Recomendado para usted
En la opinión del OEM de empaquetado Harpak-ULMA, la transformación digital supone la expansión de lo que es posible no solo en sus propias operaciones, sino también en las de sus clientes.
El fabricante de máquinas de empaquetado y soluciones de automatización de línea de empaquetado de extremo a extremo inició su trayecto hacia la transformación digital en 2018. La iniciativa de múltiples fases y de muchos años tiene como propósito impulsar el crecimiento de ingresos y crear nuevas líneas de negocio para Harpak-ULMA. También aspira a transformar lo que es posible para los clientes en los mercados de alimentos, productos médicos e industriales empoderándolos con máquinas de empaquetado conectadas inteligentes.
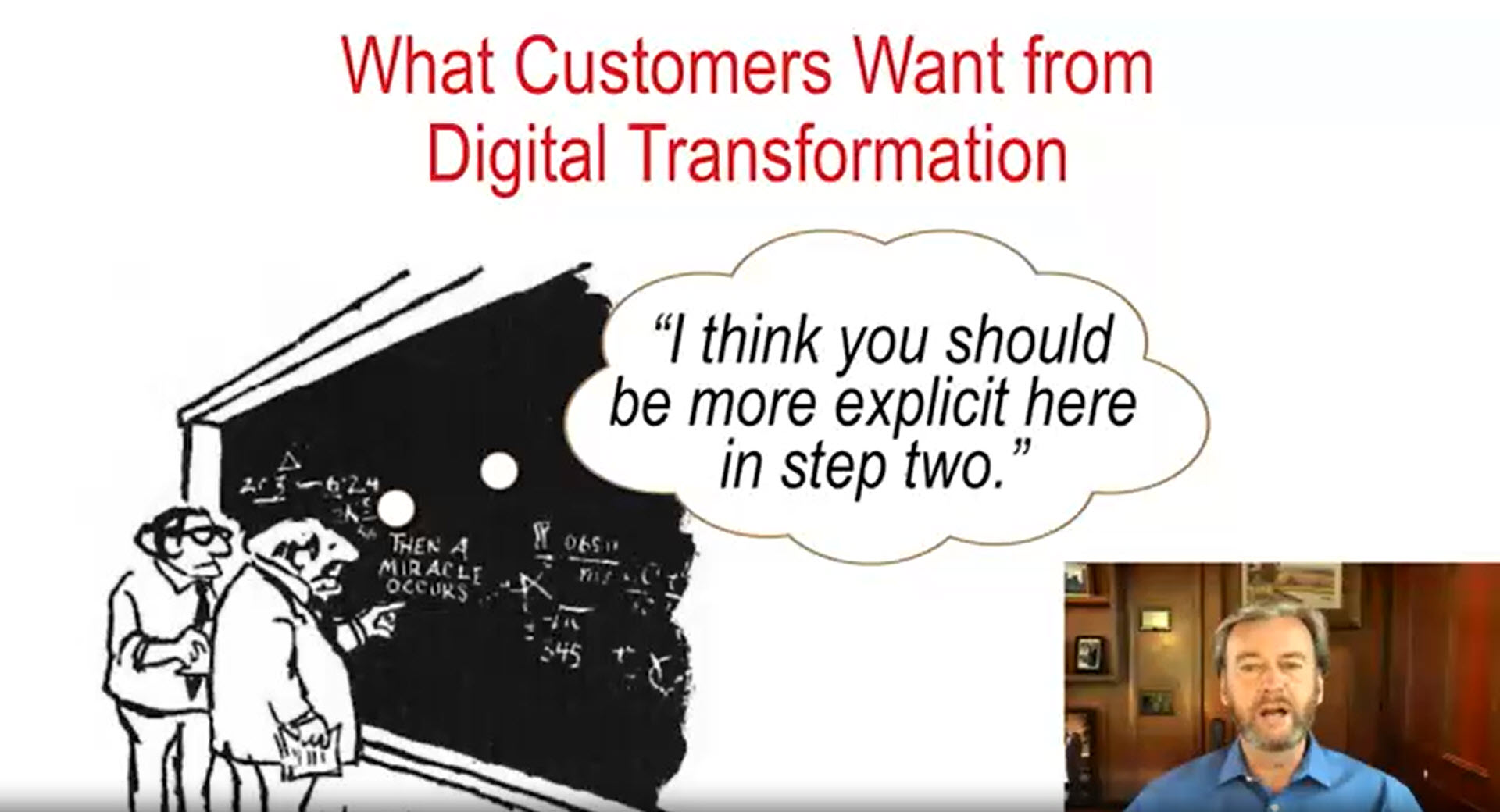
Mejorar la agilidad
Para Harpak-ULMA, el valor de la transformación digital radica en la capacidad de ayudar a los clientes a adaptarse mejor a los cambios del mercado.
“Existe una razón por la que la transformación digital es un éxito”, dice Kevin Roach, presidente, Harpak-ULMA. “Nos ayuda a hacer más con mayor rapidez aprovechando datos a fin de manipular mejor las barreras tradicionales al cambio, es decir, tiempo, costo y riesgo”.
La compañía lanzó su transformación digital en octubre de 2018 en función de una hoja de ruta de tecnología que incluyó cuatro fases.
La primera fase constó de establecer un fundamento conectado inteligente para los clientes migrándose a una única plataforma de control estandarizada. Harpak-ULMA decidió estandarizarse en los controles y componentes de Rockwell Automation. Esto le brindó a la compañía un fundamento de arquitectura abierta para máquinas conectadas inteligentes. Las soluciones de control de Rockwell Automation ofrecieron además la compatibilidad preintegrada con las aplicaciones de software de IoT innovadoras de PTC, tales como Vuforia y ThingWorx, que ayudan a reinventar la manera en la que se operan y mantienen los activos de producción.
La segunda fase incluyó la implementación de flujos de trabajo de realidad aumentada (AR) para contribuir a impulsar la productividad.
Con conocimientos profundos a demanda y orientación visual proporcionados por tecnología de AR, Harpak-ULMA puede brindar asistencia técnica a sus clientes desde cualquier lugar e introducir nuevas capacidades tales como pruebas de aceptación de fábrica virtuales. Asimismo los clientes pueden aprovechar la tecnología para reducir las curvas de aprendizaje de los operadores y el tiempo dedicado a la incorporación del personal nuevo.
Crear nueva información útil
Harpak-ULMA ha hecho buenos progresos en la fase dos y ahora está trabajando en la fase tres, la cual involucra la incorporación de más puntos de contacto con IoT. En efecto, esto combina las máquinas de empaquetado con sus gemelos digitales para ofrecer experiencias de operación e integración de información mejoradas.
“Ampliar la envergadura de IoT incorporado nos permite la integración con aplicaciones de IoT avanzadas que exponen las operaciones de máquina detalladas en tiempo real al personal de producción”, comenta Roach.
Para los clientes, más datos significan más información de producción contextualizada en tiempo real disponible tanto al personal como al diagnóstico incorporado.
“En esta fase estamos ampliando nuestras capacidades de AR para crear un más amplio conjunto de capacidades en tiempo real que le brindará al personal lo que denominamos la visión de rayos X”, añade Roach. “La exposición del gemelo digital de una máquina constituye una manera interactiva de aprender más y diagnosticar mejor”.
Por ejemplo, si un técnico recibe una alerta sobre un problema de máquina, no le es necesario desactivar la máquina, realizar los procedimientos de bloqueo-etiquetado y abrir el gabinete de control para investigar el problema. En lugar de ello, el técnico puede usar un aparato de AR, un teléfono inteligente o una tableta para ver un gemelo digital de la máquina e identificar el fallo.
Predicciones futuras
En la cuarta fase de la transformación digital de Harpak-ULMA, la compañía aplicará el aprendizaje automático y la inteligencia artificial a la gran cantidad de datos recolectados durante la producción. Esta tarea en la fase de planificación permitirá que la compañía cree nuevos modelos de negocio al introducir servicios de mantenimiento predictivo y de referencias basados en la nube.
“Esta fase final representa un paso evolucionario para los clientes en cuanto a su relación con el OEM”, añade Roach. “Las soluciones de macrodatos que aprovechan el aprendizaje automático y la inteligencia artificial facilitarán la obtención del santo grial de la analítica de mantenimiento en nuestros mercados”.
El mantenimiento predictivo puede ayudar a los clientes a reducir el tiempo improductivo no programado y a reestructurar los modelos anticuados de mantenimiento y costos. Es más, la obtención de referencias en toda la industria les ofrece a los clientes una oportunidad de entender de otra manera la eficacia de sus procesos de producción.
Por supuesto, hacer estos conceptos realidad en los entornos de producción de los clientes acarreará desafíos.
“Necesitaremos resolver los problemas relativos a la propiedad de los datos y abordar los temas relacionados con el monitoreo del mantenimiento predictivo”, dice Roach. “Pero sí ya existen precedentes. Si es posible implementar el concepto para motores de avión, es posible también implementarlo en un entorno de producción de empaquetado.
Publicado 1 de diciembre de 2020