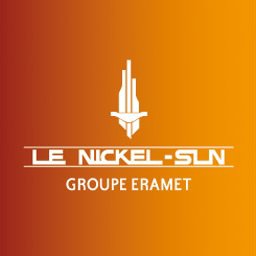
Société Le Nickel (SLN), parte de Eramet Group, el mayor productor de ferroníquel del mundo.
- El sistema obsoleto era demasiado lento y causaba desconexiones eléctricas debido a una temperatura elevada de los productos, lo que perjudicaba la calidad de estos.
- El sistema obsoleto no era fácil de operar ni mantener, lo que causaba problemas de tiempo productivo.
- La plataforma FactoryTalk Analytics Pavilion8® de Rockwell Automation, una solución de control predictivo basado en modelo que controla la planta en tiempo real. La plataforma ofrece una capa de inteligencia que se coloca sobre los sistemas de automatización y evalúa continuamente los datos operacionales actuales y pronosticados.
- Rendimiento mejorado que utiliza datos autónomos y en tiempo real, y compara esto con los resultados deseados. El control predictivo basado en modelo establece nuevos objetivos de control dentro del sistema de control a fin de reducir la variabilidad de los procesos, mejorar el rendimiento y optimizar la eficiencia.
- Reducción de los errores, incluida una reducción del 6 % en la temperatura de los productos y una reducción del 16,1 % en la variabilidad del perfil de temperatura.
- Mejora del tiempo productivo, que aumentó del 70 % al 83 % con el nuevo software Rockwell.
El níquel, caracterizado por la capacidad de resistir la corrosión a altas temperaturas y su utilidad como elemento de aleación, tiene un rol fundamental en una gran cantidad de sectores industriales, desde el área aeroespacial y química hasta eléctrica y automotriz.
Société Le Nickel (SLN), parte de Eramet Group, el mayor productor de ferroníquel del mundo. La compañía de 140 años también produce manganeso, litio y titanio, que son fundamentales para la fabricación de baterías, pigmentos para pinturas y turbinas eólicas, entre otros productos.
El procesamiento de minerales es una actividad compleja que exige el control estable del perfil de temperatura de los hornos giratorios y la automatización de operaciones en distintos rangos operativos. Los minerales de alimentación introducidos al horno de calcinación giratorio se someten a calcinación al recorrer la longitud del horno. Si el producto calcinado no alcanza la temperatura suficiente, la calidad del producto se ve perjudicada.
El calor se distribuye de manera uniforme por el horno y se suministra aire para que se produzca la combustión. Si se suministra demasiado aire, es necesario quemar más combustible a fin de mantener la misma temperatura del producto, lo que disminuye la eficiencia energética. Debe minimizarse el exceso de oxígeno a un nivel seguro a fin de reducir los costos operativos y los gases de efecto invernadero.
Desfases en el sistema obsoleto
SLN estaba utilizando un sistema experto, un controlador de lógica de aproximación, diseñado para automatizar la operación del horno. No obstante, la compañía enfrentaba varios desafíos con el sistema obsoleto, especialmente con el contenido variable de minerales y los valores variables de calentamiento, lo que ocasionaba picos de temperatura y desconexiones eléctricas frecuentes. La temperatura elevada del producto causaba desconexiones, lo que perjudicaba tanto la calidad del producto como la integridad de los equipos.
“La lógica de aproximación no lograba reducir el combustible a una velocidad suficiente para prevenir las desconexiones y, durante la operación manual, los operadores no lograban reaccionar con la rapidez suficiente”, explicó Leslie Hii, una de los ingenieros de control de procesos avanzados de Rockwell Automation responsable de entregar el proyecto de SLN.
“Mantener la temperatura requerida en el horno puede ser complejo y desafiante dada la cantidad de variables que deben gestionarse. El tipo de combustible puede ser petróleo, carbón o una mezcla de los dos, cada uno con sus características térmicas únicas. Asimismo, la tasa de alimentación de material afecta la temperatura del horno y se debe administrar con cuidado”, explicó Hii.
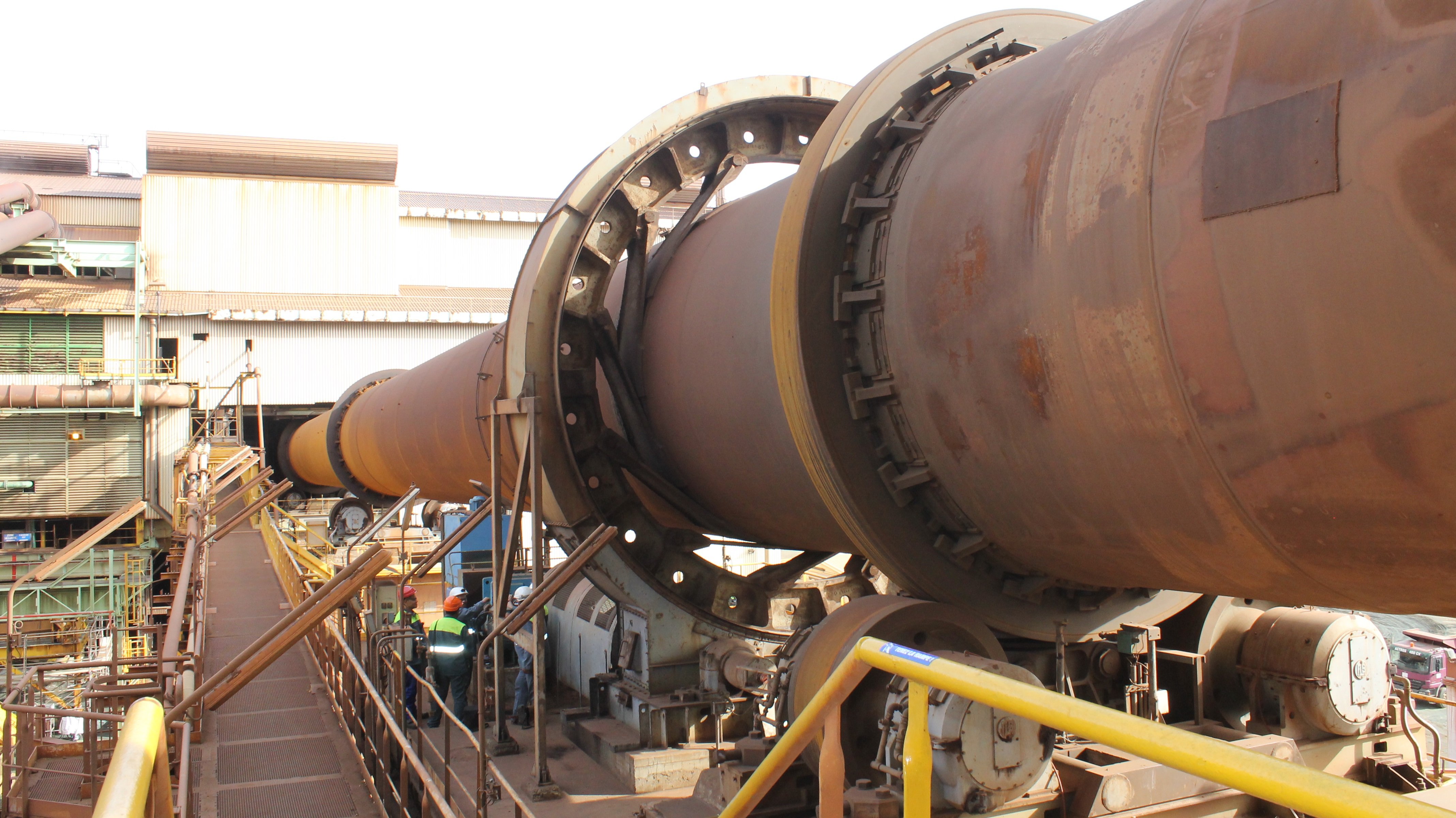
Société Le Nickel (SLN), part of the Eramet Group, is the world’s largest producer of ferronickel. Pictured is one of the five furnaces managed by Rockwell Automation’s FactoryTalk® Analytics™ Pavilion8® software. Image copyright: Société Le Nickel (SLN), part of the Eramet Group.
Adición de una capa de inteligencia
El sistema experto solo puede encenderse cuando el horno está operando normalmente y, en caso de cualquier inestabilidad, los operadores lo desactivan y toman el control. El sistema experto también tenía malos resultados en términos de facilidad de uso y mantenimiento, y ambos factores contribuían a un bajo tiempo productivo del sistema.
A fin de rectificar la situación, SLN actualizó al sistema FactoryTalk® Analytics™ Pavilion8® de Rockwell Automation. Esta solución de control predictivo basado en modelo (MPC) ofrece una capa de inteligencia que se coloca sobre los sistemas de automatización y evalúa continuamente los datos operacionales actuales y pronosticados. Seguidamente compara estos datos con los resultados deseados y promueve nuevos objetivos de control para reducir la variabilidad de los procesos, mejorar el rendimiento y aumentar la eficiencia, todo de manera autónoma y en tiempo real.
“El uso de una solución de control predictivo basado en modelo es un ejemplo ideal de cómo Rockwell Automation está utilizando inteligencia artificial a fin de lograr mejores resultados operativos mediante el uso de datos disponibles. En este proyecto, también usamos aprendizaje automático, conocimiento de procesos y datos a fin de desarrollar modelos de hornos de calcinación adaptados a las operaciones de SLN”, comentó Hii.
La fase inicial de la solución mejorada se llevó a cabo correctamente en solo 13 meses, a diferencia de los años que se demoró en implementar el sistema experto. Ya se ha implementado en cinco hornos giratorios en la instalación de SLN. Los operadores ahora tienen la opción de minimizar el uso de fuel oil de alto valor a la vez que maximizan el carbón pulverizado de menor valor durante la operación en modo mixto.
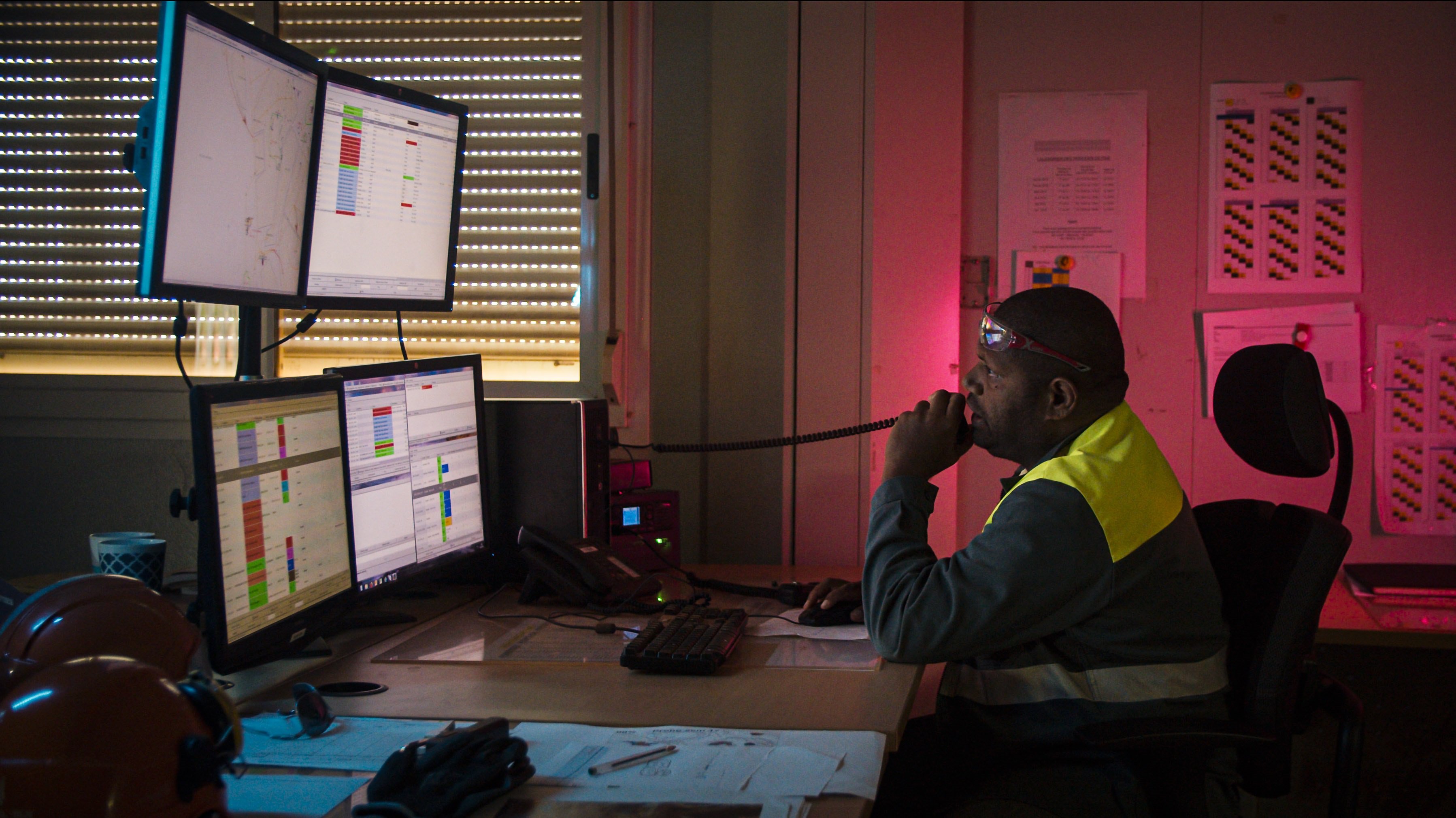
SLN upgraded to Rockwell Automation’s FactoryTalk® Analytics™ Pavilion8® to boost efficiency and performance. Image copyright: Société Le Nickel (SLN), part of the Eramet Group.
La inversión da sus frutos
“La aplicación de MPC puede manejar una variabilidad significativa en la alimentación de minerales y los valores de calentamiento, y previene las desconexiones, lo que permite que el horno mantenga la operación a una tasa más alta”, explicó Mickael Montarello, gerente de control de procesos, SLN. “Se redujeron los errores en la temperatura del producto calcinado en un 6 % y la variabilidad del perfil de temperatura del horno en un 16,1 %”.
SLN está disfrutando de los beneficios de esta inversión. “El tiempo productivo promedio del MPC de Rockwell Automation es del 83 %, en comparación con el 70 % con el sistema experto anterior”, afirmó Montarello. “La nueva solución permite que el horno mantenga la operación durante más tiempo.
“Los usuarios aprecian la facilidad de uso y la flexibilidad de la herramienta. En caso de un problema con un elemento del proceso, los operadores pueden intervenir fácilmente en el elemento en cuestión, lo que permite que el MPC continúe controlando las demás variables manipuladas.
“Gracias a esta nueva herramienta, surgen nuevas oportunidades de optimizar el control y la gerencia, que no eran posible con el controlador de lógica de aproximación anterior. Nuestro objetivo para 2024 es lograr una tasa de utilización del 90 %”, concluyó Montarello.
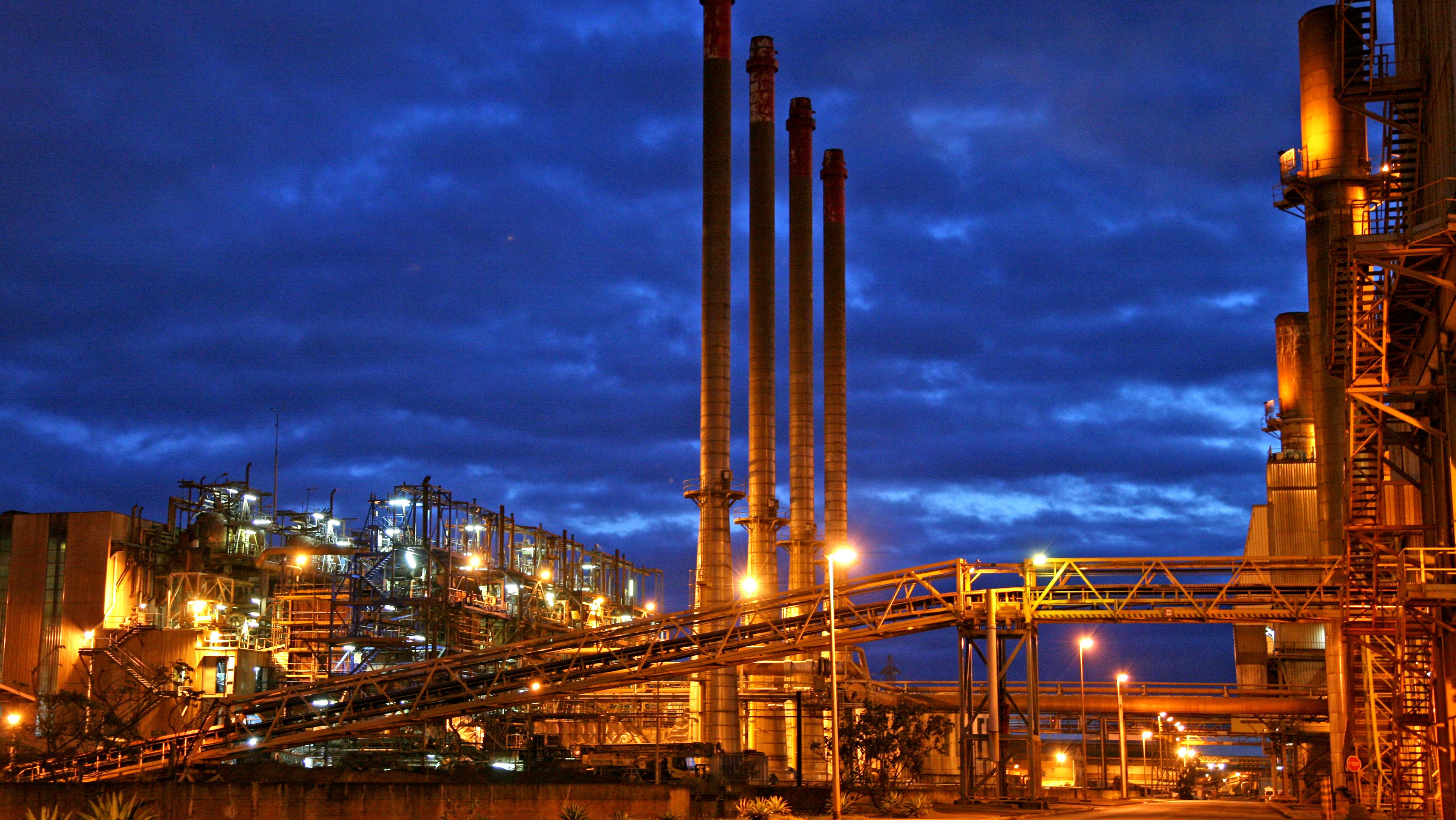
The average uptime of Rockwell’s MPC is 83% compared with 70% with the earlier expert system. Image copyright: Société Le Nickel (SLN), part of the Eramet Group.
Publicado 5 de enero de 2024