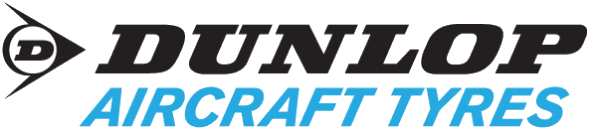
Dunlop Aircraft Tyres is headquartered in England with additional retread and after-market service facilities located in America and China. Dunlop designs, makes and retreads world class aircraft tires for many popular narrow bodied, wide bodied, regional and military aircraft from manufacturers including Airbus, Boeing, Bombardier and Embraer.
- Reactive maintenance approach that led to inefficiencies
- Lack of on-site engineers that doubled workload for available engineers
- Maintenance data management relied on paper and Excel and limited ability to schedule or plan maintenance work
- More efficient maintenance scheduling and execution
- Better resource allocation and reduced human error in data collection
- Failure prevention through early risk detection and intervention
- More visibility to historical work order data and machine history
Challenge
Challenge: Overcoming Reactive Maintenance
Like many other manufacturing teams, leading UK tire manufacturer Dunlop Aircraft Tyres started its maintenance journey rooted in reactive methods, which is not a reliable or effective way to keep a manufacturing facility running. They were constrained by a lack of on-site engineers, which meant doubling the workload of the engineers who were on-site.
Additionally, maintenance data was stored in an in-house database built on Microsoft Access. The database had no capabilities for scheduling or planning maintenance work, and those tasks would be done on paper and Excel.
This slowed operations tremendously, making it even harder to escape the daily firefighting that comes with a reactive strategy. If Dunlop Aircraft Tyres Plant and Controls Engineer Michael Thomas wanted to improve production, he knew this maintenance management process would not suffice.
Solution
Choosing Fiix
Longevity was a key factor in choosing software. Fiix was a newly acquired software company under the Rockwell Automation brand. Since Dunlop's plant floor equipment is mostly controlled by Rockwell Automation PLCs, the established trust in the brand made Fiix an easy sell.
In terms of software needs, Dunlop was looking for a system that could view machine history and historical work order data. Lastly, their engineers needed to be able to login and access their work from a phone or tablet from anywhere in the facility.
Result
Day-to-day use of Fiix CMMS
The impact of switching to Fiix CMMS was pretty quick for the team. “We saw improvements within the first few months,” Michael says. For example, the use of the CMMS includes producing daily reports for plant managers who previously had to create the reports manually. “There has been a tremendous time savings,” says Michael.
Created daily, the reports generated using the analytics tool are key to tracking things like Mean Time Between Failure (MTBF), which is reported on in weekly maintenance meetings.
Other benefits of implementing Fiix CMMS included:
- Better time management: by eliminating paper and Excel and improving access to machine data, the team wasted less time finding answers and more time-solving problems.
- Enhanced decision-making: access to daily and weekly reports facilitated better decision-making.
- Improved data quality: quality of data was free from human error, aiding in more accurate scheduling and resource allocation.
Added Solution: Fiix Asset Risk Predictor
After about a year of using the Fiix CMMS, Michael heard about this new predictive maintenance tool, Fiix Asset Risk Predictor (ARP). Michael felt that ARP would be worth the effort of testing because it could predict and report when an asset is at risk of failure.
With the power of both a CMMS and a predictive maintenance tool in place, root cause analysis of past failures could be performed by quickly cross-checking with the other systems they use to record temperature and pressure.
They’ve also set up the system to prepare automatic work orders based on individual asset risk thresholds. When a predetermined number of ‘amber alerts’ occur over a short period of time, the system will push out an automatic work order using Fiix® Asset Risk Predictors, Prescriptive Maintenance feature. “Using risk scores has been really helpful,” says Michael.
A match made in heaven: Fiix CMMS and Asset Risk Predictor
While Dunlop Tyres is taking time to build out the usage of Fiix ARP across the rest of their assets, the good news is that they haven’t seen any full-blown failures yet and will continue to look for other opportunities to utilize its features. Moving forward, the facility aims to continue leveraging technology to optimize maintenance operations, affirming the significant role of digital tools in industrial maintenance management.
This case study is a replicated version, with the original available on the Fiix website. To access the original version, please click here.
Published September 24, 2024