Consigliato per voi
Per Harpak-ULMA, un OEM nel settore del packaging, trasformazione digitale significa espandere ciò che è possibile non solo nelle sue operazioni ma anche in quelle dei suoi clienti.
Il produttore di macchine da imballaggio e di soluzioni di automazione per linee di imballaggio end-to-end ha iniziato il suo percorso di trasformazione digitale nel 2018. Il processo in più fasi e della durata di diversi anni mira a incrementare le entrate e a creare nuove opportunità di crescita per Harpak-ULMA. Inoltre, punta a migliorare le possibilità dei clienti nei mercati alimentare, medicale e industriale, dotandoli di macchine per l’imballaggio intelligenti e connesse.
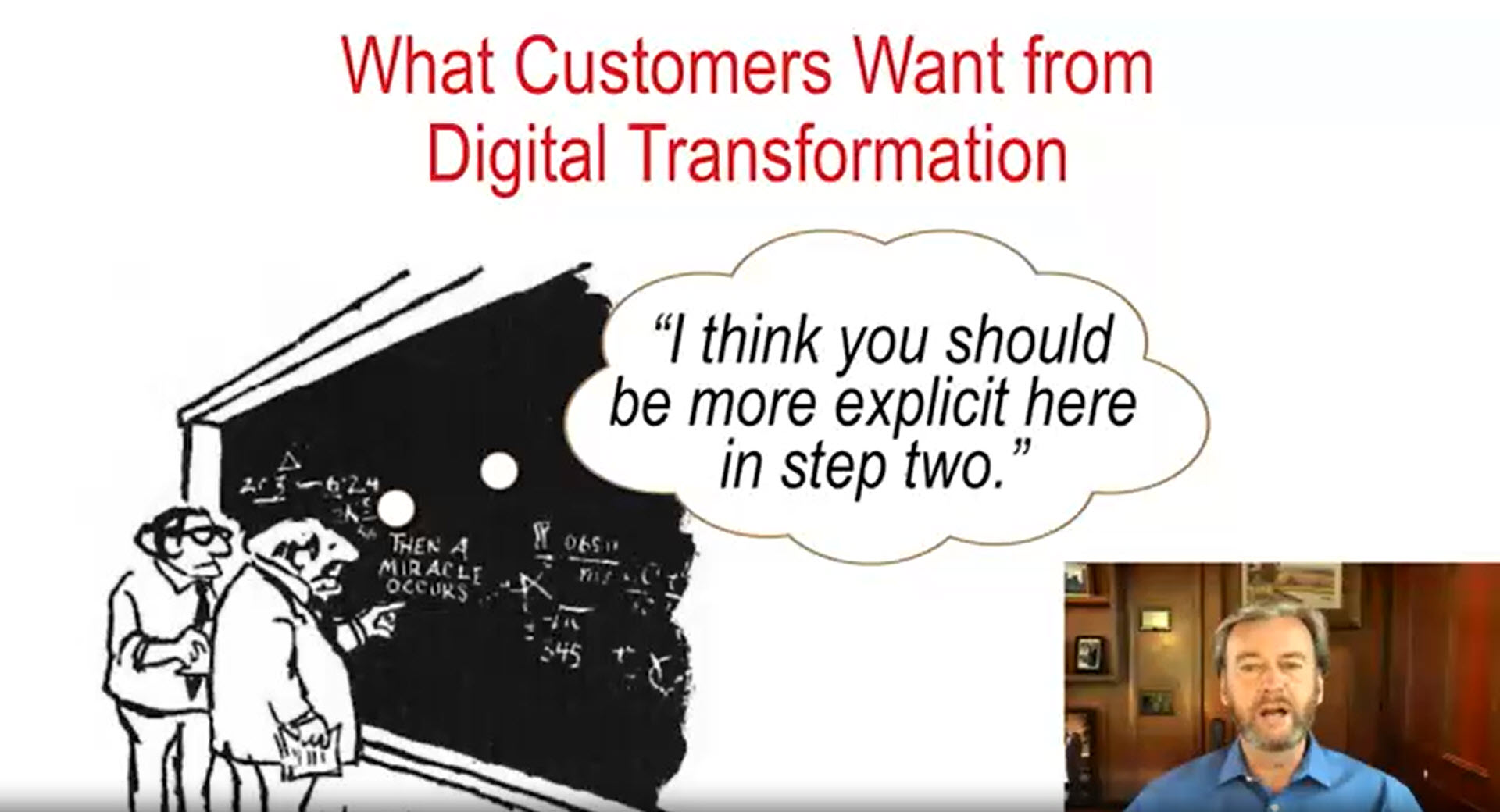
Migliorare l’agilità
Per Harpak-ULMA, il valore della trasformazione digitale sta nella sua capacità di aiutare i clienti ad adattarsi meglio ai cambiamenti del mercato.
“La trasformazione digitale ci dà tanti vantaggi”, ha dichiarato Kevin Roach, presidente di Harpak-ULMA. “Ci aiuta a fare di più e ad essere più veloci, sfruttando i dati per gestire al meglio le tradizionali barriere al cambiamento, cioè tempo, costi e rischi.”
L’azienda ha avviato il suo progetto di trasformazione digitale nell’ottobre 2018 con una roadmap tecnologica che comprendeva quattro fasi.
La prima fase è stata quella di definire una piattaforma intelligente e connessa per i clienti, migrando a un’unica piattaforma di controllo standardizzata. Harpak-ULMA ha scelto di affidarsi ai controlli e ai componenti Rockwell Automation. In questo modo l’azienda ha potuto sfruttare i vantaggi di un’architettura aperta per macchine intelligenti e connesse. Le soluzioni di controllo di Rockwell Automation hanno anche permesso una compatibilità pre-integrata con le innovative applicazioni software IoT di PTC, come Vuforia e ThingWorx, che aiutano a cambiare il modo di gestire ed eseguire la manutenzione degli asset di produzione.
La seconda fase ha riguardato l’implementazione di flussi di lavoro in realtà aumentata (AR) per aiutare a migliorare la produttività.
Grazie alla consulenza e alla guida visiva fornita attraverso la realtà aumentata, Harpak-ULMA può supportare i clienti da qualsiasi luogo e introdurre nuove funzionalità come i collaudi in fabbrica virtuali. I clienti possono inoltre utilizzare la tecnologia per ridurre i tempi di apprendimento e di formazione dei nuovi operatori.
Nuovi dati e informazioni
Harpak-ULMA ha fatto notevoli progressi nella fase due, ed ora è in atto la fase tre che comporta l’integrazione di altri elementi IoT. Si tratta essenzialmente di creare i gemelli digitali delle macchine da imballaggio al fine di offrire una migliore esperienza operativa e un’integrazione delle informazioni.
“Espandere il raggio d’azione IoT ci permette di integrarci con applicazioni IoT avanzate che mostrano al personale di produzione operazioni dettagliate della macchina in tempo reale", ha aggiunto Roach.
Per i clienti, disporre di più dati significa avere più informazioni di produzione in tempo reale e contestualizzate, disponibili sia per il personale che per la diagnostica a bordo macchina.
“In questa fase, stiamo ampliando le capacità AR per fornire un set più completo di funzioni in tempo reale che permetteranno al personale di avere quella che noi chiamiamo visione a raggi X”, ha detto Roach. “La creazione di un gemello digitale di una macchina è un modo interattivo per imparare di più e diagnosticare meglio.”
Per esempio, se un tecnico riceve un allarme da una macchina, non ha bisogno di spegnere la macchina stessa, eseguire le procedure di lockout/tagout e aprire l’armadio di controllo per cercare il problema. Si può semplicemente usare un visore AR, uno smartphone o un tablet e guardare un gemello digitale della macchina per identificare il guasto.
Previsioni future
La quarta fase del processo di trasformazione digitale di Harpak-ULMA consiste nell’applicare sistemi di machine learning e intelligenza artificiale alla grande quantità di dati raccolti durante la produzione. Questo progetto, ancora in fase di pianificazione, permetterà all’azienda di creare nuovi modelli di business introducendo servizi di manutenzione predittiva e di benchmarking basati su cloud.
“Questa fase finale rappresenta un passo avanti per i clienti in termini di rapporto con gli OEM”, ha commentato Roach. “Le soluzioni basate sui big data che sfruttano il machine learning e l’intelligenza artificiale renderanno possibile l’analisi dei dati della manutenzione predittiva nei nostri mercati.”
La manutenzione predittiva può aiutare i clienti a ridurre i tempi di fermo non pianificati, oltre a riorganizzare i modelli di manutenzione e di controllo dei costi. E il benchmarking a livello industriale offre l’opportunità di ottenere una nuova comprensione dell’efficacia dei loro processi produttivi.
Naturalmente, la realizzazione di questi concetti negli ambienti di produzione dei clienti comporterà delle sfide.
“Dovremo risolvere i problemi relativi alla proprietà dei dati e alla connettività che sorgono con il monitoraggio della manutenzione predittiva”, ha precisato Roach. “Non è che non ci siano precedenti al riguardo. Se è successo già per i motori degli aerei, sarà possibile anche per il settore delle macchine da imballaggio.
Pubblicato 1 dicembre 2020