The smart safety solution at AKD provides new insight into the mill’s operational status. By capturing rich diagnostic information, safety and operational data can be used to substantially improve safety compliance and performance. “The integrated smart safety solution provides all the data needed to create a comprehensive picture of the status of the mill,” said Matthew Treeby, account manager, Rockwell Automation. “The whole system at AKD is moving towards a Connected Enterprise, generating safety and operational data to help improve productivity and reduce downtime at the mill.”
Challenge
- To commission an innovative new saw line to replace legacy system that could no longer meet volume throughput requirements of the mill
Solutions
- Integrated Control and Safety - Allen‑Bradley® GuardLogix® controllers and PowerFlex® 755 drives with safe torque-off delivered integrated control and safety at the mill
- Smart Safety - Guardmaster® 442G Multifunctional Access Box (MAB) delivered integrated access control and guard locking
- Information Solutions - FactoryTalk® View SE delivers insight and visibility into the system
Results
- Fault-finding time has been reduced from hours to seconds
- Guardmaster 442G Multifunctional Access Box (MAB) delivered access control and guard locking
- The maximum processing speed of the saw line has increased by approximately 75 percent
- Line Speed has increased by 55 percent
- Recovery increased by 8 percent
AKD Softwoods is an Australian owned and operated integrated forestry and timber processing company with operations in Victoria, New South Wales and Queensland. The company is proud of its 60 year history – founded in Colac, Victoria in 1955.
The AKD team is committed to growth through investing in long-term sustainable assets and building strong relationships with customers and suppliers. With continual reinvestment in the business, AKD has a strong focus on plant expansions, plantation growth and employee development.
AKD service the Australian and Asian market, producing a range of products which includes sawn timber that is predominantly kiln dried, dressed, and machine graded for use largely in the construction industry. In addition, high grade by-products such as woodchip, pine bark, sawdust and dry shavings are also generated.
With an ongoing commitment to growth and productivity, AKD recently commissioned a new saw line that implements the latest safety, processing, automation, scanning and optimisation technologies.
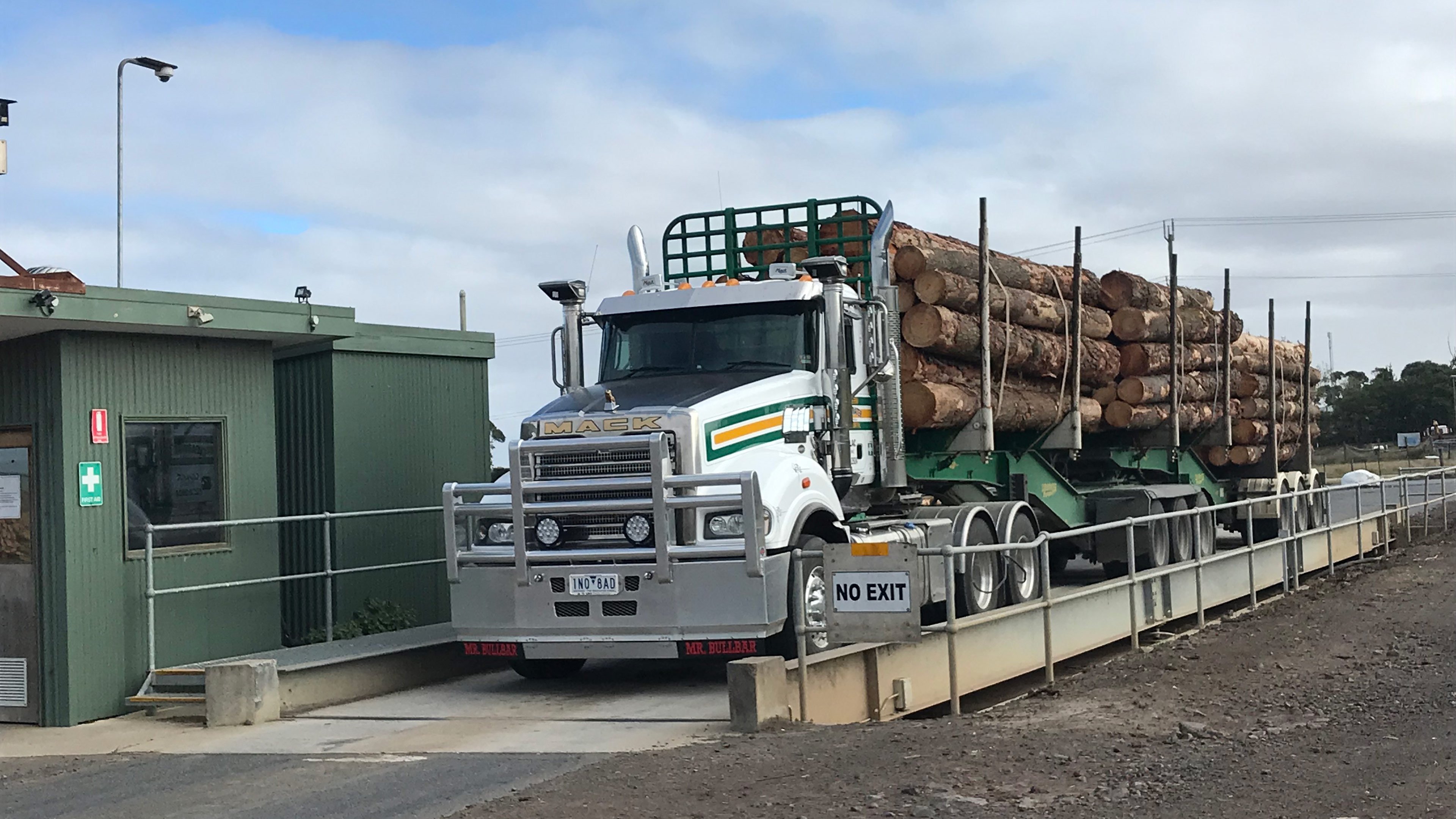
AKD Softwoods is an Australian owned and operated integrated forestry and timber processing company with operations in Victoria, New South Wales and Queensland.
Cutting-edge new saw line
AKD is distinctive amongst its key competitors for its reputation as a high quality producer and its vertically integrated operations. Locally sourced logs are processed at their Colac green mill. The logs are loaded on conveyors and pass through scanning devices to assess log rotation, grading of timber, board density and fibre stiffness. Each log is then automatically rotated to ensure maximum recovery (optimal usage of each log) prior to passing through the saw line. The sawn timber is then transported from the green mill for kiln drying and further processing, according to the intended end use.
The existing legacy saw line at AKD was 25 years old and reached its limit in terms of volume throughput. Being a forward thinking company, AKD knew that by investing in new technology, they could future proof the mill as well as improve reliability, throughput and recovery.
“When we decided to build a new saw line, we visited mills in the US and Europe to see how the latest technologies were being used and the benefits they provide,” explained Brady Wicks, National Automation and Controls Manager, AKD Softwoods. “A key priority for the new line was to reduce the amount of electronics on the machine, by housing them in a climate controlled environment to avoid mechanical damage resulting from dust and vibrations on the saw line. After looking at a few different options, we decided to implement a modular saw line with centralized I/O,” he said.
The new saw line leverages the latest control, automation, information and safety technologies from Rockwell Automation, using Ethernet communications. Allen‑Bradley® GuardLogix® Programmable Automation Controllers provide integrated control and safety for the saw line and PowerFlex® 755 variable speed drives with safe torque-off meet the challenging drive and safety requirements of the conveyors, band saws, kilns and processing equipment. Studio 5000® software was used for commissioning – minimising complexity and reducing the risk of potential errors.
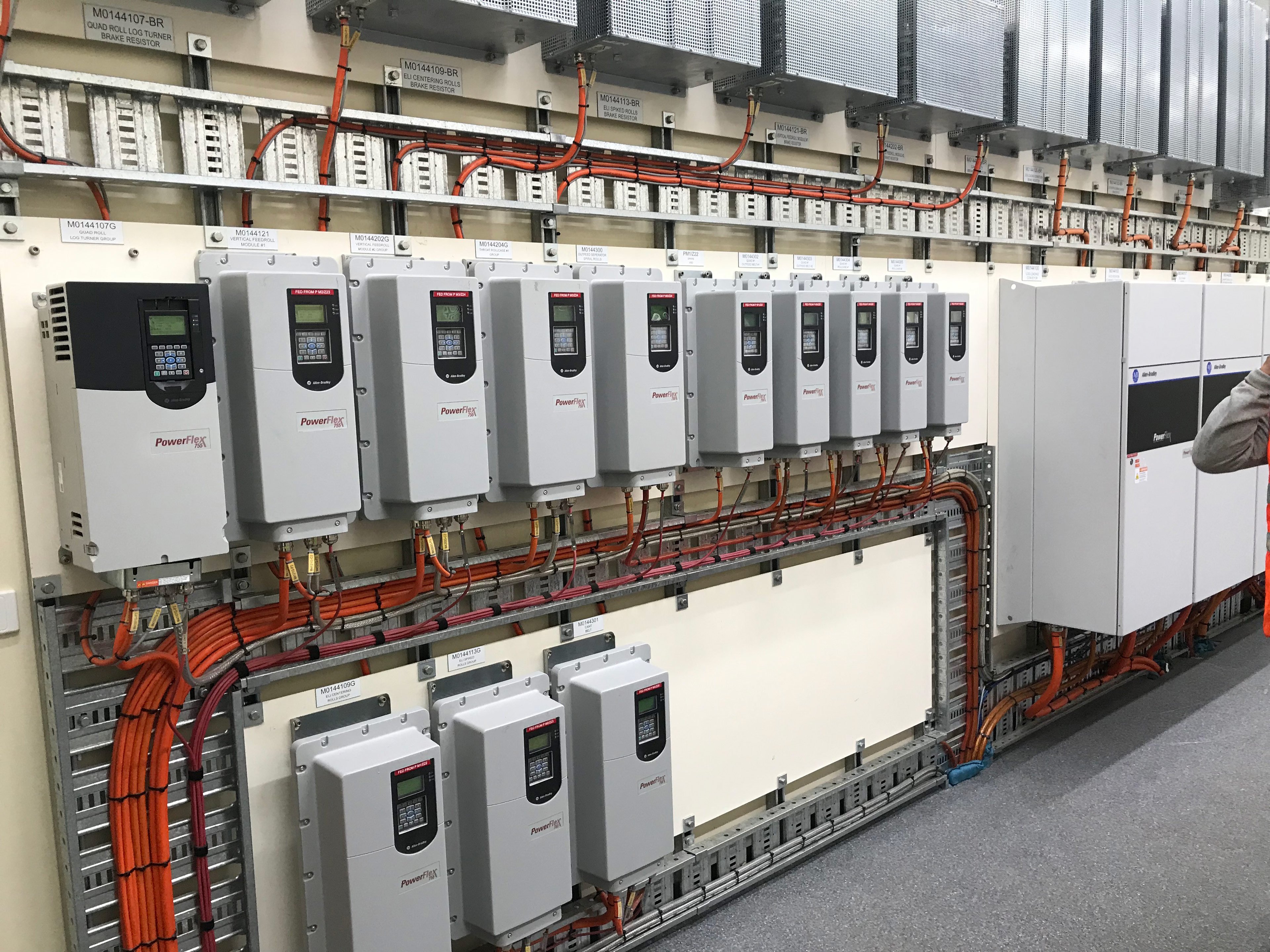
PowerFlex 755 variable speed drives with safe torque-off meet the challenging drive and safety requirements of the conveyors, band saws, kilns and processing equipment.
Smart safety simplifies system
Due to the nature of the saw line, safety and guarding was a key priority for the mill. Safety technologies have advanced significantly, improving safety compliance, machinery productivity, and performance. AKD worked with Rockwell Automation and their distributor NHP Electrical Engineering Products (NHP) to leverage the latest smart safety solutions at the mill.
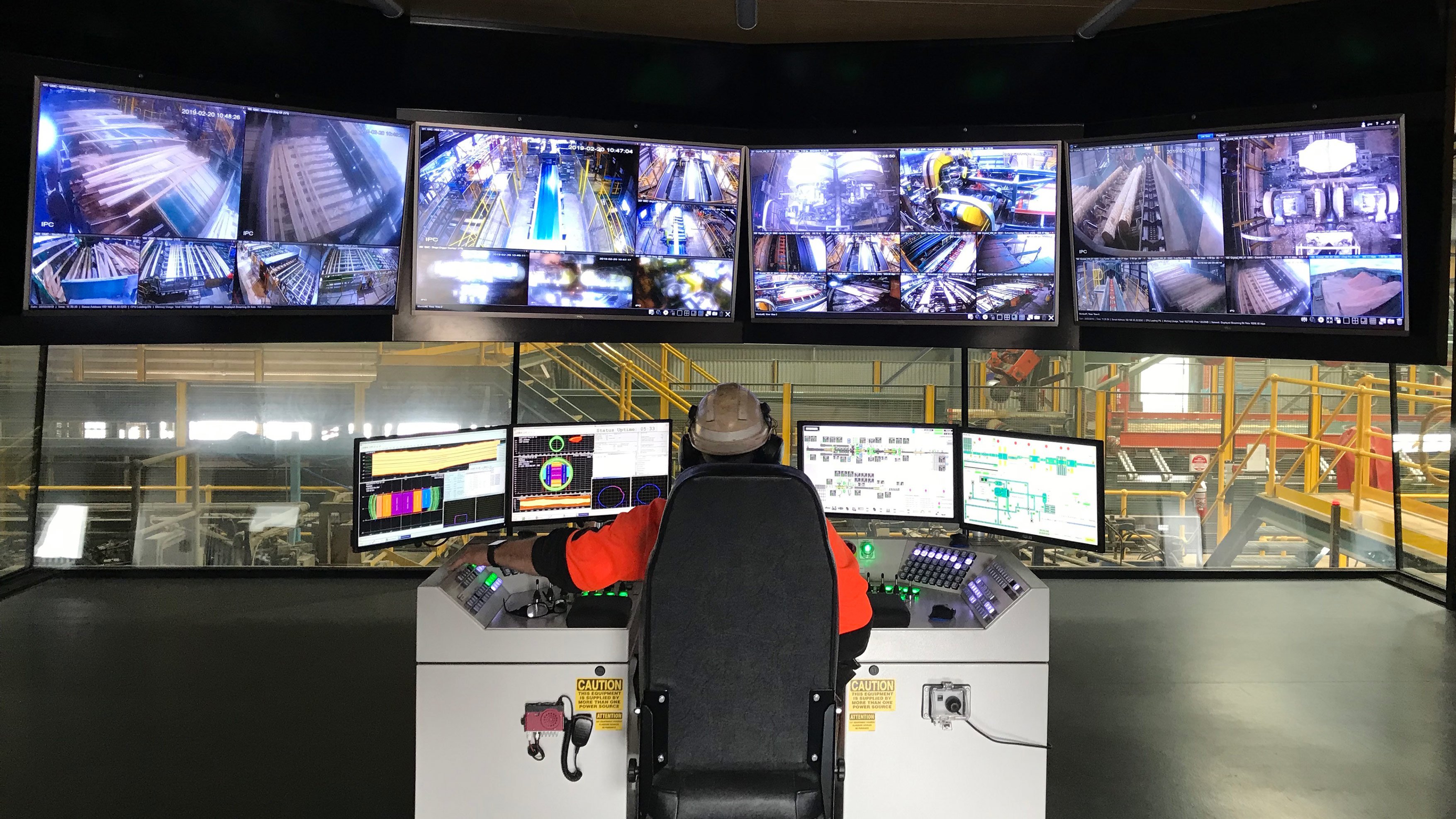
The smart safety solution provides new insight into the mill’s operational status
A high level of machine guarding is required at the mill to restrict operator access while the saw line machinery is in operation. The most appropriate choice for this application was the latest Guardmaster® 442G Multifunctional Access Box (MAB). The MAB is an integrated access control and guard locking device which provides a complete safeguarding solution for full body access applications. It is TUV certified to PLe performance level and with Ethernet/IP connectivity, hardwiring was not required which made commissioning seamless.
“Using the new MABs with safety over Ethernet simplified installation and commissioning. It reduced the requirement for additional safety devices and also the risk involved with having to commission multiple hardwired safety devices,” explained Wicks.
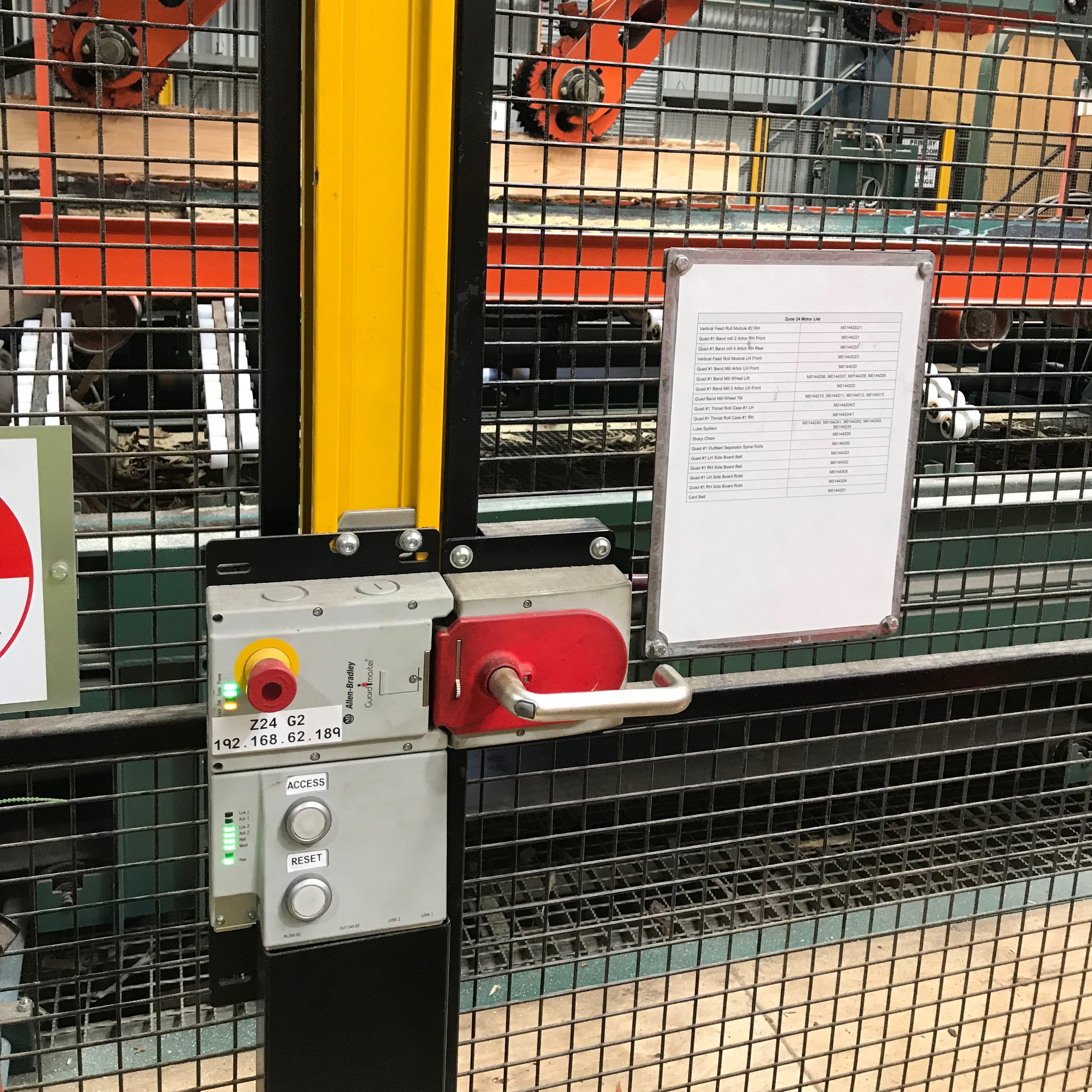
The MAB is an integrated access control and guard locking device which provides a complete safeguarding solution for full body access applications.
Improved Recovery and Productivity
The new saw line at AKD’s Colac mill is reaping the rewards offered by greater visibility into the system. Fault-finding time has been reduced significantly – from as long as two hours to now just a couple of seconds – thanks to rich diagnostic information available in real time through the FactoryTalk® View Site Edition (SE) HMI. AKD’s control is maximised by the ability to access the system remotely.
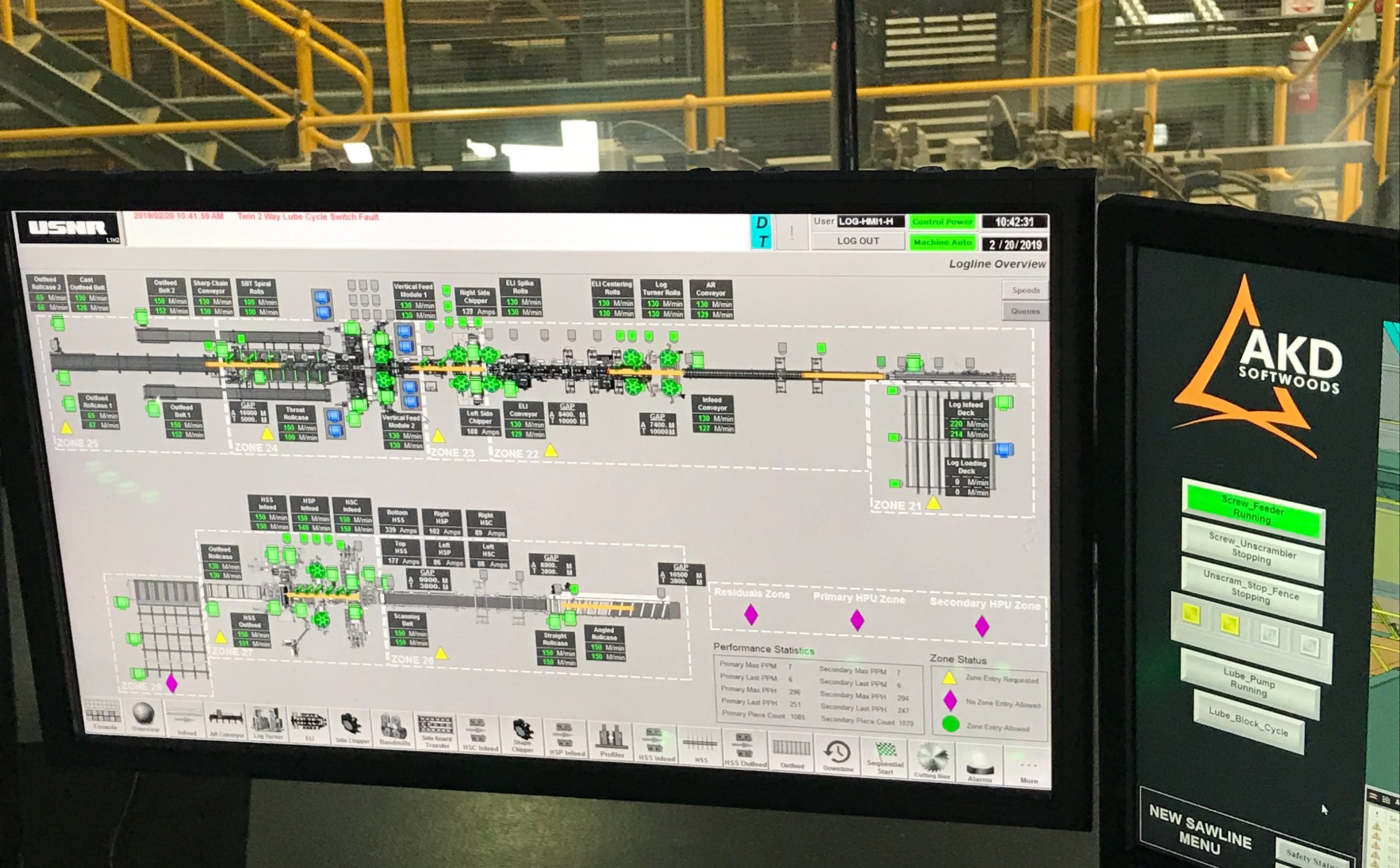
Thanks to rich diagnostic information available in real time through the FactoryTalk View SE HMI, fault finding time has been reduced significantly.
The maximum processing speed of the saw line has increased significantly by approximately 75 percent – from 37 metres per minute to 160 metres per minute. Prior to the upgrade, the mill was producing approximately 450,000 cubic metres of product and is now capable of increasing yield by 55 percent to approximately one million cubic metres per year.
For AKD, reducing wastage and increasing recovery of timber from logs was a principal objective of the project. “Prior to the new system, we were seeing recoveries of around 53 percent, now the mill is benefiting from recoveries of around 61 percent. This represents a significant increase in productivity and profitability for our business,” said Wicks.
“The support provided by Rockwell Automation and NHP has been exceptional. If there are any issues they are always willing to help us resolve them. As a result of the success of this project we can continue to provide a high quality product today and for years to come in what has become a very competitive market,” he concludes.
Allen‑Bradley, GuardLogix, Guardmaster, PowerFlex, Rockwell Automation, Rockwell Software and Studio 5000 are trademarks of Rockwell Automation, Inc.
Published May 15, 2019
Recommended For You