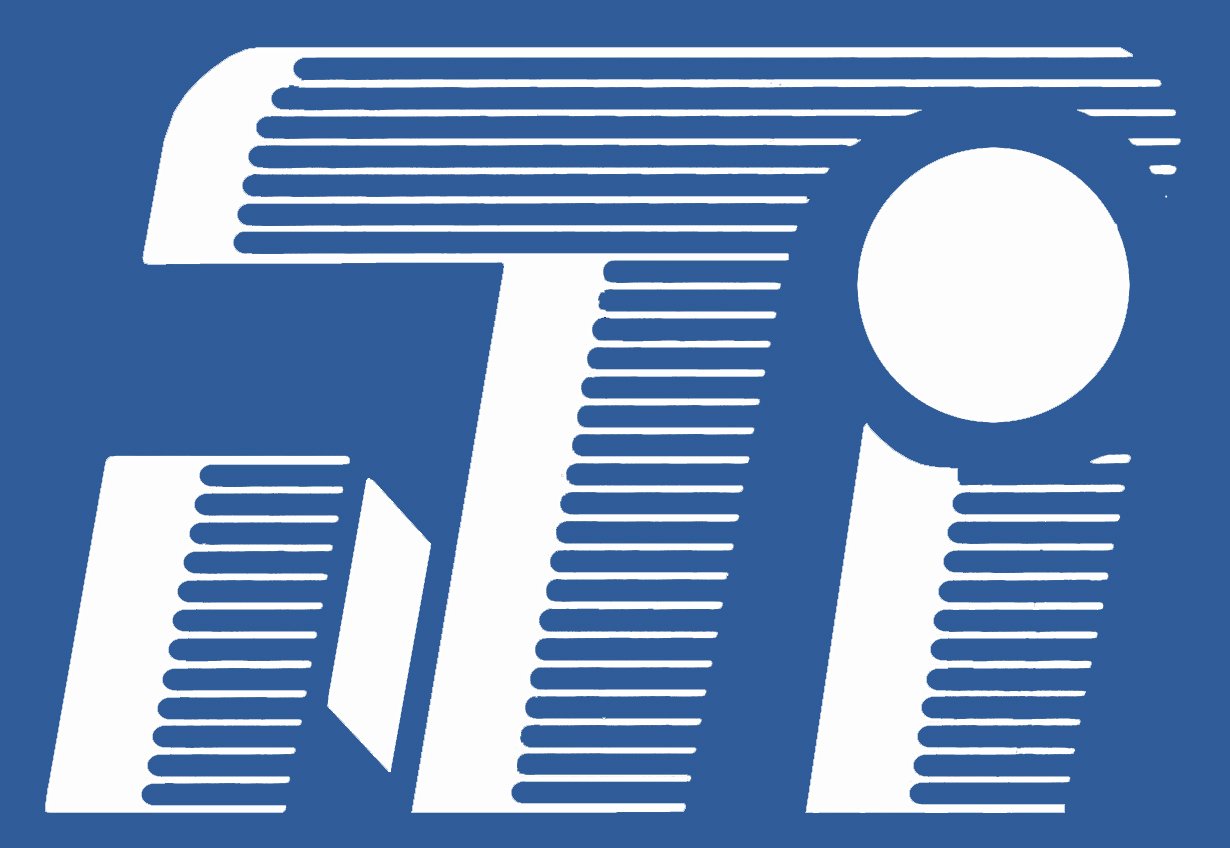
Newman Technology, Inc. is the North American Group of Sankei Giken Kogyo Co., Ltd. For over 30 years, the company has produced quality parts and developed solutions for motor vehicle markets. Quality, innovation, and continuous improvement have made them a top supplier of Exhaust, Door Frame, and Exterior Trim products.
- Antiquated processes for customer order changes
- Cumbersome to make process improvements
- Inventory process was way too time consuming
- Achieved 98% inventory accuracy
- Reduced inventory on hand cost by 25%
- 62% reduction of time for inventory checks
Challenge
Newman Technology employees build and manage hundreds of thousands of components each day in four facilities. The company receives 1,500 containers of parts a day from a myriad of suppliers. After production and assembly, Newman Technology ships out 5,000 containers of components to 15 customer locations around the world.
Manual Methods
For years, employees relied on spreadsheets and paper purchase orders to move materials through their operation, which was cumbersome and time consuming. The processes were too antiquated to support quick customer order changes, and Newman had a difficult time forecasting demand. Even worse, when a change was made to a procedure, every department’s manual had to be updated — and those updates involved producing and manually replacing forms for up to 25 binders scattered throughout four facilities.
They had a lot of inventory traffic to manage, and physical paper trails were not feasible at the scale with which they were doing business. The company needed a robust tool and disciplined processes for managing inventory.
Additionally, inconsistent container label formatting and unreliable quality made it increasingly difficult to manage processes from buyer to buyer.
Looking for a Better Way
Newman Technology realized that they needed a modern-day solution for production accuracy and accountability. The company could no longer accept incorrect inventory quantities, inconsistent packing slip information, or incorrect bills of material. Employees needed simple, rapid solutions to replace outdated methods of verifying shipments and validating invoices.
Solution
Plex’s Manufacturing Execution System (MES).
After going live with Plex in 2006 Newman Technology was familiar with Plex product offerings and was excited to start using Plex MES, a full visibility solution that would ultimately increase connectivity and provide a real-time view of the entire production lifecycle.
Streamlined Communications
With the help of Revolution Group, Newman Technology implemented Plex in a phased approach over 18 months. Plex MES helped facilitate communications between Newman Technology and its suppliers, and it cut out the excess paper in Newman’s operations.
Plex automated and accelerated Newman Technology’s processes and enabled alignment across functions both within the company and with suppliers and customers outside the company’s walls. In a fast-paced and dynamic manufacturing environment with more than 700 employees, four facilities, 220 work centers, 330,000 components received daily, and 100,000 parts shipped out daily to 15 customer locations, tight coordination and production efficiency are paramount.
The automated, paperless nature of Plex saves time and effort, and helps with ISO compliance.
Result
Getting Results
With Plex MES, Newman Technology now has everything in one place and all facilities are connected. As orders come in, all items are scheduled on the production floor, allowing employees to see each job configuration in detail. They can then schedule orders to suppliers, allowing inventory to drop to minimal levels while giving local suppliers the ability to make deliveries as needed without decreasing inventory accuracy.
Newman can also look at scheduled jobs and available inventory, as well as what needs to be ordered, giving them the ability to quickly locate any discrepancies and communicate those to the appropriate employees. Also, as an ISO-certified company, the scheduling of all audits and documentation tracking are completed in Plex.
The company completes two physical inventories per year with spot checks in between. Prior to Plex MES, this process could take multiple days given the amount of preparation involved. Now, these inventories can be completed in four to six hours.
“It took very close to a day, at least, if not multiple days to complete physical inventories, because there was so much work that went in behind it. It was a nightmare,” Luke Abrams, IT Systems Manager.
Since the addition of Plex MES, management at Newman Technology can walk through the production floor and see scrap and production rates live. This has been a game changer, providing accuracy in consistently changing data to ensure automated workflow and remove human error. Additionally, with the use of Plex throughout the COVID-19 pandemic, Newman employees were able to view demand and customer orders from remote locations. As conditions improved, Plex MES also allowed for staggered shift scheduling, keeping employees safe while allowing business to continue.
Automated Processes
Newman employees also have a better solution for documenting correct part numbers and quantities on labels, which makes for a vastly improved inventory system. When quality issues arise, Newman Technology can now use Plex’s Production Monitoring solution to control the flow of information and increase efficiency. With unique product serial numbers, employees can track and record each product through production and conduct thorough reviews if necessary, using the information collected with the system. This has improved overall quality tracing and made for rapid decision-making.
Real ROI
Newman Technology improved and accelerated domestic inventory management — going from 12 to 20 turns per month for parts used every day — and reduced manpower in the processes.
Plex also provides Newman with better internal auditing. The on-demand software delivers a strong document control system with electronic documents in one location and automatic revision tracking. Every employee has access to the documents online and receives alerts for changes and actions as soon as they are needed. Shop floor employees can better plan and adapt their tooling in response to upcoming changes.
The result is a paperless system that has saved money (and trees). It has helped Newman Technology conform to all aspects of ISO, which is critical in today’s manufacturing world.
Looking to the Future
As they look toward the future, Newman Technology is excited to finalize the Plex MES implementation at their latest site in Mexico. With the several US-based sites fully implemented, the knowledge base built up within the internal team is being used to help get each site up to speed. Given that each department has different needs, Newman has been able to utilize department leads from other sites to help progress implementation at their Mexico site.
Published December 11, 2023