You may also be interested in
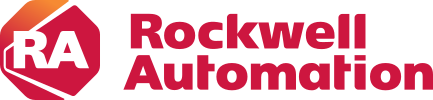
This story is about us! Rockwell Automation, Inc is a global leader in industrial automation and digital transformation. We connect the imaginations of people with the potential of technology to expand what is humanly possible.
- Legacy systems lacked scalability for energy management
- Manual energy tracking led to inefficiencies
- Limited visibility into energy usage across operations
- Need to align with Rockwell Automation’s global sustainability goals to achieve carbon neutrality by 2030
- AI-driven FactoryTalk® Energy Manager™ for real-time monitoring
- Predictive analytics for energy optimization and process efficiency
- Smart maintenance and automated facility controls
- Employee engagement with persona-driven dashboards
- 15%–30% projected annual energy savings
- 20%–40% projected reduction in Scope 1 & 2 emissions
- BCA Green Mark Platinum certification
- Increased workforce efficiency and real-time decision-making
- Scalable model for other Rockwell Automation facilities
Challenge
Driving Energy Optimization for a Sustainable Future
Based in Singapore, Rockwell Automation’s Asia Pacific Business Center (APBC), a manufacturing leader in industrial automation and a champion in digital transformation, is committed to reducing its environmental footprint and driving sustainability at its Singapore manufacturing facility.
As part of its global mission to achieve carbon neutrality by 2030 (Scope 1 & 2 emissions), the company recognizes the need for a structured and data-driven approach to energy optimization. The Singapore operations implemented best in class efforts to implement that.
The Singapore government has set out a comprehensive roadmap to meet 2050 climate targets of achieving net zero emissions, incorporating key strategies such as energy imports, carbon capture, and other sustainability-driven efforts. By aligning with these national sustainability goals, the plant is well-positioned to contribute to the country’s decarbonization journey.
In its latest 2024 Sustainability Report, Rockwell Automation highlighted its commitment to environmental stewardship and detailed its progress toward achieving carbon neutrality by 2030.
“Manufacturers today face increasing pressure to balance production efficiency with sustainability goals. However, many industrial facilities lack the necessary digital tools to analyze energy consumption, predict inefficiencies, and implement corrective measures. Our facility in Singapore aimed to bridge this gap by developing a scalable strategy that could drive tangible energy savings while supporting long-term decarbonization efforts,” explained Ferdi Aksoy, senior director of APAC operation, APBC.
Solution
A Data-Driven Sustainability Roadmap
To meet its sustainability goals, APBC embarked on a structured transformation roadmap built around data visibility, predictive analytics, and data-driven process optimization. This initiative was executed in collaboration with Kalypso, Rockwell Automation's digital services arm.
The initiative involved:
- Energy Audit & Maturity Assessment: A comprehensive review of current energy consumption patterns to identify inefficiencies.
- Integration of FactoryTalk® Energy Manager™: A real-time monitoring platform that provides dynamic feedback on power usage, enabling precise energy tracking.
- Data-driven Process Optimization: Leveraging machine learning models to analyze historical trends, predict demand fluctuations, and recommend corrective actions.
- Roadmap for Closed-Loop Energy Optimization: Implementing prescriptive controls that automatically adjust production parameters for maximum efficiency.
- Employee Engagement & Process Change Management: Driving behavioral changes through persona-driven dashboards, alerts, and decision-support tools.
- Automated Facilities Based on Production: Integrating sensors and control systems to dynamically adjust lighting, temperature, and humidity levels in response to production activities.
- Asset Optimization: Features include sleep mode for idle high-intensity assets, sequencing based on performance and closed-loop start-up/shutdown procedures.
By incorporating these elements, APBC was able to create a structured roadmap that moved beyond simple energy monitoring to real-time optimization and predictive decision-making.
Result
Measurable Energy and Emissions Reductions
Through the implementation of its energy optimization strategy, Rockwell Automation Singapore achieved significant sustainability milestones:
- 15%–30% projected Annual Energy Savings: Reduction in power consumption across key manufacturing processes.
- 20%–40% projected Reduction in Scope 1 & 2 Emissions: A major step toward realizing the company’s carbon neutrality goal.
- Scalability for Future Growth: The framework established a repeatable model that can be applied to other Rockwell Automation facilities worldwide.
- Enhanced Workforce Efficiency: By re-tasking employees to value-added activities, eliminating repetitive manual tasks, and automating data recording, the initiative has contributed to increased production capacity.
- Regulatory Compliance Achievements: Rockwell Automation’s Asia Pacific Business Center has been awarded the BCA Green Mark Platinum Certification, reinforcing its commitment to sustainable building operations.
- Real-Time Decision-Making: With FactoryTalk Energy Manager, the plant can monitor and compare energy and air consumption across multiple lines and assets. The system has enabled proactive identification of air leakages, allowing teams to rectify issues before significant energy losses occur.
Additionally, the roadmap facilitated faster executive decision-making through clear business cases, data-driven insights, and AI-powered recommendations.
Looking Ahead: Expanding Sustainability Efforts
Building on this success, Rockwell is expanding its digital transformation effort with AI-driven predictive energy optimization and further smart manufacturing innovations to enhance both sustainability and operational efficiency.
By leveraging its industrial automation and digital transformation expertise, Rockwell Automation continues to lead the way in sustainable manufacturing, empowering businesses to reduce their carbon footprint while maintaining peak efficiency.
Published April 10, 2025