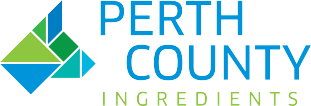
Perth County Ingredients社は、カナダをはじめ世界中の食品、飲料、スポーツ栄養市場に乾燥卵製品を提供するサプライヤです。
- メンテナンスが著しく事後対応的だった
- 時間外のメンテナンス要請が頻繁にあった
- 事後保全が54%減少
- 時間外のメンテナンス要請を47%削減
- メンテナンス費用を4万ドル削減
課題
毎日、一日中続く火消し作業
トム・ダフトン氏は2012年から請負業者としてPCI社の乾燥卵加工施設で勤務していたため、2017年に現在のメンテナンス/プロジェクトマネージャとしての職務に就いたときには、すでにプラントについて豊富な知識を持っていました。
「私がフルタイムで担当し始めたときには、施設をアップグレードする必要に迫られていました。新しいボイラーや新しい冷却装置が必要でした」と、トムは述べています。そのうえメンテナンスチームは時間とリソースを浪費しており、そのメンテナンス作業は100%事後対応でした。チームは終日火消しに追われ、本来の業務を行なえませんでした。また、彼のチームには時間外の緊急呼び出しについてほとんど知見がありませんでした。リセットボタンを押すだけでも、よくある問題の解決であっても、メンテナンスチームはアラートを受け取れば誰かが対応する必要がありました。
彼はチームがより先見的に問題に対応できるソリューションを施設に導入する必要があると感じていました。
ソリューション
Fiixを使用して事後保全に取り組み、時間を節約
施設のBASシステムはすでに導入されていましたが、良好な管理を行なうにはまだ不十分だと彼は認識していました。彼は信頼できる CMMSソフトウェア を必要とし、Fiix, by Rockwell Automationを選択しました。始めるのにそれほど時間はかかりませんでした。
「それは非常に単純でした」と、トムは施設にFiixを設置することについて述べています。「資産の追加、作業指示の作成、定期メンテナンスなどの作業を開始する前に、チームは日々の指示をそのソフトウェアで確認できます。」
トムは、Fiixソリューションはモバイルデバイスからアクセスできる必要があると認識していました。彼はメンテナンスチーム全員に Fiixアプリ を搭載したタブレットを用意することから始めました。このアプリを使用すると、チームは資産のQRコードをスキャンして、作業の記録と検索が可能です。また、標準の操作手順(SOP)、古い作業指示、およびBASに数秒でアクセスできるようになりました。これらすべてが、特に請負業者の管理が関わる場合、問題のトラブルシューティングにかかる時間を短縮するのに役立ちました。
「工場全体にWi-Fiを導入したことで、タブレットや携帯電話を使用してFiixにアクセスできるようになりました」と、トムは述べています。
また、写真やアセットタグによる定期メンテナンス項目がシステムにすべて準備してあれば、その情報を保守業者に提供すればよく、チームが手間をかける必要はありません。
全社的なメンテナンスの自動化
PCI社の運用担当副社長は、トムの施設での成功を受けて、彼に全米の他の7つのL.H. Gray社の施設にFiixを導入することを指示しました。
このプロジェクトの利点についてトムは次のように述べています。「当社の施設内の自動化により、基本的に1ヶ所から複数のオペレーションを行なうことが可能になりました。生産マネージャと私が電子メールを受信するので、常に施設の状況を把握しています。実際に現場にいなくても、何が起こっているのか分かるのです。」
「これらの自動化対策を導入することで、同時に1カ所にいる必要のある人の数を減らすことができました」と、トムは述べています。
さらにFiixの制御機能により、稼働調整を計画することなくトムは残りの実装をリモートで展開することができます。
結果
メンテナンス効率の最大化を追求
トムの戦略は功を奏しました。事後保全は54%減少し、時間外の呼び出しは47%減少しました。しかし、まだ改善の余地は十分にありました。
予防保全は依然として古い習慣に基づいて計画されていました。コンプレッサは、たとえ完全に作動していても、数週間ごとにチェックされます。オイルの交換は、技術者がオイルの良し悪しを判断したかどうかに依存していました。そして検査はまだ手作業で行なわれていました。チームは毎週、検針票をチェックし、データを記録するのに何時間も費やしていたのです。
資産の故障と修理作業は減少した一方、他のことに使うことができうるチームの時間とお金が、これらのタスクに費やされているとトムは認識していました。そこで彼はスケジュールからそれらをカットすることに着手しました。
問題が1つだけありました。トムにはそれらのジョブを特定するために必要な情報や、それらを自動化するためのツールがありませんでした。そこで彼はFiixの統合パートナである Majik Systems社 と協力して、解決策を探りました。
状態ベースのメンテナンスで年間4万ドルを節約
FiixとMajik社の協力のもと、トムは施設内のPLCをCMMSに接続することに成功しました。これによって彼は機器の状態に関するリアルタイムの情報を収集できるようになりました。今では、振動や温度など、あらゆる機械の状態を把握することができるようになりました。
しかしこのデータは、Majik社とFiixの間のリンクがなければ、ほとんど役に立たないでしょう。この接続により、トムが何もしなくても資産データがCMMSに送られます。測定値が特定のスレッショルド(閾値)に達すると、作業指示が作成されます。
最も良いことは、統合がリモートで行なわれたことです。開始から完了までわずか2週間しかかかりませんでした(同社と彼のチームの作業時間は1日足らずでした)。
トムは次のように述べています。「現在は、アラームがトリップしたら、対応が実施されない、またはメンテナンスに連絡がない場合は、シャットダウンする可能性をオペレータに警告しています。工場は年中無休24時間で稼働していますが、メンテナンスは月曜日から金曜日までです。ですから、これらすべての情報を収集することが非常に重要です。資産の状態に変化が見られた場合は、対策を実行する必要があるからです。」
結果は即座に現れ、意義のあるものでした。トムがMajik社を導入してから9ヶ月が経ちますが、故障を減らし、チームのやることリストから不要な仕事を排除することで、すでに4万ドルのコストが削減されました。これは、プロジェクトへの彼の当初の投資に対して300%の利益です。
古い問題が解消されるのを見てきました。それはモータポンプやベアリングの交換などの作業です。しかし、それらはすべて減少しました。そして、トムがメンテナンススケジュールを最適化し、会社がより賢明な設備投資の判断を下す方法を追求し続ける中で、FiixとMajik社を接続することの価値はさらに高まるでしょう。
予知保全により状態基準保全を補完
状態基準保全はPCIにとって大きな前進でした。しかしトムは、メンテナンスチームの次の課題が、より予測に基づいた対策を始めることだとわかっていました。彼は、故障が発生しそうな時点を予測できる状態を目指していました。その希望に応えたのがFiixのAsset Risk Predictorでした。
チームはMajik社の統合により、すでにポンプの電流やトルクなどは追跡していたため、そのデータをAsset Risk Predictorに供給することは合理的な流れでした。
収集データをAsset Risk Predictorに供給することにより、CMMS以上にアラートを深く掘り下げることが可能になります。今では、ポンプの軽度な不具合やシールの過度な摩耗などの問題を回避でき、スムーズな生産が維持されるだけでなく、システムに流れ込むすべてのデータを踏まえて情報に基づいた意思決定を行なうことができます。
「今のところ、非常にうまくいっています」と彼は述べています。故障に関する質問に対して、彼は冗談めかしながら、「残念ながら故障はまだ発生していませんが、いくつかのデータが黄色の注意信号を示したことはあります」と答えました。
公開 2022/05/22