The life sciences industry has found itself at the heart of disruption in response to the COVID-19 pandemic. Challenges with global supply chains, vaccination roll outs and healthcare infrastructure has transformed the risk landscape and made life sciences companies rethink their approaches to technological innovation.
Business partnerships have come to the fore as the life sciences industry navigates a new normal. The more you collaborate, the more you can accomplish. Rockwell Automation’s partnership with the Advanced Regenerative Manufacturing Institute (ARMI) is a prime example of this mutual beneficial approach. Both sides bring critical information and technology to every project, including the ARMI Center of Excellence currently in development. Through collaboration, we have moved closer to a revolutionary era of medicine that could save thousands of lives every year.
Manufacturing engineered tissue
There are currently 400,000 people worldwide on waiting lists for organs, and 20 people die each day while waiting for a transplant. For years people have been working to bridge the gap between scientific research and commercial production. ARMI’s BioFabUSA program is working towards making organ transplant lists a thing of the past. The program involves a consortium of more than 170 member organizations working towards large-scale manufacturing of engineered tissues.
Many of the participating organizations hail from the worlds of research and academia, so they know the science behind tissue generation. However, they needed assistance with determining how to scale and automate their processes. Dean Kamen, AMRI’s Executive Director called on Rockwell Automation to help. The partnership grew from there, with Rockwell Automation sharing its knowledge and technology.
Both contributions were critical to ARMI BioFabUSA’s first automated tissue line, which went online in early 2020. An individual could now insert a vial of cells at one end of the line and return 45 days later to inspect the complete bone ligament construct waiting on the other end.
Fully automating the process was an important step on the way to engineering complex organs. The Center of Excellence will help the cause as well, but only because the two organizations recognized an opportunity and found reasons to say ‘yes’ at key moments. Once such moment involved the most basic of requirements – a physical presence.
Seeing is believing
The vast majority of the 170 member organizations are in the early stages of the digital plant maturity model and would benefit from a tangible demonstration of what is possible in later stages.
For years, Rockwell Automation had explored establishing a Center of Excellence in the greater Boston area. Meanwhile, the company’s partnership with ARMI BioFabUSA had made significant strides just 50 miles north of Boston at the organization’s facility in Manchester, N.H.
The converted textile mills have vast square footage, and ARMI BioFabUSA could put it to good use. When the organization discovered Rockwell Automation’s interest in a regional Center of Excellence, it offered to provide space at no cost. It was an unexpected development but one that could help everyone in the consortium move forward.
Having the demo space right next door to a practical, cutting-edge application was an opportunity the organization could capitalize on. Both partners see the ARMI Center of Excellence as a learning tool, educating the consortium’s members about smart manufacturing. When completed, the center will demonstrate the digital transformation journey – from a manual setup to a fully automated facility talking to an enterprise resource planning system.
Making progress
The first steps toward creating that environment happened remarkably fast after ARMI BioFabUSA offered its available space in Manchester. Project organizers received an important nod from Rockwell Automation Senior Vice President and Chief Technology Officer Sujeet Chand in March 2021. Two months later, the center had equipment in place to demonstrate the first two levels of the digital plant maturity model.
ARMI BioFabUSA’s is expanding efforts to achieve its mission. With Rockwell Automation assistance, the organization will install eight more production lines over the next eight to nine months. Every one that comes online closes the gap between the science and the fully automated production of engineered tissue – and strengthens a thriving partnership.
Another winning partnership
The ARMI and Rockwell Automation partnership highlights the value of bringing science and automation together. In another winning partnership, Rockwell Automation is donating its Arena Simulation to nonprofit organizations, governmental organizations, and public health partners to plan COVID-19 vaccination clinics in their communities. The software can be used to monitor patient flow, staffing, shift changes, and maintenance of social distancing guidance for patients in queue.
The software can be used to monitor patient flow, staffing, shift changes, and maintenance of social distancing guidance for patients in queue.
“We recognize this software is a potential game changing tool in helping our healthcare partners to better address supply and staffing needs, and ultimately help expedite the vaccination process,” said Patricia Contreras, vice president of public affairs for Rockwell Automation. “We look forward to joining forces with more hospitals, health departments and other community organizations to help as many people as possible get vaccinated safely, efficiently, and quickly.”
At the start of the pandemic, Norwell Health in New York and ChristianaCare in Delaware both used Arena to manage COVID-19 inpatient care. The software is ideal for vaccine clinic planning because it helps decision-makers understand the flow of systems and the constraints of resources in an environment where every day might bring a different scenario.
According to the U.S. Centers for Disease Control and Prevention, as of Friday March 12, more than 100 million doses of the COVID-19 vaccine had been administered, with 13.5% of adults U.S. population now fully vaccinated. As vaccine supplies change and more people gain access to schedule a vaccination, better and more efficient tools will be needed to support vaccine distribution.
Arena Simulation has been used in healthcare for more than 30 years, helping hospitals and health care systems to plan for improved patient flow and realize cost efficiencies. For more information about Arena Simulation Software, visit the Arena Simulation Software Website.
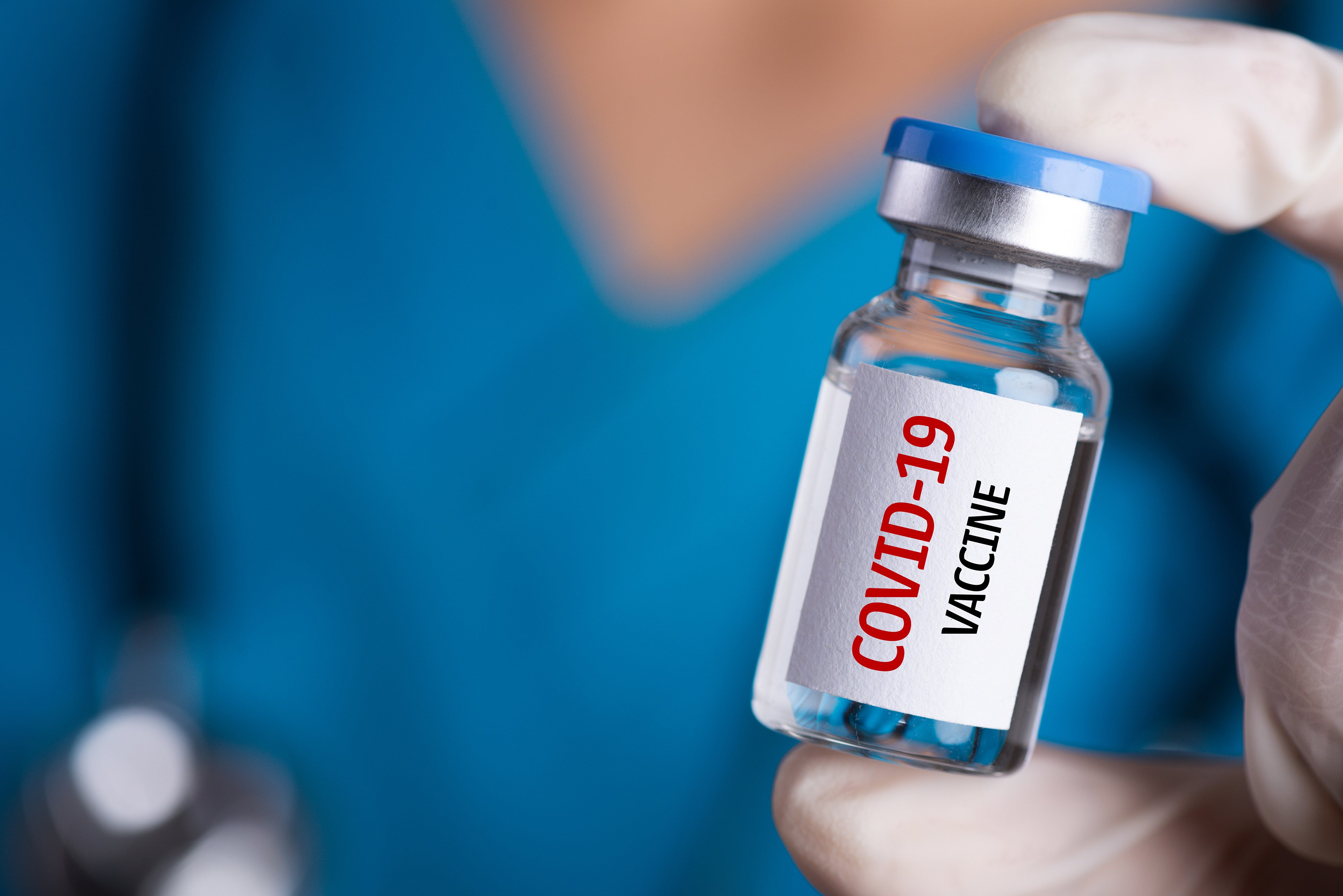
Digitizing healthcare
The COVID-19 pandemic has changed the way healthcare and life sciences organizations operate. Life sciences companies are re-evaluating their supply chains, while consumers are becoming more reliant on digital healthcare solutions.
As we move into this new way of operating, the distinction between science and technology is becoming less defined. These two industries have different knowledge bases and skillsets but as they work more closely together, consumers gain access to higher quality healthcare and improved patient outcomes.