improve safety in another. You may need to optimize performance of certain assets or an underperforming plant. Or you may be seeking to modernize technology across all of your sites. The capabilities of the Connected Enterprise can help you address some of today’s top manufacturing challenges.
However, to take advantage of the latest advances in mobility, artificial intelligence and other smart technologies, you must first address the challenges around convergence of Operations Technology (OT) and Information Technology (IT). This will allow you to capture the true value of data and analytics.
Networks and virtualization
Tighter integration between industrial assets on the production floor and the rest of the enterprise value chain requires secure networks and accessible data that can be managed under a common system. A robust, secure and scalable network infrastructure can help increase productivity and, more importantly, reduce risk.
Reducing cyber risk in your industrial infrastructure is of critical importance. By proactively discovering your vulnerabilities, misconfigurations, and unsecured network connections, your cyber risk can be reduced. Managed services can help you monitor, administer and maintain your network and virtualization infrastructure.
Pre-engineered solutions such as the Rockwell Automation Industrial Data Center (IDC) helps ease the transition to a virtualized environment for your business, saving you time and money. It combines equipment from industry leaders that are pre-configured specifically for the manufacturing and production industries.
The Versa Virtual is a new addition to the IDC and comes fully configured with remote monitoring and administration attached. Therefore, it does not require a special IT or OT skill to set up and it provides the perfect platform for applications such as Innovation Suite or PlantPAx. Versa Virtual and family of IDCs allow Rockwell Automation to proactively support and manage all phases of the lifecycle.
Services for digital transformation
Companies need to modernize systems to remain sustainable and while transforming to a more digitally focused enterprise can be overwhelming, it is critical in light of the current Covid-19 pandemic.
At its core, digital transformation enables the sharing and exchange of data and information. This is more important now than ever before as we adapt to the rapidly changing demands on production, our supply chains, and on our workforce. When implemented appropriately, digital lets you easily share information between teams, across staggered shifts, or between levels of the organization.
The Lifecycle Services group at Rockwell Automation can provide support at any step of the way, whether it is designing a new plant or working through a digital transformation. Furthermore, because the need for analytics and related support can come at anytime, the group can also help make equipment more productive and secure through a digitally enabled lifecycle. By providing scalable services for small operations through to global, multimillion-dollar enterprises, the level of support can be customized to suit your requirements.
Connected services focused on the OT space – whether managing a single network or a full OT cybersecurity program rollout across the globe – can help you sustain growth. Together with on-site maintenance and support or technical support and training, all services are driven by data and analytics.
As IT and OT convergence takes precedence, cybersecurity is not only a must for your everyday operations, but it is also critical for your ongoing digital transformation program. A security posture that is based on a single technology like a firewall is not enough, especially when insider threats can be as much of a risk as outside threats. Work with those who specialize in the security of OT systems to integrate cybersecurity into your transformation plan and technology roadmap.
A good place to start
An Installed Base Evaluation makes it easy for you to collect and analyze critical performance information within your facility, helping you to plan for future.
It can be challenging to keep a firm grasp on your installed base. With production systems in place across multiple locations, industrial assets may have been supplied by various vendors and maintained by different workers.
Perhaps you do not know that you lack a critical spare part until production goes down. Or even worse, maybe that particular part is no longer manufactured. When you lose track of the systems and parts in your facilities, you face risks like obsolescence, parts shortages, and training gaps with personnel.
However, by using digital tools you can obtain an accurate picture of your installed base. Imagine not only knowing what you have installed, but also how it is changing over time. This information can give a clear picture of the installed base and prioritize the risks that pose the greatest danger to production. It can also uncover additional risks in other areas of the business. For example, with this visibility you could evaluate the devices on your most critical assets and consider training programs to make sure that workers have proper skills for the assets they are expected to maintain and operate.
With visibility into your installed base, you’ll know whether there are sufficient spares in your inventory to make sure you can replace a device if there is a failure. This helps to reduce the risk of extended downtime.
Another opportunity during uncertain times could be to assess obsolescence risk across your installed base. Knowing the lifecycle status of your installed devices, both Rockwell Automation and a third-party, can do more than help plan modernizations. Where modernizations may not be feasible in the short term, this information can help you determine an appropriate support strategy to ensure that you have access to replacement parts and the knowledge required to maintain your assets.
A third use for this information is training. Imagine not just having access to installed base insights and analytics but also being able to connect your installed base directly to your training programs to verify that your team has the skills it needs to maintain production. With e-learning, My Equipment, and the broader application of digital toolsets, this connection across disciplines becomes possible.
Asset performance management
According to a recent ARC Strategies report, Rethinking Asset Performance Management, successful asset management requires close cooperation between the maintenance, reliability, process engineering, and operations functions in an industrial facility. New digitized tools can make that cooperation easier.
The right toolsets can also make previously manual tasks more automated to help you and your team be more productive. Accessing the right data and information, whether it be installed base insights, training programs or otherwise, is becoming increasingly important as companies try to adapt quickly to changing conditions.
With digital access available every time, you save critical time planning a response, taking action, and communicating to your stakeholders. With rapidly changing production schedules, demand planning and supply chain impact, it is more important than ever before to have trusted information available to help you make decisions and take time sensitive actions.
Securing remote access
Manufacturers need to actively manage remote access to their plant floor to avoid exposing assets to vulnerability risks and unfortunately, everyday those risks get more serious. As plant floors become more connected – from the equipment to the systems – the way manufacturers manage internal and external access to that technology is evolving.
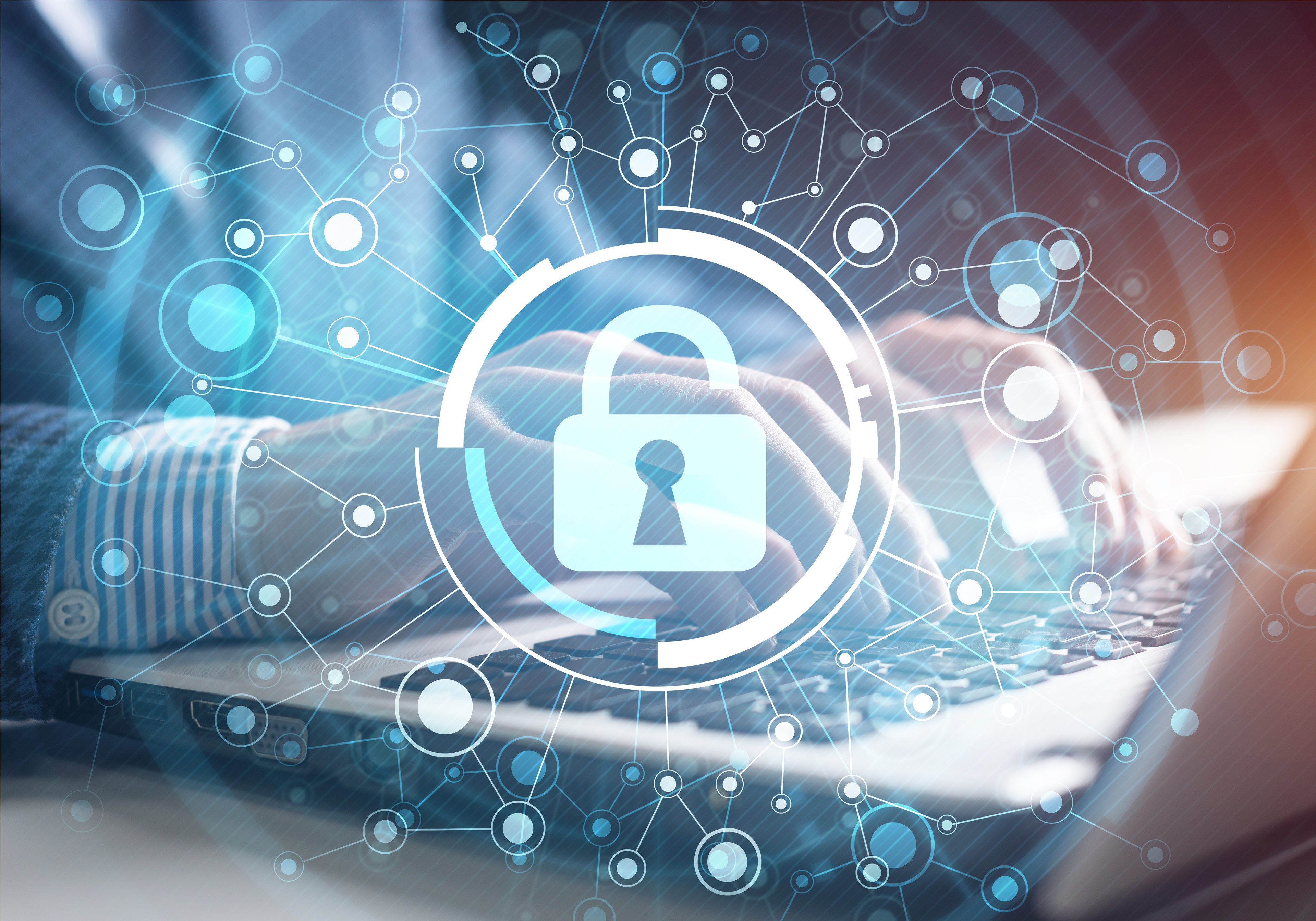
Every manufacturer should be concerned about the rise in ransomware attacks that have taken advantage of the vulnerabilities specific to the OT environment. More commonly, human errors can also result in unplanned downtime and safety and environmental risks. While remote access enables virtual troubleshooting and monitoring that would otherwise be expensive and time consuming, it also opens up the potential for mistakes. For example, it is not difficult for an off-site vendor or on-site manager to accidentally download a program to the wrong PLC, which can result in incorrect functioning, downtime production losses and additional costs.
Secure remote access provides both a secure line of communication and an avenue for remote access to enable the active management of access to the machines, equipment, controllers and systems on your plant floor. Most manufacturers use equipment brought in by OEMs or system integrators, who can remotely connect in order to troubleshoot and manage that equipment, including HMIs and PLCs. Thanks to secure remote access, they can respond more quickly to issues and provide better uptime and availability for their equipment.
Secure remote access is about much more than the technology used to enable it, which in most cases is a virtual private network (VPN). The VPN provides the infrastructure, serving as a secure virtual tunnel, for managing who is travelling through the tunnel to access your pant floor. Secure remote access allows you to manage the policy and procedures, control who has access to what, ensure secure communications and conduct audits and traceability of service.
One way to restrict access is to enact a specific firewall rule configuration that only allows outbound, not inbound, traffic from your site. That inbound traffic is restricted to specific IP addresses with authentication requirements, further limiting that access. By restricting the communications capabilities and managing access, you are able to monitor, track and log all activity.
Not only does this give manufacturers the power to proactively control the virtual traffic on their plant floors, but it provides enormous value by providing timely issue resolution and reducing unplanned downtime. In manufacturing, time is money – secure remote access can help protect your bottom line by helping you make modifications to the production environment more quickly, run more efficiently, and make better data-driven decisions.
People, Policy and Procedures
In order to make security a part of the workplace culture, manufacturers need to focus on three things: People, policy and procedures.
- People: This includes everyone who is involved in the use and management of secure remote access, including third-party security providers, OEMs and system integrators who have users with access, site staff and managers, and the corporate governance team. These teams are key to making policies and procedures work. And with the right education and training, they will help you create a culture of security in the workplace that will help decrease vulnerabilities and risk.
- Policy: The policy is where you start – this guiding principle defines how secure remote access will be managed. It should outline who needs access, to what, and why. It should address whether there’s one process or multiple, whether access is centralized or spread out, and whether this is active or passive management. Are there other policies that need to be taken into consideration when developing this one, such as the overall security profile? If you already have a policy for physical security, which might include badge access and rules about who is allowed where, how does that extend to or interconnect with the remote community? If you want to revise your current policy, review logging and traceability capabilities as well as audit results. And don’t forget to test your own system to look for holes and improvements.
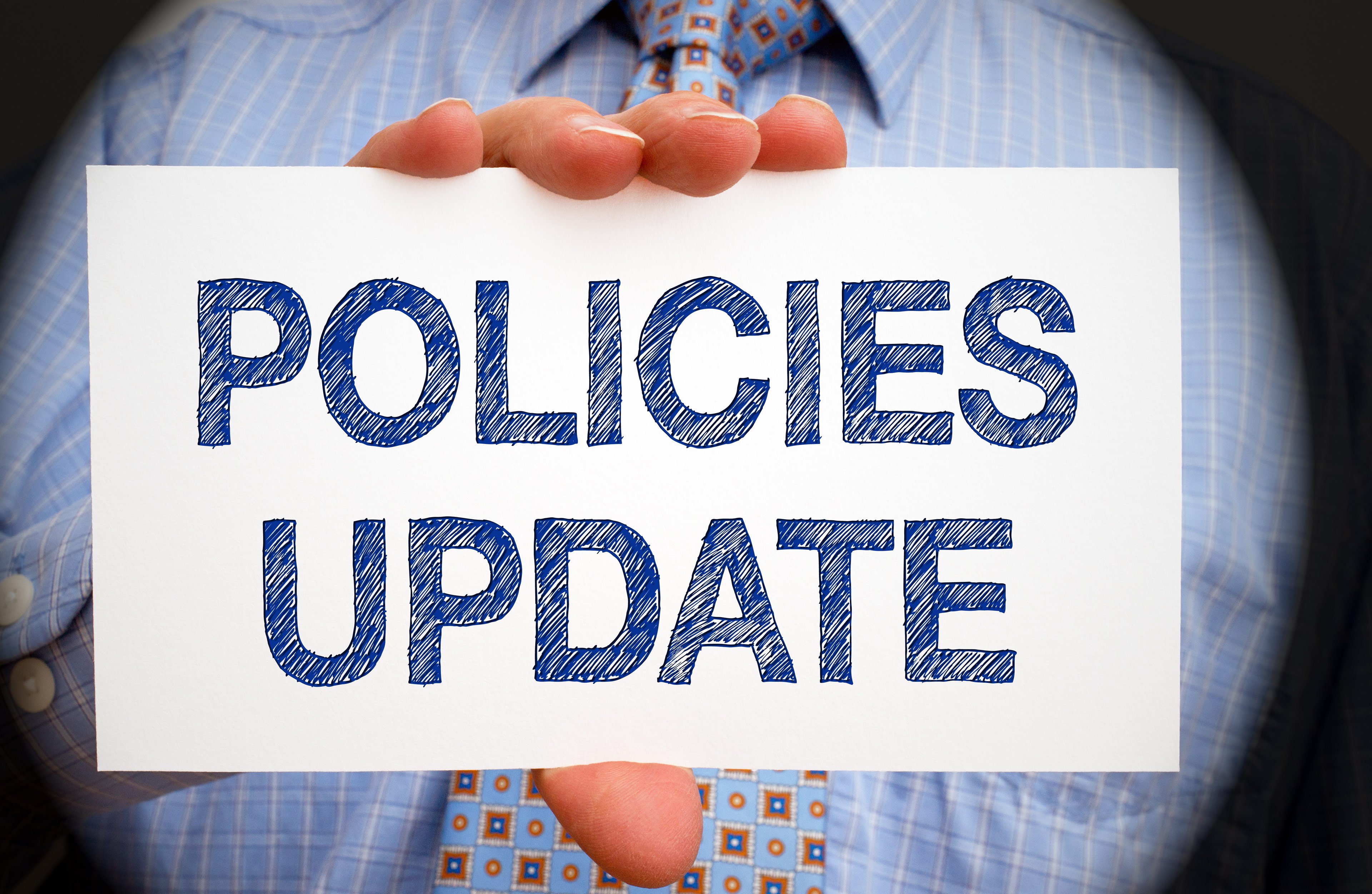
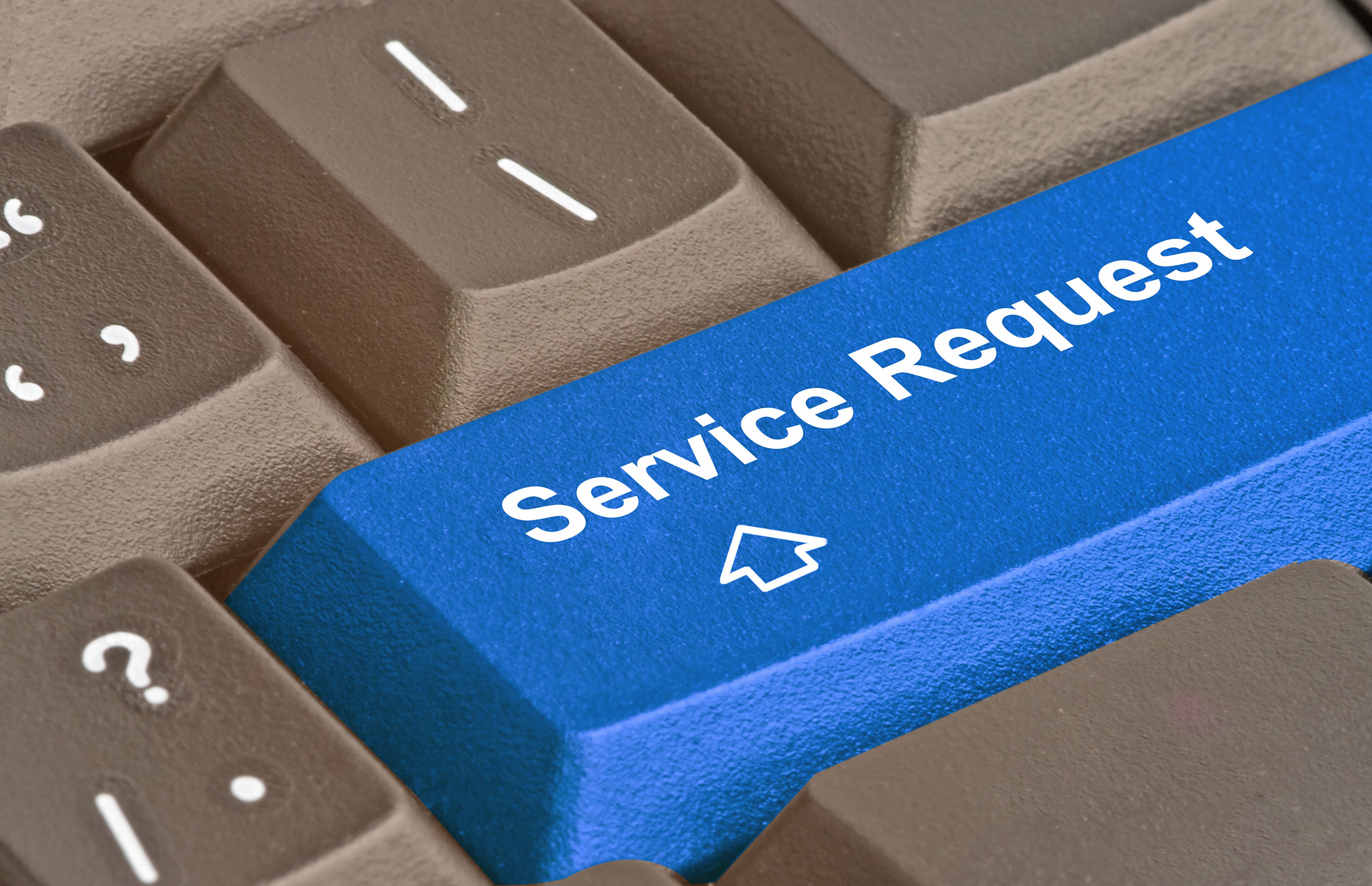
Technical issues cause headaches and can inhibit performance. Whether you need to quickly resolve production issues, improve training, or streamline software updates, Rockwell Automation TechConnect support services can help:
- Resolve your issues with online support and access your support history
- Get back up and running faster with support from product specialists, who can help install and configure, troubleshoot, or diagnose technical issues
- Specialists are ready when you need them with 24x7x365 availability
- Manage training
- Better manage software updates
- Solve issues faster with the Live View SupportTM Tool – allowing you to share a real time view of what you are seeing directly with technical experts who can help with articulating the issue and expedite the troubleshooting process
We continue to innovate and modernize the way we provide technical support to our customers by leveraging PTC’s Vuforia augmented reality (AR) platform. Our cloud-based AR library already brings a modern approach to repairing and maintaining Allen-Bradley hardware. And with a TechConnect Support contract, a mobile device and the Vuforia View application, customers can readily launch an AR experience related to the task they are performing and be walked through the proper steps.
Our lifecycle services enable you to expand what is possible through active collaboration and support, whether you are designing, building, sustaining or improving your enterprise.
No matter where you are on your lifecycle journey, our support can help you navigate the complexities and find success.
Recommended For You