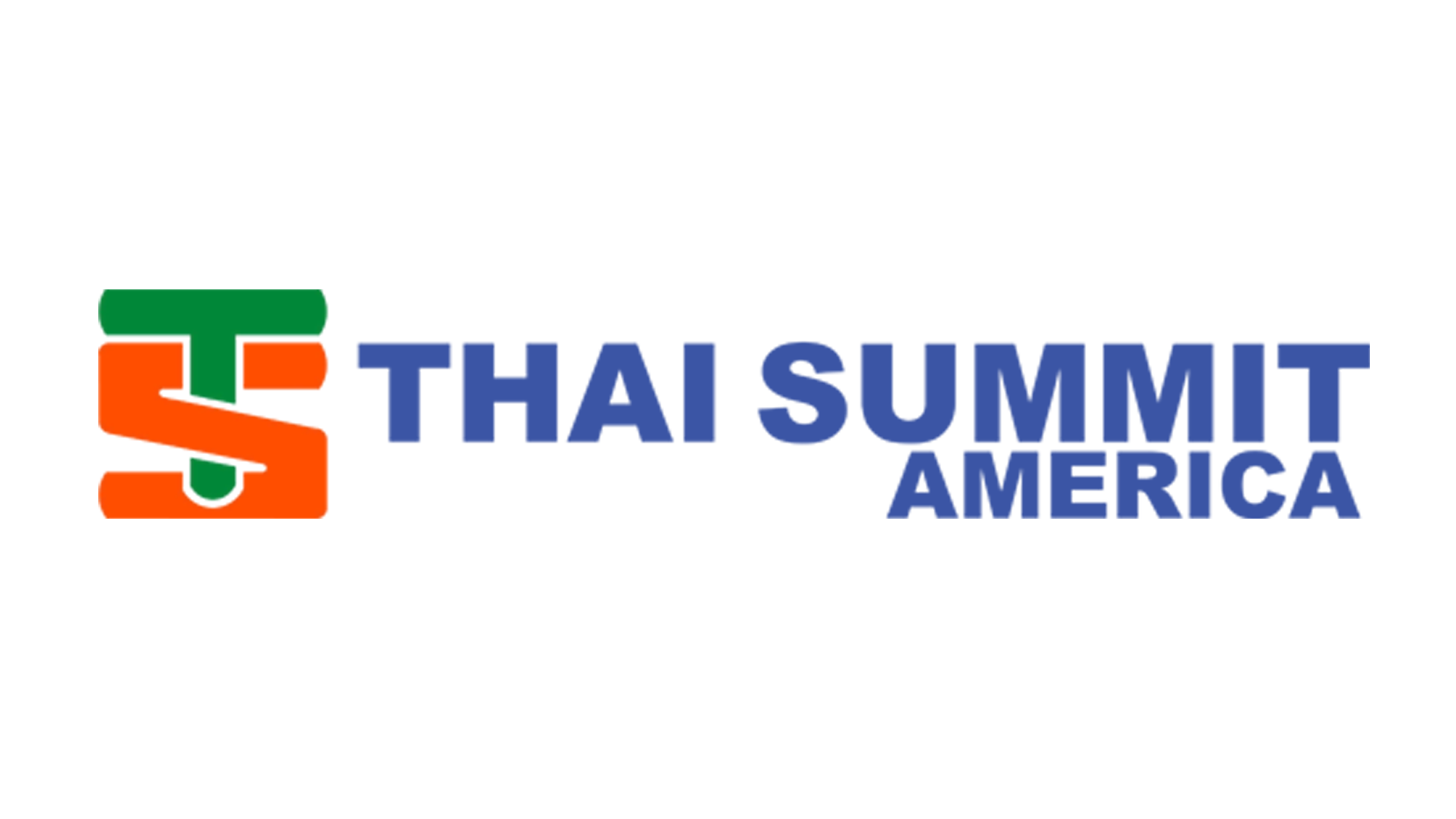
Thai Summit has made a name for itself as a leading global supplier in the sheet metal stamping industry. For over 35 years, they have provided their customers with world-class engineering, stamping, and assembly capabilities. With facilities in North America and Asia, Thai Summit is simultaneously serving a global customer base and delivering world-class technology.
- Labor shortages and constraints in manufacturing
- Inability to track downtime and stoppages
- Customers seeking more manufacturing transparency
- MTBF increases from 10-20 minutes to 40 minutes
- Line revenue increases from $8,000/hour in parts per shift to $12,000/hour in parts per shift
- Employee-led projects that leverage the Plex system have led to more than $3M in savings per year
- 80% decrease in day-to-day downtime
- Increased throughput by 70 – 112%
- Ability to provide data to customers
Challenge
Thai Summit is a leader in the sheet metal stamping industry. Their Howell, Michigan facility was the first manufacturing site in North America to productionize automated Visual Inspection systems and introduce remote laser welding. This 1.2 million square foot facility houses assembly bays, tool and die services, warehousing space, and more to help support production in North America. In partnership with customers, Thai Summit’s engineers design, manufacture, and regularly inspect their tools to ensure quality and longevity.
With labor shortages and constraints in manufacturing, Thai Summit needed a solution that could improve their day-to-day processes and help them to contend with industry challenges. After working through the global pandemic and juggling the industry impact of reduced labor availability, Thai Summit needed a way to better track downtime data, locate areas of micro-stoppages, and improve their overall manufacturing processes. Customers require increased visibility and are therefore more involved on the plant floor, asking questions and seeking out answers. Thai Summit saw an opportunity to use data as a differentiator.
Solution
The Power of Data
Since their initial implementation of Plex MES in 2017, Thai Summit has evolved their digital transformation efforts by implementing Plex MES Automation and Orchestration (MES A&O). This powerful, no-code tool enables automation of processes and orchestration of complex workflows, avoiding the need for heavy coding and manual data management, improving accuracy, and freeing valuable resource time. This new solution provided Thai Summit with the ability to capture and distribute information to their customers and partners.
This not only increased overall visibility, but it also strengthened data capture, giving Thai Summit peace of mind, and establishing a system to locate bottlenecks and areas of micro-stoppages with increased efficiency. With the Plex system in place, Thai Summit is now able to meet the needs of customers who have increased reporting requirements, resulting in new work opportunities.
Better Data Leads to Improved Maintenance Processes
“We have automated the process from the Plex system to automatically put our work center status into downtime when the equipment knows that we’re down,” said Janice D’Amico, Thai Summit Executive Manager of Business Systems and IT. “Then we have our team leaders and our operators providing the detailed reason for the downtime.”
While downtime will always exist, the ability to locate it quickly has been a game changer for Thai Summit. Having software available to tell employees when and why their machines are down versus in-person plant floor checks has allowed for more efficient problem-solving. This is not only saving money, but also improving overall quality. Thai Summit can now pinpoint any micro-stoppages in their facilities, identify the equipment causing the downtime, and allocate the right resources to solve the problem. The time between machine failures has also increased, pushing the mean time between failures from 10-20 minutes to 40 minutes. This improvement, amongst others, has brought revenue for the line from $8,000/hour in parts per shift to $12,000/hour in parts per shift.
Thai Summit Empowers Employees
Thai Summit also prioritizes continuous improvement through employee suggestions and worker empowerment. By collecting input from those working directly with the products and lines, Thai Summit has seen major savings and received over 200 employee suggestions to date.
Not only has this initiative empowered employees to share their ideas but it has also allowed the team to see that their suggestions have an impact and are being used to improve business. Thai Summit has experienced a cost savings of at least $3 million per year as a result of employee suggestions, with significant payouts to employees and teams delivering valuable suggestions.
Result
Productivity Abounds
Since their initial implementation of Plex MES in 2017, Thai Summit has evolved their digital transformation efforts. As they work towards becoming pioneers in digital manufacturing, Thai Summit employees have moved away from programs such as Excel and paper-based processes. This shows Thai Summit’s commitment to digitization and to its customers. Thai Summit currently has two facilities running the Plex solution.
Less Downtime
Prior to Plex, Thai Summit was experiencing 1.5 hours of downtime during an 8-hour shift on lines in their facility. Since implementing MES A&O, this number has dropped to approximately 20 minutes of downtime per shift, sometimes even less. This equates to nearly an 80 percent decrease in day-to-day downtime.
With Plex software available to tell Thai Summit when and why downtime is occurring, the need for in-person equipment checks has also decreased. This is not only streamlining the day-today processes but it’s also giving employees the opportunity to focus their attention on higher value-added tasks.
Differentiating with Data
The automatic tracking available with the system gives Thai Summit team leaders and operators the opportunity to produce detailed reporting daily, further adding to their overall efficiency. With a deeper level of detail when it comes to data reporting to customers, Thai Summit stands out amongst competition.
With the help of Plex’s data collection and Thai Summit’s ability to apply the proper resources to the areas that need it, they jumped from 40-50 jobs-per-hour to 85 jobs-per-hour, increasing throughput by 70-112%. They have also included a training coordinator who’s now working with IT to provide virtual instruction for operators on the plant floor, improving training processes and minimizing risk of human error. Now, Thai Summit and its employees have their eyes set on the future with plans to take the Plex system to the next level. They will continue to improve machine efficiency, advance maintenance maturity, incorporate new manufacturing technology into their processes, and continue to grow as a leading supplier in the automotive industry.
Published February 12, 2024