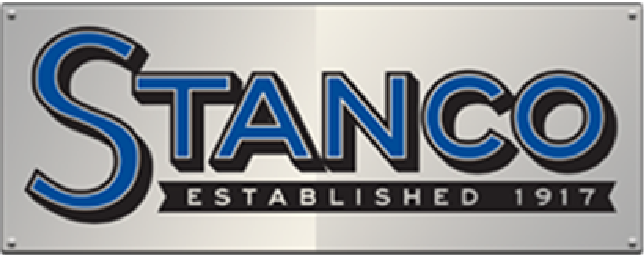
Established in 1917 and a fourth-generation, family-owned business Stanco Metal Products provides metal stamping as their main business and fabrication services in one of their three facilities throughout the United States.
- Antiquated ERP system provided zero visibility and real-time data
- Inefficient processes required manual scheduling and short prep time for workers
- Inability to track parts and provide traceability to customers
- Improved scheduling capabilities, from weeks out to months ahead
- Streamlined processes across all departments, including production, tool and dye, shipping and receiving, and more
- Provided customers with full traceability and transparency
Challenge
Lack of Visibility and Traceability with Legacy ERP
As a company established over a century ago, Stanco Metal Products relied on outdated systems to manage their metal stamping and fabrication processes. Their legacy ERP system, which was nearly DOS-based, created a “dark hole” of information, as Ketih McLane IT Systems Analyst at Stanco says.
The lack of real-time visibility hindered the company’s ability to track inventory, manage accounts, and schedule jobs efficiently. The process involved manual, paper-based communication, with the office delivering physical job books to production floors for scheduling. In addition, the company had no reliable way to trace parts from production to delivery, creating inefficiencies and limiting the ability to provide quality assurance to customers.
Solution
Implementing Plex ERP for Streamlined Operations
To bring their operations out of the dark and into a modern, data-driven environment, Stanco implemented Plex ERP. With the new system, they gained real-time visibility into every aspect of their business, from inventory management to accounts receivable and payable.
Plex allowed their production teams to view schedules in real time, eliminating the need for physical job books. Tool and dye workers could now prepare jobs months in advance, improving production flow. Shipping and receiving also benefitted from the real-time order visibility, enabling them to better prepare for upcoming shipments.
Result
The impact of Plex ERP on Stanco was profound. Scheduling, which used to only extend two weeks in advance, now allows for production planning months ahead. This change streamlined operations across departments, from production to shipping, ensuring that teams were always prepared for upcoming jobs.
One of the most transformative features of Plex ERP for Stanco was its traceability capabilities. Every part produced now comes with a serial number that can be traced back through the entire production process, all the way to the original material receipt. This provided the traceability their previous system lacked, allowing them to offer their customers complete transparency and quality assurance.
As McLane says, “Processes have gotten a lot easier. Next at Stanco is to keep implementing more modules. With Plex, you’re never finished. There’s always something new to add.”
Published September 25, 2024