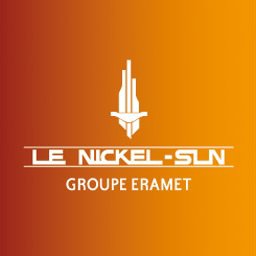
Société Le Nickel (SLN), qui fait partie du groupe Eramet, est le premier producteur mondial de ferronickel.
- Le système existant était trop lent et provoquait de fréquentes pannes électriques dues à une température trop élevée des produits, ce qui compromettait leur qualité.
- Le système existant n'était pas intuitif. De plus, il était difficile à entretenir, ce qui entraînait des problèmes de durée de fonctionnement.
- La plate-forme FactoryTalk Analytics Pavilion8® de Rockwell Automation, une solution de commande prédictive du modèle qui contrôle l'usine en temps réel. Cette plate-forme dispose d'une couche analytique au-dessus des systèmes d'automatisation qui vise à évaluer en continu les données opérationnelles actuelles et prévisibles.
- Performances améliorées grâce à l'utilisation de données en temps réel et autonomes, qui sont comparées aux résultats souhaités. La commande prédictive du modèle fixe de nouveaux objectifs de contrôle dans le système de commande afin de réduire la variabilité du procédé, d'améliorer les performances et de stimuler l'efficacité.
- Réduction des erreurs, y compris une réduction de 6 % des erreurs liées à la température du produit et une réduction de 16,1 % de la variabilité du profil de température.
- Amélioration de la durée de fonctionnement, qui est passé de 70 % à 83 % grâce au nouveau logiciel de Rockwell.
Caractérisé par sa capacité de résistance à la corrosion à haute température et son utilité en tant qu'élément d'alliage, le nickel joue un rôle essentiel dans un grand nombre de secteurs industriels allant de l'aérospatiale à la chimie, en passant par l'électricité et l'automobile.
Société Le Nickel (SLN), qui fait partie du groupe Eramet, est le premier producteur mondial de ferronickel. Cette entreprise vieille de 140 ans produit également du manganèse, du lithium et du titane, qui sont essentiels à la fabrication de batteries, de pigments de peinture et d'éoliennes, entre autres produits.
Le traitement des minerais est une activité complexe qui nécessite une régulation stable du profil de température des chaudières rotatives et l'automatisation des opérations dans différentes plages de fonctionnement. Le minerai introduit dans le four rotatif subit une calcination au fur et à mesure qu'il traverse la chaudière. Si le produit calciné n'est pas à une température suffisamment élevée, sa qualité sera compromise.
La chaleur est répartie à travers la chaudière et de l'air y est introduit pour que la combustion se produise. Si l'apport en air est trop important, il faut brûler plus de combustible pour maintenir la même température du produit, ce qui réduit l'efficacité énergétique. L'excès d'oxygène doit être réduit à un niveau adéquat pour diminuer les coûts d'exploitation et les gaz à effet de serre.
Lacunes du système existant
SLN utilisait un système expert, à savoir un automate à logique floue conçu pour automatiser le fonctionnement de la chaudière. Cependant, l'entreprise a été confrontée à plusieurs difficultés avec le système existant, notamment en raison de la variation de la teneur en minerai et des valeurs de chauffage variables, ce qui a entraîné des pics de température et de fréquents déclenchement du disjoncteur. Les déclenchements étaient dus à la température élevée du produit, qui compromettait à la fois la qualité du produit et l'intégrité de l'équipement.
« La logique floue n'était pas en mesure de réduire le carburant assez rapidement pour empêcher les déclenchements et, en mode manuel, les opérateurs ne pouvaient pas réagir assez vite », explique Leslie Hii, automaticienne en charge des procédés de pointe chez Rockwell Automation, et responsable de l'exécution du projet SLN.
« La régulation de la température requise dans la chaudière peut s'avérer complexe et difficile compte tenu du nombre de variables à gérer. Le combustible peut être du fioul, du charbon ou un mélange des deux, chacun ayant ses propres caractéristiques thermiques. En outre, la vitesse d'alimentation en matériau a une incidence sur la température de la chaudière et doit être régulée avec soin », a déclaré M. Hii.
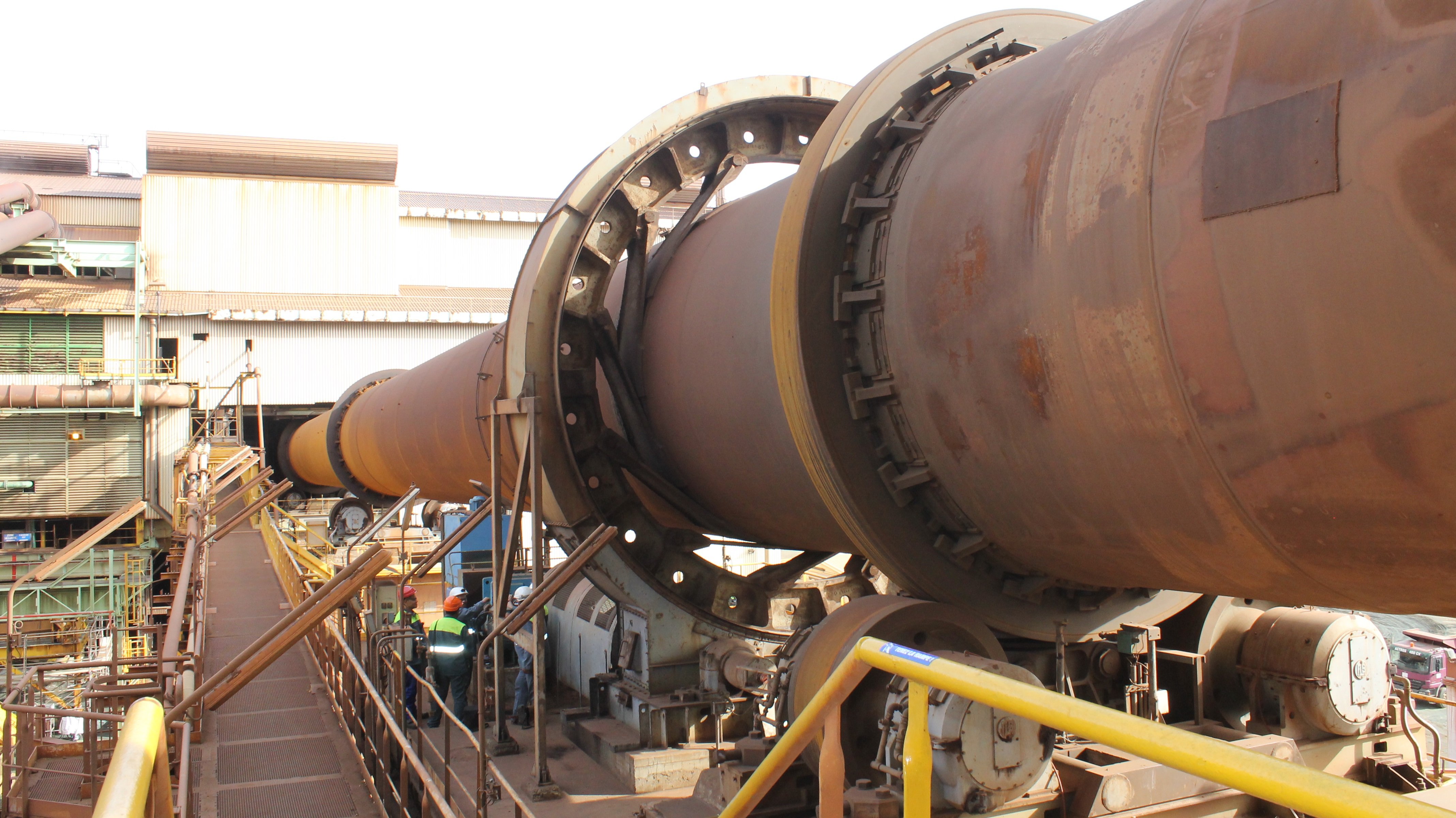
Société Le Nickel (SLN), part of the Eramet Group, is the world’s largest producer of ferronickel. Pictured is one of the five furnaces managed by Rockwell Automation’s FactoryTalk® Analytics™ Pavilion8® software. Image copyright: Société Le Nickel (SLN), part of the Eramet Group.
Ajouter une couche analytique
Le système expert ne peut être activé que lorsque la chaudière fonctionne normalement et, en cas d'instabilité, les opérateurs l'éteignent et prennent le contrôle. Le système expert a également été mal noté en termes d’intuitivité et de facilité de maintenance, deux facteurs qui contribuent au faible taux de durée de fonctionnement du système.
Pour remédier à cette situation, la SLN a procédé à une mise à niveau en adoptant la solution FactoryTalk® Analytics™ Pavilion8® de Rockwell Automation. Cette solution de commande prédictive du modèle (MPC) offre une couche analytique qui se superpose aux systèmes d'automatisation et évalue en permanence les données opérationnelles actuelles et prévisionnelles. Elle compare ensuite ces données aux résultats souhaités et définit de nouveaux objectifs de contrôle, afin de réduire la variabilité du procédé, d'améliorer les performances et d'accroître l'efficacité, le tout de manière autonome et en temps réel.
« L'utilisation d'une solution de commande prédictive du modèle est un exemple parfait de la façon dont Rockwell Automation utilise l'intelligence artificielle pour obtenir de meilleurs résultats opérationnels en exploitant les données disponibles. Dans ce projet, nous avons également utilisé l'apprentissage automatique, la connaissance des processus et les données pour développer des modèles de four adaptés aux opérations de la SLN », a déclaré M. Hii.
La phase initiale de la solution améliorée a été menée à bien en 13 mois seulement, alors qu'il a fallu des années pour mettre en œuvre le système expert. Elle a déjà été mise en œuvre dans cinq chaudières rotatives de la SLN. Les opérateurs ont désormais la possibilité de réduire au minimum le recours au fioul de haute valeur tout en maximisant l’utilisation du charbon pulvérisé de faible valeur pendant le fonctionnement en mode mixte.
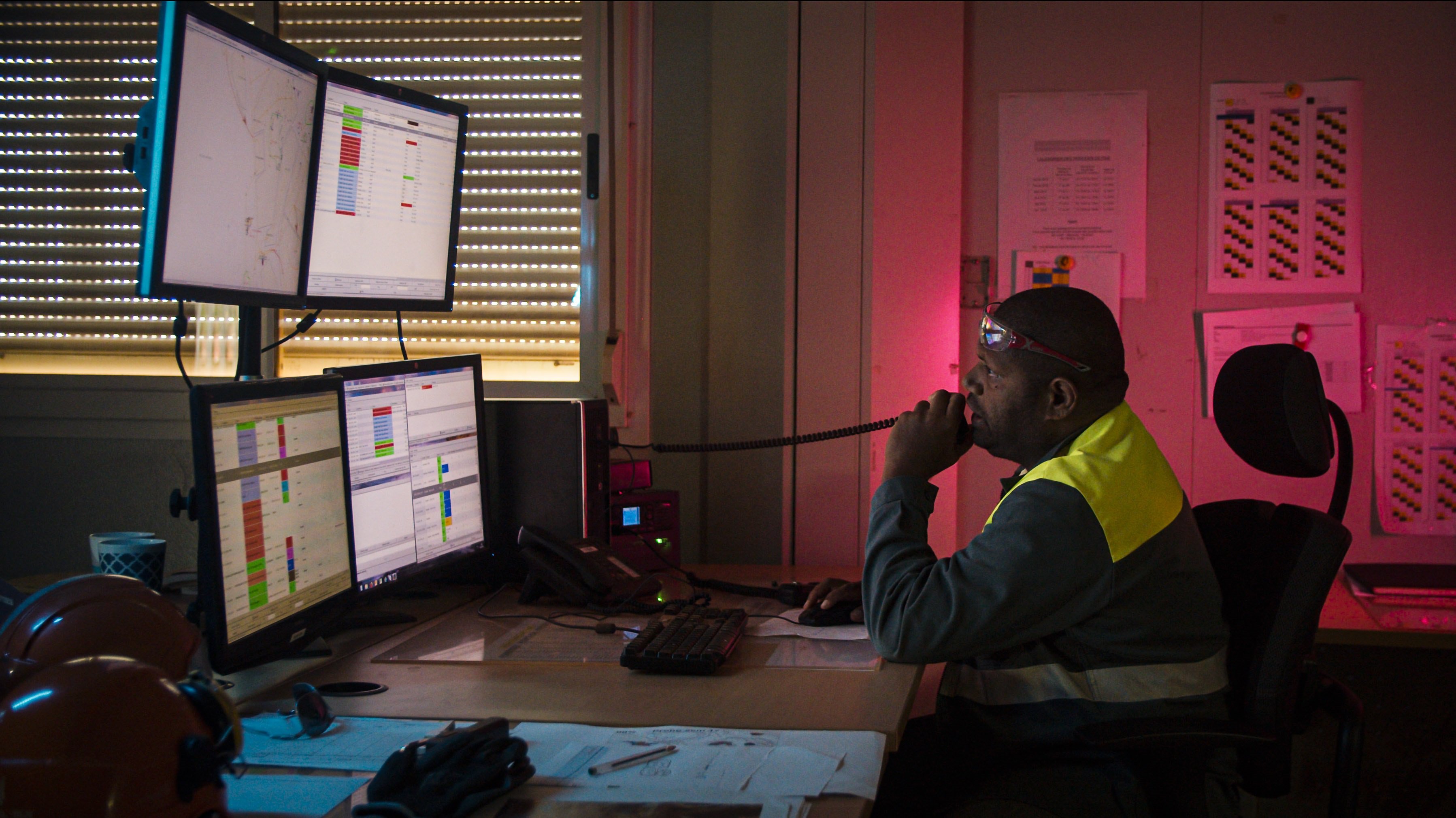
SLN upgraded to Rockwell Automation’s FactoryTalk® Analytics™ Pavilion8® to boost efficiency and performance. Image copyright: Société Le Nickel (SLN), part of the Eramet Group.
L'investissement qui porte ses fruits
“La commande prédictive du modèle peut gérer un niveau de variabilité important en termes d'alimentation en minerai et de valeurs calorifiques. De plus, elle empêche les déclenchements de sécurité, ce qui permet à la chaudière de continuer à fonctionner à un taux de disponibilité plus élevé », a déclaré Mickael Montarello, responsable commande de procédé chez SLN. « Les erreurs liées à la température du produit calciné ont été réduites de 6 % et la variabilité du profil de température de la chaudière a été réduite de 16,1 %. »
SLN récolte les fruits de cet investissement. “La durée de fonctionnement moyenne de la solution par commande prédictive du modèle de Rockwell est de 83 %, contre 70 % avec le système expert précédent », a déclaré M. Montarello. “La nouvelle solution permet à la chaudière de fonctionner plus longtemps.
“Les utilisateurs apprécient les côtés intuitif et flexible de l'outil. En cas de problème sur un élément du procédé, les opérateurs peuvent facilement intervenir sur l'élément en question, tout en permettant à la commande prédictive du modèle de continuer à commander les autres variables manipulées.
« Grâce à cet outil, de nouvelles possibilités d'optimisation de la commande et de la gestion s'ouvrent, lesquelles n'étaient pas possibles avec l'ancien automate à logique floue. Notre objectif pour 2024 est d'atteindre un taux d'utilisation de 90 % », a conclu M. Montarello.
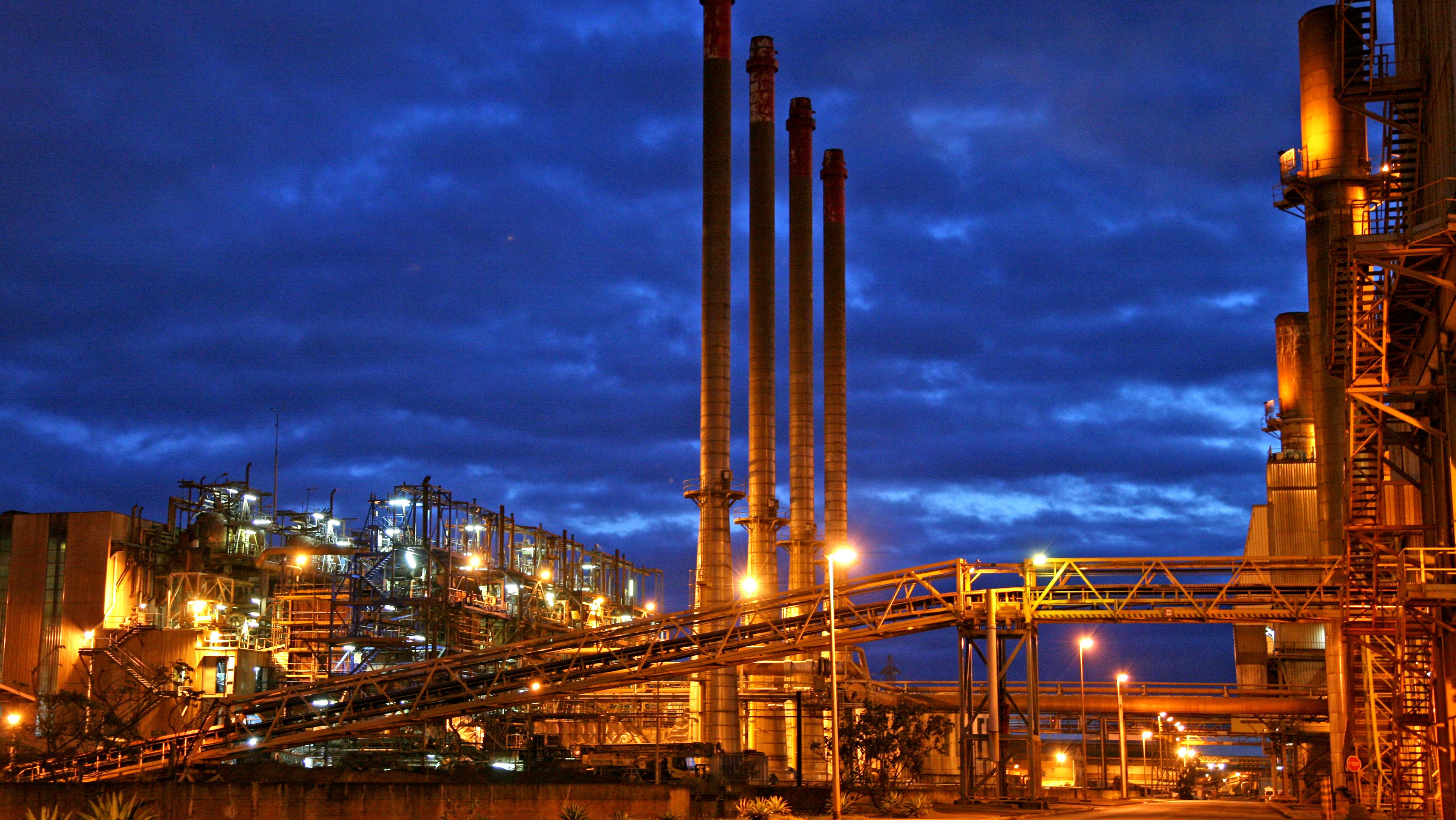
The average uptime of Rockwell’s MPC is 83% compared with 70% with the earlier expert system. Image copyright: Société Le Nickel (SLN), part of the Eramet Group.
Publié 5 janvier 2024