“This puts us firmly on the road to our 4,000-metric-ton per annum target, and discussions are already well underway with regards to usage of the recovered materials, as are the plans to expand the technology further.”
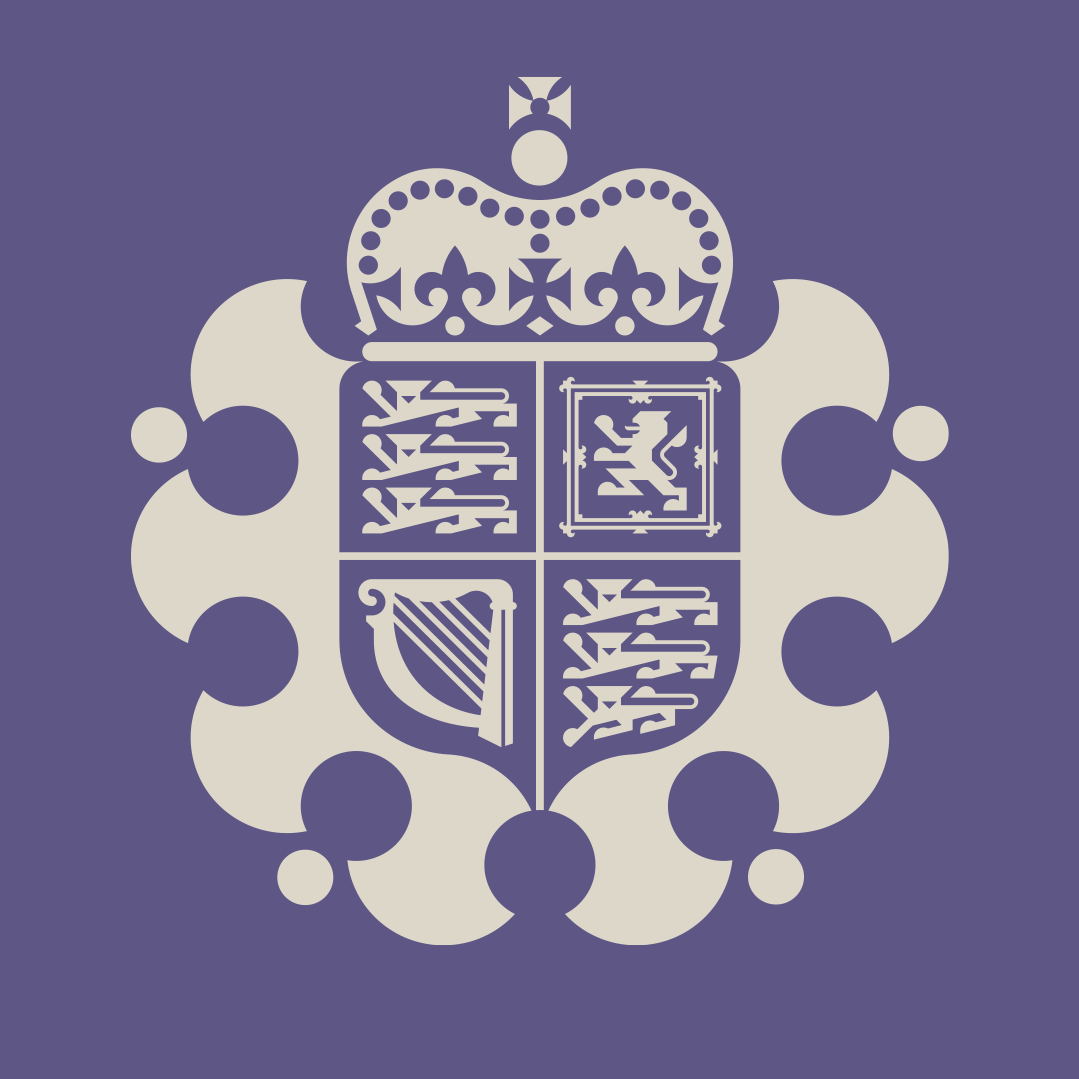
The Royal Mint is the UK’s oldest company. With a contemporary sustainability ethic at the heart of a long-term strategy, it has invested in, enhanced, and scaled a hugely promising technology used for the recovery of precious metals and other materials from e-waste.
Electronic waste is one of the world’s fastest-growing waste streams, according to Statista. With 62 million metric tons generated in 2022, the volume of discarded electronic material has nearly doubled since 2010. With e-waste generation forecast to exceed 80 million metric tons by 2030, improved recycling and recovery infrastructure is critical.
One company on a mission to help offset this is The Royal Mint, the UK’s oldest company. With a contemporary sustainability ethic at the heart of a long-term strategy, it has invested in, enhanced, and scaled a hugely promising technology used for the recovery of precious metals and other materials from e-waste.
A new precious metals recovery solution showed immense promise, but only if it could be developed, scaled and fine-tuned to hit commercial volumes
A Rockwell Automation solution was installed, which included:
- PlantPAx® Distributed Control System (DCS)
- Operator workstations (OWS), Engineer workstations (EWS)
- Broader infrastructure works
- Gold was extracted in the first run
- 500 metric tons of e-waste already processed, surpassing FY24/25 400-metric ton target
- The plant has proven its commercial potential and will now see wider deployment in other locations
Challenge
At the start of the project, the extraction technology, developed by Canadian company Excir, only existed in a prototype form, so required significant further development and scaling to hit The Royal Mint’s target of 4,000 metric tons per annum. These technological and processing hurdles were compounded by tightly controlled scheduling and investment.
“This was never going to be a straightforward project,” explains Rockwell Automation UK managing director Phil Hadfield. “We knew there were multiple challenges, some of which we could not influence, but we knew that our highly experienced process technical team and our family of tightly integrated technologies would bring the extraction process under tighter control, and once that was established further evolution and eventual scaling would be a little more straightforward.”
Solution
In The Royal Mint’s new Precious Metal Recovery facility, the circuit boards are fed via a conveyor system into a reactor and the resulting sludge then undergoes separation, sorting, and filtering using specialized chemical processes to extract molten gold and other precious metals from mixed materials, in a tightly controlled precipitation process.
The unique chemistry extracts 99% of the gold in e-waste and, importantly, this process takes place at room temperature, rather than high-temperature smelting.
And it is not just precious metals. Every part of a printed circuit board can be accounted for, even the fiberglass bi-product is “de-brominated” – where hazardous bromide is removed – as an integral part of the Mint’s circular economy and related net-zero plans.
Rockwell Automation’s Lifecycle Services team delivered a complete process control solution based on its PlantPAx® DCS system that allows integration from plant floor instrumentation up to boardroom with contextualized reporting providing insights to drive actions for optimizing production.
The PlantPAx DCS is used globally to help companies make better and faster process control decisions, helping them react more quickly, not just to local process variables, but also to changing specifications, often driven by customer demands.
PlantPAx proved ideal for this project due to its ability to scale in line with the growth and evolution of the process. It also connects disparate pieces of equipment in the complex plant and controls them in one place, using an interface familiar to the Mint’s engineers, who have worked with Rockwell Automation for more than 20 years.
“The system architecture enables different vendors to manufacture different parts of the plant and then easily plug it all together and give one, plant-wide infrastructure control when it's up and running,” Hadfield said. “That eliminates disparate control systems that you often have in projects like this and provides optimization improvements, such as common log-ons, change management, alarm management, data logging and more, visible across the entire plant, and this helps reduce the total cost of ownership.”
Result
Even with all the initial uncertainty and multiple process variables, engineers from all parties were delighted when the system delivered gold on the first run, at scale, and without any insights from an intermediate pilot stage.
According to Tony Baker, Director of Manufacturing Innovation at The Royal Mint: “After so many early challenges, we are pleased that it is all going to plan. In fact, we have already surpassed our 2024/25 target of 400 metric tons, when we hit 500 metric tons earlier this year.
“We’re still fine tuning the processes and optimizing the parameters, but we are getting really good material separation alongside more efficient pre, parallel, and post processes. The project’s success has been down to a combination of several factors, helped by the way everyone worked together to address the challenges.
Published November 27, 2024
You may also be interested in