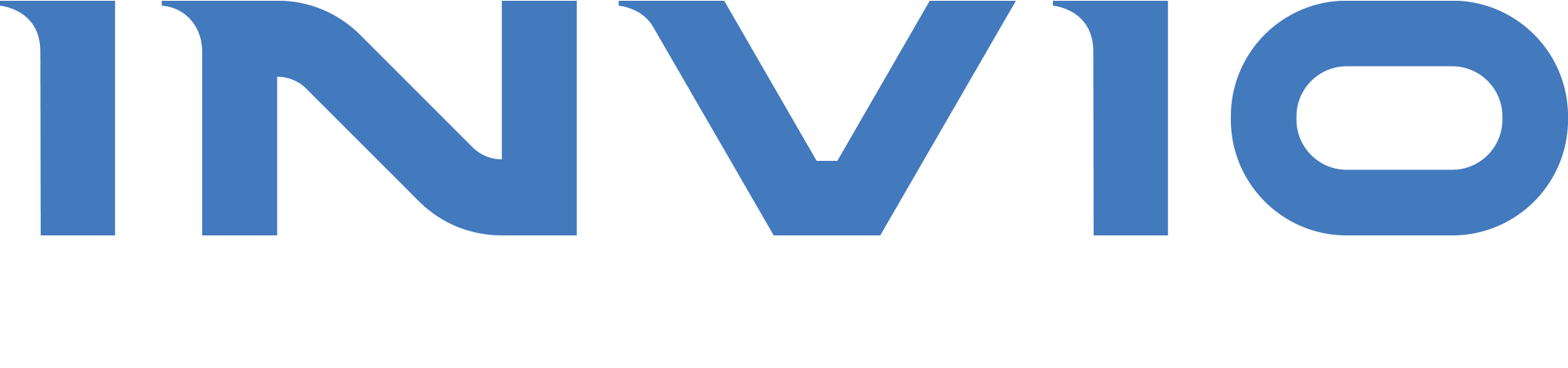
Invio Automation designs, implements, and sustains automation for the largest operations in the world. They take pride in partnering with customers to solve big challenge by exploring, testing, and customizing the latest manufacturing technology.
- Scale up production of hypodermic needles
- Bend needles into shape with accuracy
- Overcome material hardness variations without time-consuming machine setups
- Increase in daily lot production
- Improved quality
- Seamless lot changes
- Small footprint
The complex manufacturing needs of wearable drug delivery devices
Wearable drug delivery devices have transformed the lives of countless patients around the world, freeing them from the burden of daily injections and helping them comply with strict dosing schedules. Designed to be worn on the body, these small platforms incorporate smart features like closed-loop systems and sensors for continuous monitoring and feedback. Unsurprisingly, manufacturing precision is critical, particularly when it comes to producing hypodermic needles.
"Most cannulas are pretty simple to produce—they're straight needles that are glued into plastic parts. But wearable drug devices often require bent needles, and each device requires a needle of a different shape," explains Eric Peterson, Executive VP of Concepts & Solutions at Invio Automation, a producer of comprehensive automation solutions and a gold-level member of the Rockwell Automation® PartnerNetwork™ program.
Moreover, the angle of the bend in each needle must be accurate. Slight variations in simple syringe needles do not generally affect performance. That's not the case with wearable drug devices. Their needles, which share a tiny space with objects like pivoting levers, gear wheels, and fluid reservoirs, must be inserted under the skin at the correct depth to achieve the proper flow rate and avoid occlusion. It's an added complexity that medical device manufacturers must address.
So, when a long-standing customer asked Peterson's opinion about a piece of equipment it wanted to purchase to mass-produce bent hypodermic needles, he expressed concern. "The equipment was large and expensive and required a separate station for every bend. They wouldn't know they had a good product until they got to the last bend."
This lack of ability to monitor quality at each stage of production posed a significant risk to the production process. Peterson decided to help the customer identify a more viable solution to achieve its goals of reducing production cost per unit and delivering consistent quality and performance. He found inspiration in an unusual place.
Challenge
Scaling up the bending and assembly of hypodermic needles
The customer that approached Invio is an award-winning medical device company that develops and manufactures wearable insulin management systems for people with diabetes. Its flagship product attaches to the body and delivers continuous insulin based on the wearer's personal settings.
The needle inside the wearable device has a complicated shape involving at least 14 bends. It also requires an accuracy of ±0.005 inches on the first and last bend, while the total tolerance of the needle stock is ±0.015 inches. Manufacturing these needles is extremely challenging.
"The technicians were doing all these adjustments to the bends on hard tooling," said Peterson. "They were moving between different pieces of equipment and spending a lot of time tweaking the bending module every time they changed needle lots. Just a one-degree difference in material bounce back required recalibrating all bending stations."
Crunch time came when the manufacturer decided to scale up production. Jonathan Poole, VP of Automation Technology and Standards at Invio Automation, explained: "Manual and semi-automated needle bending techniques can’t scale up to mass production levels because they can't precisely form one or more bends repeatedly or efficiently."
To achieve its strategic goals, the customer needed a flexible bending and assembly machine that could automatically modify hypodermic needles into various shapes regardless of their material hardness. A brand new solution was required.
Solution
A flexible, programmable machine that forms multiple bends
The idea to automate the bending process using a programmable system came to Peterson from an unexpected place. "I was at home watching 'How It's Made'," he said. "I saw a company using a bending machine to make baskets from industrial wire. It was a light bulb moment. Long story short, we presented the idea and a prototype to the customer, who was amazed and placed an order there and then."
That prototype eventually became Invio's patented Needle-Bending and Assembly Machine, a unique solution in the market. The apparatus is programmable, allowing it to form one or more bends in a hypodermic needle in various directions and at multiple angles. This flexibility is a crucial advantage, as it allows operators to form different, user-selectable bends via a diagnostic interface and with little or no tooling changes. The flexibility greatly enhances the efficiency and adaptability of the manufacturing process.
"Our customer was excited about the flexibility and programmability of this machine," said Peterson. "Different needle lots have different hardness properties, so our machine uses an inspection camera to measure the critical dimensions. It then uses vision feedback to adjust the bending parameters in the bending modules automatically. This keeps the needle shape centered on the dimension targets. What's more, it doesn't take up much space. The cell is only 3x6 feet." As any customer using a cleanroom space can attest, equipment with a smaller footprint provides a huge cost advantage.
Automatic calibration that achieves consistent needle quality
The vision-guided process and precision part handling aspects of this machine are innovative because the bends on both ends of the needle must be highly accurate for the wearable device to function. A camera mounted in the bending module finds the ends of each needle, and a servo-driven slide positions the needles exactly where the bends are required.
While the tolerance required is ±0.005 inches, the machine can form bends at a tolerance of ±0.002 inches, fully compensating for large needle stock tolerance with every needle. This level of precision delivers consistent quality and performance, saving time and effort for operators and giving quality control peace of mind.
"The operators don't even realize the machine is calibrating itself every time they put in a new lot of material," continued Peterson. "The process is invisible. Now they can produce a needle every nine seconds. They rattle through it. And when the company wants to scale up production, all it needs to do is add more modules."
Control for the machine is built on Rockwell Automation CompactLogix® Programmable Controllers. The machine is powered by Kinetix® Servo Drives & Motors and PowerFlex® 525 AC Drives.
Switched Mode Power Supplies, Fuse Holders, Disconnect & Contactors and Stratix® Switches deliver smooth power flow, and Photoelectric Sensors are used to detect the motion of the product as it moves through the machine. Operators interact with the machine using PanelView™ Graphic Terminals and Allen‑Bradley® Push Buttons & Signaling Devices.
“We knew from the outset that we would get everything we needed from Rockwell Automation thanks to the investment we had already put into the Partnership," said Poole.
Result
Improved production efficiency and cleanroom space utilization
Once Invio had installed the bending and associated assembly machine in the customer's cleanroom, the operators were given a manual and some hands-on training. Within a matter of hours, they were independently using the machine. "That's a real benefit to manufacturers," said Poole. "They don't need skilled technicians to make adjustments because the machine makes all adjustments itself. They just need operators."
Since the installation, the medical device company has seen some impressive results. It avoided the need to buy an overly expensive machine with a ton of support equipment like boxes, belts, dies, lubrication and trays. Instead, it has a compact, modular conveyor system that takes up roughly three times less cleanroom space and requires far less maintenance.
It also has the flexibility that it needs to handle lot variation and scale up production with the ±0.005 inches precision its wearable devices demand. The production team can now keep pace with ever-increasing sales targets and changing business goals.
Helping medical device manufacturers make good decisions
Invio's expertise in vision-guided processing, precision part handling, and controls engineering, plus its partnership with Rockwell Automation, enabled the design of a unique machine that is perfect for manufacturers of drug delivery systems looking to scale up production, reduce operational costs and increase business resilience.
"We enjoy helping our customers better understand their challenges and make good decisions," said Peterson. "Thanks to our wealth of experience in automation, we're not afraid to offer alternative solutions if we think there's a better way of doing something."
Learn more about Invio Automation.
Published September 12, 2024