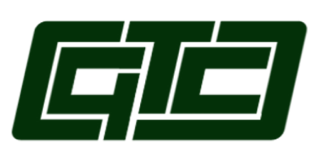
Founded in 1988, Green Tokai Co. (GTC) is a subsidiary of Tokai Kogyo Co. based in Aichi, Japan. With production and warehouse facilities in Brookville, OH and Maysville, KY, Green Tokai manufactures automotive components including door and window seals, windshield molding, and more. The company works to consistently exceed customer expectations alongside its quality goals, based on the ISO 9001:2015 quality system. Both GTC plants are ISO 14001:2015 certified.
- Relied on low-tech framework of two software systems and Excel spreadsheets
- Shop floor activities conducted manually with clipboards and paper
- Lack of PC infrastructure and access to real-time data
- Enhanced operational agility and market competitiveness through digital transformation
- Facilitated inventory serialization through intelligent cycle counts and location tracking
- Increased access to real-time production reporting
Challenge
Green Tokai (GTC) began operating in May of 1988. Since then, the global company has expanded to include three additional plants in Brookville, OH and one production facility in Maysville, KY. GTC was operating within a low-tech framework, relying predominantly on two software systems alongside Excel spreadsheets. Shop-floor activities were conducted manually, with clipboards and paper serving as the primary tools for coordinating the company’s work centers. Production reporting was also paper-based, leading to delays in data entry within the existing ERP framework.
Additionally, many GTC work centers lacked PC infrastructure, hindering digital integration and access to real-time data. Despite sporadic usage, the ERP system in place primarily served back-office functions, which resulted in a lack of linkage between master data and operational outputs. GTC also faced several challenges that impacted operations. For example, limited inventory tracking and management capabilities decreased the company’s ability to maintain accurate stock levels. The lack of real-time data resulted in operational inefficiencies and impacted timely decision-making. Quality tracking was also fragmented, relying on a combination of customer portals and spreadsheets. Manual documentation of quality checks on paper further complicated analysis and retrieval processes, despite meeting basic requirements.
Solution
Choosing Plex
Driven by these challenges, GTC initiated the search for a new ERP system. The company recognized the need for real-time data to enhance visibility and establish a single source of truth across its operations. Moreover, industry trends, including an increase in customer demand for serial traceability and quality tracking, emphasized the urgency for a comprehensive solution.
Plex emerged as the preferred choice for GTC’s new ERP system after a recommendation from a customer. Plex’s cost structure and endorsement by a significant industry player made it a compelling solution to address the company’s challenges.
Company-Wide Preparation and Successful Implementation
Successful adoption was a top priority for the entire GTC team throughout the implementation process. To enhance awareness, flyers were distributed extensively before the Plex implementation began and regular weekly meetings with department managers were held. Hands-on involvement in configuration, design, and training discussions also allowed Green Tokai team members to grasp the benefits of Plex well before implementation began.
Implementation involved multiple departments and individuals across the organization alongside Plex Implementation Partner, Revolution Group. Initially, a core team of approximately six members spearheaded the implementation process before it was extended across all 13 departments, each with designated primary and secondary super users. These super users were responsible for coordinating departmental activities, conducting training sessions, and ensuring readiness for implementation across all GTC plants.
Team leaders overseeing various work centers also ensured that their operators received adequate training. Post-implementation, these operators have demonstrated immense resourcefulness, exploring system functionalities beyond their initial training. GTC successfully implemented Plex and went live on June 1, 2023.
Result
Immediate Results and Future Growth
The adoption of Plex brought about significant improvements to GTC operations. The transition necessitated an upgrade in infrastructure, which led to an increase in PCs on the shop floor. This not only replaced many of the existing paper-based processes, but it also increased general optics for shop floor associates. The utilization of the Plex Control Panel also enabled Green Tokai’s operators to access real-time production reporting, enhancing visibility and allowing for the measurement of operational success metrics such as Overall Equipment Effectiveness (OEE).
With Plex, GTC has transitioned to a culture of continuous improvement. Increased visibility and traceability have facilitated enhancements based on real-time data, fostering a more proactive approach to problem-solving and allowing for more timely business decisions. The transition from a manual, paper-based system to Plex has empowered GTC to respond promptly to the needs of its suppliers and customers, enhancing operational agility and overall competitiveness in the market.
Additionally, Plex facilitated serialization across all inventory levels, enabling better inventory management through intelligent cycle counts and location tracking. GTC now attaches documents to transactions, providing assurance of transaction accuracy.
“The fact that we have real-time data is only starting to reap benefits in other areas,” stated Joseph Daniel, General Manager of ERP & Finance at Green Tokai. “GTC was so used to not having real-time data that we’re only now starting to run several subledger reports… to get a better understanding of how to address issues that impact our results.”
Looking forward, the company plans to continue discovering their new ERP system’s full potential. GTC is eager to implement Plex’s Maintenance Module and the GTC Quality Division is seeking new ways to phase out paper files and Excel documents every day.
Daniel stated, “The true benefits of Plex may only become apparent after going live, emphasizing the importance of a long-term vision and diligent testing.”
This Case Study is a replicated version, with the original available on the Plex website. To access the original version, please click here.
Published September 25, 2024