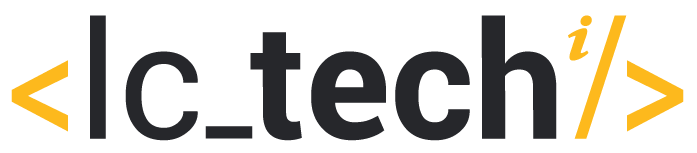
LC Tech Group es una empresa argentina dedicada a la gestión de soluciones tecnológicas y aplicaciones informáticas de procesos industriales. A través de soluciones y aplicaciones la compañía se posiciona como referente tecnológico de sus clientes, con el objetivo de obtener resultados que contribuyan a la generación de valor.
- Proyecto de automatización en la mayor planta termoeléctrica de Argentina.
- Reemplazo del sistema de control de tres compresores obsoletos tecnológicamente que alimentan las turbinas de un ciclo combinado.
- Ejecución de las obras en plazos acotados establecidos por el cliente final.
- Llevar a cabo un sistema de control sin modificar la estructura de la caseta donde estaban alojados los PLC anteriores.
- Plataforma ControlLogix® de Rockwell Automation, con periferia POINT I/O™
- PLC GuardLogix® con certificación Safety y arquitectura EthernetIP en anillo
- Plataforma FactoryTalk® View Site Edition
- Estación gráfica PanelView™ de 15’’
- Redes Ethernet/IP
- Servicio de asistencia técnica TechConnect
- Optimización de la inversión.
- Se mejoró la capacidad de diagnóstico.
- Se jerarquizó la documentación de planta.
- Reducción del stock de repuestos requeridos.
- Trabajo colaborativo con uno de nuestros socios tecnológicos.
- Migración de la plataforma a tecnología de última generación.
LC Tech Group llevó a cabo un proyecto de automatización en una central térmica situada en la zona sur del área portuaria de Buenos Aires, que utiliza como combustible diésel, gas natural y gasóleo, y que constituye hoy la mayor planta termoeléctrica de Argentina con 2305 MW de potencia instalada.
Cumplimiento de tiempos de entrega exigidos por el cliente
El proyecto realizado involucra una turbina a gas y otra a vapor en ciclo combinado, para lo cual posee una estación operativa con tres compresores que alimentan a dichas turbinas. La tecnología que manejaba dicha estación estaba bastante obsoleta, ya que los PLC’s que controlaban los compresores eran de la década de los ochenta. El sistema era difícil de manejar, era muy susceptible al ruido eléctrico, interferencia electromagnética y radial (con la consiguiente detención de todo el proceso), y la visualización funcionaba básicamente en dos.
Lo más complejo del proyecto fue realizar un sistema de control sin modificar la estructura de la caseta donde estaban alojados los PLC anteriores. “Las dos placas de montaje que confeccionamos debían corresponderse con el cableado de campo existente, que estaba acotado y no podía ser modificado”.
Cabe mencionar que el proyecto, prácticamente se llevó a cabo en un período de tan solo tres meses.
Desarrollo de un sistema de control basado en la plataforma ControlLogix®, con periferia POINT I/O™.
Concretamente, la propuesta de LC Tech Group no solo cumplía con los tiempos y la logística exigidos por el cliente, sino que además le entregó la plena confianza, ya que hubo un análisis técnico y minucioso. “Además, el pliego exigía que esta fuese una solución certificada, para lo cual utilizamos para cada compresor un controlador de seguridad GuardLogix® y para lo que fue el control de servicios auxiliares de los tres compresores, empleamos un sistema de alta disponibilidad con ControlLogix® redundante”.
ControlLogix® reúne los beneficios de la plataforma Logix (entorno de programación común, redes comunes, motor de control común) para brindar el rendimiento que la aplicación requiere en un entorno fácil de usar. Además, recibe una estrecha integración entre el software de programación, el controlador y las E/S para reducir el tiempo y el costo de desarrollo en la puesta en servicio y durante el funcionamiento normal. Dadas las características solicitadas para la seguridad del equipo, se utilizaron procesadores GuardLogix® con certificación Safety y arquitecturas Ethernet/IP.
en anillo que incrementaron la confiabilidad de las comunicaciones.
A su vez, se migró el servicio existente de HMI basado en Wonderware por un nuevo sistema integrado de software de operaciones de fábrica de Rockwell Automation.
La visualización se desarrolló en la plataforma FactoryTalk® View Site Edition, la cual permite monitorear y controlar la planta, desde una única estación de operador hasta cliente/servidor distribuido, aplicaciones multiusuario. La plataforma proporciona una vista precisa en tiempo real de las operaciones, al tiempo que satisface las demandas de múltiples partes interesadas, incluidas las tecnologías de la información de ingeniería, mantenimiento y operaciones. De forma local, el nuevo sistema es operado mediante una terminal gráfica PanelView™.
Además, se implementaron redes EthernetIP que comunican cada controlador con su periferia y a todos los controladores de planta entre sí con topología Anillo DLR (Device Level Ring) que posee capacidad de autocierre en caso de una falla en algún punto del tendido.
LC Tech Group fue capaz de unificar la plataforma de repuestos junto a otros sistemas de la planta, optimizando la inversión y reduciendo el stock de repuestos requeridos.
Hoy, la planta dispone de un sistema con un mayor nivel de seguridad y con una mejora en la disponibilidad, lo que impacta positivamente en la performance del Ciclo Combinado. “Posee una seguridad superior en materia de protocolo SIL 2, lo cual permitió cumplir con las especificaciones del cliente en esta materia”.
La capacidad de diagnóstico mejoró drásticamente utilizando herramientas modernas disponibles en las estaciones de ingeniería como es el caso del software HMI FactoryTalk® View, que incluye, entre otras cosas, alarmas y tendencias con un amplio rango de información que, además, está mucho mejor procesada.
“El servicio de asistencia técnica TechConnect que ofrece Rockwell Automation es muy bueno; a través de la vía telefónica, la compañía es capaz de dar solución a prácticamente todos los problemas que no podemos resolver como integrador; incluso, si es necesario llegar a una segunda instancia de soporte, el cliente puede conectarse directamente con un ingeniero en Estados Unidos quien es capaz de tomar el control de manera remota de las operaciones y a la larga termina resolviendo los problemas”.
Publicado 11 de septiembre de 2024