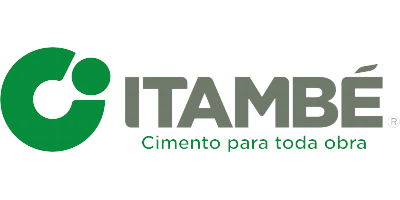
For more than 45 years, Cimento Itambé has been producing and selling cement to the civil construction sector. Itambé cements comply with technical standards and environmental preservation values.
- Optimize kiln productivity
- Increase mill productivity
- Reduce energy use
- Increased kiln productivity by 3%
- Decreased energy use in kilns by 2%
- Increased mill productivity by 5 – 10%
- Decreased energy use in mills by 5%
Challenge
Brazil-based Cimento Itambé has been producing cement for the civil construction sector for more than 45 years. The company wanted to make some improvements to lay the foundation for more growth in the future.
Specifically, Cimento Itambé wanted to standardize operational processes, gain more equipment availability, and use less energy in their manufacturing process. The company turned to Rockwell Automation for help.
Solution
We approached the project in two phases. Phase one targeted operation of the kilns. Phase two was focused on optimizing grinding operations.
Optimizing Production in Cement Kilns
Cement kilns are notoriously difficult to control because they are subject to fuel source variability and uncertainty in raw material characteristics. These variable inputs make it difficult to achieve the precise control needed to optimize energy use, maintain stable operations, and maximize production capacity.
We worked with Cimento Itambé to implement FactoryTalk® Analytics™ Pavilion8® Model Predictive Control (MPC) Technology. Pavilion8 is an intelligence layer on top of automation systems that continuously drives plants to achieve multiple business objectives—cost reductions, decreased emissions, consistent quality and production increases—in real time.
Pavilion8 calculates recommended setpoints for process control loops to optimize control performance in real time. It can understand fluctuating input variables and is able to predict and control multiple process parameters in real-time, while continuously updating control actions based on actual process values.
We were able to use Pavilion8 to optimize Cimento Itambé’s kiln operations while maintaining clinker quality requirements with minimum fuel consumption and a stable temperature. This phase of the project was completed in late 2022.
Reducing Energy in Grinding Operations
Cement grinding is a power-intensive process, and cement producers can struggle to grind and crush their product to a consistent size and hardness. Efficiencies may also vary because of changes in operating habits from shift to shift, and because of changes in clinker grindability or grinding aid composition.
MPC technology accounts for process disturbances and other influences to help consistently grind product to a specific size while maximizing capacity, which minimizes energy costs. The technology responds to different feed properties like hardness, particle size, and grade.
We used Pavilion8 to optimize Cimento Itambé’s grinding operations. Specifically, we wanted to increase mill uptime and decrease the amount of energy used. This phase of the project was completed in 2023.
Result
Increased Productivity and Reduced Energy Use
Cimento Itambé saw success with Pavilion8 during both phases of implementation. In phase one, the company experienced:
- 5% increase in productivity in each of their kilns,
- 2% reduction in the amount of energy used by the kilns,
- more stable temperatures,
- enhanced clinker quality, and
- fewer risks of cyclone blockages.
The company saw similar results with their mills in phase two. After implementing Pavilion8, Cimento Itambé achieved:
- 5% reduction in energy usage,
- increased productivity of 5-10%,
- fewer disruptions in feeding or stops related to high vibrations, and
- access to real-time data, which accelerates decision-making.
For cement producers that are not yet using AI or machine learning, MPC is a logical place to start. It is easy and affordable to implement when the right infrastructure is in place. And it can put a cement plant on the path to more stable production, reduced energy usage and higher throughput in as quickly as a few weeks.
We deliver Model Predictive Control technology through our consulting arm: Kalypso, a Rockwell Automation Business. In addition to access to the technology, customers also gain access to our team of experts who can help identify the best use cases for implementing Model Predictive Control, set it up, and optimize. Kalypso can even perform a study before a project to estimate ROI and make a business case for the project. Contact the team to learn more.
This story was featured in the May edition of World Cement magazine.
Published May 8, 2024