Recommended For You
Smart technologies can help you better understand your operations, enforce workflows, optimize asset utilization and improve collaboration. All of this is made possible through a Connected Enterprise that leverages a reliable and secure information infrastructure.
With greater connectivity comes greater risk for security threats. To make matters worse, cybercrime is increasing. It is now estimated to be a $1.5 trillion industry. Cybersecurity events can impact network availability, interrupt operations and halt productivity. To continue to innovate and prosper, you need to secure your infrastructure, help helps protect assets and maintain network availability.
Converging Information Technology (IT) and Operational Technology (OT)
A secure infrastructure provides the foundation that can help you improve asset and system performance to meet your business goals and increase productivity. Rockwell Automation and Cisco have collaborated to develop Converged Plantwide Ethernet (CPwE) Architectures to provide education, design guidance, and best practices.
CPwE helps enable the convergence of IT with OT. This converged infrastructure features the use of standard Ethernet and Internet Protocol (IP) technology – and is the backbone of The Connected Enterprise®. It addresses the needs of and provides for a common model for IT and manufacturing.
Infrastructure Development and Management
The manufacturing industry generates more data than any other sector. Delivering a fully integrated working environment, where information is available and actionable in real-time is a key priority for manufacturers. The latest control and automation technologies offer unprecedented opportunities to optimize productivity and minimize unnecessary costs. However, with the significant benefits of connecting your site and production assets come greater security risks, both internal and external.
A proactive approach to industrial cybersecurity can help. By delivering a single point of contact, Rockwell Automation can help you to design, implement and manage your infrastructure. Regardless of where you are in your infrastructure development process, network services can help you to:
- Assess: Understand the condition of your existing IT and OT assets, and identify and remediate potential performance and security issues.
- Design: Craft a secure information infrastructure that meets your business needs today and scales with you in the future.
- Implement: Deploy a robust and secure infrastructure on time and on schedule
- Validate: Confirm that your network meets installation, security and performance requirements
- Monitor and Manage: Navigate the complexities of maintaining your network to maximize uptime
Pre-engineered Network Solutions
Industrial organizations are adopting virtualization at a rapid rate. From reducing server footprint, extending application longevity and improving system availability and recovery – virtualization can improve your productivity and profitability. However, designing, deploying, and maintaining virtualized infrastructure can be costly, complex, and time-consuming.
Pre-engineered infrastructure solutions can help as they are designed for industrial applications, preassembled and preconfigured to save you time, money and hassle when building your infrastructure.
Shorten your infrastructure project timeline by up to 50%
The Industrial Data Center (IDC) can greatly ease your move to a virtualized environment. The IDC is a scalable architecture allowing you to easily scale up and out as needed. It includes all hardware, software, and installation services needed to deploy a large environment quickly. Furthermore, the Industrial Network Distribution Solution (INDS 1000, INDS 2000, INDS 3000) consolidates design, commissioning, and industrial environmental protection into a pre-engineered network distribution package. This is ideal for expanding an existing network or implementing a new one.
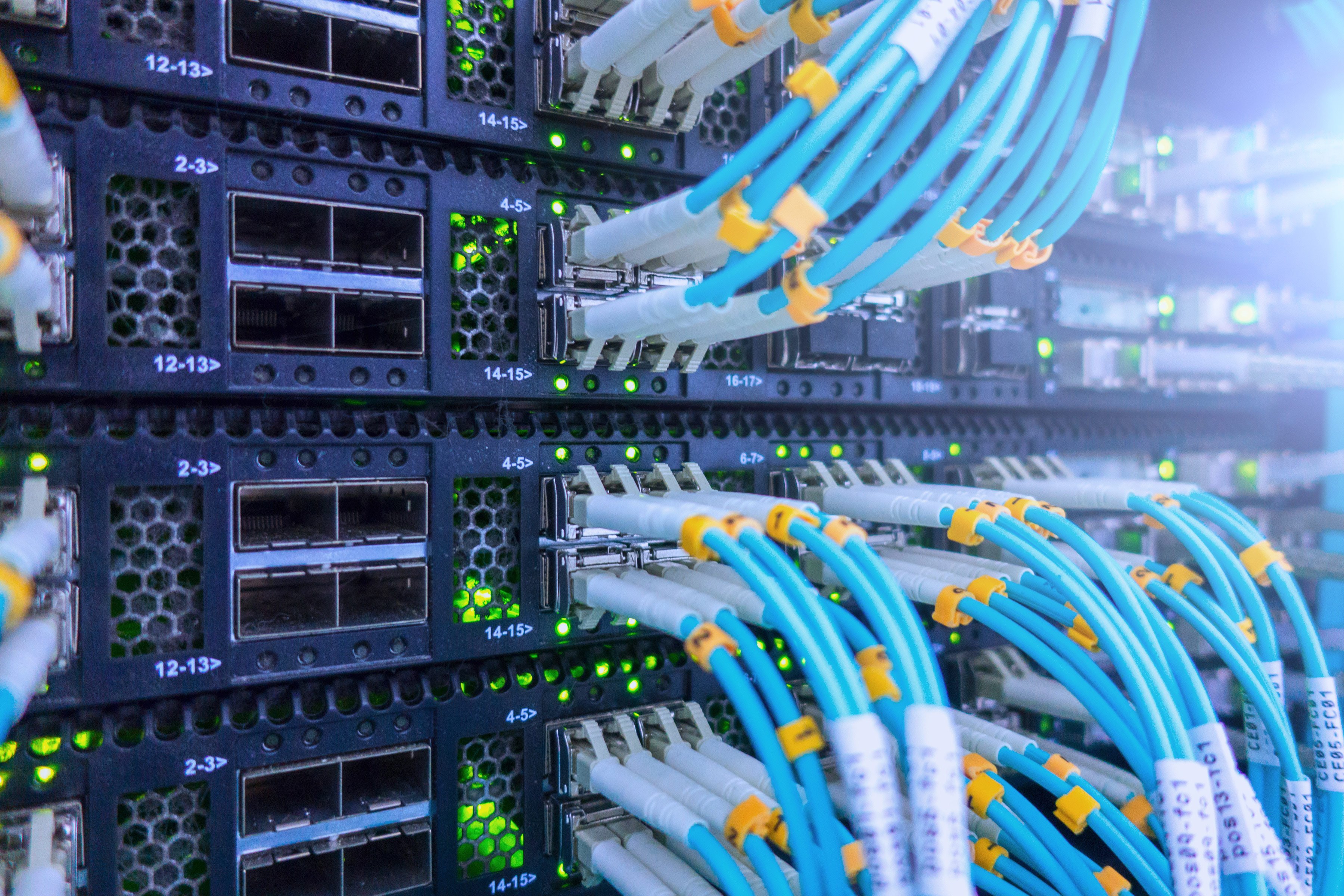
Monitoring your Assets
Once your new infrastructure is up and running, you can connect your assets and optimize their performance. Our industrial asset performance services can help you monitor your assets, improve their availability and identify issues before they lead to downtime.
Asset Reliability Services use the vast amount of maintenance data within your assets to help improve their performance and reduce risk. By creating outcome-based reliability programs and deploying an automated asset-intelligence system that delivers proactive notification of risks, tracks device changes and helps streamline maintenance-based decisions – downtime issues can be addressed.
Remote Monitoring and Analytics Services can help you monitor your critical assets and gain valuable insights into their performance. Production data, asset health and diagnostics and other information help your team make better decisions. Analytic and predictive outcomes can be used to identify or even help prevent downtime issues.
Preventive Maintenance Service Agreements can keep your critical assets running at peak efficiency. Proactively identifying pending system failures and which components should be repaired or replaced can reduce costs. This reduces or eliminates the unnecessary repairs and associated costs that occur with most time-based preventive maintenance programs.
Oil Giant Improves Cybersecurity, Lowers Manpower Costs
A large, global oil company needed a comprehensive system for gathering data from thousands of control devices, spanning six geographically dispersed oilfields. They were previously using a manual database but the information was incomplete and the collection method could not keep up with the large and dynamic installations. This included several generations of mission-critical assets. Furthermore, a corporate SCADA audit identified cybersecurity risks related to the lack of reliable control-asset data.
Rockwell Automation was able to help by implementing an Innovative Diagnostic Reliability (DR) system that provides centralized information gathering and continuous monitoring of the company’s assets. The DR system also takes a deep dive into each asset to understand its status, health and parameter changes
With improved tracking capabilities, including scans for security vulnerabilities, the system continuously checks the key switch status on processors to avoid potential cyberattacks. The DR system reports if devices are moved or missing for company personnel to address.
This resulted in full compliance with a new corporate cybersecurity policy, based on the ISA99 standard for industrial control systems. In addition, by moving from a manual database to automated real-time data collection, the company can now perform proactive maintenance. This is helping lower the cost of manpower in the field and yields more barrels of oil per day. The oil company is so impressed by the preliminary results that it is considering using the DR system as a corporate global standard.
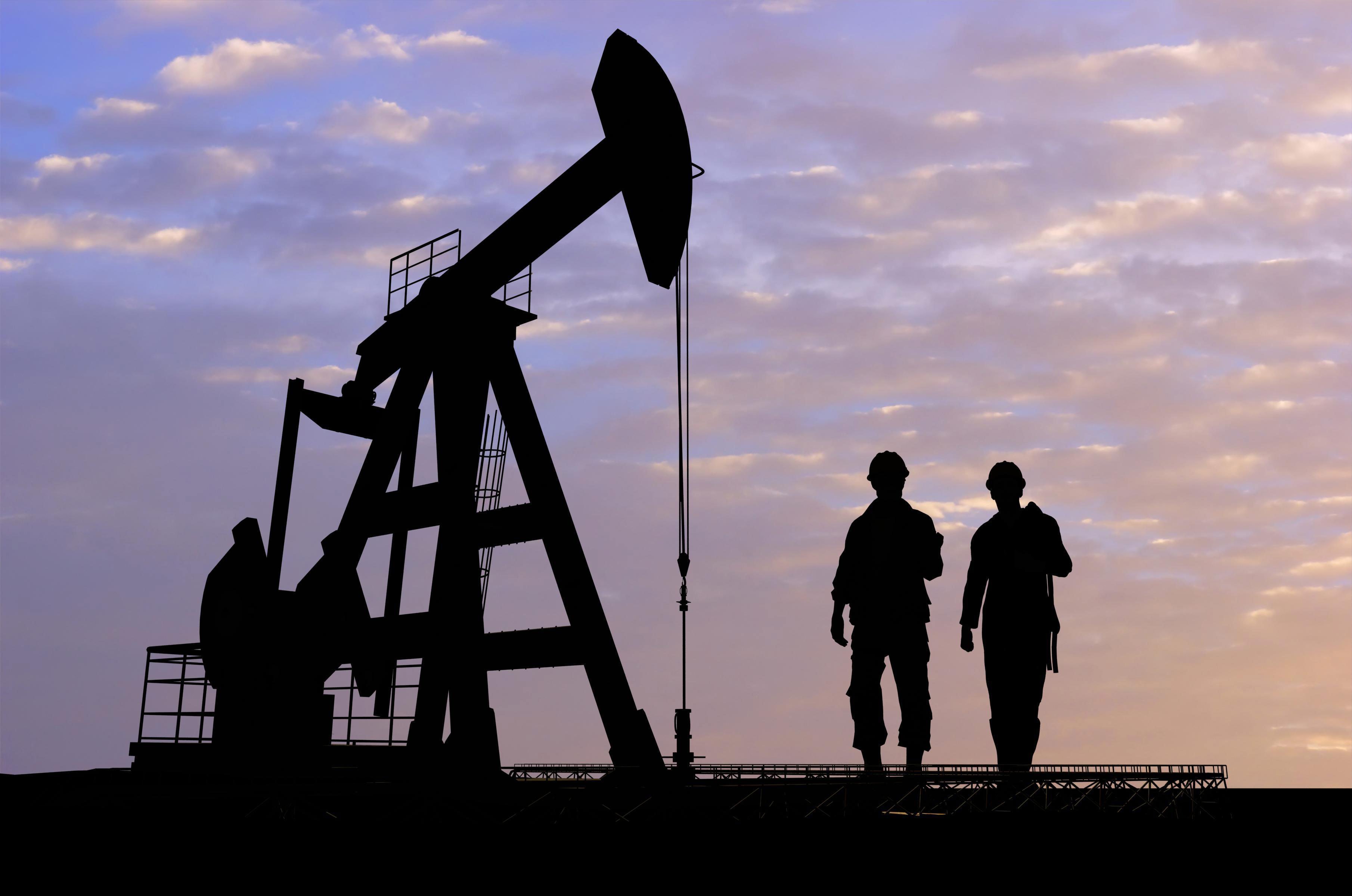