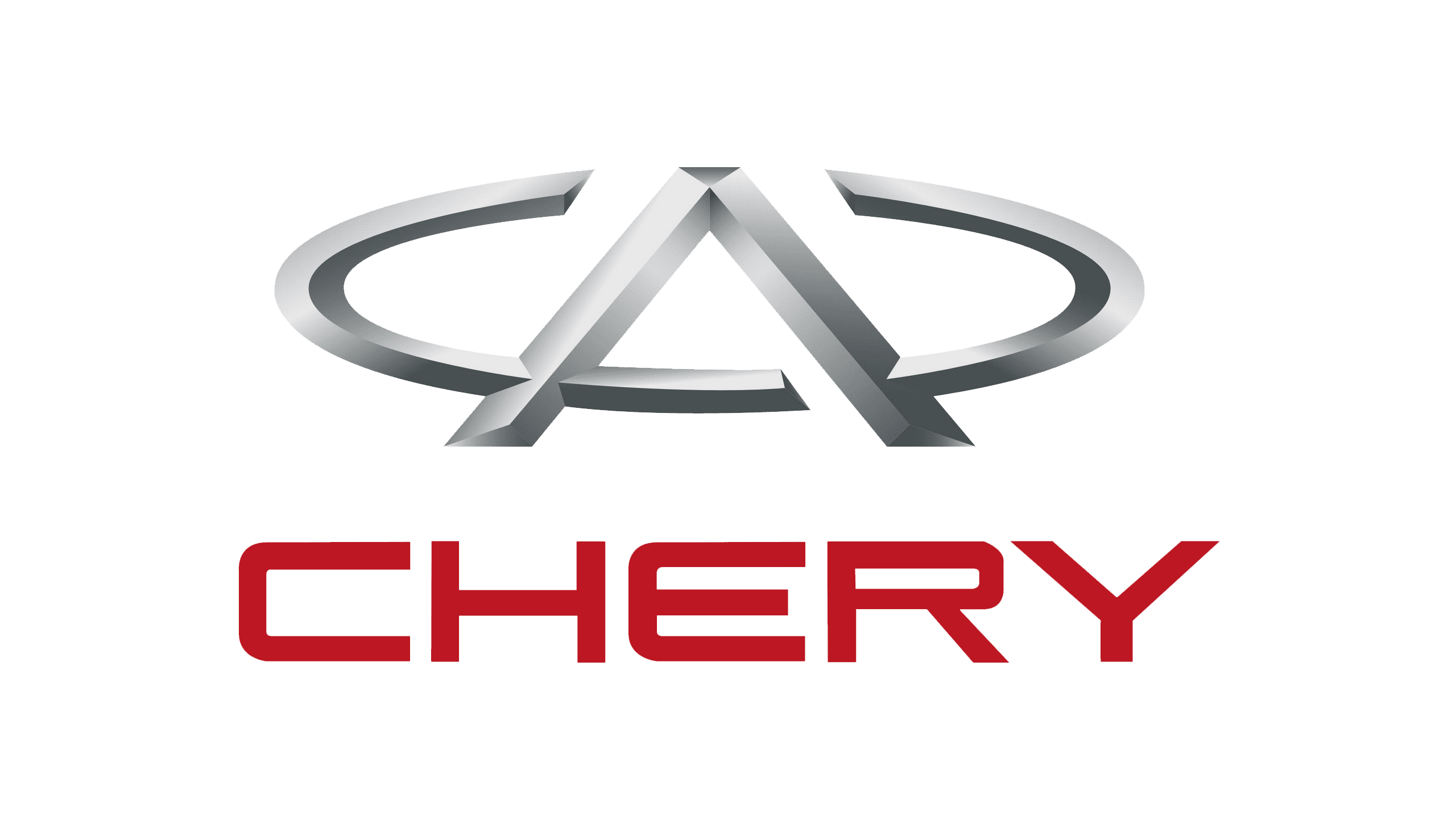
Chery Automobile Co., Ltd. is a globalized automobile brand located in China. Founded in 1997, Chery has R&D centers across the world and a team of more than 5,500 employees devoted to innovation. More than 11 million consumers worldwide own a Chery vehicle.
- Data silos
- Lack of visibility to equipment, control and monitoring data, as well as MES and ERP information. No connectivity between OT and IT data.
- 30% increase in production tempo
- 10% increase in production capacity
- 30% decrease in labor costs
Challenge
Significant changes are coming to the 140-year-old automotive industry. Battery technology and charging infrastructure continue to evolve, and traditional automobile manufacturers are under growing pressure to enter the EV market. Simultaneously, consumers are increasingly expecting the ability to customize a vehicle to make it best suit their needs. The competition in the industry is fierce.
In response to these challenges, automobile manufacturers are launching new models faster and faster, shortening time to market, strictly controlling manufacturing costs, and adding the ability to customize products. These changes require more advanced automobile manufacturing technology, which is turning into a competitive advantage itself.
Chery Automobile, a leading manufacturer of Chinese automobiles, has brought to life its "Digital Chery" strategy in the past few years by building two intelligent and connected super factories in Anhui, China. As Cherry’s products grow smarter, so do its manufacturing operations.
Solution
In the era of change, manufacturing technology is a competitive advantage
Chery Automobile knew that the key to achieving connectivity and operational visibility was aggregating and contextualizing data from traditionally siloed areas of the business. From the OT side, they needed visibility to equipment, control and monitoring data. From the IT side, they needed visibility to MES and ERP information.
Automobile manufacturing involves tens of thousands of parts. Assembly and production processes are complicated, robots are used in many places, and customized special equipment is often required to enable automated production. Collecting and aggregating data from all these sources can be a challenge. Chery wanted a platform that had Kepware industrial connection software. The platform had to have built-in drivers to make connectivity to devices simple. It also had to support common protocols like OPC UA, MQTT, REST, EFM, ODBC or SNMP.
After conducting much research, Chery Automobile chose the Rockwell Automation FactoryTalk® InnovationSuite Internet of Things platform.
FactoryTalk InnovationSuite Enables Intelligent, Connected Super Factory
Today, FactoryTalk InnovationSuite aggregates and contextualizes data from disparate devices, applications, and data sources across Chery’s super factory. It provides a single source of truth where maintenance technicians can securely access data from plant field devices and operators can access data from the production line.
For Chery, it was also important that FactoryTalk InnovationSuite could connect to Andon – the visual display management tool the company uses to issue alerts and trigger events when operations are outside of expected parameters.
It was also important to Chery that FactoryTalk InnovationSuite was able to connect to the factory’s energy management system. By establishing this connection, Chery is now able to track energy consumption for each piece of production equipment and run analytics on this data to optimize future operations.
To better connect production with operations, Chery also decided to implement FactoryTalk® ProductionCentre®, which enhanced the capabilities of the factory's original MES system.
Result
Technology and expertise connect to produce results
For this project, Rockwell Automation acted as the general contractor, providing Chery with consultation, project research, system blueprint design, functional design of the target system, and full life-cycle services such as project implementation, system development, online commissioning, and acceptance.
Less than 3 months after implementing the dual-platform architecture of FactoryTalk InnovationSuite and FactoryTalk ProductionCentre, the production tempo at the super factory has increased by 30%, with a brand-new vehicle rolling off the assembly line every minute.
Fuel vehicles and electric vehicles are produced together on the same line. This increases production capacity by 10% and brings agility to product customization.
Completely automatic production allows Chery to stay on target with their aggressive goals of zero product anomalies, zero work-in-progress inventory, low energy consumption, and zero emissions.
In addition to production benefits, going paperless and increasing operational visibility has reduced Chery’s labor costs by more than 30%.
In this factory, digitalization has made mass customization a reality. FactoryTalk InnovationSuite played a central role, allowing the industrial Internet to truly empower the automotive industry to move towards high-quality development. Chery Automobile’s intelligent super factory, built on FactoryTalk InnovationSuite, has created a benchmark for smart manufacturing in the entire automobile industry.
Published September 20, 2023