Brian Patrick is vice president, engineering, for Pearson Packaging Systems, a provider of comprehensive automation solutions and a Gold-level OEM member in the Rockwell Automation PartnerNetwork. From individual equipment to integrated systems, Pearson Packaging Systems has deployed more than 22,000 machines worldwide.
Reduce Lead Times with Digital Twin Software
As part of its lean manufacturing process and effort to reduce lead times, Pearson Packaging Systems uses Emulate3D™ digital twin software from Rockwell Automation to support the design, build, test and commission all of its machines virtually. Prior to using Emulate3D, the company performed these same tasks right on the shop floor where the machines were built.
“We were looking for ways to have more machine turn. Machines sitting on the floor don't make money. The end customer wants their machine. They want to be able to run it,” Brian explains. “Emulate3D gives us the ability to build in the digital world and be ready for the machine when it hits the shop floor. It's all about lead time and doing everything that we can to deliver to the customer on the date expected.”
Watch the Video
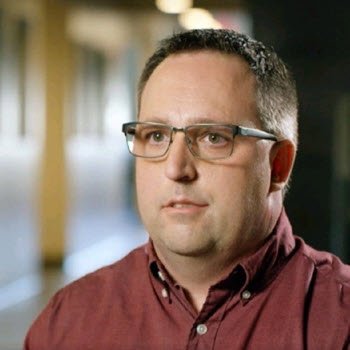
Brian Patrick
VP of Engineering, Pearson Packaging Systems
Virtual Technology Increasingly a Customer Expectation
Pearson Packaging Systems has created an expectation shift for packaging industry customers: at least some level of virtual machine design, build, and testing has now become the market expectation.
“Customer are asking us asking upfront, ‘What would you do to solve this problem? How will the upgrade work?’ They’re concerned about downtime. They don’t want us to show up at a site, bring the line down and not be able to bring it up in a very quick turn,” Brian says. “We’re able to show them our concept first without having a physical machine.”
Pearson Packaging Systems also uses Emulate3D as a service tool that allows them to virtually troubleshoot issues when customers call.
“We’re able to provide immediate support. We load the code from the machines in the field and put it through Emulate3D first, so we have the digital twin in front of us,” Brian explains. “Often times we can avoid deploying expensive resources, like engineering, just by being able to see what the customer is seeing at the other end.”
Enhancing Workforce Productivity and Training
In fact, one of Brian’s top goals when first evaluating Emulate3D was the desire to keep engineers in the building.
“We’re all working in a resource-constrained environment with labor and supply chain challenges,” he says. “Emulate3D allows us to do so much more with our engineers here rather than deploying them to the field.”
The software has also become a useful training resource for when Pearson Packaging Systems onboards new engineers or transfers them to new product lines.
“They can review. They can test. They can basically do everything virtually that they need to before actually touching machines,” Brian says. “Emulate3D has become an everyday tool we rely on as often as CAD. It's great to see how much our engineers want to use it.”
Published April 4, 2023