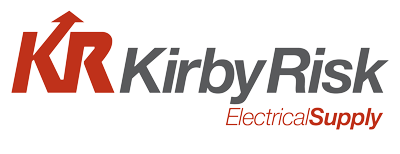
Kirby Risk Corporation is a multi-faceted organization dedicated to meeting customer needs with innovation and effective solutions. Kirby Risk provides a wide range of services including quality electrical supplies, electrical apparatus sales and repair services, wiring harness/cable manufacturing and quality industrial component manufacturing.
The food manufacturer featured in this story is a Fortune 500 company. They have more than 40 manufacturing facilities in the U.S. and a diverse portfolio of iconic food brands.
- Unplanned line stops
- Increased safety risk
- Manual troubleshooting increased downtime
- Costly production delays
- Unplanned downtime – reduced by 75%
- Preventive maintenance time – reduced by 50%
- Cost savings – ongoing savings of $70,000/year
- Fast upgrade – saved 61% in installation time/packer
Challenge
Known for its quintessentially American brands, a packaged foods leader was running two case packing lines for its refrigerated whipping topping product when a costly downtime event occurred.
The maintenance team had to examine long wiring runs in order to locate and repair the issue, which was traced to the tongue interlock door switches. Wiring of multiple safety tongue interlock switches and e-stops in series to a safety relay made troubleshooting difficult and caused delays. Ultimately, one of the packing lines was down for more than 70 hours.
The manufacturer needed a solution that would alert for safety issues with the packing machines and minimize downtime by enabling the maintenance team to identify the problem faster. The company turned to its trusted supplier, Rockwell Automation distributor Kirby Risk, for a solution.
Solution
Kirby Risk has been providing customers with Rockwell Automation products and solutions since 1940. When this customer reached out to the Kirby Risk automation team to discuss downtime issues, the customer’s project engineer was interested in Allen‑Bradley® SensaGuard™ non-contact safety switches as a replacement. Status LEDs on these switches provide visual indication when a door is open. However, after collaborating further with the Kirby Risk Rockwell Automation Safety Consultant, the customer chose to upgrade the safety system with GuardLink™ device-level safety linking technology.
Kirby Risk also suggested a risk assessment by the Rockwell Automation Safety Services team, which provided safety improvement recommendations. The distributor worked with the project engineer to utilize Rockwell Automation Safety Automation Builder® to streamline the safety system design and import the data to SISTEMA for performance level verification.
Diagnostic Data Speeds Issue Resolution
A primary advantage Kirby Risk brought to the customer was visibility into its machines for faster issue diagnosis and resolution. The SensaGuard non-contact safety interlock switches and e-stops were wired to Dual GuardLink safety relays using GuardLink Smart Tags, which communicate door status and other diagnostic information to the case packer’s ControlLogix PLC via the Guardmaster® EtherNet/IP™ Network Interface. The operator interface indicates not only when a door is open or an e-stop is actuated, but also which device is tripped, saving critical time and avoiding the need to check every door and e-stop before the machine can be restarted.
The upgrade to advanced diagnostics represented one of this customer’s steps toward smart manufacturing. The GuardLink solution also helped the company achieve the highest safety level and increase worker safety.
“It’s always rewarding to be able to provide a solution that helps operators do their jobs efficiently and safely,” said Amber Gray, Automation Consultant at Kirby Risk. “Having that relationship where you are a trusted advisor – the person customers call for guidance – is key for our business.”
Result
Smart, integrated safety system reduces downtime and total cost of ownership
GuardLink’s simple, quick-disconnect wiring saved the packaged foods manufacturer 61% in installation time per case packer, which minimized downtime with the upgrade. Ongoing preventive maintenance time has been reduced by 50%, and average unplanned downtime has been reduced by 75%. The reduction in maintenance and overall downtime delivers ongoing savings to the company of more than $70,000 per year.
“Our customers depend on us to support them in achieving real, measurable savings,” said Gray. “With Rockwell Automation products, I can help them drive the highest levels of safety performance – one of their top priorities – and reduce downtime and cost.”
Published May 20, 2024