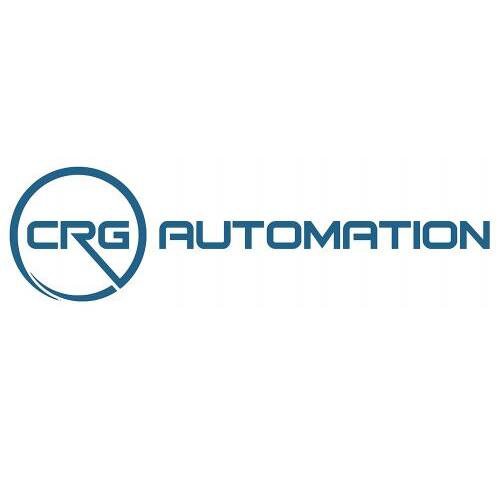
For more than 20 years, customers have relied on CRG Automation’s custom engineered systems and machines to package their products. Since its founding in 2000, The Kentucky-based OEM has built an award-winning reputation as an innovator, earning honors from TIME, Fast Company and Inc. Magazines.
- Labor and skills shortage
- Employee safety
- Minimize downtime
- Increase output
- Fast changeovers
- Intuitive training and operation
- Less downtime
For more than 20 years, customers have relied on CRG Automation’s custom engineered systems and machines to package their products. Since its founding in 2000, The Kentucky-based OEM has built an award-winning reputation as an innovator, earning honors from TIME, Fast Company and Inc. Magazines.
As an OEM member of Rockwell Automation PartnerNetwork™ program, CRG has embedded a number of our latest technologies into its newest custom automation machine: the C-IMC Cartoner. Cartoners place products, such as toothpaste or trash bags, into the retail cartons shoppers find on store shelves.
During assembly, cartoners retrieve products from production lines, insert them into cartons formed by the machine, and then fold, tuck or glue the flaps closed. These machines can also label, scan or perform other required tasks before cartons move to the next station, which is typically case packaging.
“We’ve been building cartoners for two decades. We’re proven and reliable,” said James DeSmet, CEO at CRG Automation. “Our new automated cartoner infuses the best of our legacy with modern technology and flexibility. Designed and built by the same professionals behind our other innovations, the C-IMC Cartoner is engineered to meet today’s industrial challenges.”
Challenge
Workforce Issues and Machine Rigidity Limit Packaging Capabilities
Like many manufacturers, frequent employee turnover and a lack of technical skills are the primary challenges facing CRG’s customers. But in today’s fast-paced production environments, they no longer have weeks or months to spend training new hires.
“The labor shortage is real. It’s getting harder to find and keep experienced people on the job,” DeSmet explained. “What we heard is that customers want a machine that’s simple to use, easy to operate, and includes on board training and troubleshooting guidance so technicians can self-diagnose or self-adjust.”
With an increasingly inexperienced workforce, machine safety is also critical. “Safety is always number one. And if new workers are not intrinsically familiar with the factory environment or the specific machinery,” DeSmet said, “then it’s especially important that the machinery is intrinsically safe.”
Lastly, packaging customers must respond quickly to changing consumer preferences for various product sizes.
“Companies don’t want to buy several different machines to do their packaging,” explained Kevin Houk, OEM Account Leader, Rockwell Automation. “They want one machine that goes from trial and travel sized products to family sized products with minimal changeover time.”
Changeovers for traditional cartoners are mechanically driven. This means operators must shut down machines in order to manually adjust components and settings, which then results in downtime, lost productivity and less output.
Solution
Inherently Safe and Flexible
The cartoner is also built to enable automated, single-button changeovers. With the machine’s preloaded cartoner recipes and ArmorKinetix® Distributed Servo Drives, changeovers are quick, accurate and hassle-free. The C-IMC Cartoner handles various rectangular carton sizes.
“Now with the push of a button the machine will change itself over or direct the operator to the specific dials or adjustments they need to make,” DeSmet said. “Lengthy setup times are a thing of the past, which helps our customers increase productivity and output.”
Inherently flexible and easy to use, the C-IMC Cartoner also prioritizes the safety of every operator with CompactLogix™ integrated safety control to help ensure a secure and productive manufacturing environment.
Result
Generates and Contextualizes Actionable Information
The machine is ideal for mid-range production with the capability to process about 60 cartons a minute.
“The C-IMC Cartoner is truly a smart machine that generates vast amounts of real-time data,” Houk said. “With FactoryTalk Optix, customers can contextualize and turn data into actionable information.
“Optix is different because it offers a broad range of deployment options. Running Optix on a PC-based machine provides customers additional application and IIoT opportunities, including the ability to perform analytics on machine,” Houk continued. “Then, depending on how data-ready they are, they can port to the cloud, connect and compare with other machines or facilities, and share and access information from manufacturing execution systems.”
The platform also provides secure remote connectivity through FactoryTalk® Remote Access™ allowing CRG to support and service customers, and even proactively alerting them to potential issues.
“The C-IMC Cartoner is designed to inform, improve and optimize operations,” DeSmet said. “It’s built to complement and enhance existing production lines while positioning our customers to thrive and grow in their markets.”
Published January 18, 2024