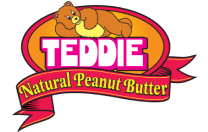
Founded in 1925 by Armenian immigrant Michael Hintlian, The Leavitt Corporation, doing business as Teddie All Natural Peanut Butter, is now a fourth generation family business producing the leading brand of all natural peanut butter in the Northeast, with global distribution to over 25 countries.
- Legacy system
- Lack of real-time operations visibility
- Paper-based quality and production management
- Change management issues
- Increased data access and accuracy
- Improved performance and management
- Easy employee transition
Jamie Hintlian is Chief Executive Officer and COO of The Leavitt Corporation, the family-owned and operated business that produces Teddie Peanut Butter and packaged nut products. Hintlian’s grandfather, an Armenian immigrant, founded the company in 1925. The iconic New England brand produces 75,000 pounds of peanut butter a day.
Challenge
Legacy System Limits Global Ambitions
“We’re the number one, all-natural peanut butter in New England and growing nationally. We have an international presence as well,” Hintlian said. “We have a lot of ambition for growth, but our systems and technology just weren’t positioned for us to achieve our growth objectives.”
Previously Teddie Peanut Butter used a custom built, on-premises ERP system. While Hintlian said it served the company well, the system was no longer supported and lacked the functionality to meet the producer’s ambitions for productivity and growth.
“We were looking for greater visibility to all aspects of the business,” he explained. “Real-time performance data for what's being made, what's not being made, quality management, shipping, financials – everything.”
But, as a company about to mark its 100th anniversary, migrating to a new ERP platform was a major change management concern. Generations of employees work at Teddie Peanut Butter, some of whom have been with the company for decades.
“Moving to new ways of doing things. Not just new methods, procedures and processes, but the technology itself presented obvious challenges and opportunities,” Hintlian explained. “How would line operators and workers who were used to clipboards, checking boxes and writing numbers transition to barcodes, smart scanners, and workstations and be able to operate in a new environment seamlessly?”
Solution
Pilot Prepares Employees for Shift to the Cloud
Teddie Peanut Butter selected Plex ERP and Plex MES.
“Literally every function of the company is now on Plex in the cloud. It runs the entire company, all of our operations – finance, accounting, customer service, sales, marketing, logistics, and quality management,” Hintlian said. “We went from an entirely paper-based environment for production and quality control to an entirely paperless environment.”
To ease employees through that transition, the company set up a large scale conference room pilot for training all functions.
“We had a miniature version of the operation. It got people used to the idea of having to scan things and track material in real time,” Hintlian explained. “This was one of the big changes. Every time you move something, it has to be accounted for and this was a different mindset from before.”
Result
Information at Our Fingertips
Employees quickly adapted to the new system. “The transition went remarkably smooth,” Hintlian said. “People got it right away.”
For example, year-end inventory was completed in a fraction of time than previously and with “incredible” accuracy. That was just one of the new system’s many benefits.
“Now we’re able to measure real time productivity, line effectiveness and performance. All that information is at our fingertips for analysis, literally by the hour, day or month,” Hintlian explained. “We’re able to show what's important in terms of performance at the operational, finance and accounting level and from a quality management perspective as well.”
Change and Preparation Mindset Key to Digital Transformation
Hintlian offers a few key pieces of advice for other similar sized companies embarking on their digital transformation journey.
“First, it’s not nearly as challenging as you might think but there are a lot of moving parts. Prepare and involve everybody equally, even people you think might be more on the periphery of the operation,” he said. “Everybody should appreciate what the environment is, what the to-be world will look like, and also why it's important. Once those concepts are understood, with a mindset towards change and preparedness, implementation should go very smoothly.”
Published April 29, 2024