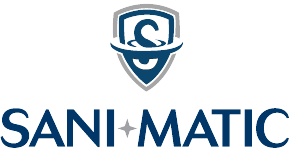
Sani-Matic, Inc. is a US-based manufacturer of automated cleaning technology, hygienic component solutions, services, and digital solutions for the food, beverage, personal care, and pharmaceutical industries.
- Regulatory demands
- Manual data collection
- Paper-based reporting
- Limited data access
- SaniTrend® Cloud Cleaning Reports
- Digital Process Recorder Powered by SaniTrend® Cloud
- ThingWorx IIoT Platform
- Expanded revenue generation opportunities
- Improved customer service
- Operational data insights
- Reduced cleaning times
- Reduced water usage
Peter Barrie is Product Management Director for Sani-Matic, which designs and manufactures automated cleaning solutions including Clean-in-Place (CIP) and Clean-Out-of-Place (COP) systems, equipment and components. A member of the Rockwell Automation PartnerNetwork™, Sani-Matic serves food and beverage, personal care, and nutraceutical and pharmaceutical companies.
Peter develops his hygienic design and process technical knowledge through participation in ASME Bioprocessing Equipment (BPE) Committees and 3-A Work Group Member Meetings. He is a Preventive Controls Qualified Individual (PCQI) and is Hazard Analysis and Critical Control Points (HAACP) certified.
Challenge
Regulatory demands and manual data collection and reporting
“These are regulated industries,” Barrie says. “Their process equipment must be clean, and they’re required to collect and report critical cleaning.”
Traditionally, many of Sani-Matic’s customers collected this data manually and generated paper-based reports with limited automation and data insight.
Solution
Cloud-based software solution
That’s why Sani-Matic developed its SaniTrend® Cloud Cleaning Reports® (CR) software product in 2020. Built on the ThingWorx IIoT Platform, SaniTrend is an automated, cloud-based solution that allows customers to securely collect, store and report data from any automated CIP or COP system.
“We initially developed it for our food and beverage audience, but have since launched additional versions,” Barrie explained. “We have some customers that just want the basic Cleaning Cycles report, but others are also interested in insights about things such as overall equipment effectiveness.”
Sani-Matic now offers three tiers of SaniTrend Cloud – Essentials, Insights and Insights+. The Essentials tier includes reporting of all critical cleaning data while the Insights and Insights+ versions offer additional features including OEE trends, event logs, and preventative maintenance. All of which increase visibility into systems and operator efficiency.
“We developed the Insights+ version especially for our pharmaceutical audience. With full traceability, if someone’s changed anything on the HMI it’s captured in an audit trail,” Barrie says. “We also have our Digital Process Recorder offering, which is unique in that it can go with one of our cleaning systems, but it can also be paired with other process equipment.”
Like the other versions of SaniTrend Cloud, the Digital Process Recorder replaces traditional data collection methods, including paper-based Chart Recorders.
“These are circular paper charts that collect things like temperature data or process data, and you take that paper, store it and comment on it,” Barrie explains. “But paper, as we know, is inefficient – it fades and gets damaged over time. The Digital Process Recorder is a direct replacement for that paper Chart Recorder and an easy starting point for customers who want to try out cloud-based technology but don’t know where to begin”.
Result
Operational insights lead to faster cleaning times and reduced water usage
Sani-Matic’s digital solutions have allowed the company not only to expand revenue generation streams beyond its systems and equipment business, but also leverage its expertise, improve customer service, and differentiate Sani-Matic from its competitors.
“With our wealth of knowledge and our ability to remotely access and review customer data, we’ve gathered valuable insights that have allowed us to provide recommendations on how customers can better use their systems, including how to clean faster,” Barrie says. “Because the customer wants to clean as fast as they can and get back to their production processes.”
Some Sani-Matic customers have reduced clean times by 20% and reduced water use by 50%.
“All because we have ‘virtual boots on the ground’ where we can see what’s going on with a customer’s system and make recommendations quickly,” Barrie says.
Published June 25, 2024