You may also be interested in
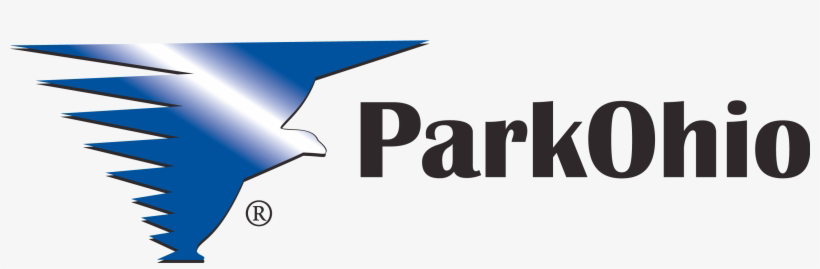
ParkOhio is a diversified international company providing world-class customers with a supply chain management outsourcing service, capital equipment used on their production lines, and manufactured components used to assemble their products.
- Outdated legacy ERP system
- Lack of accurate information
- Manual batch processes
- Need to integrate newly acquired plants quickly
- Access to real-time information
- Automated processes
- Improved quality control
- Reduced unnecessary costs
- Improved profitability
- Remote data access
Mike Gerber is the VP, Information Technology for ParkOhio’s Assembly Components Group (ACG). ParkOhio is a diversified global provider of supply chain management outsourcing services, production equipment and manufactured components.
The ACG division is a leading manufacturer of highly engineered components used in cars, agricultural equipment, commercial trucks, forklifts, engines, and industrial equipment. The business segment has 19 manufacturing, assembly, and warehouse facilities in the US, Mexico, and China that use Plex ERP, Plex MES and MES Automation & Orchestration (A&O). Their first Plex installation was in 2009.
Challenge
Outdated ERP systems and lack of information
Following the financial crisis of 2008, ParkOhio found themselves in a challenging situation. They needed to launch four plants, and their contract with their ERP provider was ending.
“We were in dire straits for a new ERP system,” Gerber said. “One of the biggest challenges we faced was a shift from a batch environment to a more real-time environment. Before, the information was collected in batches, and it wasn’t precise enough to truly understand our costs. Bills of Materials were not updated in the system. But, when you start working in a real-time environment, where the shop floor will shut down if the information is not accurate, you need more precision to enable good business decisions.”
ParkOhio needed a new system that could be deployed across the four globally disparate locations, and one that had the ability to track information to the level of detail required to enable real-time operation.
Solution
Error-prone manual processes get automated
With Plex, the ACG was able to automate tedious paper-based and error-prone processes. The division selected Plex because it was a cloud-based solution that allowed them to bring plants online in a short time frame.
“We successfully launched our first four plants in six months,” Gerber explained. “Because Plex is a cloud-based environment, we didn’t have the overhead of infrastructure, so we were able to move very quickly.”
Integrated new acquisitions seamlessly
Plex has been foundational to the division’s digital transformation and smart manufacturing strategy. It’s also been key to supporting the ACG’s rapid acquisition growth.
“Every time we acquire a new plant, our goal is to implement Plex within six months. It provides us with a common information platform,” Gerber said. “The existing management team knows how to interact with Plex and once that’s in a new acquisition, they don’t have to keep asking the acquired company for information. They know how to get their own answers and with consistent information, they can make better decisions quicker.”
Prioritized change management
The ACG prioritizes change management for each facility’s Plex implementation. They form a core team with members that represent each of the functions at that plant’s location.
“Our goal is to bring as many people along as possible. We train them and have them go through many pilots of the system,” Gerber explained. “We try to break their old habits and instill in them that this is real time. They’re running production. They can’t wait until tomorrow to fix issues.”
Result
Reduced unnecessary costs
Better understanding costs has been a business imperative for the ACG and one of the most significant outcomes of using Plex.
“We recently completed our last three Plex implementations,” Gerber said. “Now that these plants truly understand their costs, we’re seeing profitable return as they understand where they must go after improvements – whether it’s materials, pricing, labor efficiency gains, etcetera.”
Increased product quality
Quality improvements have been another Plex benefit for the ACG. With the ability to integrate machine data into Plex, the division created a data-driven poka-yoke in its rubber hose vulcanizing process. Vulcanizing is critical to producing high-quality, safe and durable rubber hose. Poka-yoke is a continuous improvement process that helps prevent errors. For this application, the ACG designed the poka-yoke, using an Allen‑Bradley® PLC, to prevent under-cured rubber from being shipped.
“Typically, a poka-yoke is in one operation. You put the widget in and it’s go or no go,” Gerber explained. “But with integration, we can follow a part from one end of the plant to the other and if there’s a failed process, it stops the next process from running.”
Vulcanizing process errors are communicated immediately with a quality alert text message and the hose is isolated by the system. Use of the hose in subsequent operations is blocked and shipping is prevented.
Ability to monitor process metrics
The division has also used Plex to access real-time process and usage data in its rubber mixing operation, which requires careful attention to ingredients.
“It’s important to monitor oil tank levels, so we created a system that allows buyers to monitor levels remotely and sends alert messages when levels get to a critical reorder point,” Gerber said. “Instead of having to go over to a plant to get a manual reading to make sure they don’t run out of oil, which would shut down their plants, they can just sit at their desk and check the tank level.”
These are just a few of the innovative ways ParkOhio’s ACG uses Plex and why it was named Plex’s 2023 Industry Leader Impact Award.
Published October 28, 2024