You may also be interested in
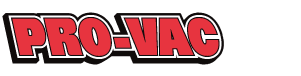
Pro-Vac is an advanced full-service storm maintenance and environmental service company serving customers throughout the Pacific Northwest. Based in the Seattle area, Pro-Vac operates a substantial fleet of over a hundred assets that require regular maintenance. Their slogan, “Because size matters,” is no joke; nationally, Pro-Vac operates an impressive team of 50-plus mechanics spread across 13 North American sites. The team is responsible for managing the repairs and maintenance of over 700 assets, working around the clock to make sure that all equipment is in top-notch condition and ready to be put to the test on the road.
- Existing systems couldn’t keep up with rapid growth of business
- Relied on manual processes for data entry and assessing availability of inventory
- Poor visibility on different site locations
- 27% reduction in fleet downtime
- 17% improvement in route planning efficiency
- 12% better accuracy in fuel consumption tracking
- Streamlined compliance for DOT audits
Challenge
Keeping Up with Rapid Fleet Management Growth and Multi-Site Visibility
Dealing with fleet equipment is a challenge. The equipment is literally on the move and subject to the wear and tear and physical demands of driving long distances. But with the recent acquisition of new sites, Seattle-based storm maintenance and environmental service company Pro-Vac team found themselves in an interesting position. The company had expanded, acquiring new sites and growing its fleet to over 700 assets. Managing such a geographically dispersed fleet, with more than 200 pieces of equipment at a single site, required seamless coordination and visibility across locations.
Jeff Potts, Director of Fleet at Pro-Vac, expresses both excitement and concern: “We’ve grown exponentially, and understanding what’s happening across all these sites, along with how each mechanic is performing, can be overwhelming.
Specifically, keeping track of equipment status and responding to work orders in a timely manner became a significant paint point. Just as someone's personal car alerts them every thousand or so miles that service is needed, fleet trucks work the same way. The team’s existing systems lacked the ability to scale and provide centralized oversight, making it difficult to maintain reliable, road-ready equipment.
Solution
Streamlined Fleet Management and Maintenance with Fiix CMMS
Pro-Vac adopted Fiix® CMMS, a centralized platform that integrated smoothly with their current fleet management tool Samsara. This integration allowed critical fleet data, such as mileage, hours, and maintenance schedules, to flow into the CMMS automatically, eliminating the need for manual data entry.
The platform’s ability to track work orders, evaluate asset criticality, and prioritize tasks significantly reduced bottlenecks. Drivers now submitted work requests with accompanying photos, enabling Pro-Vac to make faster, more informed decisions.
Additionally, the systems’ inventory management capabilities helped the team set minimum stock thresholds so that parts were available when needed. Fiix® CMMS also simplified compliance with Department of Transportation (DOT) regulations by centralizing maintenance records.
Result
Fleet Management Efficiency, Reduced Downtime, and a Foundation for Scalable Growth
As the team says, Fiix® has been a lifesaver for Pro-Vac. It’s a part of the company now, giving real-time snapshots of the fleet’s health and helping them scale.
By leveraging Fiix® CMMS, Pro-Vac achieved tangible improvements across company operations. The integration of the CMMS with Samara allowed for seamless tracking of fleet data, reducing downtime by 27% through proactive maintenance scheduling. Enhanced visibility into work requests, supported by visual aids like photos, supported faster decision-making and better prioritization of tasks, resulting in quicker repairs and improved fleet reliability.
Pro-Vac also optimized their inventory management by leveraging the parts tracking features from Fiix® CMMS so that critical components were always in stock and helping prevent unnecessary downtime. This streamlined approach not only saved time and resources, but also supported compliance efforts, making DOT audits much easier with centralized maintenance records. As Pro-Vac continues to expand, Fiix® CMMS has become an indispensable tool for maintaining operational excellence and supporting their growth strategy.
This case study is a replicated version, with the original available on the Fiix® website. To access the original version, please click here.
Published February 11, 2025