Success in manufacturing has always been tied to your capacity to innovate quickly. Imagine if you could gather each party and their data, around the world, together in the cloud with everyone collaborating early and often in the design process? The digital thread makes this possible. It enables seamless data flow throughout the organization, which leads to improvements and benefits throughout the entire operation.
From collaborating in real time across the value chain, to validating new lines and processes virtually, simplifying data science and increasing your manufacturing flexibility – the digital thread can help you reimagine your ambitions.
While an asset’s lifecycle is linear, the best digital thread is a digital feedback loop. This end-to-end solution enhances decision-making through visibility into an asset’s past, present, and future state. Collaborators across the value chain can easily leverage insights generated by upstream and downstream stakeholders.
Early adopters of digital thread methodology are surging ahead in productivity and innovation. They are moving from siloed systems and business functions to an enterprise connected with the digital thread. However, any company that has tried to create a digital thread knows it can be difficult to integrate data across disparate tools and systems.
Recognizing the inherent challenges in creating a digital twin, a group of leading vendors have joined forces to create a better, less disruptive alternative. Their approach involves integrating their digital technologies and services to reduce the work you need to do to connect tools like CAD packages, simulation software and automation design software. This can help you create a digital thread while allowing engineers to keep tools that they use and prefer today.
Expanding the possibilities
A digital thread expands what is possible in your business using digital engineering. For example, it can connect a new machine’s CAD model to control system code. This allows you to use simulation software to perform virtual controls testing which can help speed up machine commissioning and avoid last-minute surprises. Going a step further, you can simulate how the new machine will perform as part of a larger system to help identify issues like bottlenecks.
A digital thread can also be used to create a digital link to your products, allowing you to monitor their health and performance once they are in the hands of customers. This can improve your ability to service products. It can also help inform customers of future product changes or the development of new products.
Realizing opportunities like these can be greatly simplified with an open, integrated ecosystem of digital technologies and services. This allows you to spend less time integrating technologies and standardizing data across your industrial operations and the business functions that are adjacent to them. In addition, because the vendors involved in this effort are leaders in their respective field, you are likely to benefit from keeping some or all of the engineering tools you already use today.
This reduces your need to buy new technology and any disruption to how workers to their jobs. It also reduces the battles you need to fight to connect data across your operations.
One major consumer-good producer is using an ecosystem of digital solutions to help optimize a new product line and get it up and running faster. The company chose best-in-class tools that, while provided by different suppliers, are integrated and allow engineers to use digital engineering workflows to develop the new line.
For example, the company is pulling design data from its CAD package into industry-leading simulation software to create simulated models of some of the more complex aspects of the line. Then, the company is pulling those models into a separate emulation software to test them with the controls code and virtually commission the line.
Doing this work virtually and seamlessly thanks to integration between the different tools will help reduce engineering time and onsite commissioning time for the new line.
To help simplify implementation and enhance quality of digital initiatives across industries, Rockwell Automation created the Digital Partner Program. Working with companies like ANSYS and EPLAN, we can help you solve complex engineering challenges and create a digital thread that can help you be more productive not only at the design and development stage, but also in your operation and maintenance activities.
Your next competitive advantage
Speed is crucial to maintaining your competitive edge. Today’s customers expect increasingly personalized products while new competitors innovate at record rates. World class manufacturers are investing heavily in digital transformation initiatives. A holistic digital strategy, powered by the digital thread, helps manufacturers move faster by removing friction between disparate teams and systems.
‘The biggest takeaway from the performance of digital versus nondigital industrial organizations is how the performance gap increases over time.’
- IDC
Digital transformation can deliver many advantages to your systems and business functions including:
Accelerate time to value with enhanced collaboration: Digital transformation delivers the ability to collaborate in real time across the value chain. It removes dependencies by bringing every stakeholder together in real time from the start. It also allows you to emulate processes and manufacturing changes virtually and has been shown to accelerate commissioning by as much as 50%.
Empower your workforce with digital augmentation: Benefits of digital transformation include being able to leverage expertise anywhere with remote collaboration. Manufacturing expertise can be scaled across the workforce with augmented reality. Operator effectiveness and safety can be increased with high-fidelity training and on-the-job instruction. In fact, digital transformation has been shown to decrease training time by up to 75%.
Increase operational efficiency and agility: By automating IT/OT convergence you can harvest scalable insights with an information model optimized for the digital thread. Optimizing operations by connecting the plant to the digital content created by other business functions delivers ability to accelerate data science time to value by up to 70%. It also increases manufacturing flexibility and agility by removing friction between enterprise systems. It enables lights out manufacturing by allowing you to download and execute orders, at any plant and line around the world, without human intervention.
The digital thread in action
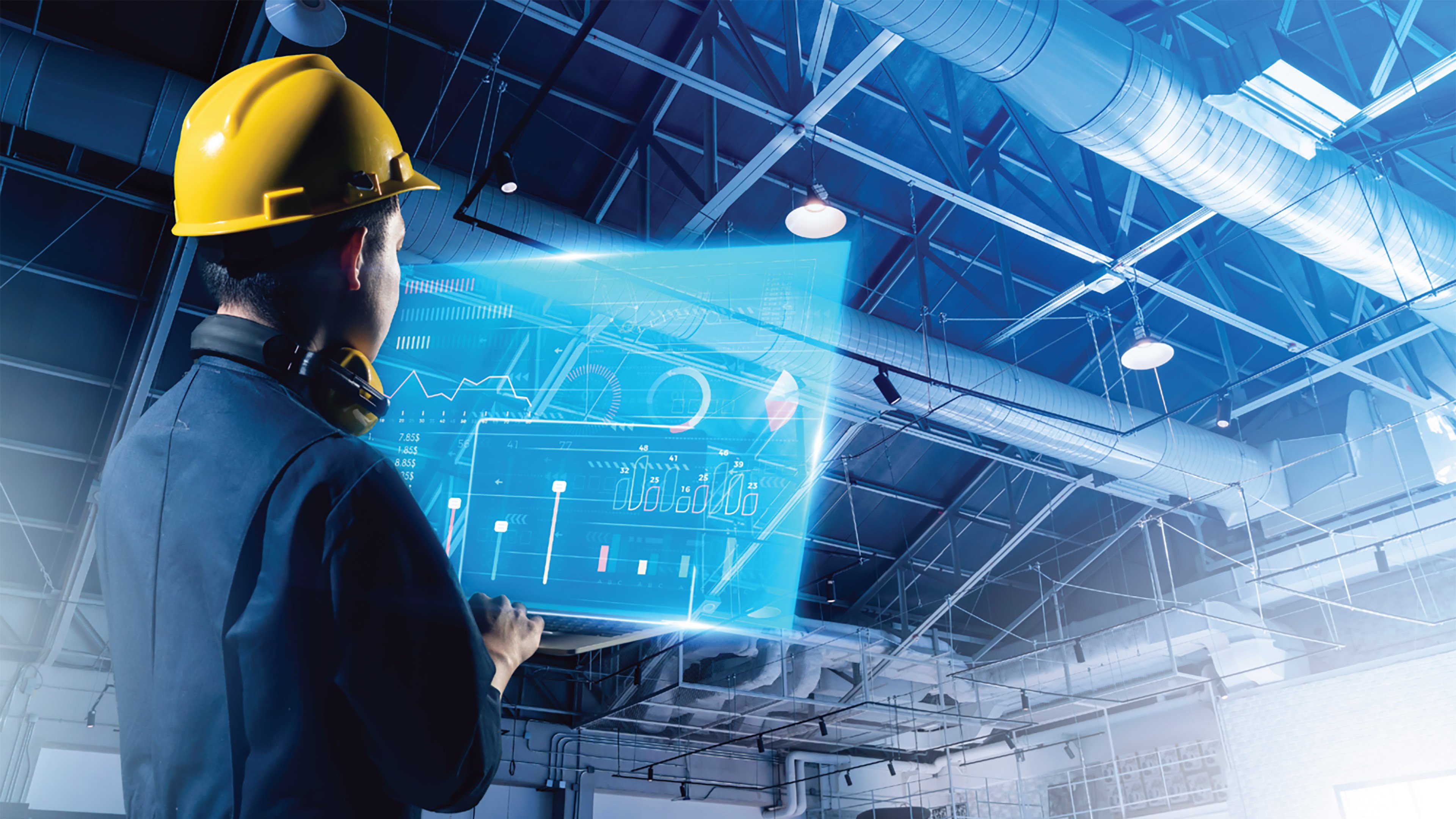
The story of Rockwell Automation’s own digital transformation journey has pushed beyond the initial stages of the journey to reach a state of continuous improvement – so they can remain on the forefront of whatever comes next. As both a global manufacturer and leading technology provider, Rockwell Automation is uniquely positioned to drive their own digital transformation.
As a manufacturer, about one-third of their 23,000 employees work at 20 global manufacturing plants and manage a product catalog of nearly 400,000 SKUs. And as the world’s largest company dedicated to industrial automation and digital transformation, they help companies around the world improve processes, reduce inefficiencies, and increase productivity.
The Rockwell Automation manufacturing arm embraced digital transformation before it became a buzzword. They started by combining multiple, disparate systems into one enterprise resource planning (ERP) system that could manage many others around the world. In parallel, they rolled out a MES as its centralized system of record – and spent the next several years going plant by plant to connect factories, processes and people to a single MES.
This delivered high-level IT/OT convergence and gave them the foundation to standardize workflows and processes across all facilities. Rockwell Automation established a globally standardized approach for connecting their factories around the world and set the stage for the next wave of digital transformation.
The results were significant. Rockwell Automation lowered their total cost of ownership, reducing inventory days from 120 to 82 and capturing 30% in annual capital avoidance. They have accelerated their time to market, with supply chain deliveries now up to 96% and lead times cut in half. Additionally, the company estimates it has experienced a 4-5% annual improvement in productivity.
Although well into their own digital transformation and yielding significant improvements as a result of their factories being connected with a single connected system across the globe, Rockwell Automation asked the hard question: what’s next?
Rockwell Automation wanted to ensure it was realizing the full benefits of their connectivity by driving standardization across operations. To do this, a team of connected enterprise specialists focused on key use cases designed to further optimize factory assets and empower their workforce with digital tools and resources.
Optimizing people, products & processes
FactoryTalk InnovationSuite, powered by PTC was employed by Rockwell Automation to build and advance to the next stage of their transformation. Across six global facilities, the suite infused edge-to-enterprise analytics, machine learning, IoT, and augmented reality directly into their industrial operations. The technology provides a comprehensive and effective way for manufacturers to optimize their people, products, and processes, and to accelerate their industrial transformation.
While the technology on its own has enormous potential, without specific use cases that can scale to multiple scenarios and facilities, the value can be limited and never hit the double-digit impact Rockwell Automation was looking for. To ensure a successful rollout, Rockwell Automation identified use cases that would have the greatest benefit to their global operations and employees. By piloting the use cases in each location, they were able to facilitate a digital culture shift and help employees develop the right skillsets. At a high level, these use cases span from intelligent asset optimization to workforce productivity and enterprise operational intelligence.
To create an intelligent approach to asset management, the operations team leveraged real-time monitoring, diagnostics, and predictive and prescriptive analytics to gain valuable visibility and better understand the health and diagnostics of their machines. Equipped with these powerful monitoring tools, they were able to avoid unplanned downtime and maximize asset utilization. The team implemented three use cases in this area:
Throughputs
Rockwell Automation leveraged powerful real-time monitoring and analytics tools to both increase the quantity of output and decrease the labor cost per unit produced. With detailed data analysis of the production process – specifically around time between units and time per step – Rockwell Automation was able to optimize throughput for a new product in high demand. At one facility, double-digit results include a 33% increase in labor efficiency, a 70% increase in outputs and a 50% reduction in training time.
At one facility, double-digit results include a 33% increase in labor efficiency, a 70% increase in outputs and a 50% reduction in training time.
Predictive maintenance
Rockwell Automation uses 35 injection molding machines of varying complexity and age, which made it difficult for them to efficiently determine machine status and prevent downtime. Leveraging IoT technology to collect vital, real-time information across legacy machines, they created a unified view of their factory floor, and achieved an 8% improvement in productivity. This enables them to enhance quality control, improve machine uptime, and ensure maintenance needs are met based on machine utilization.
Analytics
In order to reduce long production times on ball grid arrays, the team piloted a new machine learning test good and bad ball grid connections. They created a 3D profile of the paste applied to boards, which will enable them to quickly determine whether there was a bad paste profile. As a result, they were able to detect issues earlier in assembly, reduce time to fix from hours to minutes, provide better quality assurance, and reduce paste related defects by 51%.
Through each of these uses cases, Rockwell Automation was able to optimize asset efficiency, reduce machine downtime, and increase throughput to satisfy customer demand. “Now we have data sources connected and identified, and we can create new models to further improve our processes,” says Lion Moeliono, IT Manager, Global Plant Systems at Rockwell Automation.
A digital workforce
Rockwell Automation sought to empower their workforce with digital tools – not only improving productivity but also creating an environment where employees feel valued for their accomplishments, day in and day out. They implemented four targeted use cases to better empower their workforce:
Work queue visibility
By combining data from IT and OT sources and visualizing it together, Rockwell Automation realized a 75% reduction in line starved-condition downtime due to lack of materials, which enabled operators to optimize their work.
Standardized performance reporting
The team needed a clearer way to see the impact of downtimes on hourly performance, so they developed a common KPI dashboard for use across all plants. Combining disparate information from scheduling systems, SAP, MES and other sources, the configurable and modular dashboard enabled workers to better visualize performance trends, make data informed decisions and increase labour efficiency by 13%.
AR-guided wiring & training quiz
Ensuring employees could wire effectively had become an increasing challenge due to turnover. Additionally, there was no objective means to measure success, resulting in risks to quality and safety. Using AR technology to deliver a better training experience in an engaging way, Rockwell Automation was able to train employees and simultaneously measure competency to identify skills gap.
AR-guided standardized work instruction product transfer
Relocating plants between Switzerland and Poland required teams to transfer critical and detailed knowledge across countries and languages. The team in Switzerland began recording work instructions using AR technology, breaking down tasks into step-by-step instructions with pictures, video, and voiceover and reduced training by 30%.
A smart supply chain
When Rockwell Automation experienced a jump in demand for component parts for electronic assembly and had to procure material from an external source, they quickly discovered that non-conforming parts had been introduced into their supply chain. Leveraging the intelligence from FactoryTalk MES, unified IT and OT systems, and standardized processes, they were able to identify the issue and trace it through their supply chain to prevent any more problems in the future. This capability can reduce recalls by 80% or more, in any given situation.
Rockwell Automation reduced recalls by 80% or more.
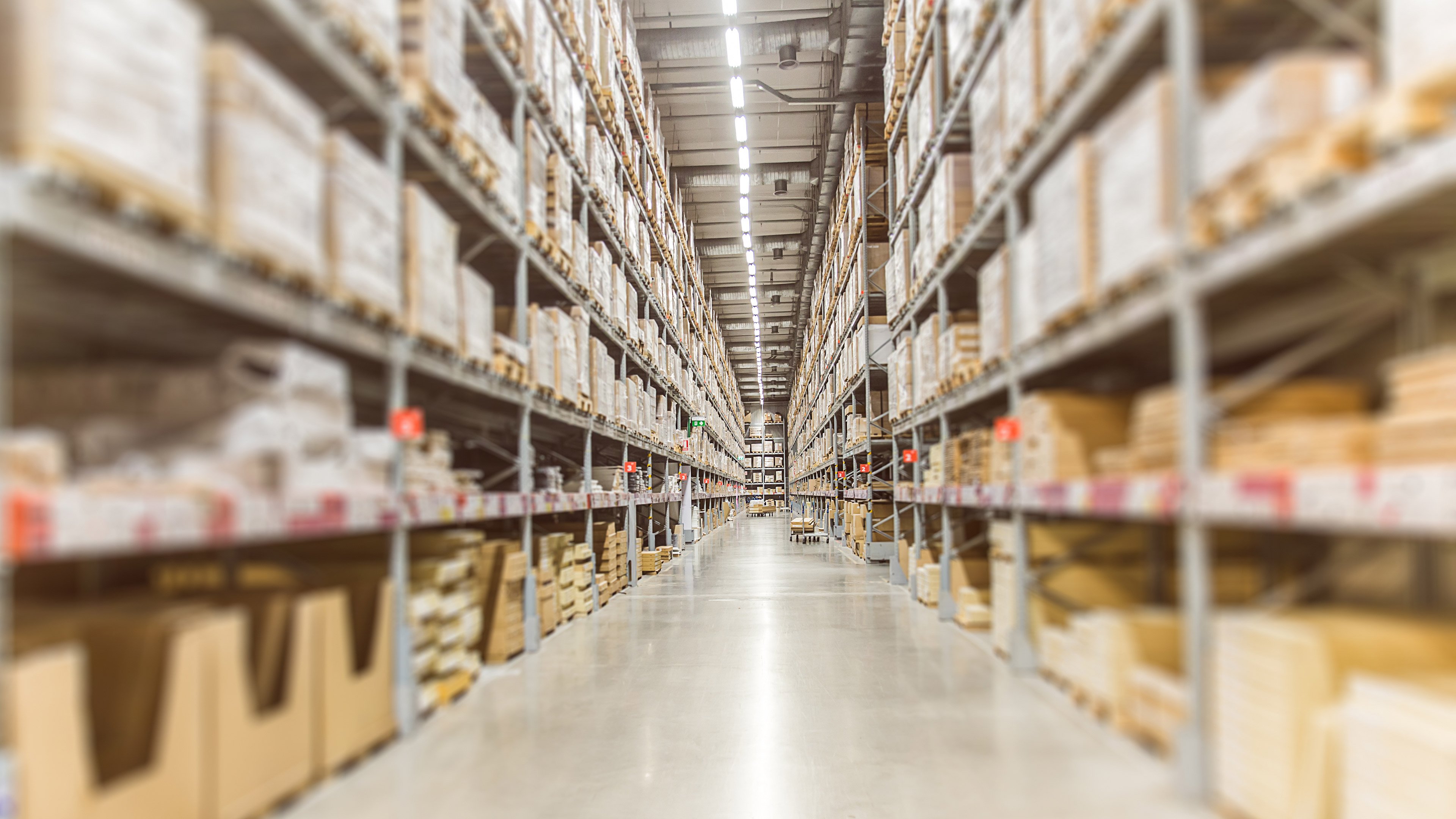
Building on these learnings
Looking forward, Rockwell Automation is building on these recent learnings. They are challenging themselves on how they can drive further improvements for workers, equipment, and processes, with the goal of creating even more customer and employee value.
They are arming employees with better training by leveraging breakthrough AR technology and providing opportunities for higher level responsibility as more manual tasks become automated. They are protecting their assets by turning data into improved prediction and prescription capabilities to manage machine performance and maintenance at a new level of precision.
Every day, they are learning more about the capabilities of their own technology, only limited by their imaginations and time it takes to continuously improve and transform, one step at a time.