How to Design a Digital Transformation Architecture at Life Sciences Organizations
Integrated systems are the foundation of digital transformation.
To derive meaningful insight from the data generated by thousands of devices across global facilities, Life Sciences manufacturers need to adopt a new information strategy. It’s nearly impossible to establish enterprise-wide visibility when facilities are operating in digital siloes and leveraging poorly integrated systems. Only an intelligent architecture built for the industrial enterprise provides the connectivity and control required to realize the value of digital transformation.
An intelligent architecture establishes control and reduces variability by building intelligence into processes that are enforced and acted upon by the system. Knowledge-driven operations rely on seamless interconnection between the assets and processes that control production. When the control system anticipates deviations in the process, it can proactively guide operations to take action to maintain optimal conditions.
When designing an intelligent architecture, the key is bi-directional, seamless data flow. The systems governing production must be able to both monitor and influence production control. But the production environment is complex; production planning is as integral to success as information and control. True digital transformation requires all systems from the shop floor to the top floor to be integrated through an interconnected architecture.
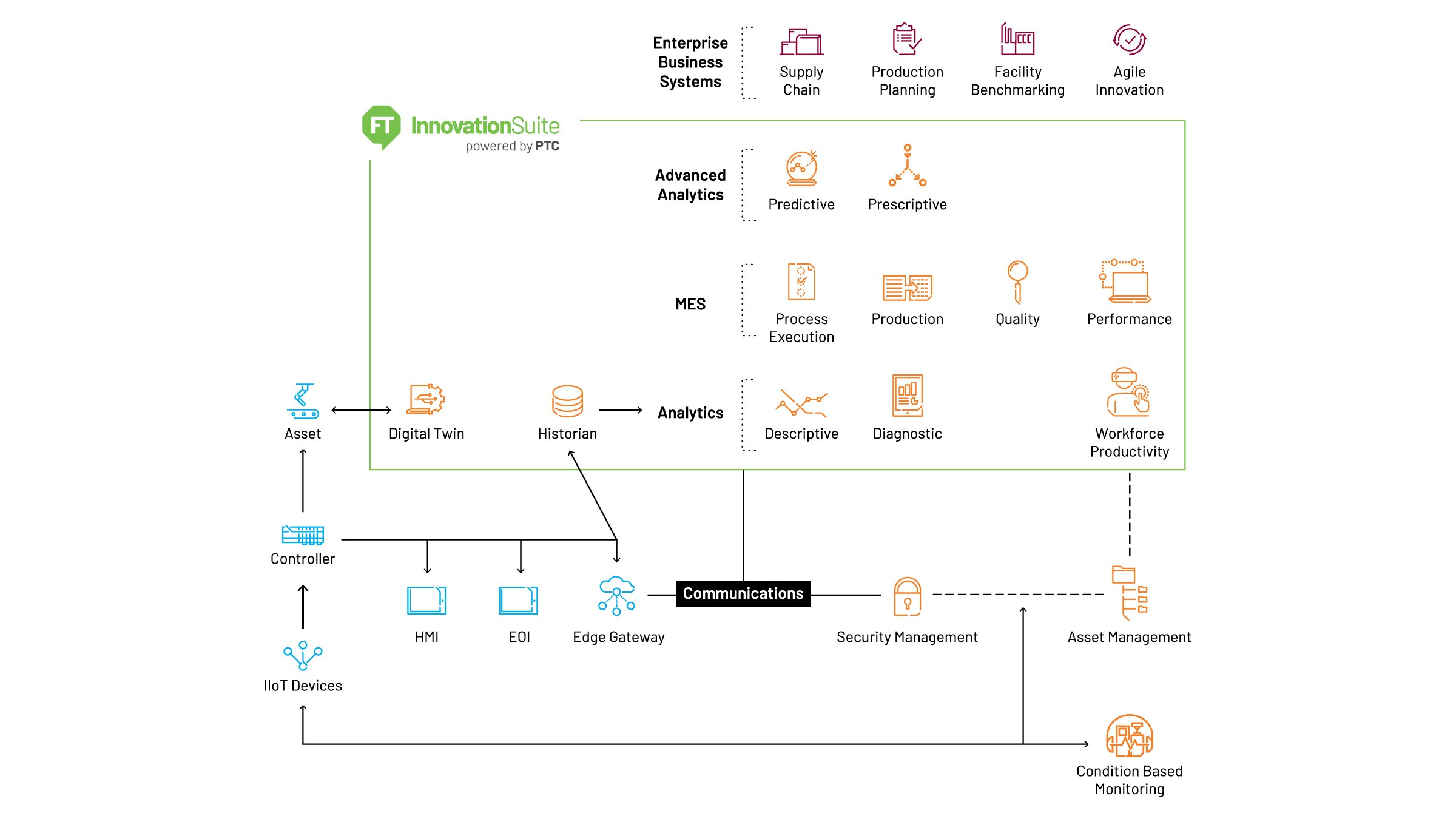
Universal Connectivity
Every digital transformation journey starts with connectivity. Universal connectivity enables the information generated by your operations – from machines, equipment, people, and more – to become available for consumption by higher-level systems. This single point for data aggregation and integration lays the foundation for all digital transformation initiatives to follow.
Establishing connectivity to your OT equipment and system doesn’t have to require revalidation. Through read-only connections, Life Sciences manufacturers gain visibility into rich OT data without altering their control system. This provides meaningful insight into performance and drives actionable insights for future process improvements.
Manufacturing Operations Management
Production control and information management systems are the heartbeat of your digital transformation. These systems monitor current operating conditions and manage enforceable workflows to maintain optimal throughput and outperform quality standards. Integrating the information from your operations management systems into this layer affords manufacturers a greater level of consistency than would be possible through control or information alone.
These systems also fuel continuous improvement and error-proofing initiatives. An integrated information enablement strategy adds critical production context to data, enriching future analytics projects with insight into machine- and product-level context.
Enterprise Integration
Integration into the broader enterprise enables facilities to adapt to the needs of the market. Enterprise systems like Enterprise Resource Planning (ERPs) provide valuable production planning context to production control systems like Manufacturing Operations Management (MOMs). This allows for autonomous production planning and execution based on customer orders.
Life Sciences organizations need to expand beyond intelligent, siloed facilities and begin building their intelligent facility network. This provides visibility into enterprise-level production and enables dynamic scheduling across the network, reducing your time to market and cost of inventory.
Operational Intelligence
Operational intelligence is the backbone of your digital transformation. Industrial analytics transform operations data into actionable insights, enabling transformative capabilities. With an interconnected architecture, analytical models can be deployed anywhere from edge to cloud to uncover meaningful insights and prescribe the appropriate action. These prescriptive insights drive process optimization by constantly modelling the impact of changes on the current state and identifying the optimal action.
Knowledge-Driven Operations
Analytics are only valuable when insights are connected to the right people and systems at the right time. The bi-directional data flow that is inherent in a well-designed intelligent architecture enables information-driven production control at the asset or facility level. Autonomous systems remove human error from the production process and deliver more consistent results. But systems aren’t the only aspect that benefit from knowledge-driven operations. Operators armed with integrated AR solutions receive real-time alerts and prescriptive insights leading to more informed decisions and efficient production.
Improving the Employee Experience Across the Facility
Engineering Design
Validating changes to an existing line may not be worth the investment if you’re not confident in the resulting value for production. With access to rich data from operations and digital twin simulations, engineers have the capability to investigate and verify the impact of process improvements before the organization makes any changes in the physical world. This functionality empowers engineers to confirm improvements in quality and throughput, reducing risk in the revalidation processes.
Operations
Access to real-time production data and prescriptive analytical insights in a single pane of glass takes the guesswork out of operations for your employees. Armed with role-based dashboard views and prescriptive guidance, connected workers identify production issues and prevent losses before they occur. And digital work instructions visualized through AR delivers on-demand, hands-free guidance on the shop floor to reduce process errors and accelerate issue resolution.
Maintenance
Keeping up with increasingly complex equipment and maintenance procedures is challenging for any engineer, especially those new in the role. However, when engineers have access to predictive insights and digital work instruction visualizations, they achieve higher first-time fix rates and accelerate time to resolution. Additionally, enforceable workflows and automated record keeping confirm machine calibration and cleaning procedures are completed on schedule.
Quality Assurance
Digital recordkeeping streamlines compliance and accelerates batch release by simplifying the review process. Electronic batch records automatically capture the key quality and compliance information throughout production without requiring human intervention. This provides immediate access to accurate data and enables review in real time by exception only. There’s no longer a need for the quality assurance team to wait until a batch is complete to review quality.
Production planning
Managing a global supply chain and adapting to disruption is the new normal for production planning. End-to-end supply chain integration provides full visibility into raw material inventory, expiration dates, work in progress, and customer demand across the enterprise. These insights empower production planning managers to dynamically schedule production to meet the needs of the market while minimizing operating costs.
IT/OT Administration
As production and IT systems become more integrated and responsibilities are shared, streamlining IT/OT convergence is critical. Interoperable IT and OT systems simplify and drastically shorten the process to integrate new applications into the architecture. And with point solutions and major platforms offering varying stability and support, IT admins can rest easy knowing their digital transformation architecture is built on a platform that provides longevity and recognized stability.
Companies that invest in an enterprise-wide transformation strategy built upon an intelligent architecture will be best equipped to adapt to shifts in the market and capitalize on tomorrow’s opportunities. Integrated technology provides access to the information needed to make decisions in real time and optimize operations in any situation.