Recommandé pour vous
Pour l’équipementier de chaînes d’emballage Harpak-ULMA, la transformation numérique consiste à étendre le champ des possibles non seulement au sein de ses propres exploitations, mais aussi dans celles de ses clients.
Le constructeur de machines d’emballage et de solutions d’automatisation de bout en bout pour ligne de conditionnement a entamé sa transformation numérique en 2018. Cette initiative multi-phases de plusieurs années vise à stimuler la croissance des revenus et à créer de nouvelles opportunités commerciales pour Harpak-ULMA. Mais elle entend également transformer ce qui est possible pour les clients dans les secteurs de l’agroalimentaire, du médical et des marchés industriels en les équipant de machines d’emballage intelligentes connectées.
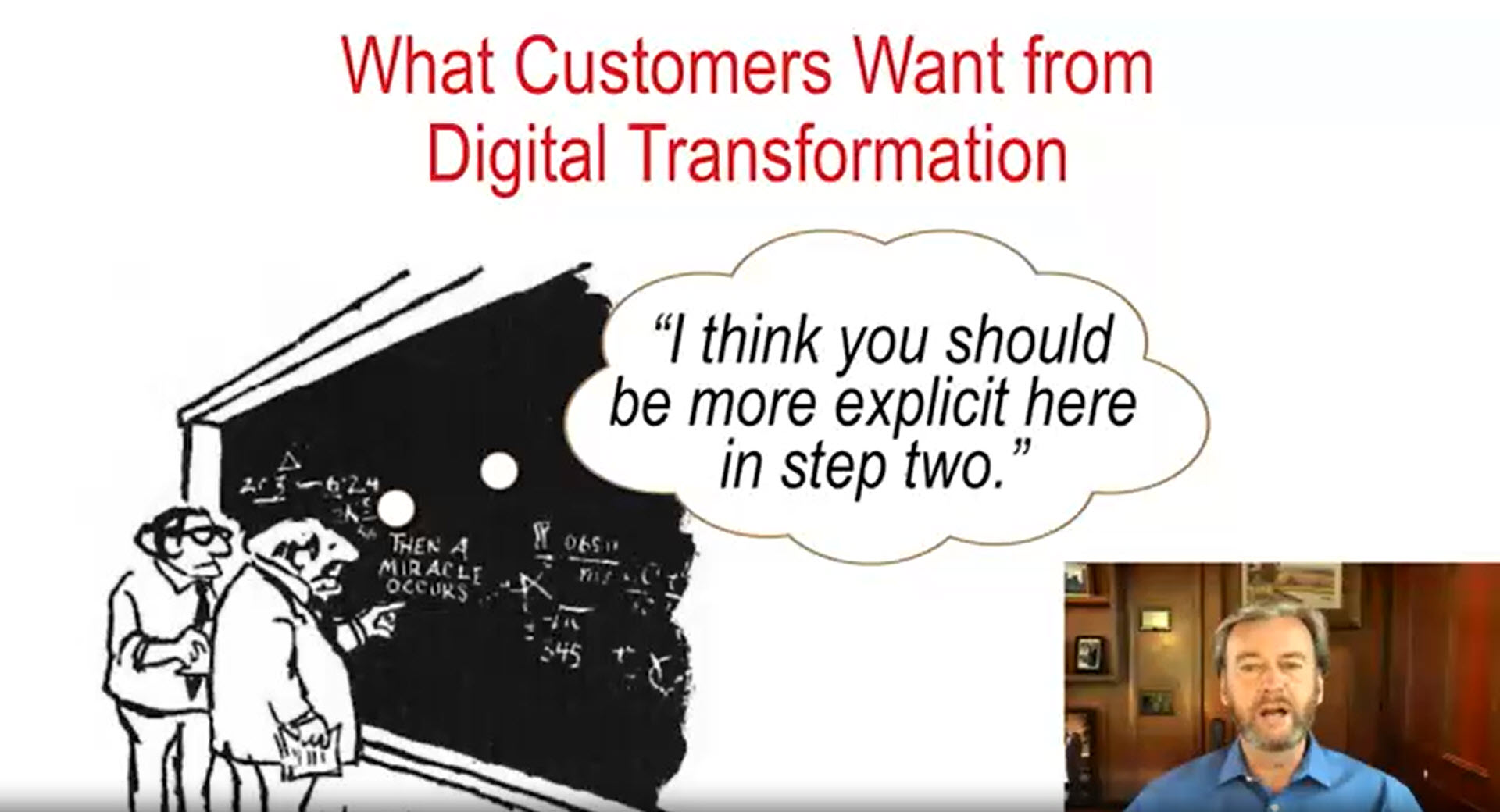
Agilité optimisée
Pour Harpak-ULMA, la valeur de la transformation numérique réside dans sa faculté à aider ses clients à mieux s’adapter aux évolutions du marché.
« La transformation numérique est pleinement justifiée », selon Kevin Roach, Président d’Harpak-ULMA. « Elle nous aide a gagner en productivité et en rapidité en s’appuyant sur des données pour pouvoir surmonter plus facilement les habituels obstacles aux changements – à savoir les délais, les coûts et les risques. »
L’entreprise a lancé son initiative de transformation numérique en octobre 2018 suivant une feuille de route en quatre étapes.
La première phase consistait à jeter les bases intelligentes et connectées pour permettre aux clients de migrer vers une plate-forme de commande unique standardisée. Pour mener à bien cette standardisation, Harpak-ULMA a opté pour les systèmes de commande et composants de Rockwell Automation. Cette solution a conféré à l’entreprise le fondement d’une architecture ouverte en vue de machines intelligentes connectées. Les solutions de commande de Rockwell Automation proposent également la compatibilité pré-intégrée avec des applications loigicielles IoT innovantes de PTC, telles que Vuforia et ThingWorx, qui aident à reconcevoir comment les gens font fonctionner et entretiennent les actifs de production.
La seconde phase consistait à mettre en place des organisations de travail en réalité augmentée (AR) pour stimuler la productivité.
Grâce à l’expertise sur demande et aux aides visuelles fournies par la technologie de réalité augmentée, Harpak-ULMA peut apporter aux clients toute l’assistance nécessaire en n’importe quel lieu et introduire des nouveautés, telles que des tests de réception d’usine virtuels. Entre temps, les clients peuvent utiliser la technologie pour réduire les délais d’intégration et d’apprentissage des opérateurs.
Acquisition de nouvelles connaissances
Harpak-ULMA a fait des progrès significatifs lors de la deuxième phase, et évolue maintenant vers la phase trois qui implique l’incorporation d’un plus grand nombre de points d’interaction IoT. Il s’agit essentiellement de combiner les machines d’emballage avec leurs jumeaux numériques pour offrir des expériences de fonctionnement améliorées et une meilleure intégration des informations.
« L’extension de l'étendue et de l’ampleur des systèmes IoT embarqués nous permet d’intégrer des applications IoT avancées qui exposent en détail et en temps réel le fonctionnement des machines au personnel de production » relate Roach.
Pour les clients, plus de données signifie qu’un plus grand nombre d’informations contextualisées sur la production est mis en temps réel à la disposition du personnel tout comme des systèmes de diagnostic embarqués.
« À ce stade, nous développons nos capacités de réalité augmentée (AR) en vue de fournir un ensemble plus exhaustif de capacités en temps réel afin que le personnel puisse disposer de ce que nous appelons une vision radioscopique. » dit encore Roach. « Présenter le jumeau numérique d’une machine est un moyen interactif d’apprendre davantage et d’établir de meilleurs diagnostics. »
Ainsi, si un technicien reçoit par exemple une alerte signalant un problème sur une machine, il n’est pas nécessaire d’arrêter la machine, de déclencher des procédures de verrouillage/signalisation ni d’ouvrir l’armoire de commande pour chercher l’origine du problème. Car il suffit d’un casque de réalité augmentée, d’un smartphone ou d’une tablette pour pouvoir examiner le jumeau numérique de la machine et identifier le défaut.
Prédictions futures
La quatrième phase de la transformation numérique d’Harpak-ULMA consiste à appliquer l’apprentissage et l’intelligence artificielle au vaste volume de données collectées lors de la production. Cet effort, encore au stade de la planification, permettra à l’entreprise de créer de nouveaux modèles de gestion opérationnelle en introduisant la maintenance prédictive basée sur le cloud et les services d'analyse comparative.
« Cette étape finale représente une évolution pour les clients quant à leurs relations avec les fournisseurs OEM » atteste Roach. « Les solutions Big data qui mettent en œuvre l’apprentissage machine et l’intelligence artificielle permettront réellement d’atteindre l’objectif visé en termes d’analyses de maintenance prédictive dans notre activité. »
Pour les clients, la maintenance prédictive peut leur permettre de réduire les temps d'arrêt imprévus, de même que restructurer les modèles de maintenance et de coûts établis. De plus, une analyse comparative à l'échelle de l'industrie leur offre l’opportunité de mieux connaître l’efficacité de leurs processus de production.
Relever ces défis permettra évidemment de concrétiser ces concepts dans les environnements de production du client.
« Nous devrons encore résoudre les questions de propriété des données et remédier aux problèmes de connectivité qui se posent avec la surveillance de la maintenance prédictive » ajoute Roach. « Or ce n’est pas comme s’il n’y avait pas de précédent. Si cela a pu être fait pour des moteurs d’avion, c’est aussi transposable aux environnements de production d’emballage.
Publié 1 décembre 2020