It is an all too familiar scenario, a critical manufacturing line is down and for each minute of downtime, thousands of dollars are lost in productivity. All manufacturing plants experience challenges with downtime but although it is a common challenge, the way organizations respond can influence productivity.
Improved uptime can be achieved when remote monitoring is part of your application support service. The examples below indicate what happens when a company relies on traditional call center support in a downtime situation, compared with the alternative scenario, when a company has a Rockwell Automation contract for application support with remote monitoring.
Scenario 1: A traditional technical support solution
Mike is an operations manager for a global manufacturer. The company was having trouble with unscheduled downtime. In the past few months, several critical assets have gone down and unfortunately Mike and his team do not have visibility into the root causes.
Today, an alarm went off because a critical production line went down again. The operations team quickly notifies Mike because the company could lose thousands of dollars for each minute this line is not producing. Mike immediately calls his on-site maintenance team to start troubleshooting the issue. Several hours later, the maintenance engineer is still unable to find the cause and calls an off-site technical support center.
Several support engineers are engaged to assess the issue but after hours of troubleshooting, the technical support engineer determines an on-site visit is necessary to isolate the issue. The technical support center sends a specialist who spends a few hours familiarising himself with the line, trying to determine the issue. He works with Mike’s operation team to correct the server motor program. After 10 hours and $50,000 in downtime later, they finally get the line up and running.
With this traditional technical support solution, hours are spent troubleshooting with both on-site and off-site teams engaged. Furthermore, with no capacity for remote monitoring, hundreds of thousands of dollars can be lost from downtime.
Scenario 2: Application support with remote monitoring
Rachel is the director of production at a large beverage company that has also been trying to reduce unscheduled downtime. Last quarter, she implemented an application support with remote monitoring service contract offered by Rockwell Automation. It is a proactive approach that helps her company drastically reduce the number of downtime incidents, giving her more peace of mind. Rockwell Automation assigns a dedicated technical support team to specific customer accounts so they know their systems inside and out.
Rachel’s timing was perfect. The day she returned from vacation, Sofia – a Rockwell Automation application support engineer, was monitoring their system remotely and called the production line supervisor just before an alarm went off. Sofia noticed a positioning error fault on the number two palletiser, indicating that one of the servo motors was failing. The line operator diverted the packaging to the number three palletiser, before any product was damaged. Sofia confirms that the servo motor needs to be replaced, which allows the on-site team to resolve the issue quickly.
The following day, Logan, who is also part of Rachel’s Rockwell Automation support team, calls the shift control engineer. He notices a duplicate MAC ID error. With Logan’s help, the control engineer is able to access the drives communications parameters and resolves the issue quickly. Rachel is notified about the event and that it has been resolved quickly.
In contrast to the first scenario, with this application support and remote monitoring, manufacturers benefit from proactive support, 24 hours a day, seven days a week, 365 days a year. Advanced troubleshooting is provided by a remote monitoring team helping you to avoid hours of costly downtime.
Virtual support on hand
During the COVID-19 pandemic, manufacturers have been challenged to support their organizations effectively, efficiently and remotely. Lockdowns and border closures have made it difficult for face-to-face interactions. Thankfully, virtual technologies can help. FactoryTalk InnovationSuite Vuforia Chalk is a powerful collaboration and communication tool for your organization’s experts to provide real-time assistance to technicians facing complex or unfamiliar challenges. With augmented reality you can quickly scale problem-solving guidance, support and expertise to your factory operations and service teams.
Quickly scale problem-solving guidance, support, and expertise to your factory operations and services teams with Augmented Reality.
As many companies and employees are navigating their ‘new normal’, digital transformation and modernization in their plants are a top priority. LifecycleIQ services can support your organization along your modernization journey by utilizing accessible technologies and expertise.
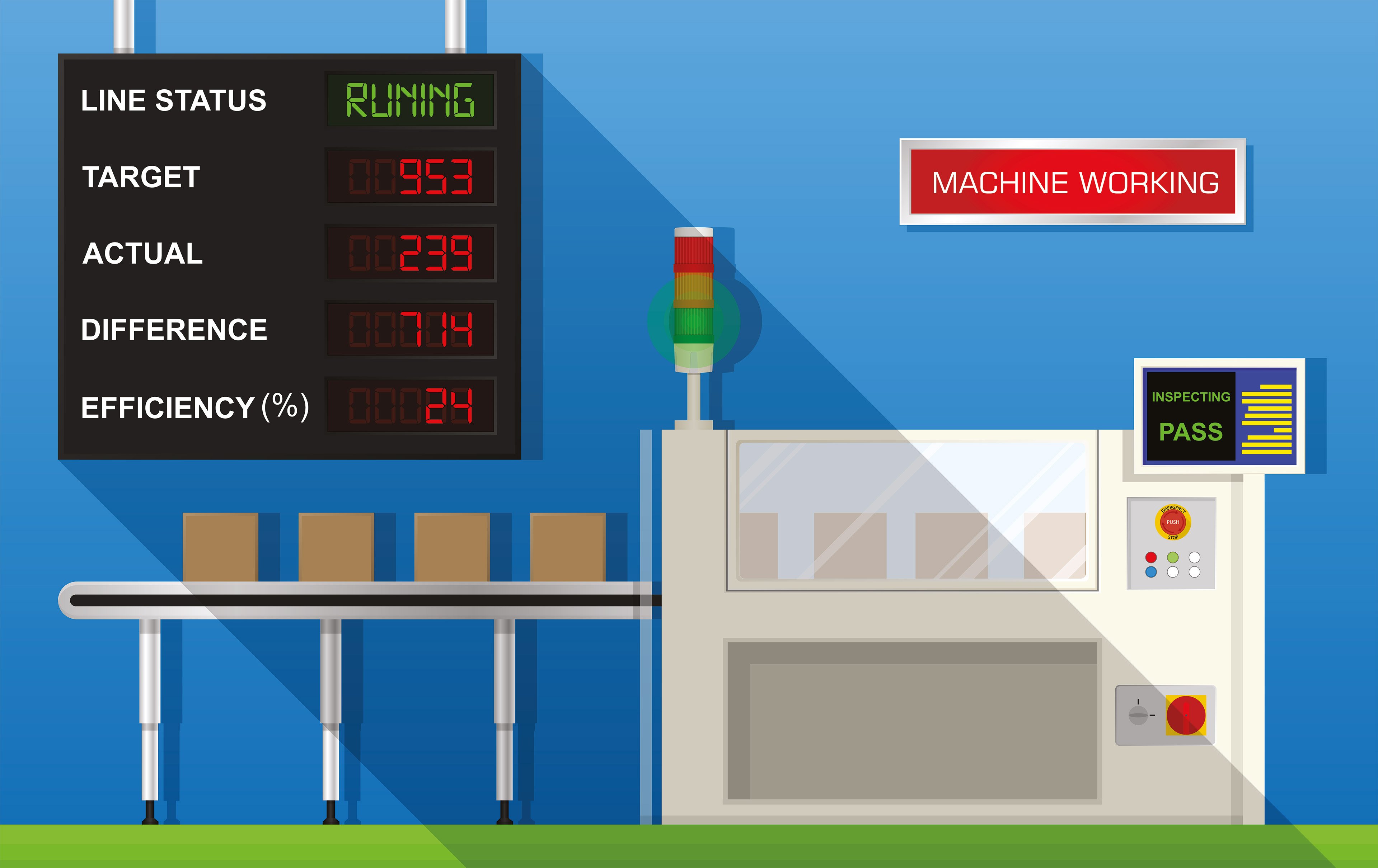
Remote monitoring and support improves uptime
More. Better. Faster. Is the slogan for any commodity manufacturer intent on prevailing in the marketplace. And it is a familiar mantra at one paper mill in the U.S. Midwest. This particular mill produces corrugated paper from recycled paper – definitely a commodity good but the operation is far from run-of-the-mill.
Several years ago, one of the mill’s aging paper machines began to show signs of wear and inefficiency, threatening the mill’s high standards of productivity and uptime. Replacing the colossal machine meant a major investment in time and capital, but it was unavoidable.
To optimize asset performance and uptime, the mill specified a Rockwell Automation control solution. The machine, engineered by Rockwell Automation, uses an AllenBradley PowerFlex 755 AC drive system to provide adjustable-speed motor control for the wet end, dryer, reel-and-spool and winder sections. The control architecture incorporates a total of 30 drives and motors, running from 5 to 400 horsepower. The machine also is equipped with an AllenBradley ControlLogix programmable automation controller to integrate the drive systems, and execute all control and motion functions.
After working through the challenges of installation and commissioning, the mill’s management realized that their ongoing maintenance requirements would exceed the capabilities of their small crew. They decided to support machine maintenance through remote monitoring.
A team from the mill toured another company’s steel mill and spoke with the plant’s lead engineer about their positive experience with Rockwell Automation. Following these discussions, the team at the time was confident that a Rockwell Automation Assurance Integrated Support contract was the way to go.
Rockwell Automation worked closely with mill engineers and management to provide detailed financial justification for the support agreement. They used machine historical data to calculate the potential cost avoidance of downtime and labor expenses against increased uptime and efficiency. The analysis was thorough, and the lifecycle savings were compelling.
Today, Rockwell Automation provides the mill with real-time, application-level industrial support from a designated team. The support includes 24/7 remote monitoring of more than 2,000 machine data points, supplemental consultation on machine changes and additions, and quarterly performance reviews.
The results are outstanding. The mill has achieved a 91 percent system uptime, reduced labor and parts costs, improved asset performance, increased paper machine return on investment, as well as documented lifecycle savings.
“The remote monitoring and support we get from Rockwell Automation has definitely helped with our uptime,” the supervisor said. “When we have a problem, it becomes their problem as well. They help us work through it and provide the additional knowledge to address the issue. That kind of help can be priceless.”
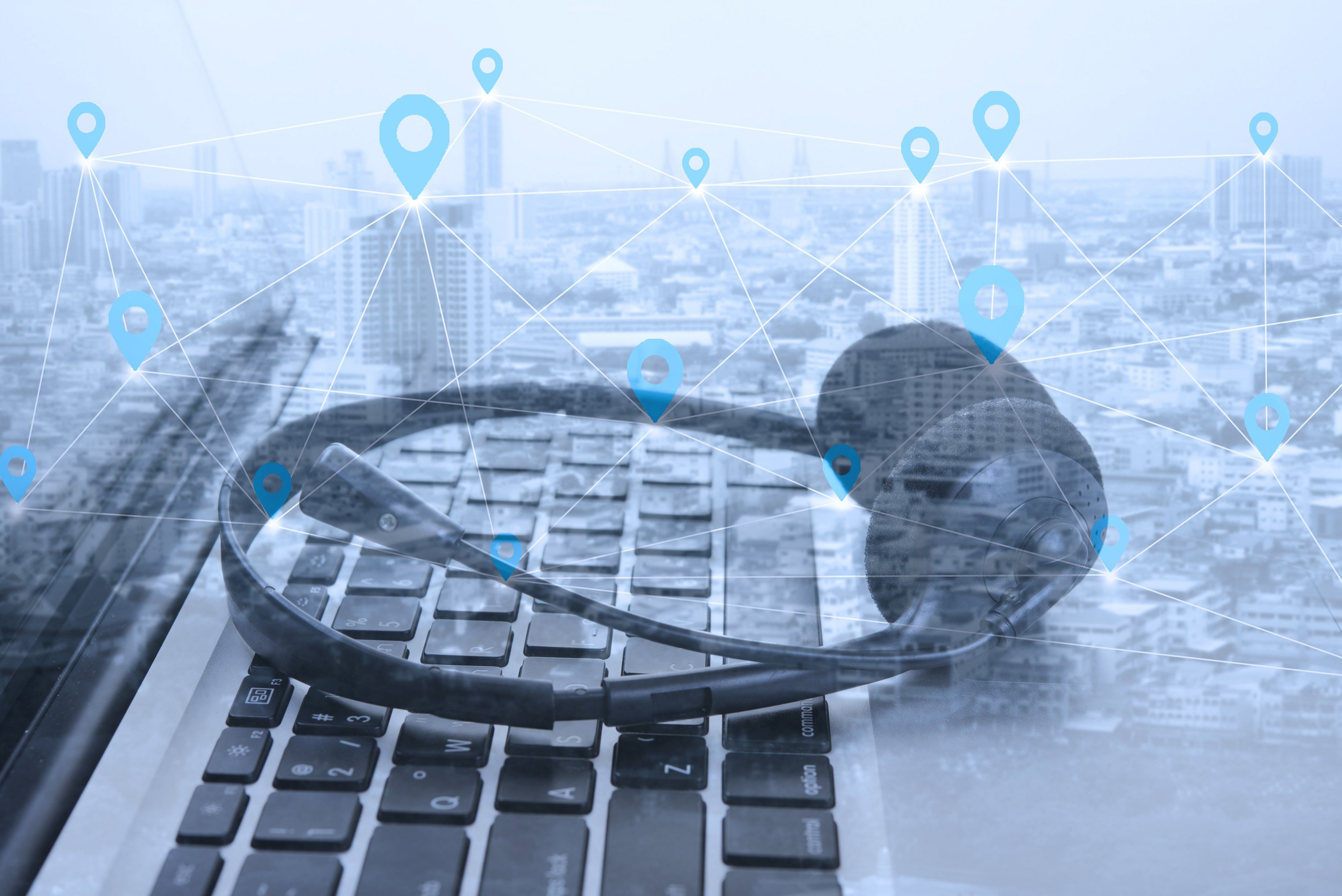