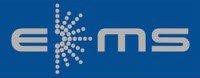
EDMS Consultants Sdn Bhd provides digital solutions and services including Content, Document and Business Process Management. EDMS assists in automating and streamlining clients’ business processes – resulting in improved business profitability and productivity.
- Manual tracking of asset management and maintenance activities
- Insufficient equipment information including limited historical data and spare parts availability
- Frequent emergency breakdowns, reactive maintenance, and delayed parts leading to increased downtime
- Fiix CMMS (Computerized Maintenance Management System™) software platform
- Increased Preventative Maintenance Compliance score to a world-class rate of 88%
- Reduced total monthly downtime rate to 4.52%
An Asia Pacific engineering and construction firm is helping to advance the region’s digital industrialized building system (IBS) capabilities and revolutionize the local construction industry. IBS is a process in which precast walls, slabs and other structural elements are produced off-site and later assembled and installed at the construction site.
With digital IBS, cloud-based Building Information Modeling is integrated with high-level automation and robotic production to produce parts to specification in a controlled manufacturing setting. This technique provides greater precision and accuracy, leading to enhanced product quality and reduced waste. It also accelerates construction timelines, reduces the need for manual labor, improves project safety, and minimizes the carbon footprint during construction.
Using digital IBS, this firm has the production capacity to deliver up to 10,000 housing units annually and make a significant contribution to local affordable housing inventory and goals.
Challenge
Limitations of Manual Asset Management
Despite running an advanced manufacturing operation featuring a large base of complex machinery and robotics, the firm was tracking its asset management and maintenance activities manually using spreadsheets. This led to insufficient equipment information, including limited data about previous performance issues, repair history, and current availability of spare parts. As a result, reactive maintenance and emergency breakdowns often took place, and there were frequent delays in securing replacement parts. All of which increased downtimes.
To remedy those issues and become more strategic with maintenance operations, the firm registered for a free trial with Fiix, a Rockwell Automation company. Fiix provides a comprehensive CMMS (Computerized Maintenance Management System) software platform that automates maintenance management.
Solution
Automate Asset Management and Maintenance with Fiix
Quickly seeing the value of Fiix, the firm ultimately adopted the CMMS platform and eventually engaged EDMS Consultants in 2019 for further support. EDMS partners with Fiix to provide digital solutions and services to help clients automate and streamline processes, including asset management.
“Fiix’s user-friendly interface and real time data access has empowered this client’s maintenance team to proactively address issues, optimize asset performance and minimize downtime,” said Mohammad Thaqif Taher, EDMS application consultant.
Using Fiix’s Asset Management module, the firm now registers, tracks and manages assets and lifecycle performance in a centralized dashboard that offers necessary stakeholders access to real-time information.
“This has led to better asset utilization and maintenance planning, including preventative maintenance,” Thaqif explained. “Information available includes the historical maintenance activities associated with a particular asset from day one so users can see everything that has been done previously.”
The firm uses Fiix’s Work Order Management module to improve and streamline incoming work orders. This feature allows employees to submit a work order request even if they’re not a licensed Fiix user.
“This module also allows them to analyze the thousands of work orders previously completed,” Thaqif said. “Such data-driven insight leads to more informed decisions regarding asset maintenance, resource allocation and long-term planning.”
Whether on-site or working remotely, all of these capabilities and information are available in Fiix’s mobile app. Further, the firm uses Fiix’s reporting tools to generate and send custom reports with critical insights to its maintenance and management teams.
Result
World-Class Preventative Maintenance Compliance and Reduced Downtime
With real-time access to asset performance and other critical information, the firm increased its Preventative Maintenance Compliance rate from about 60% to a world-class rate of 88% by the end of its 2020 fiscal year (and before the global pandemic changed production patterns and standards).
“Fiix is one of the best CMMS software products that I have ever used for maintenance planning activities,” said a senior maintenance engineer with the firm. “After several years of using Fiix, we’ve seen a lot of improvement in my department especially with maintenance downtime that impacted production.”
By 2020, the firm had lowered its total downtime to 4.52%, below its 6% monthly target rate.
“The implementation of Fiix has increased the visibility and enhanced the overall operation efficiency of their maintenance operations,” noted Thaqif. “With a clear view of activities and asset status, they’re maximizing the lifespan of its critical equipment.”
Explore CMMS and ERP System Integration
As part of its engagement with this firm and its other clients, EDMS provides a regular schedule of Health Check reports and sessions. In these sessions, they look at how clients are using Fiix and identify opportunities to maximize the platform’s full capabilities.
“For example, this firm has the opportunity to use Fiix’s Parts Forecaster tool to gain valuable predictive insights into spare parts availability, which enhances parts and purchasing management by reducing stock out, related downtime and maintenance costs,” Thaqif said.
“We also hope to integrate this and other Fiix data with their ERP system, Thaqif added. “We want them to leverage all of Fiix’s modules and we’re committed to providing ongoing support during their Fiix journey.”
Published January 18, 2024