お客様へのご提案
工場の生産性がすべての世界では、休業時間を伴う災害(LTA: Lost Time Accident)は誰もが必要としないものです。このような事故は、OSHAの記録可能なイベントとなり、企業の安全記録に傷をつけることになり、予定外のダウンタイムにもつながります。休み時間、事故調査、書類作成、生産量の低下などを考えると、休業時間を伴う災害のコストはあっという間に膨らんでしまいます。では、どうすれば休業時間を伴う災害を防ぐことができるのでしょうか? また、利益を損なうことなく、強固な安全文化を実現するにはどうすればよいのでしょうか?
LNSリサーチ社の「Asset Performance Management and Risk Management」レポート(2020年発行)によると、多くの組織が従業員の福利厚生や職場の安全をコアバリューと捉え、責任ある運営を行なうことで正しい行動をとるよう努めています。EHS (環境・労働安全衛生)を改善する最大の目的は、人、生産、環境に害を及ぼす可能性のあるリスクをコントロールし、コンプライアンス義務を果たせないリスクを減らすことです。LNS Research APM 4.0の調査に参加した300人のビジネスリーダのうち、46%がオペレーショナルエクセレンスがEHSの重要な推進力であると回答し、51%がオペレーショナルリスクの低減をEHSの重要な目的として挙げています。
OSHA (米国労働安全衛生庁)の概要によると、業務上の傷病が以下の1つ以上の原因となった場合、記録しなければなりません。
- 基本的な応急処置を超える医療行為
- 意識の喪失
- 仕事に復帰できない、または仕事を休んだ日がある
- 医療上の制限による就業制限または他の仕事への転換
- 医療専門家によって診断された重大な傷害または疾病
- 従業員の死亡
休業時間を伴う災害の最も一般的な原因は、人間工学的な問題に起因する捻挫、緊張、または涙ですが、多くの休業時間を伴う災害は、適切な管理を行なうことで防ぐことができます。これらの制御・管理には、物理的な障壁、プロセスや手順の変更、工学的制御、または個人を危険から守るために設計された特定の機器が含まれます。
安全を向上させる機会を探す際には、「制御の階層」を考慮してください。
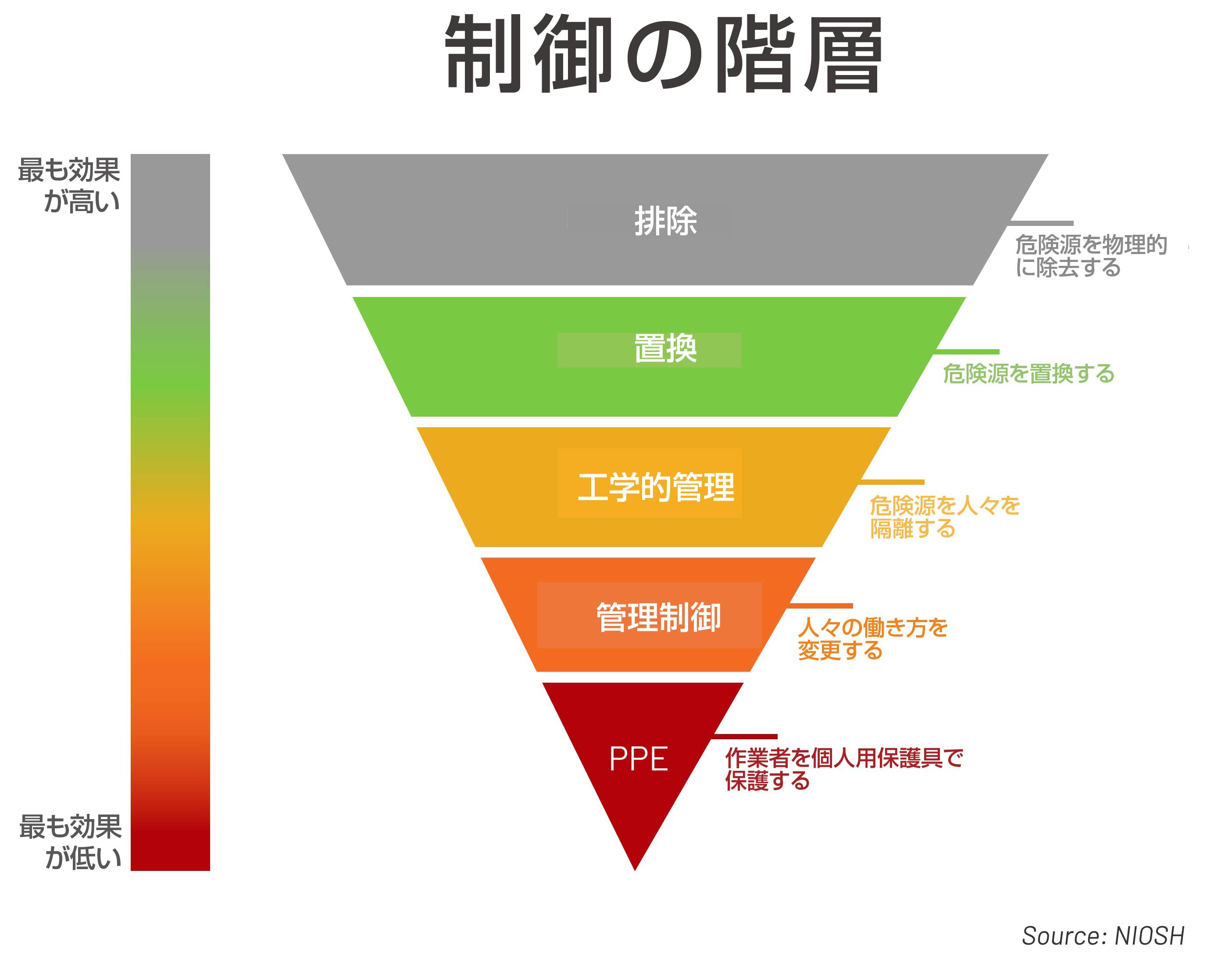
個人用保護具(PPE)
PPEは一般的に最も効果の低い制御方法ですが、それでも確立すべき重要な制御であることに変わりはありません。しかし、適切なPPEを提供することは簡単なことです。しかし、適切なPPEを供給するのは簡単なことですが、どのようなPPEがいつ必要かについて従業員を教育し、PPEの使用を強制することは、効果を低下させる大きな課題となります。
従業員を教育するために、どのPPEが必要かをトレーニングコースと標識を掲示することで明確に伝えてください。アークフラッシュのラベルを更新して、すべてのパネルに計算されたラベルと必要なPPEのカテゴリを必ず記載し、権限のある人が要件を知ることができるようにしてください。ロックアウト/タグアウト、閉鎖空間への立ち入り、またはその他のSOP文書のための書面化された手順を補完するために、特定の作業のためのツールの使用および正しいPPEに関する標識を施設全体に追加してください。
PPEの使用を強制することは、効果的なリスク軽減の鍵となります。適切なPPEの使用を奨励する方法を見つけ、不適切なPPEによる休業時間を伴う災害を防ぐために、従業員が定期的に摩耗したPPEを点検し、交換することを奨励してください。
管理制御
管理制御は、従業員の働き方を変えるものであり、方針の変更、手順の文書化、またはさまざまな形態のトレーニングが含まれます。これらの変更は、職場での事故防止に積極的に役立ちます。
手順書とトレーニングを完備したロックアウト/タグアウトプログラムを開発・実施することで、多くの休業時間を伴う災害を防ぐことができます。遵守されたロックアウト/タグアウト手順は、従業員が機器で安全に作業するために必要な情報を提供します。優れたLOTOトレーニングプログラムは、権限のある従業員に、関連する危険性と制御方法を伝えます。
簡単なサービス手順(またはAlternative De-Energization Procedures (ADP): 代替電源切断手順)や文書化された標準作業手順(Standard Operating Procedure (SOP))などの追加手順は、管理制御を適用し、記録可能な事故を防止するための方法です。これらの文書化された手順は、タスクを実行するための正しく安全な方法を文書化したものであり、有効性を示すために完全なリスクアセスメントが完了している限り、使用することができます。
工学的制御
次のレベルの管理では、作業者と危険の間に物理的な障壁を設けます。工学的制御は、従業員がPPEを使用したり手順に従うことに頼るのではなく、物理的に職場を変化させます。従業員にかわって行動したり考えたりする必要はありません。
現在の物理的な障壁について、機械警備の監査を行なうことを検討してください。機器が現在、適切な機械保護具を備えているか、または追加の保護具が必要かどうかを判断します。
また、機械のリスクアセスメントは、現在の制御の有効性を確認し、施設内の未解決のリスクを特定するためにも有効な手段です。
必要性を特定し、必要な工学的制御を導入するための先行投資は、最初の2段階の能動的な制御よりも高くなりますが、最終的には工学的制御の方が傷害事故や休業時間を伴う災害の防止に効果的です。さらに、ROIと長期的な安全と生産性の向上により、投資を正当化することができます。
置換と緩和
最後に、職場での怪我やOSHA記録に残る事故を防ぐための最も効果的な方法は、怪我につながる危険源をすべて置き換えるか軽減することです。これは必ずしも可能ではないかもしれませんが、それでも検討すべきです。
機器をアップグレードして、より高い安全遂行レベルのPLdやPLe部品など、より安全な制御システム部品を導入することで、人が頻繁に介在する機械の中・高リスクを軽減することができます。また、これらの安全の高い機器を導入することで、一部のタスクをこれらの代替手段で安全に実行できるようになり、タスクの迅速な完了と稼働率の向上につながります。
最終的な目標は、機械のリスクを設計的に排除し、個人がそもそもその危険源に遭遇する可能性を減らすことです。従業員がこれらの危険源に接触しなければ、休業時間を伴う災害につながる怪我はそもそも起こりません。
さらなる検討事項
工場の安全を向上させるために、従業員が仕事以外の怪我を報告することを奨励してください。業務外で発生した軽度の怪我であっても、勤務時間中に悪化する可能性があります。人身事故を把握することで、重大な事故が発生する前に、従業員の職務内容を変更することができます。
基本的な応急処置は記録可能な事故ではありませんので、事故を過剰に扱ったり、過剰にエスカレートさせることは避けてください。
仕事に関連した事故であるかどうか、休暇が必要かどうかを適切に判断するために、従業員が医療機関を受診する際には必ず医師の診断書を要求し、確認してください。
職場における安全の重要性について従業員を教育してください。安全な行動を促すために、安全を従業員にとって身近なものにしてください。
最後に、企業文化が安全を支えていることを確認します。生産性向上のプレッシャーがなくなることはありませんが、従業員には常に安全のための時間があることを伝え、経営陣は安全な方法で物事を行なうための時間を確保することをサポートします。従業員が安全よりも迅速性を求められていると感じると、結果的に手抜きにつながり、労働災害の可能性が出てきます。リスクを軽減するためには、これらの対策を実施するだけでは不十分であり、企業は安全文化を醸成する必要があります。
制御の階層化を実施する上でサポートが必要な場合は、RACSMSAFETY@ra.rockwell.comにご連絡ください。ロックウェル・オートメーションの安全サービスの専門家がお手伝いします。
公開 2021/06/11