Soren Rasmussen is Managing Director for Green Hydraulic Power, Inc. (GHP), North America’s leading supplier of variable frequency drive solutions for industrial hydraulics. Parent company MJC Engineering & Technology, a custom machine tool builder, started GHP to meet the growing demand for these emerging types of hydraulic systems.
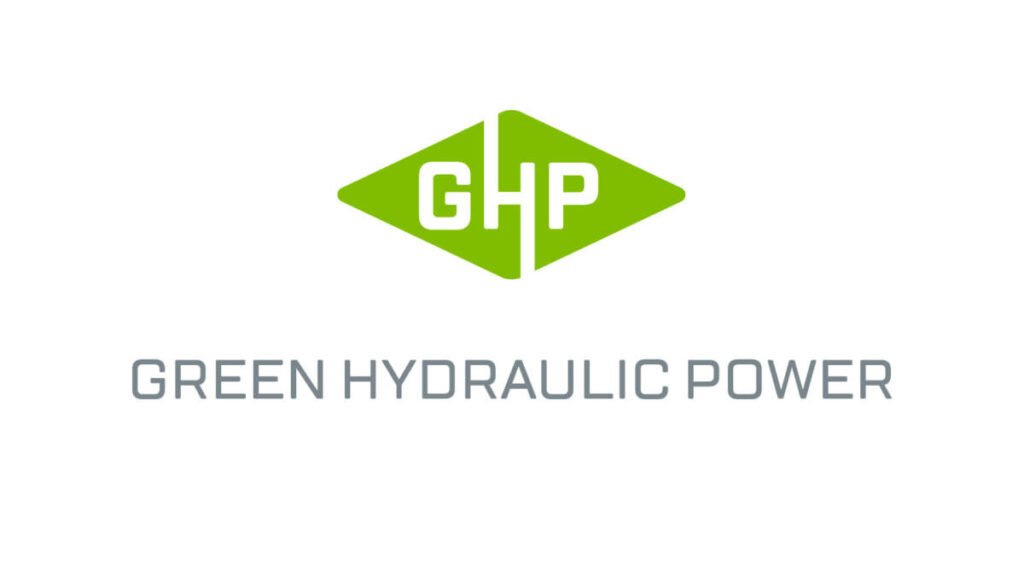
Green Hydraulic Power, Inc. (GHP) is North America’s leading supplier of variable frequency drive solutions for industrial hydraulics.
- Systems always on despite use
- Energy waste
- Extreme noise
- Engineered, turnkey system
- On-demand hydraulic pressure and flow
- Allen‑Bradley® PowerFlex® 755 VFDs
- Lower carbon footprint
- Up to 80% energy savings
- Reduce noise emissions by 20 decibels
Challenge
Energy intensive, noisy equipment
Hydraulics power a wide range of manufacturing equipment including presses, expanders, press brakes, machine tools, and material handling machines. According to GHP, electric motors that run these types of equipment consume nearly 25 percent of the world’s electrical energy production. In the US, that percentage is much higher.
“In many manufacturing environments, there’s a lot of dwell time when there’s no action on the production line, so there’s no need for flow or pressure,” Rasmussen explained. “Yet, traditional hydraulic systems run continuously, and at high speeds, so that they’re available when needed. That wastes a lot of energy and other resources.”
Conventional systems are also extremely loud, which can impact worker safety.
Solution
On-demand hydraulic pressure and flow
Using variable frequency drives, GHP has developed turnkey systems that provide hydraulic pressure and flow only when needed.
“With these drives, we basically reduce the motor speed. When there is no need for flow and pressure, we slow it down,” Rasmussen said. “For example, for motors that usually run at a full speed of 1750 RPMs, we slow it down to 300 RPMs, which saves a lot of energy.”
The systems include Allen‑Bradley® PowerFlex® 755 VFDs.
“We started using Rockwell Automation drives a few years ago. They’re very easy to work with,” Rasmussen explained. “The engineers are excited every time we make a machine with a Rockwell Automation drive. They’re intuitive and easier to program.”
System requires little to no cooling
Because hydraulic pressure and flow are used only on demand, GHP’s patented systems also generate less heat. So, little to no cooling is required.
“A lot of energy is saved that way as cooling can be energy hungry as well,” Rasmussen noted. “We’ve even been able to eliminate cooling towers in some factories.”
Result
Substantial energy savings and improved workplace safety
One of GHP’s customers, an international metals fabricator, is replacing its current hydraulic equipment with GHP units as part of its sustainability strategy to lower its carbon footprint.
“They operate 24/7. We created a baseline of their current energy use,” Rasmussen said. “We estimate once our new systems are installed, they’ll see an energy savings between 50% to 75% on equipment that’s running a 100-horse motor. That’s substantial.”
Overall, GHP’s VFD hydraulic systems typically use up to 80% less energy than conventional systems and dramatically reduce noise pollution leading to a safer and more productive workplace. GHP units lower noise emissions on average by 20 decibels. No hearing protection is necessary while working on or around the equipment. Operators are better able to concentrate and communicate with coworkers resulting in higher productivity with less fatigue.
“Noise is a huge problem in factories. Whenever we install this type of equipment, most of the feedback is about the noise reduction,” Rasmussen explained. “You can actually stand next to our machines and carry on a normal conversation.”
Published October 10, 2024