製造業での成功は常に素早くイノベーションを行なう能力と結びついてきました。全員が設計プロセスで早い段階から頻繁に連携できるクラウドで、世界中の各関係者と関係者のデータを集められることを想像してください。デジタルスレッドはこれを可能にします。全社でシームレスなデータフローが実現され、オペレーション全体の改善と便益につながります。
バリューチェーン全体でのリアルタイムなコラボレーションから、新しいラインとプロセスのバーチャル検証、データサイエンスの簡略化、製造の柔軟性向上まで、デジタルスレッドは目指すものを再考するために役立ちます。
資産のライフサイクルは直線的ですが、最高のデジタルスレッドはデジタルのフィードバックループです。この全体的なソリューションは、資産の過去、現在、将来の状態を可視化して意思決定を強化します。バリューチェーン全体の協力者は、上流と下流の利害関係者による洞察を簡単に活用できます。
デジタルスレッド手法を早い段階で導入した企業は、生産性とイノベーションで最先端を走り、孤立したシステムと事業部門からデジタルスレッドに接続された企業に移行しています。ただし、デジタルスレッドの構築を試みたことがあるすべての企業は、ばらばらのツールとシステムに散らばるデータの統合は難しいこともあることを実感しています。
一流の製造メーカは、デジタルツインの作成に固有の課題を認識し、集まってより良く混乱の少ない代替手段を創造しようと力を結集しています。このアプローチでは、デジタルテクノロジとサービスを統合し、CADパッケージ、シミュレーションソフトウェア、自動設計ソフトウェアなどのツールを接続するために実行する必要がある作業を削減します。現在使用している好みのツールをエンジニアが使用し続けられる形でのデジタルスレッド作成を支援します。
可能性を拡大
デジタルスレッドは、デジタルエンジニアリングを使用してビジネスの可能性を拡大します。例えば、新しいマシンのCADモデルを制御システムのコードに接続することができます。これにより、シミュレーションソフトウェアを使用して、マシンの立上げを迅速化し最終段階での想定外の問題を避けることができる仮想制御のテストを実行できます。さらに一歩進んで、新しいマシンがより大規模なシステムの一部としてどのように動作するかをシミュレートし、障害などの問題特定に役立てることもできます。
また、デジタルスレッドを使用して製品へのデジタルリンクを作成し、お客様に届けた後の動作状況とパフォーマンスをモニタすることも可能です。これにより、製品の修理対応力を強化できます。また、今後の製品の変更や新製品の開発をお客様に知らせるためにも役立ちます。
このような機会の実現は、デジタルテクノロジとサービスのオープンな統合エコシステムで大幅に簡略化できます。また、生産工程と隣接する事業部門間でテクノロジ統合とデータ標準化にかける時間を削減できます。さらに、この取組みに携わる製造メーカは各分野のリーダであるため、お客様はおそらく現在すでに使用しているエンジニアリングツールの一部またはすべてを使用し続けることで恩恵を得ることができます。
つまり、新しいテクノロジを購入する必要性や仕事の進め方をめぐる混乱を抑制できます。また、オペレーション間でデータを接続するための労力も軽減されます。
ある主要な消費財メーカは、デジタルソリューションのエコシステムを新しい製品ラインの最適化と立上げ期間の短縮に役立てています。この企業が選択した業界最高水準のツールは、複数のサプライヤによって提供されているものの、統合され、エンジニアはデジタル・エンジニアリング・ワークフローを使用して新しいラインを開発できます。
例えば、設計データをCADパッケージから業界トップクラスのシミュレーションソフトウェアに移行し、ラインのより複雑な側面の一部のシミュレーションモデルを作成しています。その後、これらのモデルを別のエミュレーションソフトウェアに移行して、制御コードでテストし、仮想空間でラインの立上げを行ないます。
異なるツール間の統合により仮想空間でシームレスに行なわれるこの作業は、新しいラインのエンジニアリング時間および現場での立上げ時間の短縮に役立つでしょう。
ロックウェル・オートメーションは、デジタルイニシアチブの実装の簡略化と品質の向上に役立てるために、デジタル・パートナ・プログラムを開発しました。ANSYSやEPLANなどと連携し、複雑なエンジニアリング上の課題を解決し、設計および開発段階だけではなくオペレーションとメンテナンス作業においても生産性向上に役立つデジタルスレッドを作成するお客様を支援することができます。
次の段階の競争上の優位性
競争上の優位性の維持にはスピードが極めて重要です。新規の競合他社が記録的スピードでイノベーションを進める一方で、個人に合わせた製品への期待がますます高まっています。世界クラスの製造メーカは、デジタルトランスフォーメーションのイニシアチブへの投資を大々的に進めています。デジタルスレッドの技術を活用した包括的なデジタル戦略は、製造メーカがバラバラのチームとシステム間の摩擦をなくし、行動を迅速化するために役立ちます。
デジタルと非デジタルの産業組織のパフォーマンスから得られる最大のポイントは、時間の経過と共にパフォーマンスのギャップが大きくなることです。- IDC
デジタルトランスフォーメーションは、以下のような多数の利点をシステムと事業部門にもたらします。
連携の強化による価値実現までの期間の短縮: デジタルトランスフォーメーションにより、バリューチェーン全体でリアルタイムなコラボレーションを実現できます。すべての利害関係者を最初からリアルタイムにまとめることで、依存関係が解消されます。また、プロセスと製造に関する変更を仮想空間でエミュレートできるため、立上げ時間を半減できることも証明されています。
デジタル拡張による従業員の能力向上: デジタルトランスフォーメーションの利点の一例として、リモートコラボレーションによりどこでも専門知識を活用できるようになります。製造に関する専門知識を拡張現実で全従業員に拡大できます。オペレータの作業効率と安全は、忠実性の高いトレーニングと仕事中の指示で向上させることができます。実際にデジタルトランスフォーメーションがトレーニング時間を最大75%短縮できることも証明されています。
稼働効率と機動性の向上: IT/OTのコンバージェンスの自動化により、デジタルスレッド向けに最適化された情報モデルで拡張性に富んだ洞察を採取できます。プラントを他の事業部門が作成したデジタルコンテンツに接続してオペレーションを最適化すると、データサイエンスから価値を実現する期間を最大70%短縮できます。また、企業システム間の摩擦をなくし、製造の柔軟性と機動性を向上させることもできます。人の介入なく世界中のどのプラントやラインでも指示をダウンロードして実行できるため、完全自動の製造を実現できます。
稼働中のデジタルスレッド
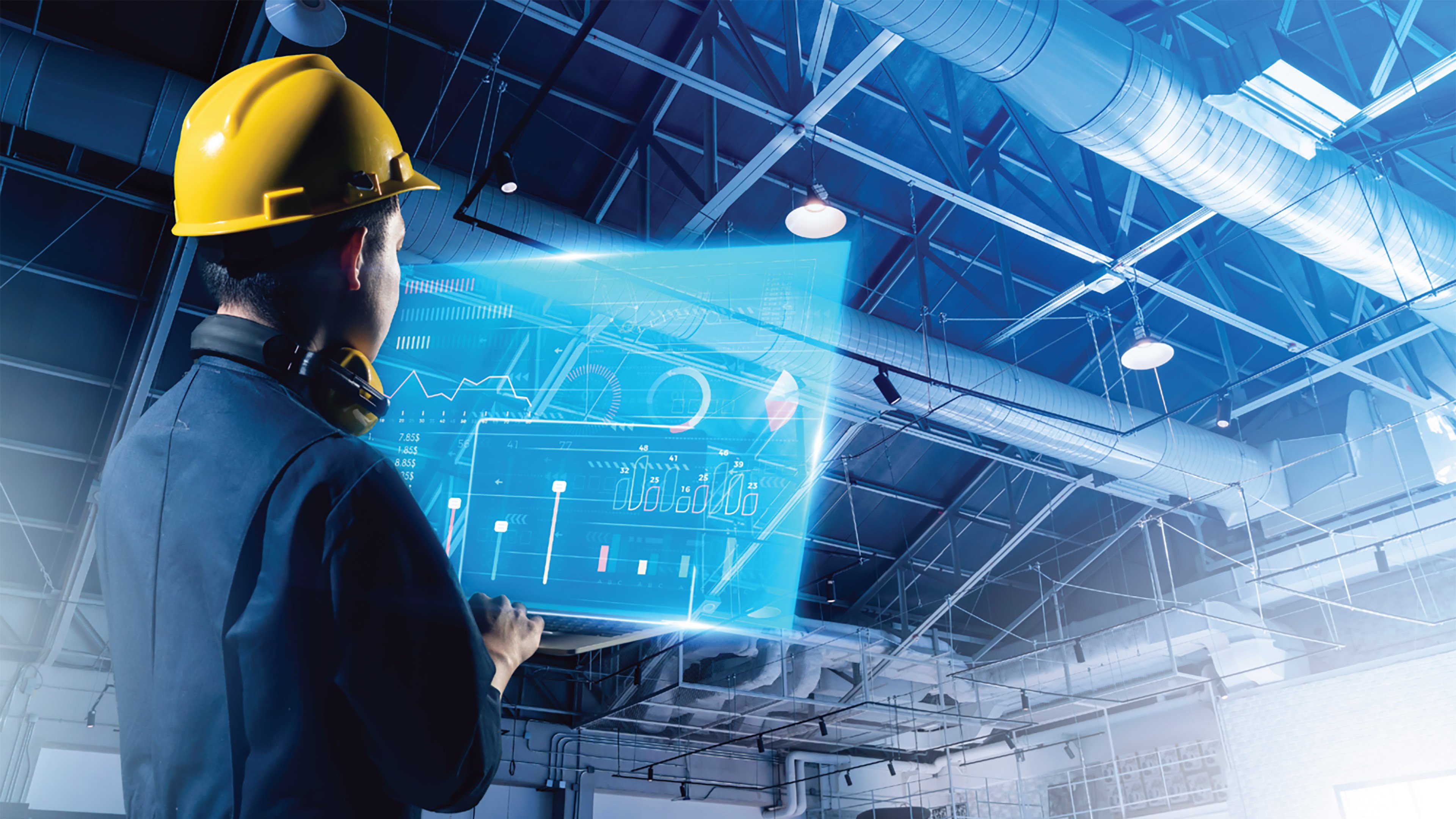
ロックウェル・オートメーションは、デジタルトランスフォーメーションの初期段階を超えて、継続的な改善の状態に到達しました。これにより、デジタルトランスフォーメーションは、次に来るものの最前線に立ち続けることができます。
ロックウェル・オートメーションは、グローバルメーカであり、主要なテクノロジプロバイダであり、独自のデジタルトランスフォーメーションを推進する独自の立場にあります。
製造メーカとして、23,000人の従業員の約3分の1が20の世界中の製造工場で働いており、40万SKU近くの製品カタログを管理しています。産業オートメーションとデジタルトランスフォーメーションを専門とする世界最大の企業として、世界中の企業がプロセスを改善し、非効率性を減らし、生産性を向上させることを支援しています。
ロックウェル・オートメーションの製造部門は、流行語になる前にデジタルトランスフォーメーションを採用していました。彼らは、複数の異なるシステムを1つのエンタープライズ・リソース・プランニング(ERP)システムに結合することから始めました。これにより、世界中の他の多くのシステムを管理できます。並行して、彼らは一元化された記録システムとして製造実行システム(MES)を展開し、次の数年間、工場、プロセス、および人員を単一のMESに接続するためにプラントごとに移動しました。
これにより、高レベルのIT/OTコンバージェンスが実現し、すべての施設でワークフローとプロセスを標準化するための基盤が提供されました。これにより、すべての施設でワークフローとプロセスを標準化するための基盤が提供されました。ロックウェル・オートメーションは、世界中の工場を繋げるための国際的に標準化されたアプローチを確立し、デジタルトランスフォーメーションの次の波への準備を整えました。
結果は大きなものでした。ロックウェル・オートメーションは総所有コストを削減し、在庫日数を120日から82日に短縮し、年間の資本回避を30%削減しました。サプライチェーンの納品が最大96%になり、リードタイムが半分に短縮されて、市場投入までの時間が短縮されました。さらに、生産性が年間4〜5%向上したと推定しています。
ロックウェル・オートメーションは、独自のデジタルトランスフォーメーションに精通し、大幅な改善をもたらしましたが、その栄光に満足することはできませんでした。ロックウェル・オートメーションは、工場が接続され、世界中に単一の接続されたシステムがあるため、難しい質問をしました。さて、次は何ですか?
ロックウェル・オートメーションは、運用全体の標準化を推進することにより、接続のメリットを最大限に活用できるようにしたいと考えていました。これを行なうために、コネクテッドエンタープライズのスペシャリストのチームは、工場資産をさらに最適化し、デジタルツールとリソースで従業員に力を与えるように設計された主要なユースケースに焦点を合わせました。
人、製品、およびプロセスの最適化ロックウェル・オートメーションはFactoryTalk InnovationSuite, powered by PTCを採用して、変革の次の段階を構築し、前進させました。このスイートは、6つのグローバル施設全体で、エッジ・ツー・エンタープライズ分析、機械学習、モノのインターネット(IoT)、拡張現実(AR)を直接産業運営に取り入れました。この強力なスイートは、データへのアクセスを容易にし、より多くの情報に基づいたビジネス上の意思決定を可能にし、長期的な成長と継続的なイノベーションを促進します。FactoryTalk InnovationSuiteは、製造メーカが従業員、製品、およびプロセスを最適化し、産業の変革を加速するための最も包括的で効果的な方法です。
テクノロジ自体に大きな可能性があっても、複数のシナリオや施設に拡張できる特定のユースケースがなければ、価値が制限され、ロックウェル・オートメーションが求めている2桁の影響得られることはありません。ロックウェル・オートメーションは、グローバル展開を成功させるために、グローバルな運用と従業員に最大のメリットをもたらすユースケースを特定しました。各場所でユースケースを試験的に実施することで、デジタル文化の転換を促進し、従業員が適切なスキルセットを開発できるように支援することができました。大まかに言えば、これらのユースケースは、インテリジェントな資産の最適化から、従業員の生産性や企業の運用インテリジェンスにまで及びます。
資産管理へのインテリジェントなアプローチを作成するために、運用チームはリアルタイムのモニタ、診断、予測および処方分析を活用して、貴重な可視性を獲得し、マシンの状態と診断をよりよく理解しました。これらの強力なモニタツールを装備することで、計画外のダウンタイムを防止し、資産の使用率を最大化することができました。チームは、この分野で3つのユースケースを実装しました。
スループット
ロックウェル・オートメーションは、強力なリアルタイムモニタおよび分析ツールを活用して、生産量を増やし、生産単位当たりの人件費を削減しました。ロックウェル・オートメーションは、生産プロセスの詳細なデータ分析(特に、ユニット間の時間とステップ当たりの時間)により、需要の高い新製品のスループットを最適化することができました。ある施設では、2桁の結果として、労働効率が33%向上し、生産量が70%増加し、トレーニング時間が50%短縮されました。
ある施設では、2桁の結果として、労働効率が33%向上し、生産量が70%増加し、トレーニング時間が50%短縮されました。
予知保全
ロックウェル・オートメーションは、複雑さと製造年が異なる35台の射出成形機を使用しているため、機械の状態を効率的に判断してダウンタイムを防ぐことは困難でした。IoTテクノロジを活用して、旧式の機械全体で重要なリアルタイム情報を収集し、工場フロアの統一されたビューを作成し、生産性を8%向上させました。これにより、品質管理を強化し、機械の稼働時間を改善し、機械の使用率に基づいてメンテナンスのニーズを確実に満たすことができます。
分析
ボール・グリッド・アレイでの長い生産時間を短縮するために、チームはボールグリッド接続の良し悪しについて新しい機械学習テストを試験的に実施しました。彼らはボードに適用されたペーストの3Dプロファイルを作成しました。これにより、不良なペーストプロファイルがあったかどうかを素早く判断できます。その結果、組み立ての早い段階で問題を検出し、修正にかかる時間を数時間から数分に短縮し、品質保証を向上させ、ペースト関連の欠陥を51%削減することができました。
これらの各ユースケースを通じて、ロックウェル・オートメーションは資産効率を最適化し、機械のダウンタイムを削減し、スループットを向上させてお客様の需要を満たすことができました。そして、これはほんの始まりに過ぎません。「これでデータソースが接続され、識別され、プロセスをさらに改善するための新しいモデルを作成できます」と、ロックウェル・オートメーションのグローバル・プラント・システムのITマネージャであるリオン・ムリオノは述べています。
デジタルワークフォース
ロックウェル・オートメーションは、生産性を向上させるだけでなく、従業員が日々の成果に価値を感じられる環境を作り出すために、デジタルツールを使用して従業員に力を与えることを目指しました。彼らは、従業員の能力を高めるために、4つのターゲットを絞ったユースケースを実装しました。
ワークキューの可視性
ロックウェル・オートメーションは、ITソースとOTソースからのデータを組み合わせて視覚化することにより、材料不足によるラインの飢餓状態のダウンタイムを75%削減し、オペレータが作業を最適化できるようにしました。
標準化されたパフォーマンスレポート
チームは、ダウンタイムが1時間ごとのパフォーマンスに与える影響を確認するためのより明確な方法を必要としていたため、すべてのプラントで使用する共通のKPIダッシュボードを開発しました。スケジューリングシステム、SAP、MES、およびその他のソースからのさまざまな情報を組み合わせることで、構成可能でモジュール式のダッシュボードにより、作業者はパフォーマンストレンドをより適切に視覚化し、データに基づいた意思決定を行ない、労働効率を13%向上させることができました。
ARガイド付き配線トレーニングとクイズ
従業員が効果的に配線できるようにすることは、離職によりますます困難になっています。さらに、成功を測定する客観的な手段がなかったため、品質と安全にリスクが生じました。ロックウェル・オートメーションは、ARテクノロジを使用して魅力的な方法でより良いトレーニング体験を提供することで、従業員をトレーニングすると同時に、スキルのギャップを特定する能力を測定することができました。
ARガイド付きの標準化された作業指示製品の転送
スイスとポーランドの間で工場を移転するには、チームが国や言語間で重要で詳細な知識を伝達する必要がありました。スイスのチームは、ARテクノロジを使用して作業指示の記録を開始し、タスクを写真、ビデオ、ナレーションを使用して段階的な指示に分割し、トレーニング時間を30%短縮しました。
スマートなサプライチェーン
ロックウェル・オートメーションは、電子アセンブリ用の構成部品の需要が急増し、外部ソースから材料を調達する必要があったとき、不適合部品がサプライチェーンに導入されていることにすぐに気付きました。
FactoryTalk MES、統合されたITとOTシステム、および標準化されたプロセスからのインテリジェンスを活用して、問題を特定し、サプライチェーン全体で追跡して、将来の問題を防ぐことができました。この機能により、特定の状況でリコールを80%以上削減できます。
ロックウェル・オートメーションは、リコールを80%以上削減
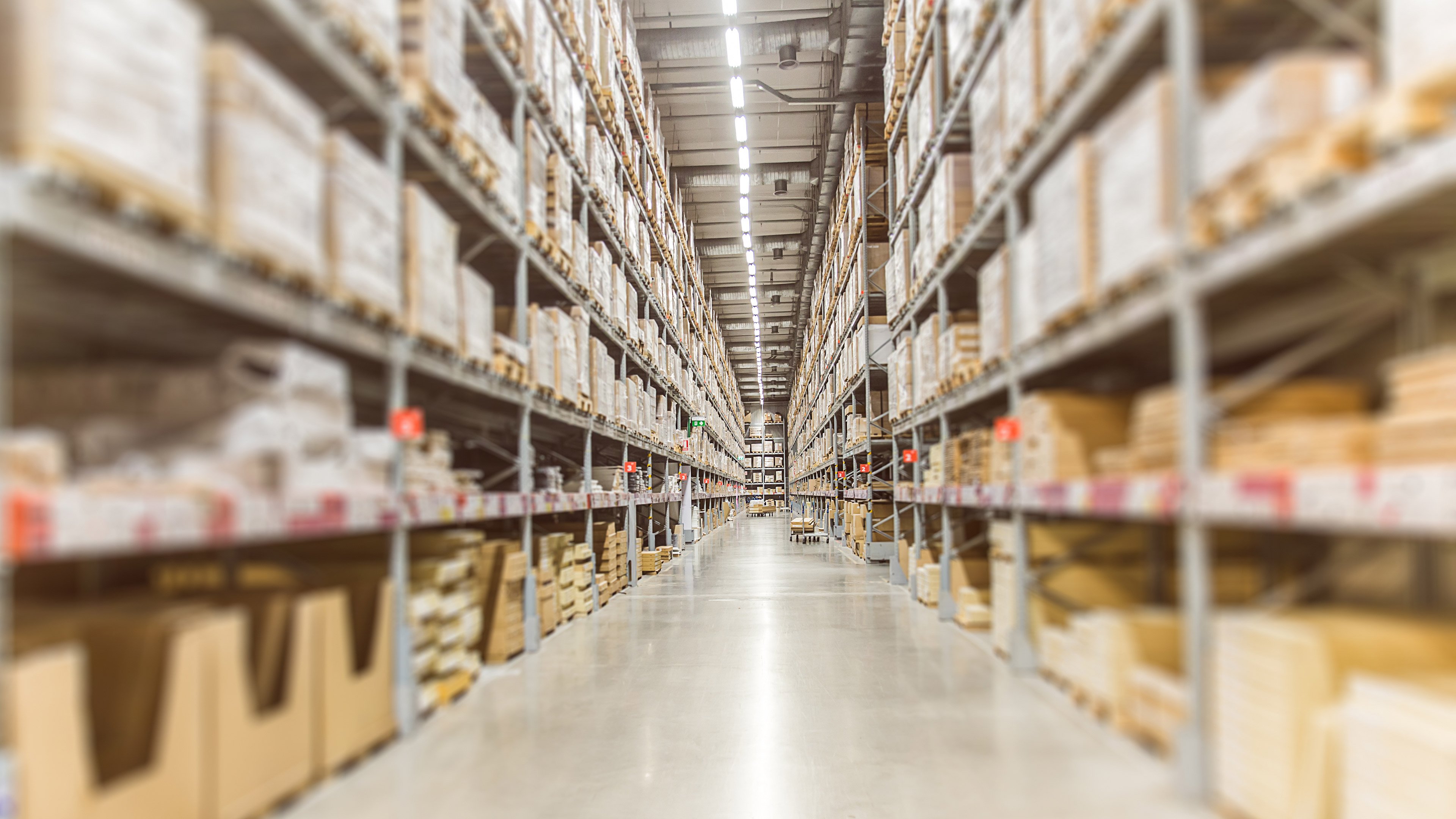
学習に基づいて構築
将来を見据えて、ロックウェル・オートメーションはこれらの最近の学習を積み上げています。お客様と従業員の価値をさらに高めることを目標に、作業者、設備、プロセスのさらなる改善を推進する方法に挑戦しています。
私たちは画期的なARテクノロジを活用し、より多くの手動タスクが自動化されるにつれて、より高いレベルの責任の機会を提供することにより、より良いトレーニングで従業員を武装させています。また、大量のデータを改善された予測と処方機能に変換することで資産を保護し、マシンのパフォーマンスとメンテナンスを新しいレベルの精度で管理しています。
毎日、自分たちのテクノロジの機能についてより多くを学んでいます。これは、想像力と、一歩ずつ継続的に改善および変革するのにかかる時間によってのみ制限されています。