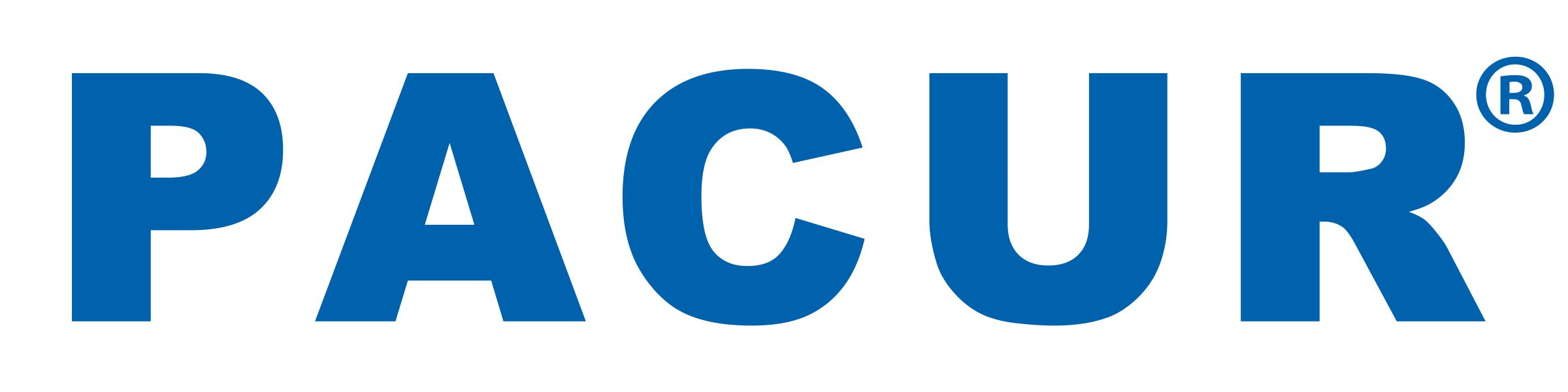
Founded in 1979, Pacur is a leading custom sheet extruder of polyesters and resins for a variety of applications. With an array of products, including polypropylenes, PETG, and sustainable materials, Pacur serves the medical packaging, food packaging, general retail and print market with roll stock and cut-to-size sheets. Pacur prides itself on its ability to create mutually beneficial relationships between customers and suppliers while exceeding quality expectations through the elimination of product defects.
- Meet quality requirements
- Support forecasted growth
- Use data to make better business decisions
- Decreased monthly close of books from 15 – 20 days to 5
- Cut invoice process from 2 weeks to 1 day
- Better management of raw material buys
- Increased level of accountability and insight based on data
Challenge
Looking for a Better Way
Pacur leadership recognized an opportunity for operational improvement and business enhancement. To make sure their vision came to fruition, Victoria Beltran, Director of Information Systems, was brought to the Pacur team with experience in system implementation and management. Alongside leadership, Beltran saw a need for a real-time, digitized manufacturing execution solution to help Pacur better serve its customer base, meet quality requirements, and support forecasted growth.
With a custom application on the shop floor, some Pacur employees were hesitant to switch systems and move away from an application that was created with their specific needs in mind. The company looked to move from an on-premise to a cloud-based solution to eliminate heavy IT system support and work within a system that would be continuously updated.
Pacur also focused on both scheduling capabilities and comprehensive quality tracking and management when looking for their new solution. They aimed to eliminate the challenges with tracking in-process quality and thereby waste resulting from manual errors and problems caught after the fact. To support compliance with their ISO certification and meet industry standards and guidelines, Pacur needed an easy-to-use, automated quality solution to be the company’s single source of truth.
Solution
Implementation Success through Change Management
After exploring several different systems, alongside a committee made up of primary stakeholders and leadership, Beltran determined that Plex Manufacturing Execution System was not only scalable, but also offered a modern user interface and an experienced network of implementation partners. Plex’s comprehensive and cloud-based offering along with a strong focus on digitized quality was the total package for Pacur.
Pacur began the implementation process with a steadfast change management plan and the help of their discovery and implementation partner Control+M. Knowing that change can be daunting, they considered that their operations team already had technology in place that they were comfortable using and that executives were cautious about storing company information in the cloud. So, throughout the implementation, Pacur made it a priority to educate employees on the benefits they would see in their day-to-day work as a result of digitization, including process streamlining, real-time inventory management, traceability, and real-time reporting.
To tackle training on Plex, Pacur started with surveys to determine the level of technology usage that employees were comfortable with. This allowed training to be individualized and crafted to the specific needs of Pacur employees. Ongoing education was a major factor in adoption success. In fact, 72 hours of training were made available and while employees were only required to attend three hours of this training, many took advantage of additional sessions for more support. “The customized training we developed in working with our stakeholders to ensure we made the most out of the system wouldn’t have been possible without the ease of use of Plex”, noted Beltran.
Just before implementation, Pacur’s ownership changed, which actually increased support from high-level executives. A positive outlook by the new leadership team on the benefits that would be realized from Plex gave employees an increased sense of security and heightened their confidence in the new possibilities now available to them. “Pacur was really good at listening,” commented Patti Nowak, Owner of Control+M Solutions. “The more you listen and acknowledge people’s input, the more they’re willing to give input and the better the project is. So, everybody really felt empowered and that was a big factor at the end of their implementation.”
Result
Real Benefits, Real ROI
Results achieved were clear after go-live. One initial requirement that Pacur defined was improved access to data. Plex has eliminated information silos, which was a drain on resources who need to communicate across these silos within the organization. Plex’s multi-tenant, cloud-based model tracks all information in real time – a critical asset for managing manufacturing – relieving Pacur’s issues with data visibility.
Pacur also shifted from error-prone paper-based quality data gathering to in-line quality data gathering using digital check sheets, which has accelerated work on the shop floor. Instead of disruptive manual quality checks, employees are able to focus their energy elsewhere and executives trust the data prepared for audits and compliance. Digitizing quality with Plex now helps reduce high costs of compliance, including data collection, re-certs, and re-audits, and the high cost of low quality, such as lost material and rework.
Another quantifiable outcome, Pacur can now send invoices within one day through an automated process, as opposed to a previous wait of up to two weeks. Eliminating data review individually by Pacur employees, this has improved accounts receivable health with invoices delivered in record time.
Pacur has also seen a substantial decrease in their monthly accounting close time, going from fifteen to twenty day closes to five days maximum. This significant improvement was made in only three months.
Plex’s cloud-based model and modern interface appeals to the work preferences and skill sets of young professionals coming into manufacturing. Working in Plex makes it easy to onboard new hires rapidly. Beltran stated, “We spend 45 minutes training people that we onboard in a Plex training session and that’s literally all it takes. From the start, we tell people that the hardest thing they’re going to do at any time with Plex is log in, which is simple to do. It’s very easy to walk them through their process steps and get them going on the floor right away.”
Beltran made note of how the data gathering process for making critical and strategic decisions that was previously long and tedious is now expedited due to Plex’s rapid data extraction capabilities. “We have made two incredibly big business decisions, capital spend and market exit, based on the data that we’ve been able to extract from Plex very quickly. Had we decided to even look into that in the past, it would’ve taken us at least six months to gather the data and then we’d have to analyze it. With Plex, the process now takes only a few weeks.”
Technology Designed for Growth
The possibilities for Pacur are endless with Plex in their corner. They recognize that with a solid quality and manufacturing processes foundation, the time is ripe to set sights on future improvements. Pacur has already completed one acquisition of a plastics manufacturing company based in France. Growing with Plex into the new facility with their firsthand implementation experience was a major benefit and the implementation process was expedited and seamless.
With the same software and metrics in both locations, Pacur can look holistically at their business and make critical business decisions faster to support future growth. Beltran shared, “Now that we understand the amount and quality of data that we can get out of Plex, we really emphasize the importance of the information that’s going into Plex so we can drive a higher level of accountability and insight.”
Published December 11, 2023