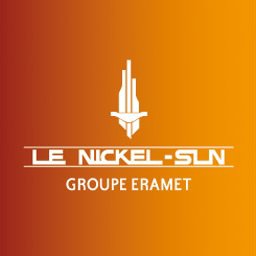
Société Le Nickel (SLN), parte del Gruppo Eramet, il più grande produttore mondiale di ferro-nichel.
- Il sistema precedente era troppo lento e causava frequenti interruzioni elettriche dovute alla temperatura troppo elevata del prodotto, compromettendone la qualità.
- Il sistema precedente non era facile da usare e richiedeva una complessa manutenzione, compromettendo il tempo di disponibilità.
- La piattaforma FactoryTalk Analytics Pavilion8® di Rockwell Automation, una soluzione di controllo predittivo basato su modello che gestisce l’impianto in tempo reale. La piattaforma offre un livello Intelligence che si colloca sopra i sistemi di automazione e valuta continuamente i dati operativi attuali e previsti.
- Miglioramento delle prestazioni, utilizzando dati autonomi e in tempo reale e confrontandoli con i risultati desiderati. Il controllo predittivo basato su modello stabilisce nuovi obiettivi nel sistema di controllo assi, con il fine di ridurre la variabilità del processo, migliorare le prestazioni e aumentare l’efficienza.
- Riduzione degli errori, inclusa una riduzione del 6% dell’errore di temperatura del prodotto e una riduzione del 16,1% della variabilità del profilo di temperatura.
- Miglioramento del tempo di disponibilità, che con il nuovo software Rockwell è passato dal 70% all’83%.
Grazie alla sua capacità di resistenza alla corrosione ad alte temperature e all’utilità come elemento di composizione delle leghe, il nichel svolge un ruolo fondamentale in una serie di settori industriali che vanno da quello aerospaziale a quello chimico, da quello dell’elettricità all’automotive.
Société Le Nickel (SLN), parte del Gruppo Eramet, il più grande produttore mondiale di ferro-nichel. L’azienda, che vanta 140 anni di attività, produce anche manganese, litio e titanio, materiali fondamentali per la produzione di batterie, pigmenti per vernici e turbine eoliche, oltre ad altri prodotti.
La lavorazione dei minerali è un’attività complessa, che richiede un controllo stabile del profilo di temperatura delle camere di combustione rotative e l’automazione dei processi in diversi ambiti operativi. Il minerale di partenza introdotto nel forno rotativo viene sottoposto a calcinazione mentre attraversa la lunghezza della camera di combustione. Se il prodotto calcinato non raggiunge una temperatura sufficientemente elevata, ne viene compromessa la qualità.
Il calore si diffonde in tutta la camera di combustione, la quale avviene grazie all’apporto di aria. Se l’aria immessa è eccessiva, per mantenere la stessa temperatura del prodotto è necessario bruciare più combustibile, riducendo così l’efficienza energetica. L’eccesso di ossigeno deve essere ridotto a un livello sicuro per diminuire i costi operativi e le emissioni di gas serra.
Lacune del sistema precedente
SLN utilizzava un sistema esperto, un controllore a logica fuzzy esistente, progettato per automatizzare il funzionamento della camera di combustione. Tuttavia, con il sistema precedente l’azienda si è trovata ad affrontare diverse sfide, in particolare legate al diverso contenuto di minerale e ai valori di calore variabili, che portavano a picchi di temperatura e a frequenti interruzioni elettriche. Tali interruzioni erano causate dall’elevata temperatura del prodotto, che comprometteva sia la qualità del prodotto stesso che l’integrità delle macchine.
“La logica fuzzy non era in grado di ridurre il carburante abbastanza velocemente da evitare interruzioni e, in caso di funzionamento manuale, gli operatori non potevano reagire con sufficiente rapidità” ha spiegato Leslie Hii, uno degli ingegneri del controllo di processo avanzato di Rockwell Automation responsabili della realizzazione del progetto SLN.
“Mantenere la temperatura richiesta all’interno della camera di combustione può essere complesso e impegnativo, dato il numero di variabili da gestire. Il combustibile impiegato può essere petrolio, carbone o un insieme dei due, ciascuno con determinate caratteristiche termiche. Inoltre, la velocità di alimentazione del materiale incide sulla temperatura della camera di combustione e deve essere accuratamente gestita” ha dichiarato Hii.
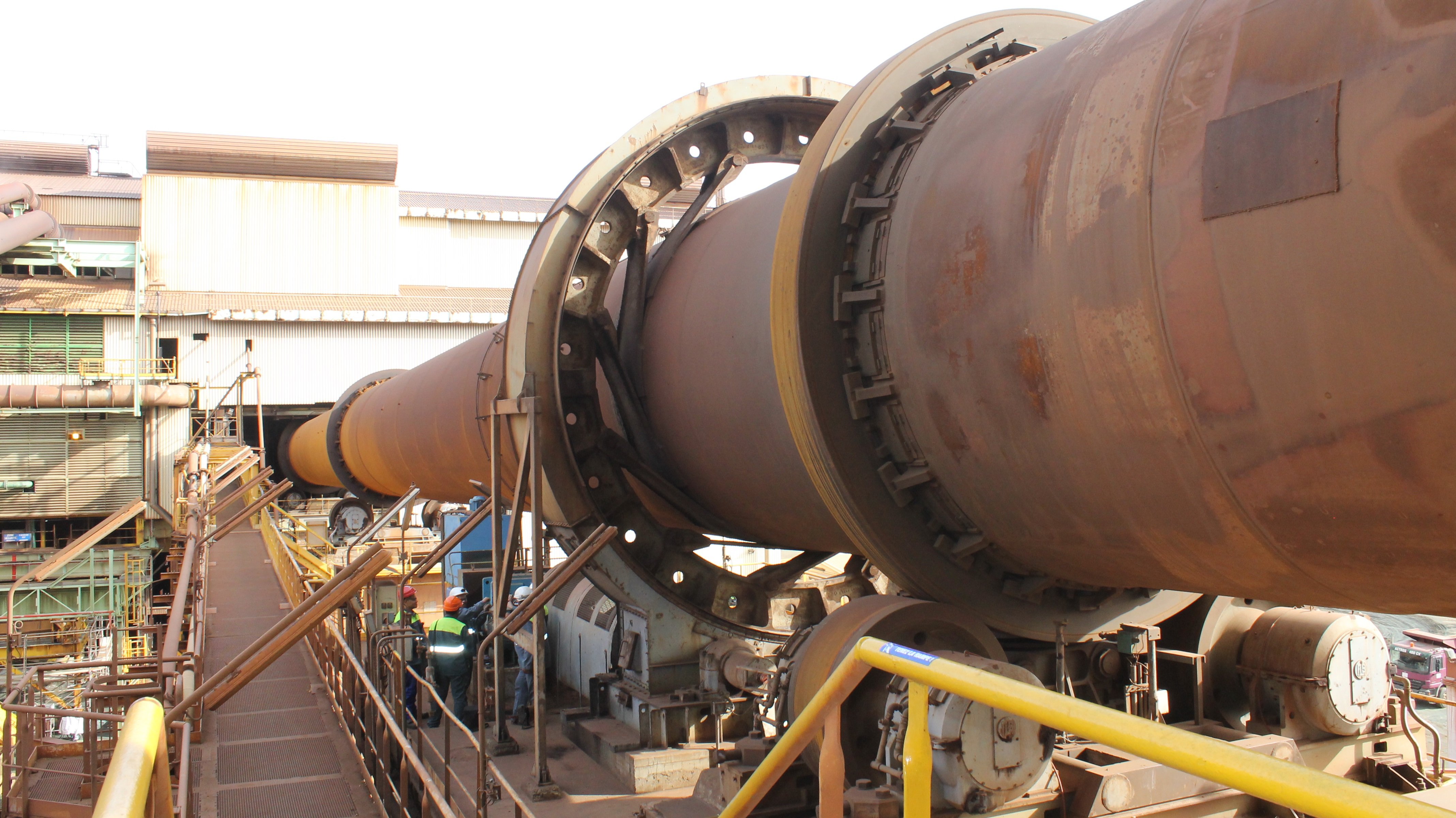
Société Le Nickel (SLN), part of the Eramet Group, is the world’s largest producer of ferronickel. Pictured is one of the five furnaces managed by Rockwell Automation’s FactoryTalk® Analytics™ Pavilion8® software. Image copyright: Société Le Nickel (SLN), part of the Eramet Group.
Aggiunta di un livello Intelligence
Il sistema esperto può essere attivato solo quando la camera di combustione funziona normalmente e, in caso di instabilità, l’operatore lo spegne e ne assume il controllo. Il sistema esperto è stato giudicato carente anche in termini di facilità d’uso e di manutenzione, fattori che compromettevano il tempo di disponibilità del sistema.
Per rimediare alla situazione, SLN è passata a FactoryTalk® Analytics™ Pavilion8® di Rockwell Automation. Questa soluzione con sistema di controllo predittivo basato su modello (MPC) offre un livello Intelligence che si colloca sopra i sistemi di automazione e valuta continuamente i dati operativi attuali e previsti. In seguito, confronta questi dati con i risultati desiderati e determina nuovi obiettivi di controllo per ridurre la variabilità del processo, migliorare le prestazioni e aumentare l’efficienza, il tutto in modo autonomo e in tempo reale.
“Implementare una soluzione MPC è il perfetto esempio di come Rockwell Automation stia utilizzando l’intelligenza artificiale per ottenere migliori risultati operativi sfruttando i dati disponibili. In questo progetto, abbiamo sfruttato anche il machine learning, la conoscenza dei processi e l’analisi dei dati per sviluppare modelli di forno appositamente pensati per le operazioni di SLN” ha dichiarato Hii.
La fase iniziale della soluzione avanzata è stata portata a termine con successo in soli 13 mesi, in netto contrasto rispetto agli anni impiegati per l’implementazione del sistema esperto. È già stata implementata in cinque camere di combustione rotative presso lo stabilimento di SLN. Durante il funzionamento in modalità mista, gli operatori ora hanno la possibilità di ridurre al minimo l’utilizzo di olio combustibile ad alto valore e di massimizzare il carbone polverizzato a basso valore.
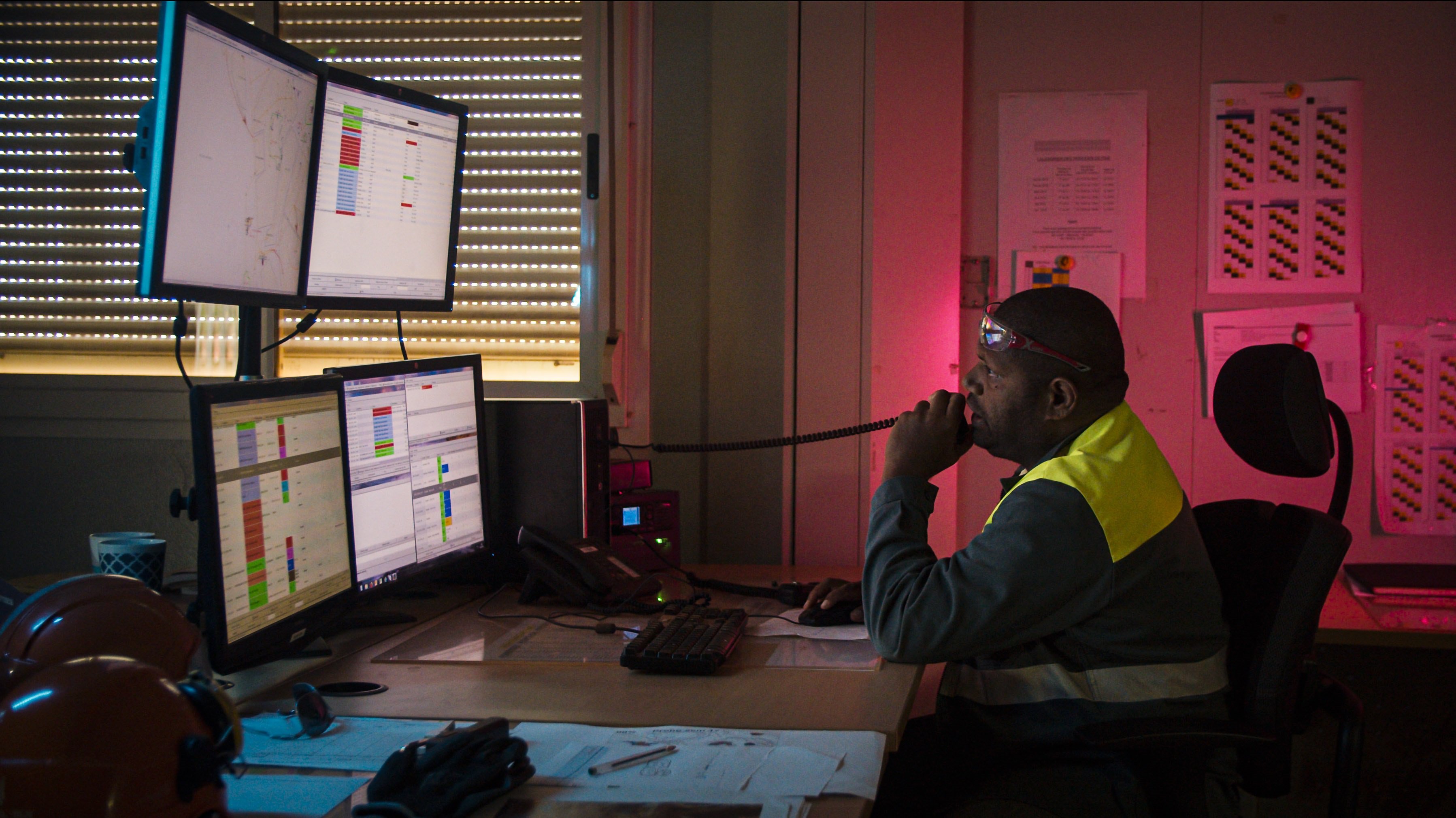
SLN upgraded to Rockwell Automation’s FactoryTalk® Analytics™ Pavilion8® to boost efficiency and performance. Image copyright: Société Le Nickel (SLN), part of the Eramet Group.
Gli investimenti ripagano
“L’applicazione MPC è in grado di gestire una significativa variabilità dei valori di alimentazione e di riscaldamento del minerale e di prevenire le interruzioni, consentendo alla camera di combustione di rimanere in funzione a un ritmo più elevato” ha dichiarato Mickael Montarello, responsabile del controllo dei processi di SLN. “L’errore di temperatura del prodotto calcinato è stato ridotto del 6% e la variabilità del profilo di temperatura della camera di combustione del 16,1%”.
SLN sta raccogliendo i frutti dell’investimento. “Il tempo medio di disponibilità dell’MPC di Rockwell è dell’83%, contro il 70% del sistema esperto precedente” ha affermato Montarello. “La nuova soluzione consente alla camera di combustione di rimanere in funzione più a lungo.
“Gli utenti apprezzano la facilità d’uso e la flessibilità dello strumento. Nell’eventualità di problemi con un elemento del processo, gli operatori possono facilmente intervenire sull’elemento in questione, mentre l’MPC continua a controllare le altre variabili gestite.
“Grazie a questo strumento, si aprono nuove opportunità di ottimizzazione del controllo e della gestione, che non erano possibili con il vecchio controllore a logica fuzzy. Il nostro obiettivo per il 2024 è raggiungere un tasso di utilizzo del 90%” ha concluso Montarello.
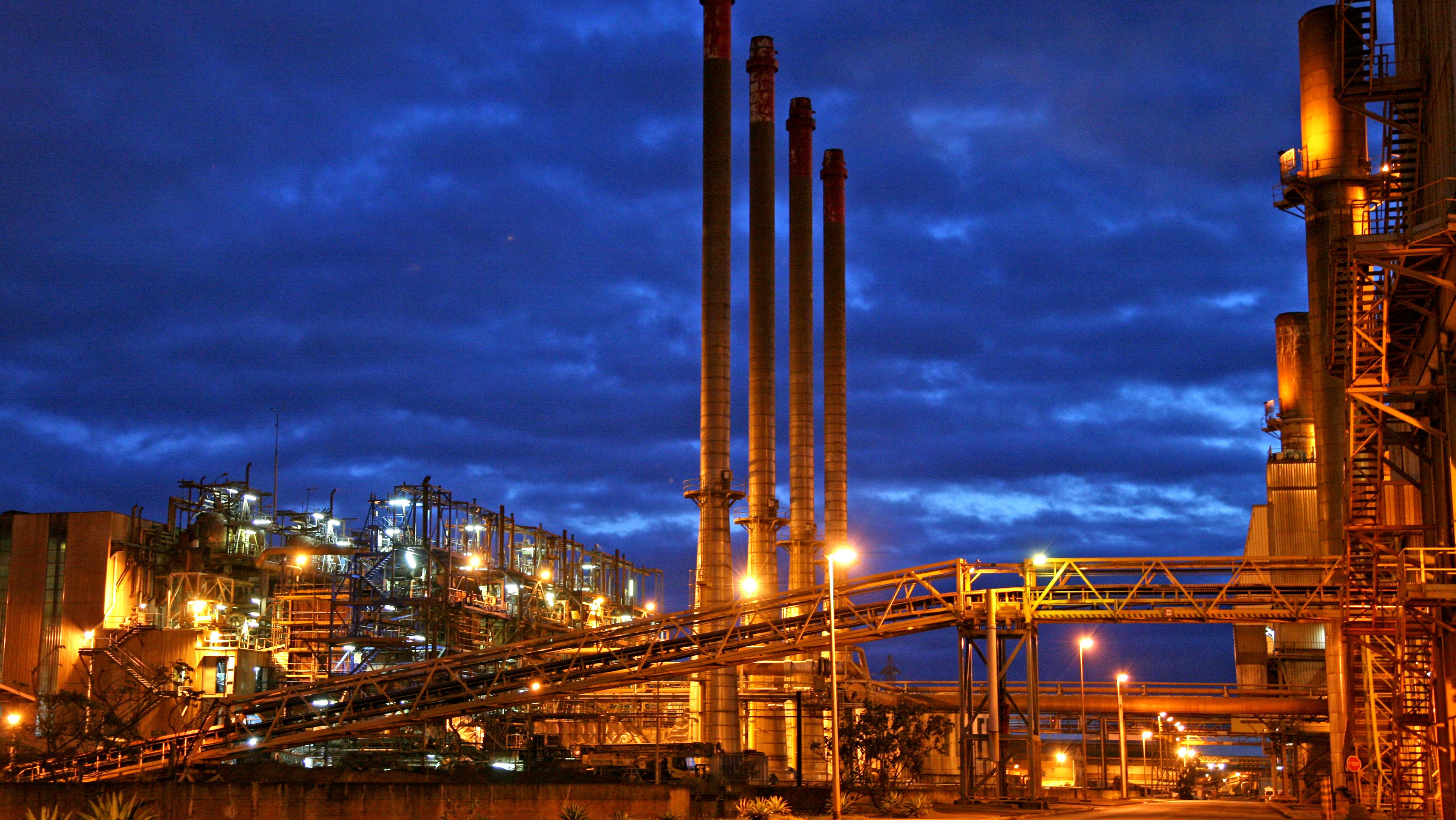
The average uptime of Rockwell’s MPC is 83% compared with 70% with the earlier expert system. Image copyright: Société Le Nickel (SLN), part of the Eramet Group.
Pubblicato 5 gennaio 2024