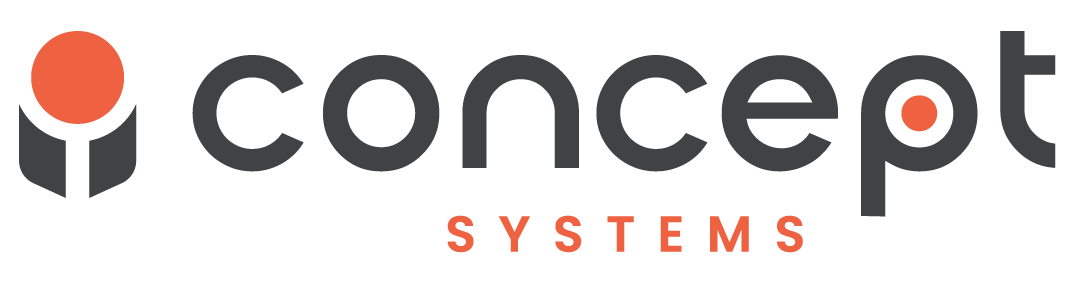
Concept Systems, Inc delivers streamlined automation systems that solve manufacturing challenges across industries worldwide with high-quality solutions that increase efficiency, reduce waste, accelerate time to production, and improve safety in manufacturing environments.
- No palletizing equipment existed that could handle multiple packaging sizes
- Labor shortages
- Production downtime
- Workplace hazards
- ControlLogix® Control System
- Compact GuardLogix® with CIP Safety
- PanelView™ Graphic Terminals
- PowerFlex® Variable Frequency Drives
- Input/output Modules
- FANUC robots and cobots
- Additional production capacity
- Increased throughput
- Enhanced employee safety
Steve Strong is Chief Executive Officer for Concept Systems, Inc. The firm, a Gold member of the Rockwell Automation PartnerNetwork™, develops automation systems that solve manufacturing challenges across industries worldwide.
Challenge
Palletizing equipment that could handle multiple packaging sizes
The need for a palletizing cell able to accommodate multiple packaging sizes was among the recent challenges facing a large packaging manufacturer.
“They had roughly 100 different types of packaging that they needed to palletize,” Strong said. “They had gone to several OEMs, but the industry didn't support that amount of variability.”
Labor shortages led to downtime
Labor shortages, workplace hazards, and implementing upgrades within a brownfield manufacturing facility were also issues that required attention.
“There were constraints around the size of the facility and having to work around the existing equipment,” Strong explained. “One of their biggest challenges was they couldn't keep the facility running because they couldn't hire enough people. Or even when they did hire people, they couldn't start the facility because workers weren't showing up for their shifts.”
Employee safety at risk
Further, employee safety was at risk because the facility pipes in steam to run presses and other equipment.
“The labor issue we’re seeing is people don’t want to do dangerous, dirty, boring jobs,” Strong said. “So, from the beginning, we looked at how we can apply and integrate automation to make operators and processes safer.”
Solution
Automated case erecting, robotic palletizing, and integrated conveyance
Concept Systems worked closely with the facility’s operations team and factory floor personnel to fully understand the packager’s process and needs, including safety concerns and building obstacles. As a result, the system integrator developed a solution with automated case erecting, robotic palletizing, and integrated conveyance.
“We were able to take their customer requirements and create a machine specific to their application that wasn't available off the shelf from other integrators,” Strong said. “We dug deep into the Rockwell Automation catalog using Rockwell Automation products throughout our solution. The PLC systems are all ControlLogix® and Compact GuardLogix® with CIP Safety, which delivers a deeply integrated safety system.”
PanelView™ HMIs allow the customer to control the palletizing cell from any HMI in the facility. The system also includes PowerFlex® Variable Frequency Drives and Input/output Modules. The robotics technology is from FANUC, a Rockwell Automation Strategic Alliance Partner.
Result
Increased production capacity and throughput
With the new palletizing system, the packaging manufacturer can now run seven lines, up from three, using the same number of personnel.
“While before they had to shut down a shift because of labor constraints, now they’re not only able to keep the facility running, but also run longer at higher efficiency producing additional product,” Strong explained. “We’re excited we were able to provide that additional capacity when it wasn’t necessarily expected, and the customer is excited to have that throughput in the same facility.”
Enhanced employee safety
Concept Systems was also able to enhance employee safety through automation and robotics.
“We moved operators further from hazardous pieces of equipment and processes.” Strong said. “By using scanners, integrated safety, and some collaborative robotics, operators now perform less dangerous activities compared to the manual efforts required previously.”
Published October 8, 2024