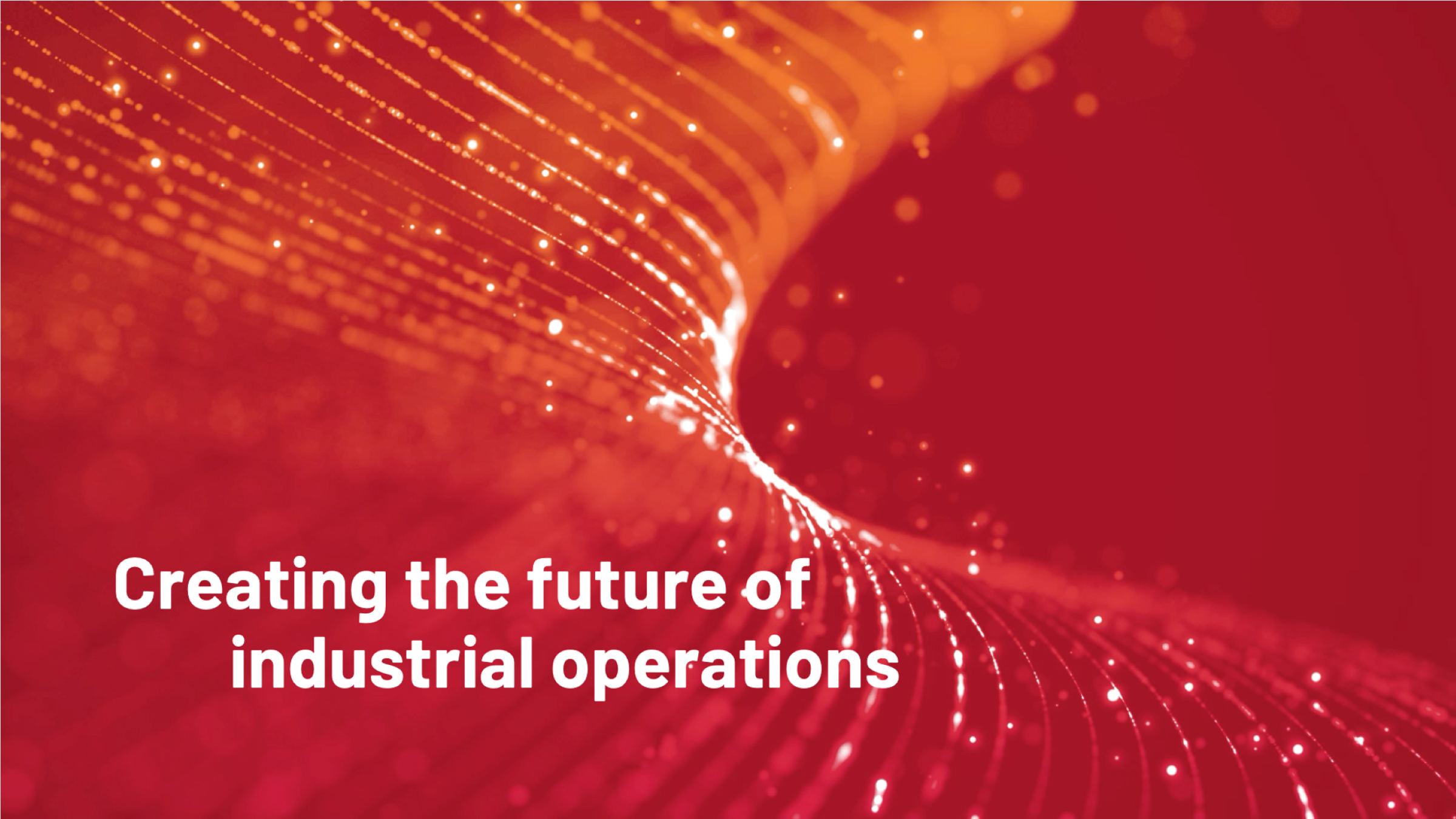
Across the globe, manufacturers are moving towards autonomous operations. With rapid advancements in artificial intelligence (AI), robotics, and the Internet of Things (IoT), autonomous manufacturing is providing businesses with increased efficiencies, enabling them to be more resilient and adaptable as they operate in more complex environments.
At our recent Automation Fair 2024, Rockwell Automation’s chief executive officer, Blake Moret, highlighted that autonomous manufacturing is about “adding additional elements of autonomy” into existing workflows. It’s about putting systems in place that can learn, using AI, to add value by being a part of existing workflows.
For instance, inline quality control systems can detect and address issues during production, avoiding costly batch rework. AI engines also optimize processes in real-time to reduce downtime and ensure seamless operations, often without manual intervention.
Echoing his sentiments, chief technology officer Cyril Perducat described the convergence of AI with integrated robotics and software-defined automation as a “unique inflection point for the industry,” and rightly so.
Autonomous manufacturing is about how people can work differently, as they learn how to use AI and automation to elevate the work they do. The ability to analyze data, predict outcomes, and quickly adapt to changing environments will give businesses that have made the pivot an edge. These capabilities will enable manufacturers to improve processes and operational efficiency, while addressing the challenge of finding and retaining a skilled workforce.
Stepping into a new era of manufacturing
In our latest State of Smart Manufacturing Report, almost all the manufacturers surveyed said they use smart manufacturing technology like collaborative robots (cobots), autonomous mobile robots (AMRs), and autonomous guided vehicles (AGVs) to augment their workforce. Emerging technologies such as AI and wearable technology also ranked highly on the list of investment areas.
Based on these results, it’s clear that manufacturers are keen to explore these solutions. Recent advancements have made it easier to integrate these technologies into workflows, acting as enablers to drive greater efficiencies and positive impact.
A principal area of focus for Rockwell Automation over the next few years will be in production design, control, and logistics. Our autonomous material handling solution, OTTO, has already been transforming production logistics with flexible and nimble autonomous operations. Using two OTTO AMRs, global packaging leader Mauser improved throughput by 600% and was able to reallocate three workers to higher value-added roles. We’re also planning to strengthen our edge and cloud technologies, whereby edge can serve as the data broker for information in the cloud, to enable a more resilient bridge between the two.
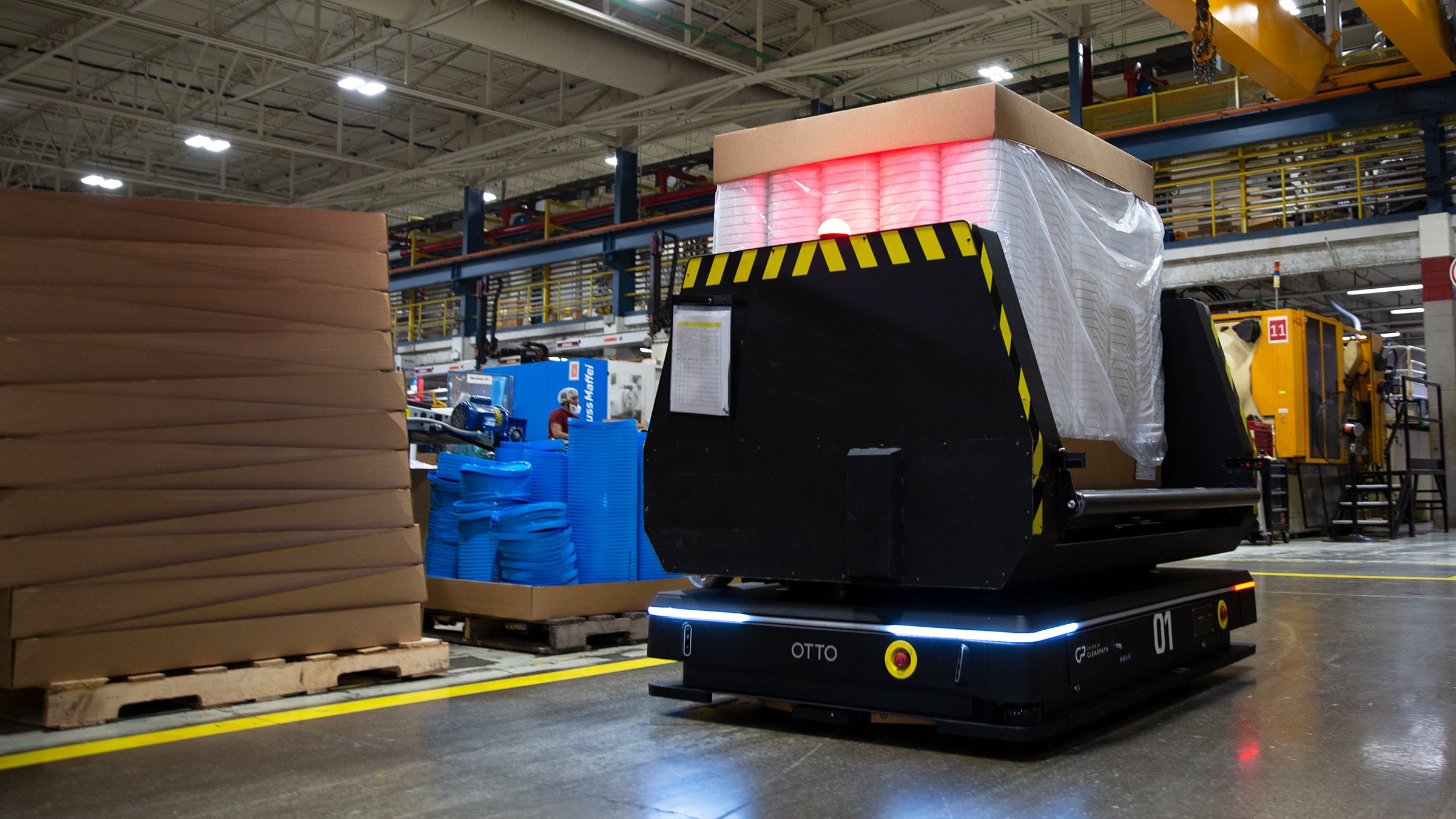
In the area of design, digital twin software like Emulate3D is helping manufacturers build and simulate full-scale operations before actual implementation. This helps teams identify any roadblocks or defects for troubleshooting ahead of time, saving valuable time and resources. Kenmec Mechanical, for example, identified potential issues in its production lines and machine designs with Emulate3D. As a result, the team could implement solutions in real-life with confidence, improving efficiency and overall precision. Meanwhile, ECM Technologies was able to cut its commissioning time by 50%, through virtual commissioning, throughput simulation, and industrial demonstration.
Software like FactoryTalk DataMosaix helps pull together siloed data to decipher and make sense of it so that it can be used for root-cause analysis or predictive analytics. Companies like InControl Systems that deliver process automation systems, have been able to tap on FactoryTalk DataMosaix to accelerate the delivery of digital solutions for clients and deliver new capabilities.
Together with FactoryTalk Analytics VisionAI, manufacturers can run advanced defect detection with specialized AI models that are trained, so that even the subtlest and rarest possibilities for anomalies are identified. One of the key parts is its implementation, as it uses a no-code approach, making it a user-friendly tool for those with little to no coding experience too.
These are just a few ways we are already moving towards industry autonomy and software-defined operations.
Autonomous manufacturing goes beyond just efficiency and business bottom lines. It’s about creating more resilient, agile, and sustainable workplaces, by using technology to support humans with refined intelligence.
This article was originally published on Scott Wooldridge’s LinkedIn here.