The Asia Pacific region is expected to consolidate its standing as the global frontrunner in food production, driven by the rapid growth of populations and strong economies. Asian consumers are set to double their spending on food by 2030, creating a USD$8 trillion market, and delivering the world’s largest food and beverage market, according to a joint report by PWC, Temasek and Rabobank.
The primary goal of the food and beverage (F&B) industry is to deliver high-quality food to consumers. However, F&B manufacturers are grappling with various challenges; technology adoption, evolving consumer preferences, workforce shortages, and emerging ESG reporting requirements among them.
Manufacturers grapple with operational inflexibility due to outdated warehouse management systems and the complex task of aligning suppliers with demand, leading to operational inefficiencies. Additionally, they are under pressure to enhance safety and implement robust supply chain management systems to meet changing consumer demand.
To solve these challenges, the F&B industry needs to adopt technologies that can help address most or all of those challenges, notably Internet of Things (IoT), connecting machines, equipment, and products to near-real-time data, enabling smarter decision-making and process optimisation. Manufacturers can also integrate IoT solutions with enterprise systems, such as ERP (Enterprise Resource Planning) and MES (Manufacturing Execution System), creating a unified view of operations.
IoT integrations can bring numerous advantages, including heightened food safety, improved traceability, reduced waste, and decreased costs and risks in the food processing and packaging phases.
Embracing IoT in the Food and Beverage Industry
In the F&B industry, many manufacturers initiate IoT projects, but too often fail to implement them due to inadequate staff training, or poor collaboration with technology partners.
For IoT to truly improve processes and drive operational excellence across the entire value chain, you need to get the whole team on board. Manufacturers need to ensure that everyone, from operations to system integrators and machine builders, are part of the transformation.
The vast diversity in food applications presents distinct manufacturing challenges and requires specialised knowledge and considerations, particularly for IoT implementation. The food industry is incredibly varied; making cheese is not the same as making chicken nuggets. The needs of a dairy producer are vastly different from those of a seafood processor. A one-size-fits-all approach is ineffective.
Each segment of the food industry has its own set of manufacturing challenges and requires a nuanced approach to IoT implementation. This is crucial to ensure that IoT solutions effectively enhance quality management systems, accommodating the unique recipes and controls needed for each product type.
Another common problem manufacturers face is complex processes, leading to operational issues such as quality problems, delivery delays, and production bottlenecks. One aspect of this complexity is integrating modular solutions into operations. Manufacturers often adhere to traditional methods and need a shift from conventional production lines to more modular approaches. This shift aims to optimise space usage, reduce migration costs, and replace outdated mechanical engineering with digital technology.
While there might be standard modules available, like Overall Equipment Effectiveness (OEE) dashboards, or a quality management system (QMS), IoT customised solutions remain important to cater to specific F&B product needs and production processes.
Last but not least, the manufacturing industry is experiencing a workforce shortage. According to the 8th Annual State of Smart Manufacturing report by Rockwell Automation, 45% of manufacturers in the APAC region are in need of a more skilled workforce. To address this challenge, IoT can automate manual processes, enhance operational efficiency and reduce costs, even with a reduced number of workers on the assembly line. It enables manufacturers to maintain steady production and minimize downtime.
Leveraging IoT in Sustainability Efforts
Many manufacturers have not fully embraced IoT transformation or Manufacturing Operations Management (MOM) operations; some still rely on simple spreadsheets for reporting.
In today's business landscape, where environmental, social, and governance (ESG) considerations are crucial, there is a growing need for accurate and comprehensive reporting. IoT technologies present a viable solution, offering real-time data collection and analysis to enhance the accuracy and efficiency of ESG reporting.
Besides documenting energy consumption, another important aspect of sustainability is actively managing it. Manufacturers might have detailed reports but often lack actionable strategies for improvement. IoT stands out as a transformative tool, enabling real-time monitoring and management of energy and resources. By identifying energy-intensive areas and optimising resource use, manufacturers can significantly reduce waste and their environmental footprint.
IoT's contribution also extends to improving operational efficiencies and supporting lean manufacturing objectives. It offers detailed insights into material usage and waste generation, promoting informed decision-making.
By streamlining these elements, manufacturers can meet regulatory demands and sustainability goals. They can also achieve significant operational improvements, paving the way for a more sustainable and profitable future.
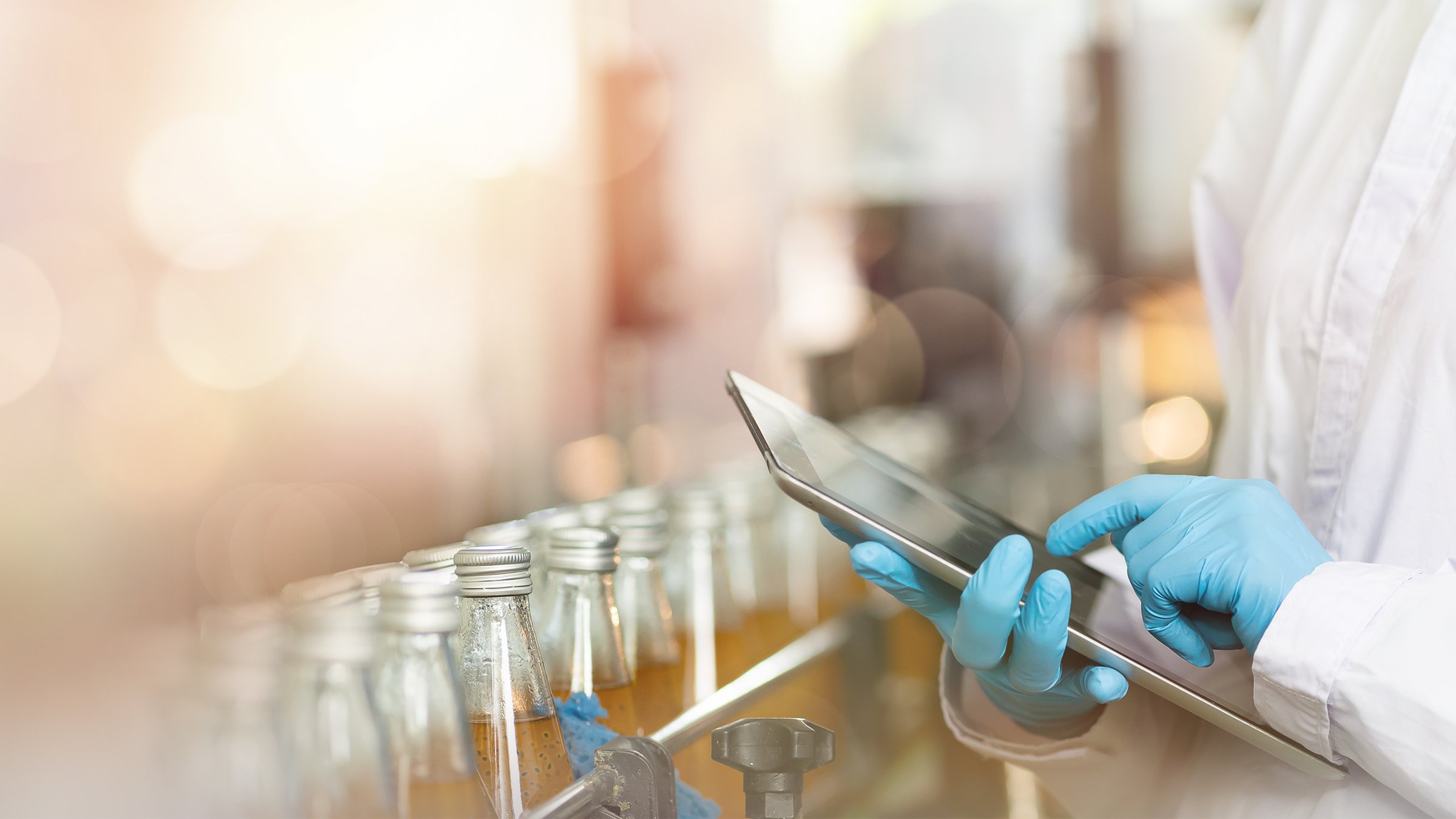
Harnessing IoT for Enhanced Efficiency in the Food & Beverage Industry
In the past, everything was paper-based, and there was no precise way to gauge a manufacturing line's effectiveness. This was because reporting depended on the operator's skill and was manually documented.
OE (Overall Equipment) visibility now allows manufacturers to understand how production lines are performing. Manufacturers can also achieve real-time performance monitoring through Digital Performance Management (DPM) tools, providing instant OEE (Overall Equipment Effectiveness) data. These enable real-time visibility of factory performance, identifying bottlenecks and monitoring energy management efficiently. Unlike a decade ago, where decisions were made weeks after an issue occurred, decisions can now be made instantaneously, addressing problems as they arise. IoT solutions are pushing the F&B industry toward a predictive maintenance approach, enabling decisions to be made proactively to avoid production halts.
The recipe to succeed in the food manufacturing industry today ultimately boils down to these two capabilities: full visibility insights into every stage of your food manufacturing process and control of production workflow. And this is where IoT benefits come into play.
Supply Chain Improvements: IoT helps track raw materials in real-time with sensors, leading to smarter inventory management, less waste, and timely restocking. Sensors for temperature and humidity are crucial for keeping perishable items fresh during transport, helping to ensure products reach consumers in the best condition.
Predictive Maintenance: In terms of equipment upkeep, IoT brings in predictive features to avoid expensive shutdowns. Sensors keep an eye on machinery health, spotting problems early. This proactive method cuts down on sudden failures, boosting equipment efficiency and lifespan. For instance, SATS, a Singapore provider of catering to aviation, healthcare, hospitality and government agencies, is set to build a S$150 million food production hub that uses automation and IoT technology to increase operational efficiency, increase asset utilisation and reduce food waste.
Quality Control and Traceability: IoT also helps with quality control, monitoring factors like temperature, humidity, and pressure to help make sure products meet high standards during production and storage. It allows for full traceability, making it easier to recall any products if needed, maintaining customer trust and meeting regulatory requirements.
For example, Fonterra Co-operative Group, a New Zealand-based multinational dairy co-operative, needed to meet the growing demands of customers around the world, while ensuring its products were made with the same high quality in each facility. They also faced challenges like limited production capacity and the potential for quality issues and unplanned downtime. To solve these, they adopted a digital transformation solution integrating Rockwell Automation's control hardware and software with Microsoft's cloud services and PTC's IIoT platform. This edge-to-cloud solution linked plant operations with business teams, creating a single source of reliable data.
Process Automation: IoT aids in automating manufacturing processes, leading to operational excellence. It ensures precise ingredient mixing, recipe accuracy, and consistent product quality. By minimising human errors and variability, IoT boosts efficiency and ensures the industry's high-quality standards are met consistently.
Empowering the Future of Food and Beverage Manufacturing with IoT
IoT stands as a crucial component in the formula for successful food and beverage manufacturing, offering a level of flexibility that can transform business operations. Smart manufacturing, enabled by IoT, provides immediate access to important data, empowering manufacturers at all levels to make well-informed decisions. This enhances the overall efficiency and effectiveness of the manufacturing process in the food and beverage industry.
Originally published on Asia Pacific Food Industry