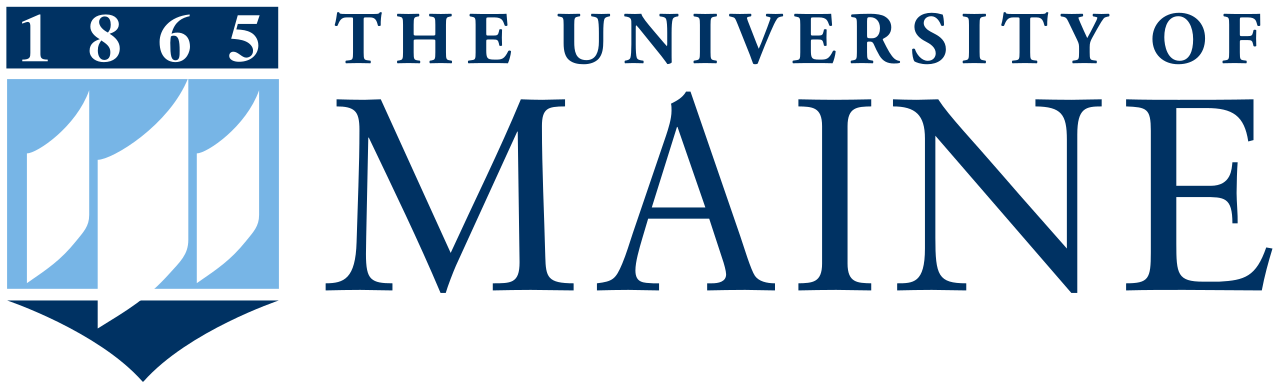
The University of Maine Process Development Center (PDC) creates opportunities for paper manufacturers to research new sustainable products and for students to participate in industry innovation.
- Obsolete web handling drive system led to unscheduled downtime incidents
- Limited availability of parts delayed return to production, sometimes by a week or more
- Canceled technical services cost PDC manufacturing clients up to $20K/event
- Machine unreliability threatened PDC’s operations and budget
- Industry collaboration enabled selection and funding of an advanced automation solution
- Students’ capstone project developed scope of system modernization
- Paper Web Handling Coordinated Drive System Solution will provide operational reliability and system visibility
- Installation and implementation targeted for early 2025
- Critical infrastructure upgrades will increase reliability, production and asset cybersecurity
- PDC will be able to maximize machine availability and minimize project risk
- PDC will be able to continue operating as a premier forest-products research facility serving manufacturers, faculty and students
Challenge
The University of Maine Process Development Center (PDC) is a globally recognized partner to pulp and paper manufacturers who require access to a test facility for product and process innovation. Forest-fiber packaging is a sustainable alternative to plastics, and researchers at leading packaging and paper manufacturers use the PDC’s pilot paper machine and technical services regularly.
While most PDC customers are based in North America, European and South American companies pursuing sustainable packaging rely on the PDC as well. The PDC also supports research by UMaine faculty, and engages UMaine students in paid, hands-on-learning experiences.
Unscheduled Downtime Increases
Legacy automation systems are increasingly difficult to maintain, and after 35 years, breakdowns of the pilot paper machine’s web handling drive system increased. Downtime incidents cost PDC customers up to $20,000 per event, and the loss of income was impacting PDC’s operating budget. The unreliability of the pilot paper machine threatened PDC’s reputation as a leading center for pulp and paper industry research. The system crashes also disrupted research by UMaine faculty, and student learning.
“The pilot paper machine is our lifeblood for the university,” said Colleen Walker, Ph.D., PDC Director. “The industry is spending a lot of time and money to be here to trial their new products and we've had to send them home because it crashed and we couldn't get started again. We don't have to run 24/7, but it's even more important that when we need to run, we run.”
When the PDC turned to the UMaine Pulp & Paper Foundation for help with upgrading the obsolete coordinated drive system, Packaging Corporation of America (PCA), a Foundation corporate member and longstanding customer of both UMaine PDC and Rockwell Automation, stepped up. The UMaine PDC selected Rockwell Automation as the solution provider and funded this essential modernization.
Solution
PCA recommended that the Paper Web Handling Coordinated Drive System Solution by Rockwell Automation was the right choice to improve reliability and maximize uptime of the PDC’s pilot paper machine. Inclusion of the PremierSystems™ Toolset and Enhanced TrendPlus on the engineering workstation will give PDC operators enhanced visibility and actionable data through predictive diagnostics and analytics features.
Designed for Efficient, Reliable, Sustainable Paper Web Handling
Rockwell Automation uses coordinated drive system global solution standards designed for the complexities of paper web handling, from properly closing the nip to correctly building the roll profile. Seamless power and process integration reduces both engineering and commissioning time. Faster time to production and machine reliability, continual advancement and long-term support made the Rockwell Automation solution the right fit for the PDC.
Minimizing Downtime, Optimizing Production with Data
PremierSystems simplifies the work of paper machine operations and maintenance in a unified interface. Advanced diagnostic tools reduce troubleshooting time and help operators resolve run issues without additional support. Empowered by data, operators can resolve issues in less time and perform more efficiently.
Rockwell Automation predictive diagnostics built into the PowerFlex® 755T AC drive series also offer early warnings by providing visibility into critical component life and detecting upcoming equipment failures. These advanced diagnostics can help reduce unscheduled downtime and excessive repair expenses associated with running to failure. Essential documentation and other technical support infrastructure is embedded within PremierSystems, which means operators can make the right decisions independently and with confidence.
Enhanced TrendPlus is also an integral part of the diagnostics solution. The high-speed data acquisition software by iba America, LLC captures data at a 5-millisecond rate, converting everything the controller sees into data that can be analyzed. Rockwell Automation adds value to this trending package by integrating it into the PremierSystems toolset and in the way it is configured specific to the drive system solution.
Students Lead Modernization Planning
UMaine engineering students worked with PCA and Rockwell Automation to create the scope of work for the system upgrade. This became the students’ capstone project and was used to inform the project proposal and implementation plan.
Result
With implementation of the advanced web handling drive system planned for early 2025, the PDC will once again enjoy reliable pilot paper machine performance for its customers. The premier forest-products research facility will continue to enable innovation by manufacturers, faculty and students.
Rockwell Automation will provide full support for the drive systems upgrade, including startup and commissioning. We are pleased to support the UMaine PDC in conjunction with PCA and appreciate the opportunity to help the PDC move toward smart manufacturing.
The modernization will also give UMaine students the chance to see and train on an advanced automation solution, whether they are interested in the paper industry, sustainable packaging, or the mechanics of manufacturing.
“The purpose of the PDC is to serve industry, but it’s also to get potential students interested in a school that’s developing sustainable solutions using forest fiber,” said Walker. “Students want a career that's going to solve problems that really matter. This upgrade keeps us relevant and moving in that direction. This modernization will provide industry users with additional information and will demonstrate what is possible today to UMaine students.”
Published September 11, 2024