Augmented Reality (AR) can revolutionize manufacturing. It can empower your workers to perform better and avoid safety and compliance risks by providing easy access to the information they need. This is particularly relevant, given the challenges associated with the COVID-19 pandemic. Lockdowns and social distancing requirements have made it difficult for workplaces to maintain face-to-face operations but in spite of this, production must continue.
Thankfully AR can make this possible. These tools help plant workers adapt to new norms and specialists respond in real-time. FactoryTalk InnovationSuite Vuforia AR makes work instructions handsfree and delivered in real time where assembly or field service takes place. Knowledge of experienced workers is easily captured and shared with new workers and service technicians. Remote expertise can be delivered regardless of location and training manuals become a thing of the past as AR training has been proven to more effective and efficient.
Keeping essential industries working
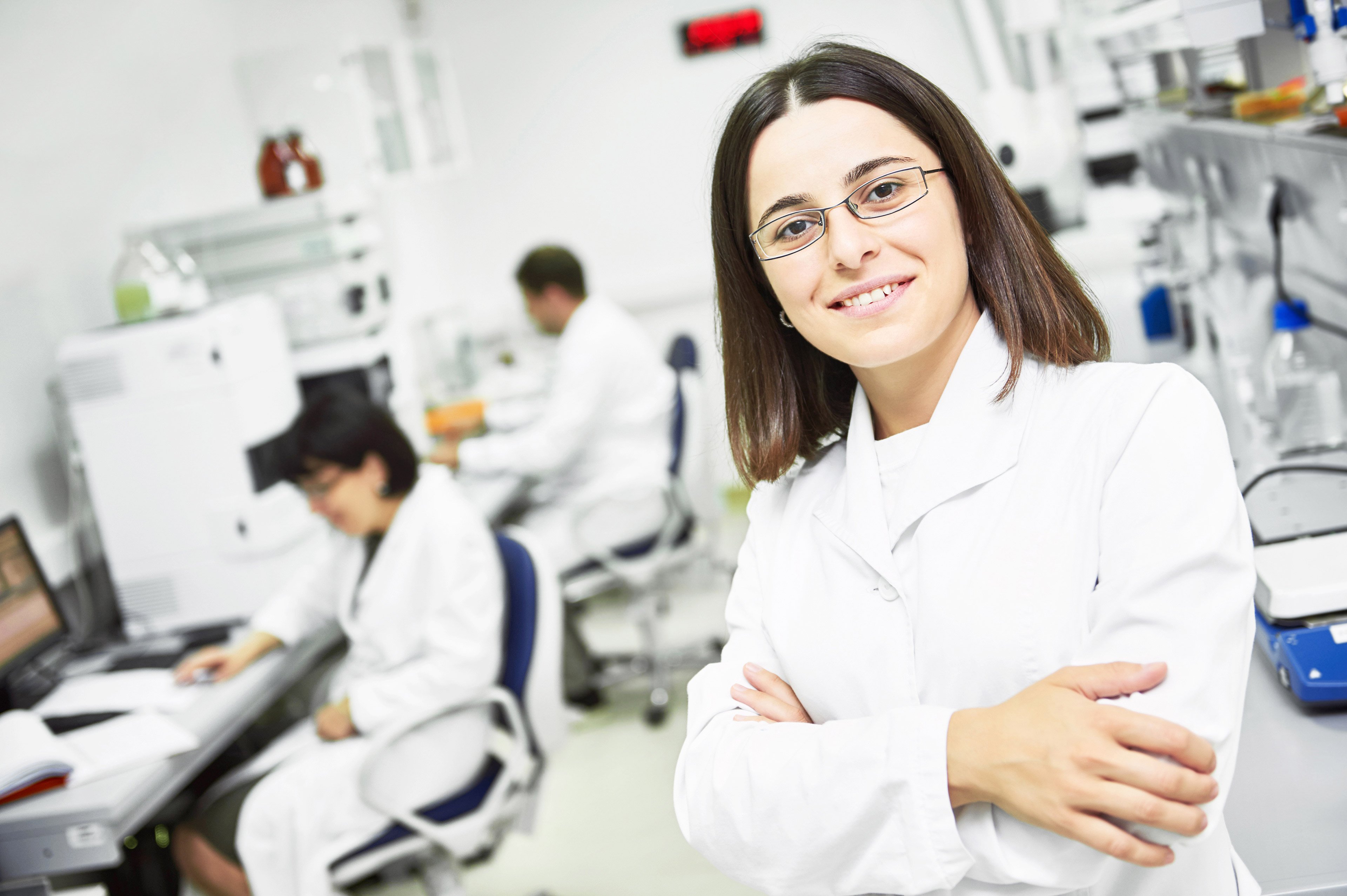
During the pandemic, many manufacturers have been classified as essential businesses. For industries such as pharmaceutical or medical equipment manufacturing, balancing meeting skyrocketing demand whilst staying compliant with social distancing measures and limits to maximum group capacity remains a challenge.
To help, Rockwell Automation is providing complimentary access to its AR program; an advanced simulation tool that can capture manual activities in real-time and enable rapid knowledge transfer to bridge expertise gaps.
AR allows remote experts to help onsite personnel perform the critical tasks and maintenance, such as those required to recover from unplanned downtime or outages. For example, equipment-manufacturer intelligence can be streamed directly to an engineer’s device, even as maintenance staff at other plants help with the diagnosis.
Mixed reality devices also help frontline employees to safely assemble complex products, by equipping them with real-time production data and instructions as required while performing the task. Simulation tools enable engineers with tasks such as mapping equipment layouts and studying the impact layout changes have on productivity and throughput equipment from anywhere in the world.
Customer servicing and learning and development does not need to take a backseat during the lockdowns. Employees are equipped with technology to help them remotely service customers, troubleshoot implementation issues, and continue monitoring ongoing projects through their laptops and even mobile phones, reducing their need to return to our offices.
AR improves efficiency
Industrial AR improves workforce productivity, efficiency and customer satisfaction with real-time, step-by-step work instructions. Vuforia AR solutions enable you to create and deliver easily consumable instructions with new or existing media content/capture, 2D & 3D content, sequences, IoT data and real-time annotations in shared environments. AR experiences authored in Vuforia can be deployed to the cloud or on premises, and users can access them from smartphones, tablets and wearable devices via a single universal viewer application.
There are three tools in the Vuforia AR solutions that are optimized for specific capabilities and use cases including:
Vuforia Expert Capture – allows your experts to capture first-person step-by-step video of procedures as they perform them. They can control the entire capture process by voice commands, gestures, and include location-based steps. Once they capture a procedure, they can revise and enhance it, then publish. Other employees can access completed work instructions through the Vuforia View app.
Vuforia Studio – Create game-changing AR experiences tailored to specific audiences and deploy them via desktop, mobile and wearable devices. Get up and running quickly using a drag-and-drop interface. No prior coding knowledge is required, and you can leverage existing 3D data, animated sequences and IoT data.
Vuforia Chalk – A collaborative remote assistance tool that uses AR to help employees who need to share real-time instructions and guidance without being physically on site to increase workforce effectiveness and efficiency. Experts can see and discuss situations in the field and guide technicians through a process. Both technicians and experts can use their fingers on the screen to draw digital annotations that accurately anchor to physical objects.
Augmented reality makes human labor 30-50% more efficient.
AR in action
In March 2020, Rockwell Automation found itself, like so many others, adjusting to the months to come as remote work became a worldwide phenomenon. In the case of one of Rockwell Automation’s premier customers, a pressing installation and start-up of a new replacement machine – a critical planned downtime event booked from the previous year – was scheduled just a few weeks away on April 1.
As strict travel bans unfolded, it became increasingly clear that Rockwell Automation would not be able to send a full team of field engineers and product experts to install the customer’s medium-voltage soft starter. This complex paper pulping machine required highly specialized experience and safety training, and without the machine in the line-up, the entire production run would be in jeopardy of shutting down, causing lost revenue and detrimental delays in the distribution of essential products.
To prevent catastrophic production delays, Rockwell Automation turned to Vuforia Chalk. They knew that Vuforia Chalk would be the most time-efficient and effective way to complete the scheduled service via remote assistance. Chalk allows remote experts to draw on-screen instructions for onsite workers to view and follow in real time, with digital annotations anchoring to the recipient’s local environment to help them see what’s happening – making it the ideal solution for this situation.
By combining real-time audio and video with AR technology, Chalk allowed the remote experts to view the end-customer’s equipment and annotate directly on the screen. With Chalk’s ‘over-the-shoulder’ ease of use, Rockwell Automation’s local field service engineer, Alexei N. Wilson-Eorgan, could follow along as the expert’s digital annotations guided him through the process.
With additional diagnostics and analysis software running on the machine, he also used Chalk to share real-time data readings with the extended team, helping them work through the changeover together in under two days.
Despite having a very short amount of time to train and prepare for his field engagement, Wilson-Eorgan was able to leverage Chalk’s simplicity to keep everyone connected and able to collaborate more effectively. This was a significant accomplishment – the equipment was so new that very few people had been trained on it, and even with decades of experience in the industry, Wilson-Eorgan still found himself with a completely new field service experience. “Chalk was the single most important link in the chain of diagnostic tools and expertise,” he said.
Future-proof your operations today
As new strains of COVID-19 continue to challenge our pandemic responses, it is likely that travel restrictions and lockdowns will be part of our new normal for the foreseeable future. As such, leading companies are embracing new IIoT technologies to future-proof their productivity and profitability.
AR is one of the tools you need in your arsenal. Your workers will be more productive and generate higher-quality products more safely. You will be able to train workers faster and more effectively so they can make proactive decisions and perform better. With trained and productive workers, you will benefit from lower costs and improved time to market.
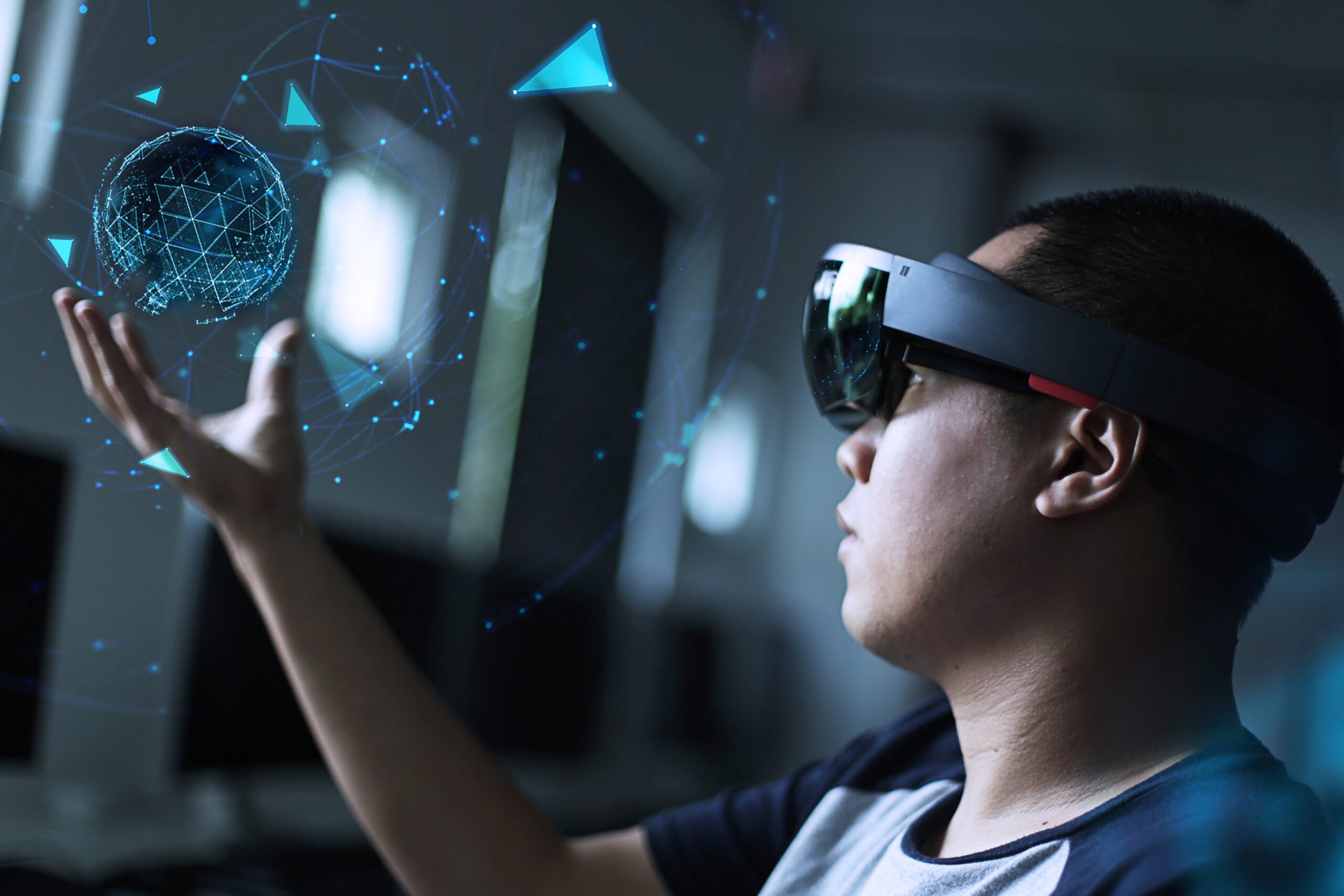